Introduction to CCA Electronics
CCA (Circuit Card Assembly) electronics refer to the process of designing, manufacturing, and assembling electronic circuits on a printed circuit board (PCB). This process is critical in the production of various electronic devices, ranging from smartphones and computers to medical equipment and automotive systems. In this comprehensive guide, we will explore essential tips and procedural guidance to help you navigate the world of CCA electronics effectively.
The Importance of Proper PCB Design
Choosing the Right PCB Material
When designing a PCB for your CCA electronics project, selecting the appropriate material is crucial. The most common PCB materials include:
- FR-4: A popular choice for its affordability and durability
- High-Frequency Laminates: Ideal for high-speed applications
- Aluminum-backed PCBs: Suitable for heat dissipation in power electronics
Consider factors such as the operating environment, required performance, and budget when choosing the PCB material.
Optimizing Component Placement
Proper component placement on the PCB is essential for several reasons:
- Signal Integrity: Place components to minimize signal path lengths and crosstalk
- Thermal Management: Position heat-generating components to facilitate efficient heat dissipation
- Manufacturing Efficiency: Group similar components together to streamline the assembly process
Use PCB design software to optimize component placement and ensure adherence to design rules.
Implementing Effective Grounding Techniques
Proper grounding is vital for the stability and performance of CCA electronics. Follow these tips for effective grounding:
- Use ground planes to provide a low-impedance return path for signals
- Implement a star grounding topology to minimize ground loops
- Separate analog and digital grounds to reduce noise interference
Regularly review your grounding scheme to identify and resolve potential issues.
CCA Assembly Best Practices
Solder Paste Application
Applying solder paste accurately is critical for achieving reliable solder joints. Consider these tips:
- Use a laser-cut or electroformed stencil for precise solder paste deposition
- Regularly calibrate the solder paste printer to maintain consistency
- Monitor solder paste viscosity and replace it as necessary
Implementing a robust solder paste inspection process can help identify and correct issues early in the assembly process.
Component Placement Techniques
Accurate component placement is essential for ensuring proper functionality and reliability. Follow these guidelines:
- Use a pick-and-place machine for high-speed, precise component placement
- Implement machine vision systems to verify component presence and orientation
- Regularly calibrate the placement machine to maintain accuracy
Proper operator training and adherence to standard operating procedures (SOPs) can further enhance placement accuracy.
Reflow Soldering Optimization
Reflow soldering is a critical step in the CCA assembly process. Optimize your reflow soldering process by:
- Selecting the appropriate reflow profile based on the PCB and component characteristics
- Monitoring oven temperature and conveyor speed to ensure consistency
- Implementing a nitrogen atmosphere to reduce oxidation and improve solder joint quality
Regular maintenance and calibration of the reflow oven are essential for maintaining optimal performance.
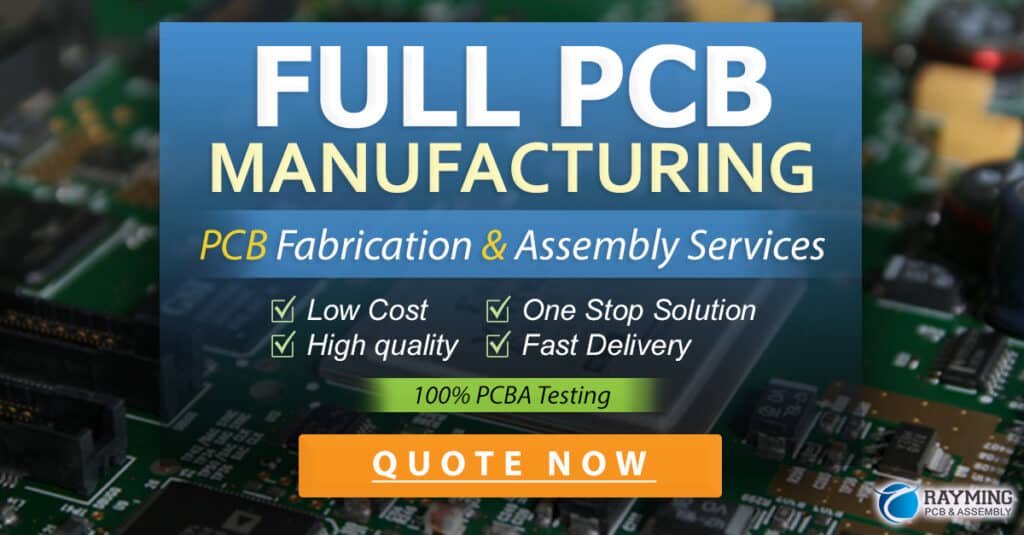
Quality Control and Testing
In-Circuit Testing (ICT)
ICT is a powerful tool for identifying manufacturing defects and ensuring product quality. Consider these tips:
- Develop comprehensive test coverage to detect potential faults
- Use a bed-of-nails fixture to provide reliable contact with test points
- Integrate ICT into your manufacturing process for early defect detection
Regularly review and update your ICT program to accommodate design changes and improve test effectiveness.
