Introduction to Capacitor Film
Capacitor film is a crucial component in the world of electronics, playing a vital role in various applications ranging from energy storage to signal processing. This article delves into the intricacies of capacitor film, exploring its properties, construction, and diverse applications.
What is Capacitor Film?
Capacitor film is a thin, flexible dielectric material used in the construction of capacitors. It serves as an insulating layer between the conductive plates of a capacitor, allowing the device to store electrical energy in the form of an electrostatic field.
Key Properties of Capacitor Film
The properties of capacitor film greatly influence the performance and characteristics of the resulting capacitors. Some of the essential properties include:
-
Dielectric Constant: The dielectric constant, also known as relative permittivity, is a measure of a material’s ability to store electrical energy. A higher dielectric constant allows for greater capacitance in a given volume.
-
Dielectric Strength: Dielectric strength refers to the maximum electric field a material can withstand before breakdown occurs. Films with high dielectric strength enable capacitors to operate at higher voltages without failure.
-
Dissipation Factor: The dissipation factor, or tan δ, represents the energy loss in a capacitor due to the dielectric material. A lower dissipation factor indicates better efficiency and lower power loss.
-
Temperature Stability: Capacitor film should maintain its properties over a wide temperature range to ensure reliable performance in various operating conditions.
-
Mechanical Strength: The film must possess sufficient mechanical strength to withstand the stresses encountered during capacitor manufacturing and operation.
Types of Capacitor Film
Several types of capacitor film are commonly used, each with unique properties and advantages. The choice of film depends on the specific requirements of the application.
Polypropylene (PP) Film
Polypropylene film is widely used in capacitors due to its excellent electrical properties and low cost. It offers a high dielectric constant, low dissipation factor, and good temperature stability.
Polyethylene Terephthalate (PET) Film
PET film, also known as polyester film, is another popular choice for capacitors. It provides high dielectric strength, good mechanical properties, and excellent moisture resistance.
Polyphenylene Sulfide (PPS) Film
PPS film is known for its exceptional thermal stability and resistance to high temperatures. It is well-suited for applications requiring reliable performance in harsh environments.
Polytetrafluoroethylene (PTFE) Film
PTFE film, commonly known as Teflon, offers superior chemical resistance and low dielectric loss. It is often used in high-frequency and high-voltage applications.
Construction of Capacitor Film
The construction of capacitor film involves several key steps to ensure the desired properties and performance.
Film Extrusion
The first step in capacitor film production is the extrusion process. The chosen polymer material is melted and extruded through a die to form a thin, continuous film. The film thickness is precisely controlled to achieve the desired capacitance and voltage rating.
Metallization
To create the conductive plates of the capacitor, a thin layer of metal, typically aluminum or zinc, is deposited onto the film surface through a process called metallization. This can be done using techniques such as vacuum deposition or sputtering.
Winding
The metallized film is wound into a cylindrical or flat shape, with the metallized surfaces acting as the capacitor’s electrodes. The winding process must ensure proper alignment and tension to prevent defects and maintain consistent performance.
Encapsulation
Finally, the wound capacitor element is encapsulated in a protective housing, such as a plastic case or epoxy resin. The encapsulation provides mechanical support, insulation, and protection against environmental factors.
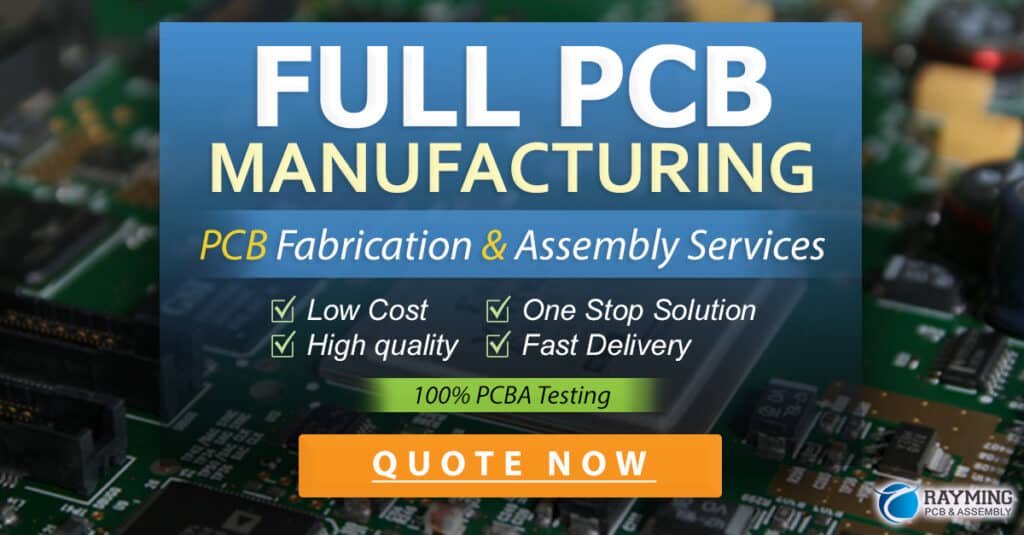
Applications of Capacitor Film
Capacitor film finds extensive use in various electronic applications due to its versatility and performance.
