The Importance of cEDM in the Modern Electronics Industry
The electronics industry is rapidly evolving, with new technologies and consumer demands emerging at an unprecedented pace. To remain competitive in this dynamic landscape, companies must adopt efficient and flexible design and manufacturing processes. cEDM addresses these challenges by providing a comprehensive framework for electronics development, enabling organizations to:
- Accelerate product development cycles
- Enhance product quality and reliability
- Reduce manufacturing costs
- Improve collaboration among teams
- Respond quickly to market changes and customer needs
Key Components of cEDM
1. Electronics Design
The foundation of cEDM lies in the design phase, where engineers create the schematics, layouts, and 3D models of electronic devices. This stage involves several key aspects:
a. Schematic Design
Schematic design is the process of creating a diagram that represents the electrical connections and components of a device. Engineers use specialized software, such as Altium Designer or OrCAD, to create detailed schematics that serve as the blueprint for the entire project.
b. PCB Layout Design
Once the schematic is complete, engineers move on to the PCB (Printed Circuit Board) layout design. This involves arranging the components on the board and routing the electrical connections between them. Proper PCB layout is crucial for ensuring the device’s functionality, reliability, and manufacturability.
c. 3D Modeling
In addition to the schematic and PCB layout, engineers create 3D models of the device to visualize its physical structure and enclosure. This helps in assessing the mechanical fit and identifying potential design issues early in the development process.
2. Prototyping and Testing
After the design phase, cEDM emphasizes the importance of prototyping and testing to validate the device’s functionality and performance. This stage includes:
a. Prototype Fabrication
Engineers create physical prototypes of the device using various methods, such as 3D printing, CNC Machining, or rapid PCB Prototyping. These prototypes allow for hands-on testing and evaluation of the design.
b. Functional Testing
Prototypes undergo rigorous functional testing to ensure they meet the specified requirements. This includes testing individual components, subsystems, and the complete device under various operating conditions.
c. Compliance Testing
Electronic devices must comply with various industry standards and regulations, such as FCC, CE, and RoHS. cEDM incorporates compliance testing to ensure the device meets these requirements before moving to mass production.
3. Manufacturing
Once the design is finalized and tested, cEDM focuses on the manufacturing process to ensure efficient and cost-effective production. This stage involves:
a. Supply Chain Management
Effective supply chain management is essential for ensuring a steady flow of components and materials needed for production. cEDM emphasizes the importance of establishing strong relationships with suppliers and implementing robust inventory management systems.
b. Assembly Processes
cEDM optimizes the assembly processes to maximize efficiency and minimize errors. This includes implementing automated assembly lines, using advanced manufacturing techniques like surface mount technology (SMT), and employing lean manufacturing principles.
c. Quality Control
Strict quality control measures are integrated throughout the manufacturing process to ensure the produced devices meet the required standards. This includes in-line inspections, functional testing, and statistical process control (SPC) to identify and address any issues promptly.
Benefits of Adopting cEDM
Implementing cEDM offers numerous benefits to electronics companies, enabling them to:
- Reduce development time and costs
- Improve product quality and reliability
- Enhance collaboration among design, engineering, and manufacturing teams
- Increase flexibility and adaptability to market changes
- Maximize production efficiency and minimize waste
By adopting cEDM, organizations can streamline their electronics development processes, resulting in a competitive advantage in the fast-paced electronics industry.
