Table of Contents
- Introduction to DFM Analysis
- Benefits of DFM Analysis
- Key Elements of DFM Analysis
- Design for Assembly (DFA)
- Design for Manufacturability (DFM)
- Design for Testability (DFT)
- Design for Reliability (DFR)
- DFM Analysis Process
- Product Design Review
- Manufacturing Process Analysis
- Cost Analysis
- Feedback and Optimization
- Tools and Techniques for DFM Analysis
- Computer-Aided Design (CAD) Software
- Finite Element Analysis (FEA)
- DFMA-software”>Design for Manufacturing and Assembly (DFMA) Software
- Value Engineering
- Best Practices for Implementing DFM Analysis
- Case Studies
- Automotive Industry
- Consumer Electronics
- Medical Devices
- Future Trends in DFM Analysis
- Frequently Asked Questions (FAQ)
- Conclusion
Introduction to DFM Analysis
Design for Manufacturing (DFM) analysis is a systematic approach to optimizing product design for efficient manufacturing. The primary goal of DFM analysis is to identify and address potential manufacturing issues early in the design process, ultimately reducing costs, improving quality, and accelerating time-to-market.
DFM analysis involves a comprehensive evaluation of product design, materials, and manufacturing processes to ensure that the product can be manufactured efficiently and cost-effectively. By integrating DFM principles into the product development process, companies can minimize the risk of manufacturing issues, reduce the need for design changes, and improve overall product quality.
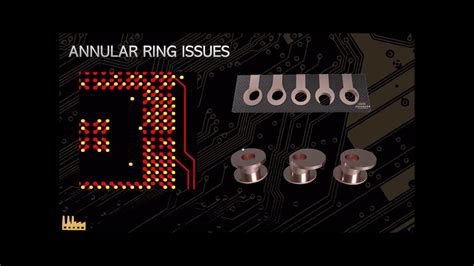
Benefits of DFM Analysis
Implementing DFM analysis offers numerous benefits to organizations, including:
-
Cost reduction: By identifying and addressing potential manufacturing issues early in the design process, DFM analysis helps reduce material costs, labor costs, and tooling costs.
-
Improved product quality: DFM analysis ensures that products are designed for optimal manufacturability, resulting in fewer defects and higher overall quality.
-
Faster time-to-market: By minimizing the need for design changes and reducing manufacturing issues, DFM analysis helps accelerate the product development process and reduces time-to-market.
-
Enhanced collaboration: DFM analysis promotes cross-functional collaboration between design, engineering, and manufacturing teams, fostering a more integrated and efficient product development process.
-
Increased profitability: By reducing costs, improving quality, and accelerating time-to-market, DFM analysis contributes to increased profitability for organizations.
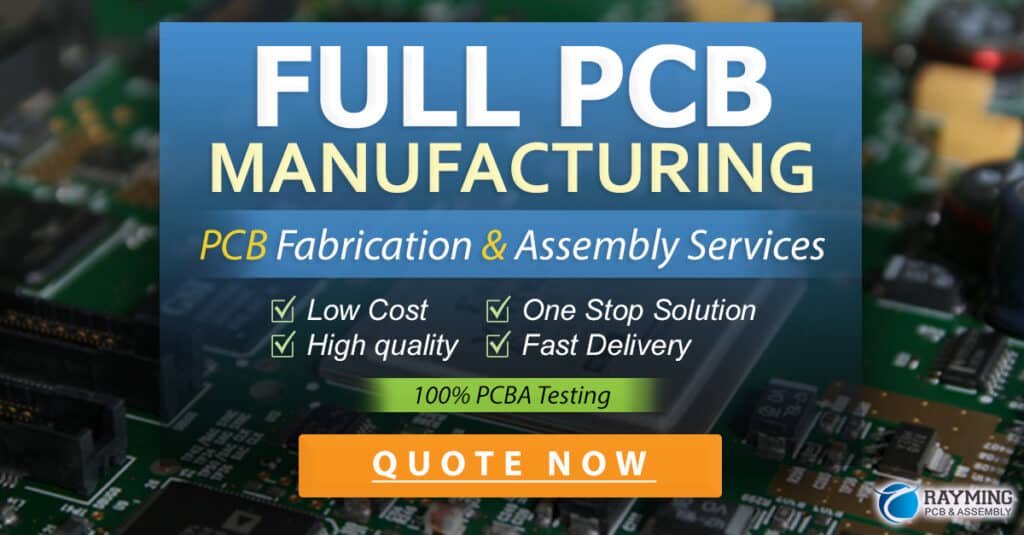
Key Elements of DFM Analysis
DFM analysis encompasses several key elements that contribute to the overall optimization of product design for manufacturing. These elements include:
Design for Assembly (DFA)
Design for Assembly (DFA) focuses on optimizing product design to facilitate efficient assembly processes. Key considerations in DFA include:
- Minimizing the number of parts
- Designing parts for easy orientation and insertion
- Eliminating the need for specialized assembly tools
- Ensuring adequate access for assembly operations
Design for Manufacturability (DFM)
Design for Manufacturability (DFM) involves designing products to optimize manufacturing processes and reduce production costs. Important aspects of DFM include:
- Selecting appropriate materials and processes
- Designing parts for ease of fabrication
- Minimizing the need for tight tolerances
- Reducing the complexity of manufacturing operations
Design for Testability (DFT)
Design for Testability (DFT) focuses on designing products to facilitate efficient testing and quality control processes. Key considerations in DFT include:
- Incorporating test points and interfaces
- Designing for automated testing
- Minimizing the need for specialized test equipment
- Ensuring adequate access for testing operations
Design for Reliability (DFR)
Design for Reliability (DFR) involves designing products to meet specific reliability requirements and minimize the risk of failures. Important aspects of DFR include:
- Selecting reliable components and materials