Functional Testing
Functional testing verifies that the assembled CCA performs as intended. Follow these guidelines:
- Develop a comprehensive test plan based on product requirements and specifications
- Use automated test equipment (ATE) to streamline the testing process
- Implement boundary scan testing for complex digital circuits
Establish clear pass/fail criteria and maintain detailed test records for traceability and continuous improvement.
Burn-In Testing
Burn-in testing involves subjecting the CCA to elevated temperatures and operating conditions to identify early-life failures. Consider these tips:
- Determine the appropriate burn-in duration and conditions based on product reliability requirements
- Use specialized burn-in chambers to maintain consistent environmental conditions
- Monitor device performance during burn-in to detect potential issues
Regularly analyze burn-in test data to identify trends and implement corrective actions as necessary.
Troubleshooting Common CCA Issues
Solder Joint Defects
Solder joint defects, such as bridging, tombstoning, and insufficient solder, can lead to reliability issues. Address these defects by:
- Optimizing the reflow soldering process parameters
- Ensuring proper solder paste application and component placement
- Implementing automated optical inspection (AOI) to detect solder joint defects
Conduct root cause analysis to identify and address the underlying causes of solder joint defects.
Electrostatic Discharge (ESD) Damage
ESD can cause latent damage to sensitive electronic components. Prevent ESD damage by:
- Implementing an ESD-safe work environment, including grounded workstations and flooring
- Using ESD-safe packaging materials for storage and transportation
- Providing regular ESD training for personnel
Regularly audit your ESD control program to ensure ongoing effectiveness.
Thermal Management Challenges
Inadequate thermal management can lead to component overheating and premature failure. Address thermal management challenges by:
- Conducting thermal simulations during the design phase to identify potential hot spots
- Selecting components with appropriate power ratings and thermal characteristics
- Implementing efficient heat dissipation techniques, such as heatsinks and thermal interface materials
Monitor device temperatures during operation and take corrective action if necessary.
Frequently Asked Questions (FAQ)
- What is the difference between through-hole and surface-mount technology (SMT)?
-
Through-hole technology involves inserting component leads through holes in the PCB and soldering them on the opposite side. SMT components are mounted directly onto the PCB surface, allowing for higher component density and smaller device sizes.
-
How can I prevent moisture-related issues in CCA electronics?
-
Moisture can cause component failure and delamination. Prevent moisture-related issues by using moisture-sensitive device (MSD) packaging, implementing proper storage and handling procedures, and baking components before assembly if necessary.
-
What is the purpose of conformal coating in CCA electronics?
-
Conformal coating is a protective layer applied to the PCB and components to prevent moisture, dust, and other contaminants from causing damage or corrosion. It is particularly useful in harsh operating environments.
-
How do I select the appropriate solder alloy for my CCA application?
-
The choice of solder alloy depends on factors such as the required melting temperature, mechanical strength, and environmental compatibility. Common alloys include tin-lead (SnPb) and lead-free alternatives like tin-silver-copper (SAC).
-
What are some best practices for rework and repair of CCA electronics?
- When reworking or repairing CCA electronics, use appropriate tools and techniques to minimize damage to the PCB and components. This includes using a temperature-controlled soldering iron, applying flux to promote solder wetting, and following ESD-safe practices. Properly document all rework and repair activities for traceability.
Conclusion
CCA electronics play a vital role in the modern world, enabling the development of increasingly sophisticated and reliable electronic devices. By following the tips and procedural guidance outlined in this article, you can enhance the quality, reliability, and performance of your CCA electronics projects. Remember to prioritize proper PCB design, optimize assembly processes, implement robust quality control measures, and stay informed about the latest industry trends and best practices. With dedication and attention to detail, you can unlock the full potential of CCA electronics in your applications.
References
- IPC-A-610: Acceptability of Electronic Assemblies
- IPC-J-STD-001: Requirements for Soldered Electrical and Electronic Assemblies
- IPC-7711/7721: Rework, Modification, and Repair of Electronic Assemblies
Word count: 1298
No responses yet