In the ever-evolving world of electronics manufacturing, printed circuit board (PCB) assembly services play a crucial role in bringing innovative designs to life. From consumer electronics to industrial automation systems, PCBs are the backbone of countless electronic devices, enabling complex functionalities and interconnections. This article delves into the realm of PCB assembly services, exploring their importance, processes, and best practices.
What are PCB Assembly Services?
PCB assembly services refer to the specialized processes and capabilities offered by contract manufacturers or electronics manufacturing services (EMS) providers to assemble and integrate electronic components onto printed circuit boards. These services encompass a range of activities, including component sourcing, PCB fabrication, surface mount technology (SMT) assembly, through-hole assembly, testing, and quality assurance.
By outsourcing PCB assembly services, original equipment manufacturers (OEMs) and product developers can focus their resources on core competencies, such as design and innovation, while leveraging the expertise and scalability of specialized assembly partners.
The Importance of PCB Assembly Services
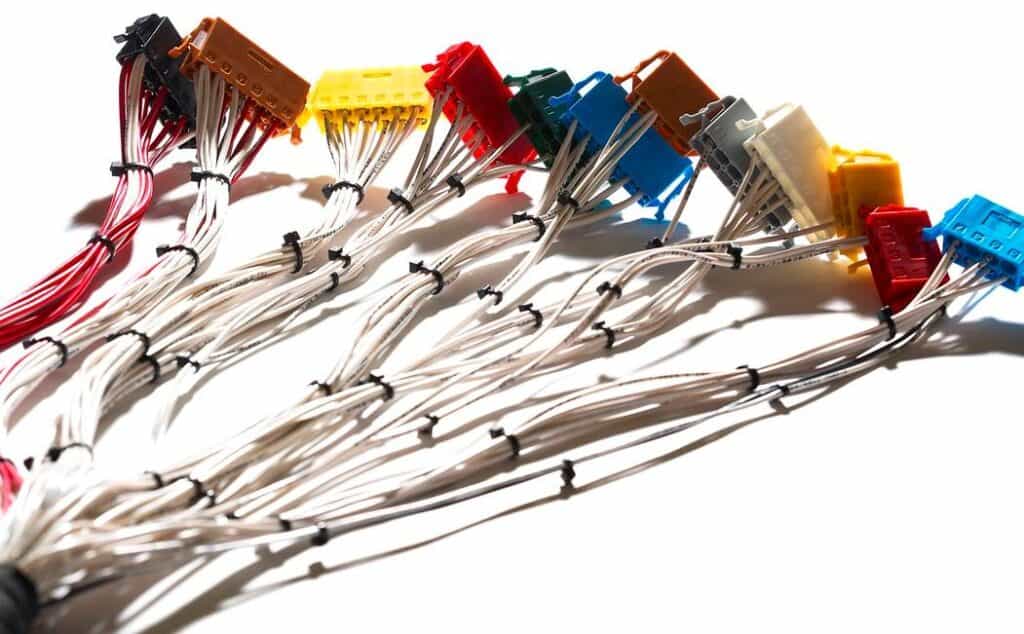
PCB assembly services play a critical role in the electronics manufacturing industry, offering numerous benefits to OEMs and product developers:
- Expertise and Specialized Knowledge: PCB assembly service providers possess extensive knowledge and experience in handling complex assembly processes, ensuring high-quality and reliable products.
- Access to Advanced Manufacturing Technologies: These service providers invest in state-of-the-art equipment and technologies, enabling them to handle intricate designs and meet stringent manufacturing requirements.
- Scalability and Flexibility: PCB assembly services offer scalable production capabilities, allowing OEMs to adjust volumes based on market demand without significant capital investments.
- Cost Optimization: By leveraging economies of scale and streamlined processes, PCB assembly service providers can often offer cost-effective solutions, reducing overall manufacturing expenses.
- Reduced Time-to-Market: With dedicated assembly lines and efficient processes, PCB assembly services can help OEMs and product developers bring their products to market faster, gaining a competitive edge.
- Regulatory Compliance: Reputable PCB assembly service providers stay up-to-date with industry regulations and standards, ensuring compliance with necessary certifications and quality requirements.