- Designing for robustness and durability
- Incorporating redundancy and fault tolerance
- Conducting reliability testing and analysis
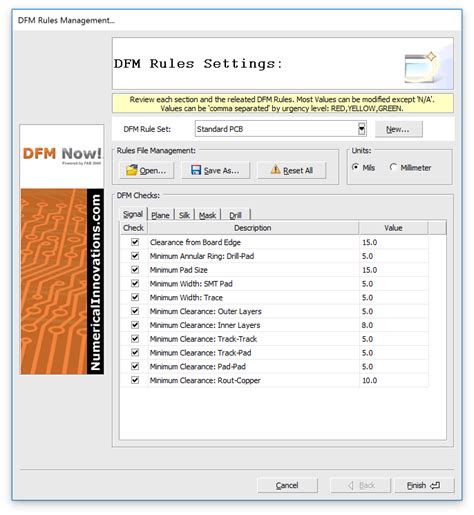
DFM Analysis Process
The DFM analysis process typically involves four main stages:
Product Design Review
In this stage, the product design is reviewed to identify potential manufacturing issues and opportunities for optimization. Key activities include:
- Reviewing design specifications and requirements
- Identifying critical features and tolerances
- Assessing the manufacturability of the design
- Identifying potential design improvements
Manufacturing Process Analysis
This stage involves analyzing the manufacturing processes required to produce the product. Key activities include:
- Identifying appropriate manufacturing processes
- Assessing the capabilities and limitations of each process
- Identifying potential process improvements
- Evaluating the impact of design changes on manufacturing processes
Cost Analysis
In this stage, the costs associated with manufacturing the product are analyzed to identify opportunities for cost reduction. Key activities include:
- Estimating material, labor, and tooling costs
- Identifying cost drivers and opportunities for cost reduction
- Evaluating the impact of design changes on manufacturing costs
- Conducting cost-benefit analysis of proposed design changes
Feedback and Optimization
Based on the findings from the previous stages, feedback is provided to the design team, and the product design is optimized for manufacturing. Key activities include:
- Communicating findings and recommendations to the design team
- Collaborating with the design team to implement design changes
- Validating the optimized design through prototyping and testing
- Documenting the final design and manufacturing specifications
Tools and Techniques for DFM Analysis
Several tools and techniques are commonly used in DFM analysis to facilitate the optimization of product design for manufacturing. These include:
Computer-Aided Design (CAD) Software
CAD software is used to create 3D models of product designs, allowing for Virtual Prototyping and analysis. Key features of CAD software for DFM analysis include:
- Parametric modeling capabilities
- Design rule checking and validation
- Integration with manufacturing simulation tools
- Collaborative design features
Finite Element Analysis (FEA)
FEA is a numerical simulation technique used to analyze the behavior of products under various loading conditions. In DFM analysis, FEA is used to:
- Evaluate the structural integrity of product designs
- Identify potential failure modes and weaknesses
- Optimize product designs for strength and durability
- Assess the impact of design changes on product performance
Design for Manufacturing and Assembly (DFMA) Software
DFMA software is specifically designed to analyze and optimize product designs for manufacturing and assembly. Key features of DFMA software include:
- Part count reduction analysis
- Assembly sequence optimization
- Manufacturing process selection and evaluation
- Cost estimation and comparison
Value Engineering
Value Engineering is a systematic approach to improving the value of products by optimizing the balance between function and cost. In DFM analysis, Value Engineering is used to:
- Identify and prioritize product functions
- Evaluate alternative design solutions
- Optimize product designs for cost and performance
- Collaborate with cross-functional teams to implement improvements
Best Practices for Implementing DFM Analysis
To successfully implement DFM analysis in your organization, consider the following best practices:
-
Integrate DFM analysis early in the product development process: Engaging in DFM analysis from the conceptual design phase allows for more significant opportunities to optimize product designs and minimize the risk of manufacturing issues.
-
Foster cross-functional collaboration: Encourage collaboration between design, engineering, manufacturing, and other relevant teams to ensure a comprehensive approach to DFM analysis.