Power Electronics
In power electronics, capacitor film is employed in DC link capacitors, snubber capacitors, and filtering capacitors. These capacitors help smooth voltage ripples, suppress transients, and improve overall system efficiency.
Motor Run Capacitors
Motor run capacitors, constructed using capacitor film, are essential components in single-phase AC motors. They provide a phase shift between the main and auxiliary windings, enabling the motor to start and run efficiently.
Audio and Video Equipment
Capacitor film is used in coupling and decoupling capacitors in audio and video equipment. These capacitors help block DC components, reduce noise, and ensure clean signal transmission.
Automotive Electronics
In automotive electronics, capacitor film is utilized in various applications such as ignition systems, engine control units, and infotainment systems. The film’s reliability and temperature stability are crucial in the harsh automotive environment.
Medical Devices
Capacitor film is employed in medical devices like defibrillators, pacemakers, and monitoring equipment. The film’s high dielectric strength and low leakage current ensure safe and reliable operation in these critical applications.
Frequently Asked Questions (FAQ)
1. What is the difference between capacitor film and other dielectric materials?
Capacitor film is a thin, flexible dielectric material specifically designed for use in capacitors. It offers a combination of desirable properties such as high dielectric constant, low dissipation factor, and good temperature stability. Other dielectric materials, such as ceramics or electrolytes, may have different characteristics and are used in different types of capacitors.
2. Can capacitor film be used in high-voltage applications?
Yes, certain types of capacitor film, such as polypropylene (PP) and polyethylene terephthalate (PET), have high dielectric strength and can withstand high voltages. However, the specific voltage rating depends on the film thickness and the capacitor’s construction. It’s important to choose the appropriate film and design for the intended voltage level.
3. How does the choice of capacitor film affect the capacitor’s performance?
The choice of capacitor film greatly influences the capacitor’s performance characteristics. Different films have varying dielectric constants, dissipation factors, temperature stability, and mechanical properties. For example, polypropylene film offers a high dielectric constant and low dissipation factor, making it suitable for high-frequency applications. On the other hand, polyphenylene sulfide (PPS) film excels in high-temperature environments due to its thermal stability.
4. What are the advantages of using metallized capacitor film?
Metallized capacitor film offers several advantages over traditional foil-based capacitors. The metallization process allows for thinner conductive layers, resulting in higher capacitance density and reduced size. Metallized film capacitors also have self-healing properties, where localized dielectric breakdowns can be isolated without causing complete failure. Additionally, metallized film capacitors often have lower equivalent series resistance (ESR) and improved high-frequency performance.
5. How do I select the appropriate capacitor film for my application?
Selecting the appropriate capacitor film depends on the specific requirements of your application. Consider factors such as the desired capacitance value, voltage rating, operating temperature range, frequency response, and environmental conditions. Consult the datasheets and specifications provided by capacitor manufacturers to compare the properties of different film types. It’s also advisable to seek guidance from experienced engineers or capacitor suppliers to ensure the optimal choice for your specific needs.
Conclusion
Capacitor film plays a vital role in the construction and performance of capacitors, enabling their widespread use in various electronic applications. Understanding the properties, types, and construction of capacitor film is essential for designing and selecting capacitors that meet the specific requirements of a given application.
With ongoing advancements in material science and manufacturing techniques, capacitor film technology continues to evolve, offering improved performance, reliability, and miniaturization. As electronic devices become increasingly sophisticated and demanding, the importance of capacitor film in enabling innovative solutions cannot be overstated.
By exploring the intricacies of capacitor film, we gain a deeper appreciation for the critical role it plays in the world of electronics. From power electronics to medical devices, capacitor film underpins the functionality and reliability of countless systems that shape our modern world.
Film Type | Dielectric Constant | Dielectric Strength (kV/mm) | Dissipation Factor (Tan δ) | Temperature Range (°C) |
---|---|---|---|---|
Polypropylene (PP) | 2.2 – 2.4 | 200 – 400 | 0.0002 – 0.0005 | -55 to +105 |
Polyethylene Terephthalate (PET) | 3.0 – 3.2 | 300 – 500 | 0.002 – 0.005 | -55 to +125 |
Polyphenylene Sulfide (PPS) | 3.0 – 3.2 | 200 – 300 | 0.001 – 0.003 | -55 to +200 |
Polytetrafluoroethylene (PTFE) | 2.0 – 2.1 | 60 – 200 | 0.0001 – 0.0003 | -55 to +200 |
Table: Properties of common capacitor film types
As we continue to push the boundaries of electronic technology, capacitor film will undoubtedly remain a fundamental building block, enabling us to store, filter, and manipulate electrical energy with unparalleled efficiency and precision. By embracing the potential of capacitor film and driving further research and development, we can unlock new possibilities and shape a future where electronics seamlessly integrate into every aspect of our lives.
No responses yet