Introduction to PCB thermal management
Printed circuit boards (PCBs) are the backbone of modern electronics, providing a platform for integrating and interconnecting various components. As electronic devices become more compact and powerful, managing heat dissipation becomes a critical factor in ensuring reliable performance and longevity. This article delves into the world of PCB thermodynamics, exploring the fundamentals of heat transfer, thermal analysis techniques, and best practices for effective thermal management.
Understanding Heat Transfer in PCBs
Conduction, Convection, and Radiation
Heat transfer in PCBs occurs through three primary mechanisms: conduction, convection, and radiation. Conduction is the transfer of heat through direct contact between materials, such as from a component to the PCB substrate. Convection involves the transfer of heat through a fluid medium, such as air or liquid coolants. Radiation is the emission of heat in the form of electromagnetic waves, which becomes significant at high temperatures.
Thermal Conductivity of PCB Materials
The choice of PCB materials plays a crucial role in heat dissipation. The thermal conductivity of the substrate, copper layers, and solder mask affects the overall thermal performance of the PCB. Common PCB substrate materials and their thermal conductivities are listed in the table below:
Material | Thermal Conductivity (W/mK) |
---|---|
FR-4 | 0.3 – 0.4 |
Polyimide | 0.2 – 0.3 |
Aluminum | 150 – 200 |
Copper | 385 – 400 |
Selecting materials with higher thermal conductivity can enhance heat dissipation and improve the overall thermal performance of the PCB.
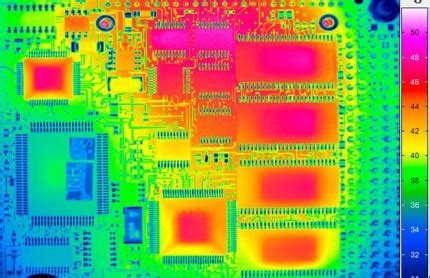
Thermal Analysis Techniques
Finite Element Analysis (FEA)
Finite Element Analysis (FEA) is a powerful numerical method for studying the thermal behavior of PCBs. It involves dividing the PCB into smaller elements and solving heat transfer equations for each element. FEA software tools, such as ANSYS and SolidWorks, enable engineers to create detailed 3D models of PCBs, assign material properties, and simulate heat flow under various operating conditions.
Computational Fluid Dynamics (CFD)
Computational Fluid Dynamics (CFD) is a technique used to analyze the airflow and convective heat transfer in and around PCBs. CFD software, such as Fluent and FloTHERM, solve the Navier-Stokes equations to predict fluid motion and heat transfer. By simulating airflow patterns, engineers can optimize the placement of components, heatsinks, and cooling fans to enhance convective cooling.
Thermal Imaging
Thermal imaging, also known as infrared thermography, is a non-contact method for visualizing the temperature distribution on a PCB. Thermal cameras detect infrared radiation emitted by objects and convert it into a color-coded image, with hotter regions appearing brighter. Thermal imaging is useful for identifying hot spots, evaluating the effectiveness of cooling solutions, and detecting potential thermal issues during testing and debugging.