-
Establish clear design guidelines and standards: Develop and communicate clear design guidelines and standards that incorporate DFM principles to ensure consistency and efficiency in product design.
-
Invest in training and education: Provide training and education to your team members on DFM principles, tools, and techniques to build organizational competency and foster a culture of continuous improvement.
-
Leverage technology and automation: Utilize CAD, FEA, DFMA, and other software tools to streamline and automate DFM analysis processes, enabling faster and more accurate results.
-
Monitor and measure performance: Establish key performance indicators (KPIs) to monitor and measure the effectiveness of your DFM analysis efforts, and use this data to drive continuous improvement.
Case Studies
To illustrate the practical application and benefits of DFM analysis, let’s explore a few case studies from different industries:
Automotive Industry
An automotive manufacturer implemented DFM analysis to optimize the design of a new engine component. By using DFMA software to analyze the initial design, the team identified opportunities to reduce the number of parts, simplify assembly processes, and optimize manufacturing processes. As a result, the company achieved:
- 25% reduction in part count
- 30% reduction in assembly time
- 15% reduction in manufacturing costs
- Improved engine performance and reliability
Consumer Electronics
A consumer electronics company applied DFM analysis to the design of a new smartphone. By collaborating with manufacturing experts and using CAD and FEA tools, the team optimized the phone’s design for manufacturability, durability, and cost-effectiveness. The results included:
- 20% reduction in manufacturing costs
- Improved phone durability and drop test performance
- Faster time-to-market due to fewer design iterations
- Enhanced customer satisfaction and brand reputation
Medical Devices
A medical device manufacturer used DFM analysis to optimize the design of a new surgical instrument. By engaging in Value Engineering and leveraging DFMA principles, the team developed a design that was easier to manufacture, assemble, and sterilize. The benefits realized included:
- 35% reduction in component costs
- Streamlined assembly processes, reducing assembly time by 40%
- Improved instrument ergonomics and user experience
- Faster regulatory approval due to robust design and manufacturing processes
Future Trends in DFM Analysis
As technology and manufacturing processes continue to evolve, DFM analysis will likely experience several trends and advancements in the coming years. Some of these future trends may include:
-
Increased adoption of AI and machine learning: AI and machine learning algorithms will be increasingly used to analyze large amounts of design and manufacturing data, enabling more accurate and efficient DFM analysis.
-
Greater integration with additive manufacturing: As additive manufacturing (3D printing) becomes more prevalent, DFM analysis will need to adapt to the unique design freedoms and constraints associated with these processes.
-
Enhanced virtual prototyping and simulation: Advancements in virtual prototyping and simulation technologies will allow for more comprehensive and accurate DFM analysis, reducing the need for physical prototypes.
-
Expansion of DFM principles to new industries: DFM analysis will continue to expand into new industries and applications, such as renewable energy, space exploration, and personalized healthcare.
-
Emphasis on sustainability and circular economy: DFM analysis will increasingly focus on designing products for sustainability, recyclability, and the circular economy, driving the development of more environmentally friendly products and processes.
Frequently Asked Questions (FAQ)
- What is the difference between DFM and DFMA?
-
DFM (Design for Manufacturability) focuses on optimizing product design for efficient manufacturing processes, while DFMA (Design for Manufacturing and Assembly) encompasses both manufacturing and assembly considerations.
-
At what stage of the product development process should DFM analysis be implemented?
-
DFM analysis should be integrated as early as possible in the product development process, ideally from the conceptual design phase, to maximize opportunities for design optimization and cost reduction.
-
What are some common design changes that result from DFM analysis?
-
Common design changes resulting from DFM analysis include part count reduction, simplification of geometries, optimization of tolerances, and selection of alternative materials or manufacturing processes.
-
How does DFM analysis impact product quality and reliability?
-
By optimizing product designs for manufacturability and identifying potential failure modes, DFM analysis helps improve product quality and reliability, ultimately leading to enhanced customer satisfaction and brand reputation.
-
What skills and expertise are required for effective DFM analysis?
- Effective DFM analysis requires a combination of skills and expertise, including knowledge of product design principles, manufacturing processes, materials science, and cost analysis. Cross-functional collaboration and communication skills are also essential for successful DFM implementation.
Conclusion
Design for Manufacturing (DFM) analysis is a powerful approach to optimizing product design for efficient, cost-effective manufacturing. By integrating DFM principles early in the product development process and leveraging tools such as CAD, FEA, and DFMA software, organizations can reduce costs, improve quality, and accelerate time-to-market.
Successful implementation of DFM analysis requires cross-functional collaboration, clear design guidelines, and a commitment to continuous improvement. As technology and manufacturing processes continue to evolve, DFM analysis will remain a critical component of product development, driving innovation and competitiveness in a wide range of industries.
By embracing DFM analysis and adopting best practices, organizations can unlock significant benefits and position themselves for long-term success in an increasingly competitive global marketplace.
No responses yet