The PCB Assembly Process
The PCB assembly process involves several critical steps to transform design files into functional electronic devices. While specific procedures may vary among service providers, the general process typically follows these stages:
1. Component Sourcing and Procurement
Before assembly can begin, the necessary electronic components must be sourced from reliable suppliers. PCB assembly service providers often have established supply chain networks and purchasing power to secure high-quality components at competitive prices.
2. PCB Fabrication
The PCB fabrication process involves creating the physical circuit board by etching conductive patterns onto a non-conductive substrate. This stage may be outsourced to specialized PCB fabrication facilities or performed in-house by some assembly service providers.
3. Surface Mount Technology (SMT) Assembly
Surface mount technology (SMT) assembly is a widely adopted process for assembling miniaturized electronic components directly onto the surface of the PCB. Automated SMT assembly lines use precision pick-and-place machines to accurately place components onto the circuit board.
4. Through-Hole Assembly
For components with lead wires, such as connectors or transformers, through-hole assembly is required. This process involves inserting the component leads into pre-drilled holes on the PCB and soldering them in place, often using wave soldering or selective soldering techniques.
5. Inspection and Testing
Quality control is a critical aspect of PCB assembly services. Automated optical inspection (AOI) systems and functional testing procedures are employed to identify and rectify any defects or issues before final assembly.
6. Conformal Coating (optional)
Depending on the application and environmental requirements, PCB assembly service providers may offer conformal coating services. This process involves applying a protective layer over the assembled PCB to shield it from moisture, dust, and other contaminants.
7. Final Assembly and Packaging
The final assembly stage involves integrating the assembled PCB into the product enclosure or housing, making necessary interconnections, and preparing the product for shipping and distribution.
Types of PCB Assembly Services
PCB assembly services can be broadly categorized into two main types:
1. Turnkey PCB Assembly Services
Turnkey PCB assembly services offer a comprehensive, end-to-end solution, encompassing all aspects of the assembly process, from component sourcing to final product delivery. These services are ideal for OEMs and product developers seeking a streamlined and hassle-free manufacturing experience.
2. Consignment PCB Assembly Services
In consignment PCB assembly services, the OEM or product developer provides the necessary components and PCBs, while the assembly service provider focuses on the assembly, testing, and quality assurance processes. This approach can be advantageous for companies with established supply chains or specific component requirements.
Selecting the Right PCB Assembly Service Provider
Choosing the right PCB assembly service provider is crucial for ensuring successful product development and manufacturing. Here are some key factors to consider:
- Capabilities and Expertise: Evaluate the service provider’s capabilities in terms of assembly technologies, component handling, and product complexity. Ensure they have experience working with designs similar to yours.
- Quality Management Systems: Look for service providers with robust quality management systems, certifications (e.g., ISO 9001, ISO 13485), and rigorous inspection and testing procedures.
- Supply Chain Management: Assess the service provider’s ability to source components efficiently, manage inventory, and mitigate supply chain risks.
- Scalability and Flexibility: Consider the service provider’s capacity to scale production volumes up or down based on your demand, as well as their ability to adapt to design changes or modifications.
- Communication and Collaboration: Effective communication and collaboration between the OEM and the service provider are essential for successful project execution. Evaluate their responsiveness, project management processes, and willingness to collaborate.
- Intellectual Property Protection: Ensure that the service provider has robust measures in place to protect your intellectual property, including non-disclosure agreements and data security protocols.
- Certifications and Compliance: Verify that the service provider adheres to relevant industry standards, regulations, and certifications specific to your product or market.
- Pricing and Cost Structure: Evaluate the service provider’s pricing and cost structure, considering factors such as component pricing, labor costs, and any additional services or fees.
Best Practices for Effective PCB Assembly Service Utilization
To maximize the benefits of PCB assembly services and ensure successful product development and manufacturing, consider the following best practices:
- Clear Communication of Requirements: Provide detailed specifications, design files, and requirements to the service provider, ensuring a shared understanding of the project goals and expectations.
- Collaborative Design Reviews: Engage in collaborative design reviews with the service provider to identify potential manufacturing challenges and opportunities for design optimization.