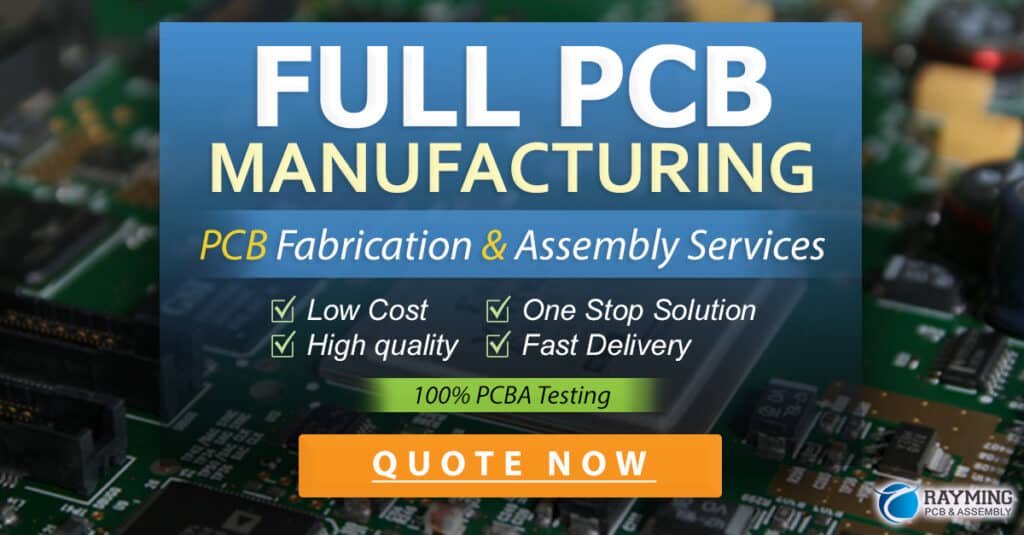
Thermal Design Considerations
Component Placement and Spacing
Proper component placement and spacing are essential for effective heat dissipation. High-power components, such as processors and power regulators, should be placed away from heat-sensitive components to minimize thermal interactions. Adequate spacing between components allows for better airflow and reduces the risk of localized hotspots.
Thermal Vias and Copper Pours
Thermal vias are plated through-holes that provide a low-resistance path for heat to flow from the component to the PCB’s internal or external layers. Strategically placing thermal vias near high-power components helps dissipate heat more efficiently. Copper pours, which are large areas of copper on the PCB surface, also aid in heat spreading and improve the overall thermal conductivity of the board.
Heatsinks and Cooling Solutions
Heatsinks are passive cooling devices that increase the surface area for heat dissipation. They are commonly used on high-power components, such as processors and voltage regulators. Heatsinks come in various shapes and sizes, including finned, pin-fin, and extruded designs. The choice of heatsink depends on factors such as the component’s power dissipation, available space, and airflow conditions.
Active cooling solutions, such as fans and liquid cooling systems, can further enhance heat dissipation. Fans provide forced convection, increasing airflow over the PCB and heatsinks. Liquid cooling systems, which use a circulating coolant to absorb and remove heat, are more advanced and typically used in high-performance applications.
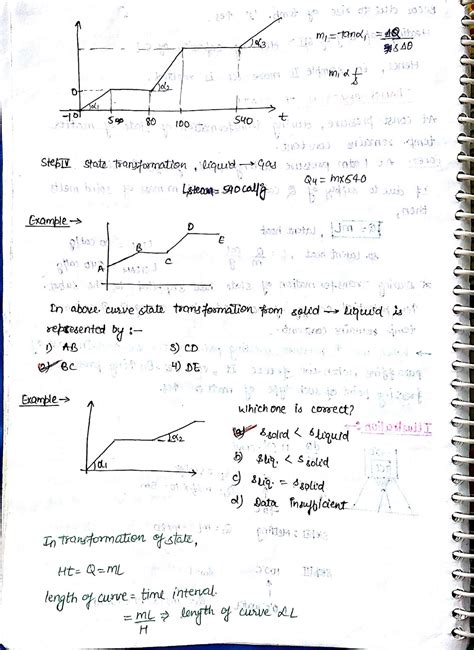
Thermal Testing and Validation
Temperature Measurement Techniques
Accurate temperature measurement is crucial for validating thermal designs and ensuring the PCB operates within safe limits. Various techniques can be employed, including:
- Thermocouples: These are temperature sensors that consist of two dissimilar metals joined at one end. They generate a voltage proportional to the temperature difference between the junction and the reference point.
- Resistance Temperature Detectors (RTDs): RTDs are sensors that measure temperature based on the change in electrical resistance of a metal, typically platinum, with temperature.
- Infrared thermometers: These non-contact devices measure the infrared radiation emitted by an object and convert it into a temperature reading.
