Introduction to BOM Components
What is a Bill of Materials (BOM)?
A Bill of Materials (BOM) is a comprehensive list of raw materials, components, and instructions required to manufacture, assemble, or repair a product or service. It serves as a centralized source of information that details each part of the product, including quantities, descriptions, and specifications.
Importance of BOM in Electronics Manufacturing
In the electronics industry, a BOM is crucial for managing the procurement and assembly processes. It ensures that all necessary components are identified, purchased, and available when needed. A well-organized BOM can help streamline production, reduce errors, and improve overall efficiency.
Key Components in an Electronic BOM
Common Electronic Components
An electronic BOM typically includes a variety of components, such as:
- Resistors
- Capacitors
- Inductors
- Diodes
- Transistors
- Integrated Circuits (ICs)
- Connectors
- Switches
- LEDs
- Printed Circuit Boards (PCBs)
Component Specifications
When listing components in a BOM, it’s essential to provide accurate and detailed specifications. This information helps ensure compatibility and performance. Common specifications include:
- Part number
- Description
- Manufacturer
- Package type
- Value (resistance, capacitance, etc.)
- Tolerance
- Voltage rating
- Current rating
Creating an Electronic BOM
BOM Structure and Hierarchy
A well-structured BOM organizes components into a logical hierarchy, making it easier to understand and manage. A typical BOM hierarchy includes:
- Top-level assembly
- Sub-assemblies
- Individual components
BOM Formats and Templates
BOMs can be created using various formats, such as:
- Spreadsheets (e.g., Microsoft Excel, Google Sheets)
- Comma-Separated Values (CSV) files
- Electronic Data Interchange (EDI) formats
- Specialized BOM management software
Using a consistent template ensures that all necessary information is captured and presented in a standardized manner.
Best Practices for BOM Creation
To create an effective electronic BOM, consider the following best practices:
- Use a consistent naming convention for components
- Include detailed specifications for each component
- Specify the quantity required for each component
- Identify alternate or substitute components, if applicable
- Regularly review and update the BOM to reflect changes in design or component availability
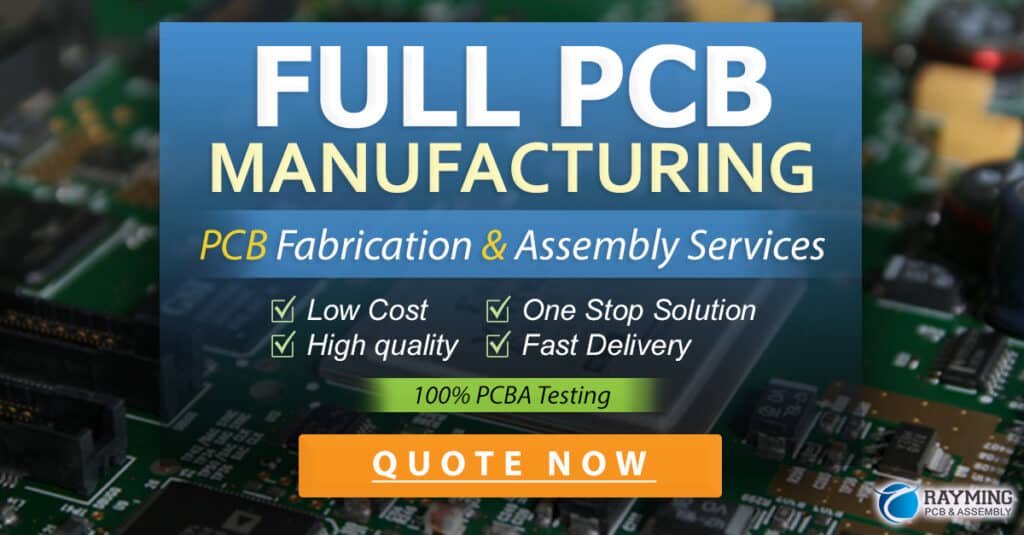
Sourcing Electronic Components
Identifying Reliable Suppliers
Choosing reliable suppliers is crucial for ensuring the quality and availability of components. When evaluating potential suppliers, consider factors such as:
- Reputation and industry experience
- Quality certifications (e.g., ISO 9001, AS9100)
- Product range and availability
- Pricing and minimum order quantities (MOQs)
- Lead times and delivery performance
- Technical support and customer service
Evaluating Component Quality and Authenticity
Counterfeit or substandard components can lead to product failures and safety issues. To mitigate these risks, take the following steps:
- Purchase from authorized distributors or directly from manufacturers
- Request and verify certificates of conformance (COCs) and other quality documentation
- Perform incoming inspections and testing to verify component authenticity and functionality
- Implement traceability measures to track components throughout the supply chain
Managing Lead Times and Availability
Component lead times and availability can significantly impact production schedules. To minimize disruptions:
- Monitor component availability and lead times regularly
- Identify and qualify alternative sources or substitute components
- Maintain adequate safety stock levels for critical components
- Communicate frequently with suppliers to stay informed of potential supply chain issues
Cost Optimization Strategies
Negotiating Pricing and Minimum Order Quantities
To achieve cost savings, consider the following strategies when negotiating with suppliers:
- Request volume discounts for larger order quantities
- Explore the possibility of blanket orders or long-term agreements
- Investigate consignment inventory arrangements to reduce upfront costs
- Collaborate with suppliers to identify cost-saving opportunities in packaging, shipping, or payment terms
Value Analysis and Value Engineering (VA/VE)
Value Analysis and Value Engineering (VA/VE) is a systematic approach to improving the value of products or processes by analyzing their functions and costs. In the context of electronic component procurement, VA/VE can help:
- Identify overspecified or unnecessary components
- Explore alternative components with similar performance at lower costs
- Optimize component selection based on the specific requirements of the application
- Standardize components across multiple products to leverage economies of scale
Inventory Management and Optimization
Effective inventory management can help minimize carrying costs and ensure the availability of components when needed. Some key strategies include:
- Implementing a robust inventory tracking system
- Regularly reviewing and adjusting safety stock levels based on demand and lead times
- Utilizing just-in-time (JIT) or kanban systems to minimize excess inventory
- Monitoring and disposing of obsolete or slow-moving components
Conclusion
A well-managed BOM is essential for the success of any electronics manufacturing project. By understanding the key components, creating a comprehensive and organized BOM, sourcing reliable suppliers, and implementing cost optimization strategies, companies can streamline their procurement processes and improve overall production efficiency.
Frequently Asked Questions (FAQ)
-
Q: What is the difference between a part number and a manufacturer’s part number?
A: A part number is a unique identifier assigned to a component within a specific company’s BOM, while a manufacturer’s part number is the identifier assigned by the component manufacturer. The manufacturer’s part number is typically used when ordering components from suppliers. -
Q: How often should I review and update my electronic BOM?
A: It’s recommended to review and update your BOM regularly, especially when there are changes in product design, component availability, or supplier information. The frequency of reviews may vary depending on the complexity of the product and the dynamics of the supply chain, but a good practice is to review the BOM at least once per quarter. -
Q: What are the risks associated with using counterfeit or substandard components?
A: Using counterfeit or substandard components can lead to various issues, such as reduced product performance, reliability issues, safety hazards, and potential legal and financial consequences. Counterfeit components may not meet the required specifications, leading to early failures or malfunctions. In some cases, they may even pose safety risks to end-users. Additionally, using counterfeit components can result in legal issues related to intellectual property infringement and non-compliance with industry regulations. -
Q: How can I ensure the security of my BOM data?
A: To ensure the security of your BOM data, consider implementing the following measures: - Use secure file storage and sharing platforms with access controls and encryption
- Limit access to the BOM to authorized personnel only
- Implement version control to track changes and maintain an audit trail
- Regularly backup your BOM data to prevent loss due to system failures or cyberattacks
-
Establish clear policies and procedures for handling and sharing BOM information with internal teams and external partners
-
Q: What are some common challenges in managing electronic BOMs?
A: Some common challenges in managing electronic BOMs include: - Ensuring the accuracy and completeness of component information
- Managing changes and revisions to the BOM throughout the product lifecycle
- Coordinating with multiple stakeholders, including design, procurement, and manufacturing teams
- Dealing with component obsolescence and finding suitable replacements
- Maintaining data consistency and integrity across different systems and tools used for BOM management
Component Type | Key Specifications |
---|---|
Resistors | Resistance value, tolerance, power rating, package type |
Capacitors | Capacitance value, tolerance, voltage rating, dielectric |
Inductors | Inductance value, tolerance, current rating, core material |
Diodes | Diode type, forward voltage, reverse breakdown voltage |
Transistors | Transistor type, current gain, voltage ratings, package type |
Integrated Circuits | Device type, package type, pin count, function |
Connectors | Connector type, number of positions, pitch, rating |
Switches | Switch type, number of poles and throws, rating, actuator type |
LEDs | Color, size, forward voltage, luminous intensity |
PCBs | Number of layers, material, thickness, surface finish |
Table 1: Common electronic components and their key specifications
No responses yet