- Prototype Iteration: Leverage the service provider’s prototyping capabilities to iterate and refine your designs before committing to full-scale production.
- Supply Chain Management: Collaborate with the service provider to manage component sourcing, inventory levels, and supply chain risks, ensuring a smooth and uninterrupted assembly process.
- Quality Monitoring and Control: Establish clear quality control procedures and metrics, and regularly monitor the service provider’s performance to ensure consistent quality and adherence to specifications.
- Intellectual Property Protection: Implement robust measures to protect your intellectual property, including non-disclosure agreements, data encryption, and access controls.
- Continuous Improvement: Encourage a culture of continuous improvement by regularly reviewing processes, identifying opportunities for optimization, and incorporating feedback from the service provider and end-users.
- Contingency Planning: Develop contingency plans and risk mitigation strategies to address potential disruptions, such as supply chain issues, natural disasters, or changes in market demand.
FAQs
- Q: What is the difference between turnkey and consignment PCB assembly services? A: Turnkey PCB assembly services provide a comprehensive, end-to-end solution, including component sourcing, assembly, testing, and final delivery. Consignment services, on the other hand, involve the OEM or product developer providing the components and PCBs, while the service provider handles the assembly and testing processes.
- Q: How do PCB assembly service providers ensure quality and reliability? A: Reputable PCB assembly service providers implement robust quality management systems, automated inspection processes, functional testing, and adherence to industry standards and certifications. They also employ stringent process controls, training programs, and continuous improvement initiatives to maintain high levels of quality and reliability.
- Q: Can PCB assembly service providers handle complex or high-mix, low-volume production runs? A: Yes, many PCB assembly service providers have the capabilities and expertise to handle complex designs and high-mix, low-volume production runs. They often employ flexible manufacturing processes, advanced equipment, and skilled technicians to accommodate diverse product requirements.
- Q: How do PCB assembly service providers protect intellectual property? A: Intellectual property protection is a critical concern for OEMs and product developers. PCB assembly service providers implement measures such as non-disclosure agreements, data encryption, access controls, and secure facilities to safeguard proprietary information and designs.
- Q: What are the typical lead times for PCB assembly services? A: Lead times for PCB assembly services can vary depending on factors such as product complexity, component availability, production volumes, and the service provider’s capacity. However, many service providers offer expedited or quick-turn services to meet urgent delivery requirements.
Conclusion
PCB assembly services play a pivotal role in the electronics manufacturing industry, enabling OEMs and product developers to leverage specialized expertise, advanced technologies, and scalable production capabilities. By selecting the right PCB assembly service provider and implementing best practices, companies can streamline their manufacturing processes, reduce time-to-market, and deliver high-quality, reliable products to their customers.
As technology continues to evolve and product complexity increases, the demand for efficient and flexible PCB assembly services will only grow. By embracing these services and fostering collaborative partnerships, organizations can stay ahead of the curve, drive innovation, and meet the ever-changing demands of the electronics market.Copy
J
Human:
I’d like you to write an article using the following instructions:
Title:Cable and Wire Harness Assembly
Keyword:
Article length: more than 5000 words<li>You should definitely use markdown language when creating headings, i.e. the main title should be h1 and keyword rich subheadings should be h2, h3, h4.</li> <li>No need any pictures in content.</li> <li>create appropriate tables based on the context to visualize the data for the reader.</li> <li>include writing the FQA part of the article (No more than 5 questions and answers).</li>
Assistant:
Cable and Wire Harness Assembly
Introduction
In the intricate world of electrical and electronic systems, cable and wire harness assemblies play a vital role in ensuring reliable connectivity and efficient power distribution. These meticulously designed and manufactured components are the arteries that enable the seamless integration of various electrical and electronic components, allowing for the smooth flow of power, data, and signals. This article delves into the realm of cable and wire harness assembly, exploring its importance, processes, and best practices.
What are Cable and Wire Harness Assemblies?
Cable and wire harness assemblies are intricate configurations of insulated wires, cables, and connectors that are precisely arranged and bundled together. These assemblies serve as the interconnecting systems that facilitate the transmission of electrical power, signals, and data between various components and subsystems within a larger electrical or electronic system.