Thermal Cycling and Stress Testing
Thermal cycling and stress testing are used to evaluate the reliability and long-term performance of PCBs under varying temperature conditions. Thermal cycling involves subjecting the PCB to repeated cycles of heating and cooling to simulate real-world temperature fluctuations. Stress testing involves operating the PCB at elevated temperatures for an extended period to assess its ability to withstand extreme conditions.
Thermal Design Optimization
Based on the results of thermal analysis and testing, engineers may need to optimize the PCB design to improve thermal performance. This can involve adjusting component placement, adding or modifying thermal vias and copper pours, selecting different materials, or incorporating advanced cooling solutions. Iterative design and analysis cycles are often necessary to achieve the desired thermal performance.
Best Practices for PCB Thermal Management
Design for Manufacturability (DFM)
Designing PCBs with manufacturability in mind is essential for ensuring reliable thermal performance. This includes considerations such as minimum trace widths and spacing, via sizes, and soldermask clearances. Adhering to DFM guidelines helps ensure consistent and repeatable manufacturing processes, reducing the risk of thermal issues caused by manufacturing defects.
Collaboration and Communication
Effective thermal management requires collaboration and communication among various stakeholders, including PCB designers, thermal engineers, mechanical engineers, and manufacturing teams. Early involvement of thermal experts in the design process can help identify potential issues and optimize the design for thermal performance. Clear communication of thermal requirements, constraints, and test results is essential for successful project execution.
Continuous Monitoring and Maintenance
Thermal management is an ongoing process that extends beyond the initial design and manufacturing stages. Continuous monitoring of PCB temperatures during operation can help detect potential issues and prevent failures. Regular maintenance, such as cleaning heatsinks and fans, ensures optimal cooling performance over time.
Frequently Asked Questions (FAQ)
1. What is the most important factor in PCB thermal management?
The most important factor in PCB thermal management is the effective dissipation of heat generated by components. This requires a combination of proper component placement, selection of materials with appropriate thermal properties, and the use of cooling solutions such as heatsinks and fans.
2. How can I identify thermal hotspots on a PCB?
Thermal hotspots can be identified using thermal imaging cameras or by placing temperature sensors, such as thermocouples or RTDs, at critical locations on the PCB. Finite Element Analysis (FEA) and Computational Fluid Dynamics (CFD) simulations can also help predict potential hotspots during the design phase.
3. What is the role of thermal vias in PCB design?
Thermal vias are plated through-holes that provide a low-resistance path for heat to flow from components to the PCB’s internal or external layers. They help dissipate heat more efficiently by increasing the thermal conductivity between layers and allowing heat to spread across a larger area.
4. How do I select the appropriate heatsink for a component?
The selection of a heatsink depends on factors such as the component’s power dissipation, available space, and airflow conditions. Heatsink manufacturers often provide thermal resistance data and selection guides to help choose the appropriate heatsink based on the specific application requirements.
5. What are the consequences of poor thermal management in PCBs?
Poor thermal management can lead to various issues, including reduced component lifespan, decreased performance, and even complete system failure. Overheating can cause components to operate outside their specified temperature range, leading to increased leakage currents, altered electrical characteristics, and accelerated aging. In extreme cases, excessive temperatures can cause permanent damage to components and pose safety hazards.
Conclusion
Effective thermal management is crucial for ensuring the reliability, performance, and longevity of PCBs. By understanding the principles of heat transfer, utilizing thermal analysis techniques, and implementing best practices in design and manufacturing, engineers can optimize PCBs for efficient heat dissipation. From material selection to component placement and cooling solutions, every aspect of PCB design plays a role in thermal management.
As electronic devices continue to push the boundaries of performance and miniaturization, the importance of thermal management will only continue to grow. By staying up-to-date with the latest technologies, tools, and techniques in PCB thermodynamics, engineers can overcome thermal challenges and create robust, reliable electronic systems that meet the demands of today and tomorrow.
No responses yet