Introduction to Computer-Aided Manufacturing (CAM)
Computer-Aided Manufacturing (CAM) is the use of software and computer-controlled machinery to automate manufacturing processes. CAM is a subsequent computer-aided process after Computer-Aided Design (CAD) and sometimes Computer-Aided Engineering (CAE), as the model generated in CAD and verified in CAE can be input into CAM software, which then controls the machine tools and related machinery to transform the design into a physical product.
CAM is used in many schools alongside Computer-Aided Design (CAD) to create objects. CAM is used to manufacture a wide range of products from medical devices to automobile parts. It enables the production of high-quality goods while reducing labor costs and production time.
Benefits of Computer-Aided Manufacturing
There are several key benefits of using CAM in manufacturing processes:
-
Increased Efficiency: CAM automates many manufacturing processes, reducing the need for manual labor and increasing production speed and efficiency.
-
Improved Accuracy: CAM software controls machine tools with a high degree of precision, resulting in products with tight tolerances and high accuracy.
-
Reduced Costs: The automation provided by CAM reduces labor costs. It also reduces waste and scrap by ensuring the first part is made correctly.
-
Increased Flexibility: CAM allows for easy design changes and the ability to quickly switch between different products, enabling manufacturers to respond rapidly to customer demands.
-
Better Quality Control: CAM provides consistent and predictable manufacturing results, reducing variations and ensuring high product quality.
Benefit | Description |
---|---|
Increased Efficiency | Automation reduces need for manual labor, increases production speed |
Improved Accuracy | Software controls tools precisely, resulting in tight tolerances |
Reduced Costs | Automation reduces labor costs and waste |
Increased Flexibility | Easy design changes, quick product switching |
Better Quality Control | Consistent, predictable results, high product quality |
Types of CAM Systems
There are several types of CAM systems, each with its own strengths and applications:
2.5D Milling
2.5D milling is a type of CAM where the cutting tool moves in two dimensions (X and Y) while the depth (Z) remains constant. It’s used for products with simple geometries and is relatively inexpensive compared to other CAM systems.
3D Milling
In 3D milling, the cutting tool moves in all three dimensions (X, Y, and Z), allowing for the creation of more complex geometries. It’s used for products with curved surfaces, cavities, or other intricate features.
Turning
Turning involves rotating a workpiece on a lathe while a cutting tool removes material. CAM turning is used to create cylindrical parts like shafts, bushings, and other turned components.
Wire EDM
Wire EDM (Electrical Discharge Machining) uses a thin wire electrode to cut through electrically conductive materials. It’s used for parts with complex shapes, tight tolerances, or hard materials that are difficult to machine with traditional methods.
CAM Type | Description | Applications |
---|---|---|
2.5D Milling | Cutting tool moves in X and Y, constant Z | Simple geometries |
3D Milling | Cutting tool moves in X, Y, and Z | Complex geometries, curved surfaces |
Turning | Workpiece rotates while tool removes material | Cylindrical parts (shafts, bushings) |
Wire EDM | Wire electrode cuts conductive materials | Complex shapes, tight tolerances, hard materials |
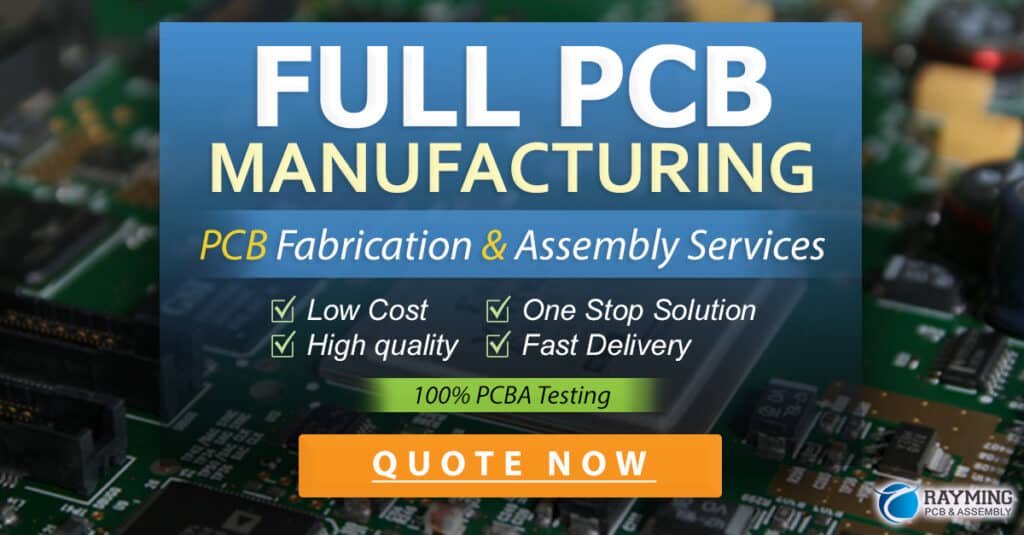
Automated High-Speed Machining
Automated high-speed machining is a type of CAM that uses high spindle speeds and feed rates to remove material quickly. It’s used to reduce cycle times and increase productivity, particularly for parts with long machining times or large production volumes.