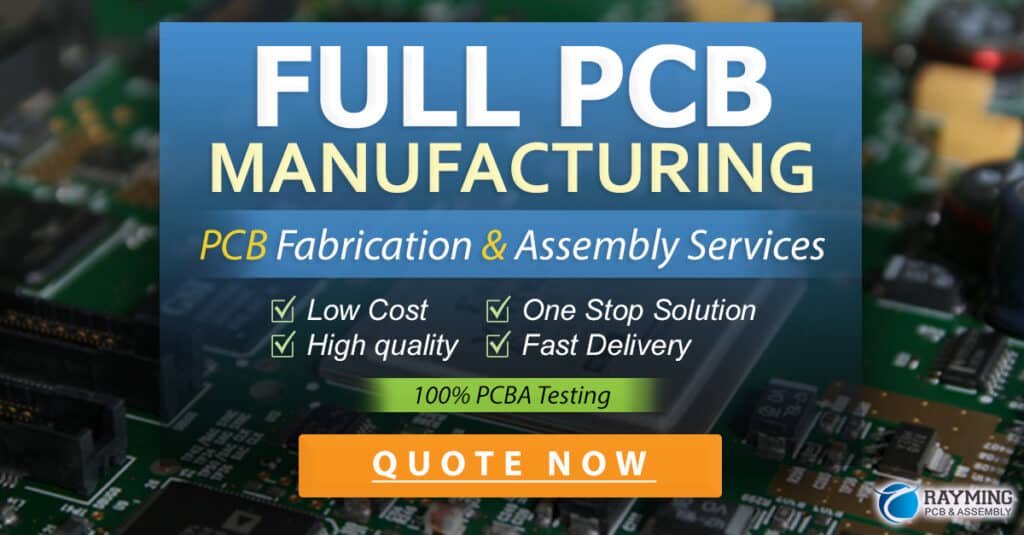
Real-World Applications of cEDM
cEDM has been successfully applied in various sectors of the electronics industry, including:
- Consumer Electronics
- Smartphones
- Wearable devices
-
Smart home appliances
-
Automotive Electronics
- In-vehicle infotainment systems
- Advanced driver assistance systems (ADAS)
-
Electric vehicle (EV) components
-
Medical Devices
- Diagnostic equipment
- Wearable health monitors
-
Implantable devices
-
Industrial Automation
- Programmable logic controllers (PLCs)
- Sensors and actuators
- Industrial IoT devices
These are just a few examples of how cEDM has been successfully implemented across various industries, demonstrating its versatility and effectiveness in electronics design and manufacturing.
Challenges and Future Trends in cEDM
While cEDM offers numerous benefits, there are also challenges that organizations must address when implementing this approach:
- Keeping pace with rapidly evolving technologies
- Ensuring data security and intellectual property protection
- Managing complex supply chains and logistics
- Adapting to changing regulatory requirements
To overcome these challenges and stay ahead of the curve, organizations must continuously monitor and adapt to emerging trends in cEDM, such as:
- Increased adoption of AI and machine learning in design and manufacturing processes
- Growing emphasis on sustainability and eco-friendly practices
- Expansion of Industry 4.0 technologies, such as IoT, cloud computing, and big data analytics
- Continued miniaturization and integration of electronic components
By staying informed about these trends and incorporating them into their cEDM strategies, electronics companies can remain competitive and drive innovation in the industry.
Frequently Asked Questions (FAQ)
- What is cEDM, and how does it differ from traditional electronics design and manufacturing processes?
-
cEDM is a comprehensive approach to electronics design and manufacturing that integrates various aspects of the development process, from initial concept to final production. It differs from traditional processes by emphasizing collaboration, flexibility, and efficiency throughout the entire product lifecycle.
-
What are the key components of cEDM?
-
The key components of cEDM are electronics design (schematic design, PCB layout, and 3D modeling), prototyping and testing (prototype fabrication, functional testing, and compliance testing), and manufacturing (supply chain management, assembly processes, and quality control).
-
What industries can benefit from adopting cEDM?
-
cEDM can be applied in various sectors of the electronics industry, including consumer electronics, automotive electronics, medical devices, and industrial automation.
-
How can organizations overcome the challenges associated with implementing cEDM?
-
To overcome challenges such as keeping pace with evolving technologies, ensuring data security, managing complex supply chains, and adapting to regulatory requirements, organizations must continuously monitor and adapt to emerging trends in cEDM, such as AI, sustainability, Industry 4.0 technologies, and miniaturization.
-
What are the future trends in cEDM that electronics companies should be aware of?
- Future trends in cEDM include increased adoption of AI and machine learning, growing emphasis on sustainability and eco-friendly practices, expansion of Industry 4.0 technologies, and continued miniaturization and integration of electronic components. By staying informed about these trends, electronics companies can remain competitive and drive innovation in the industry.
cEDM Component | Key Aspects |
---|---|
Electronics Design | – Schematic Design – PCB Layout Design – 3D Modeling |
Prototyping and Testing | – Prototype Fabrication – Functional Testing – Compliance Testing |
Manufacturing | – Supply Chain Management – Assembly Processes – Quality Control |
Table 1: Key components and aspects of cEDM
In conclusion, cEDM is a powerful approach to electronics design and manufacturing that enables organizations to streamline their development processes, improve product quality, and reduce costs. By adopting cEDM and staying informed about emerging trends, electronics companies can remain competitive and drive innovation in the rapidly evolving electronics industry.
No responses yet