Advantages of High-Speed Machining
-
Reduced Cycle Times: High spindle speeds and feed rates remove material faster, reducing the time needed to machine each part.
-
Improved Surface Finish: High-speed machining can produce better surface finishes due to reduced cutting forces and heat generation.
-
Longer Tool Life: Properly implemented high-speed machining can extend tool life by reducing the time the tool is in contact with the workpiece.
-
Reduced Vibration: High spindle speeds can reduce vibrations, leading to more precise machining and better part quality.
Advantage | Description |
---|---|
Reduced Cycle Times | Faster material removal, shorter machining time per part |
Improved Surface Finish | Reduced cutting forces and heat lead to better finishes |
Longer Tool Life | Less tool-workpiece contact time extends tool life |
Reduced Vibration | High speeds reduce vibrations for more precise machining |
Challenges of High-Speed Machining
While high-speed machining offers significant benefits, it also presents some challenges:
-
Machine Requirements: High-speed machining requires CNC machines with high spindle speeds, rapid traverse rates, and advanced controls.
-
Tooling Requirements: Special tooling, such as balanced tool holders and coated carbide inserts, is needed to withstand the high speeds and temperatures.
-
Programming Complexity: High-speed machining often requires specialized CAM software and programming techniques to optimize tool paths and cutting parameters.
-
Operator Skill: Operators must be trained in the unique requirements and best practices of high-speed machining to ensure success.
Challenge | Description |
---|---|
Machine Requirements | Need for high spindle speeds, rapid traverse, advanced controls |
Tooling Requirements | Special balanced holders, coated inserts to withstand conditions |
Programming Complexity | Specialized software and techniques for optimized tool paths |
Operator Skill | Training needed in unique requirements and best practices |
Implementing CAM and High-Speed Machining
Implementing CAM and high-speed machining requires careful planning and execution. Here are some key steps:
1. Assess Your Needs
Evaluate your current manufacturing processes and identify areas where CAM and high-speed machining could provide benefits. Consider factors such as part complexity, production volume, and cycle time.
2. Select the Right Software and Equipment
Choose CAM software that meets your needs for ease of use, functionality, and compatibility with your existing systems. Invest in CNC machines and tooling capable of high-speed machining.
3. Develop Your Processes
Work with experienced CAM programmers to develop optimized tool paths and cutting parameters for your parts. Establish best practices for high-speed machining, including proper tool selection, coolant application, and chip evacuation.
4. Train Your Team
Provide training for your operators, programmers, and maintenance staff on the new software, equipment, and processes. Ensure they understand the unique requirements and challenges of high-speed machining.
5. Continuously Improve
Monitor your results and continuously look for opportunities to improve your CAM and high-speed machining processes. Regularly review performance metrics, seek feedback from your team, and stay up-to-date with the latest technologies and best practices.
Frequently Asked Questions (FAQ)
What is the difference between CAD and CAM?
CAD (Computer-Aided Design) is the use of computer software to create, modify, and optimize product designs. CAM (Computer-Aided Manufacturing) is the use of software to control machine tools and related machinery to manufacture the designed product. CAD focuses on the design process, while CAM focuses on the manufacturing process.
Can CAM be used with any CNC machine?
Most CAM software can generate G-code (the common language for CNC machines) for a wide range of CNC machines. However, the specific post-processor used to translate the CAM output into G-code may need to be customized for the particular make and model of the CNC machine.
What are the limitations of high-speed machining?
High-speed machining is not suitable for all materials and part geometries. Very hard materials may cause excessive tool wear at high speeds, while some complex shapes may create chatter or vibration. High-speed machining also requires specialized equipment, tooling, and expertise, which can increase costs.
How does CAM impact product quality?
CAM can significantly improve product quality by providing precise and consistent control over the manufacturing process. By automating tool paths and cutting parameters, CAM reduces the risk of human error and ensures that parts are machined to the exact specifications of the digital design.
What skills are needed to work with CAM and high-speed machining?
Effective use of CAM and high-speed machining requires a combination of skills, including:
- Knowledge of machining processes and principles
- Familiarity with CAD/CAM software and G-code programming
- Understanding of CNC machine operation and maintenance
- Experience with tooling selection and optimization
- Problem-solving and troubleshooting abilities
Individuals working with CAM and high-speed machining should also be detail-oriented, able to work in a team, and committed to continuous learning in order to stay current with evolving technologies and best practices.
Conclusion
Computer-Aided Manufacturing (CAM) and automated high-speed machining are powerful technologies that can revolutionize manufacturing processes. By automating tool paths, increasing production speeds, and improving precision, CAM and high-speed machining enable manufacturers to produce high-quality parts more efficiently and cost-effectively.
Successful implementation of these technologies requires careful planning, investment in the right software and equipment, and a commitment to training and continuous improvement. By embracing CAM and high-speed machining, manufacturers can stay competitive in an increasingly demanding global market and deliver the innovative, high-quality products their customers expect.
As the manufacturing landscape continues to evolve, those who adopt and master these advanced technologies will be well-positioned for success in the years to come.
No responses yet