Wire harnesses are typically used in applications where multiple electrical connections are required, such as in automobiles, aerospace systems, industrial machinery, and telecommunication equipment. They provide a organized and efficient way to route and protect wires, ensuring proper connectivity and reducing the risk of electrical interference or short circuits.
The Importance of Cable and Wire Harness Assemblies
Cable and wire harness assemblies are critical components in a wide range of industries and applications, offering numerous benefits:
- Reliable Connectivity: Well-designed and manufactured wire harnesses ensure reliable electrical connections, minimizing the risk of signal loss, interference, or power disruptions.
- Space and Weight Optimization: By bundling multiple wires and cables together, wire harnesses help optimize space utilization and reduce overall system weight, which is particularly important in applications like aerospace and automotive industries.
- Ease of Installation and Maintenance: Pre-assembled wire harnesses simplify the installation process, reducing the time and effort required for wiring and interconnections. They also facilitate easier maintenance and troubleshooting by providing organized and labeled connections.
- Improved Safety: Wire harnesses are designed and constructed to meet stringent safety standards, incorporating features such as shielding, strain relief, and protective coverings to prevent electrical hazards and ensure user safety.
- Customization and Scalability: Wire harnesses can be customized to meet specific application requirements, allowing for flexibility in design, functionality, and scalability to accommodate future system expansions or modifications.
Cable and Wire Harness Assembly Processes
The assembly of cable and wire harnesses involves several critical steps and processes to ensure quality, reliability, and adherence to design specifications. While specific procedures may vary among manufacturers, the general process typically follows these stages:
1. Design and Engineering
The first step in the cable and wire harness assembly process is the design and engineering phase. This involves creating detailed schematics, diagrams, and specifications based on the requirements of the end application. Computer-aided design (CAD) software and electrical engineering tools are often used to optimize the design and ensure compliance with industry standards and regulations.
2. Component Selection and Procurement
Once the design is finalized, the necessary components, including cables, wires, connectors, terminals, and protective coverings, are selected and procured from reliable suppliers. Quality control processes are implemented to ensure that all components meet the required specifications and performance standards.
3. Wire Cutting and Stripping
The wires and cables are cut to the specified lengths and stripped to expose the conductive cores. This process is often automated using precision wire cutting and stripping machines to ensure consistent and accurate wire preparation.
4. Terminal Crimping and Soldering
Terminals or connectors are attached to the wire ends through crimping or soldering processes. Crimping involves deforming the terminal to create a secure mechanical connection, while soldering uses molten metal to create an electrical and mechanical bond between the wire and terminal.
5. Wire Harness Assembly
In this stage, the individual wires and cables are bundled, routed, and secured according to the design specifications. Various techniques, such as lacing, cable ties, or braiding, may be employed to keep the wires organized and protected. Connectors, grommets, and protective sleeves are also incorporated as needed.
6. Testing and Quality Assurance
Rigorous testing and quality assurance processes are essential to ensure the proper functioning and reliability of the wire harness assemblies. Electrical continuity tests, insulation resistance tests, and high-voltage tests are commonly performed to identify any defects or issues before final assembly and installation.
7. Final Assembly and Packaging
The completed wire harness assemblies are inspected, labeled, and prepared for final assembly or integration into the larger system. Proper packaging and handling procedures are followed to protect the assemblies during transportation and storage.
Types of Cable and Wire Harness Assemblies
Cable and wire harness assemblies can be categorized based on various factors, including their application, construction, and materials used. Some common types include:
- Automotive Wire Harnesses: Designed specifically for the complex wiring systems in vehicles, these harnesses must meet stringent safety and environmental standards.
- Aerospace Wire Harnesses: Used in aircraft, spacecraft, and related systems, these harnesses are engineered to withstand extreme temperatures, vibrations, and environmental conditions.
- Industrial Wire Harnesses: Employed in various industrial machinery and equipment, these harnesses are built to withstand harsh environments and provide reliable connectivity for power, control, and data systems.
- Telecommunication Wire Harnesses: Used in telecommunication equipment and networks, these harnesses facilitate the transmission of data and signals over long distances.
- Medical Wire Harnesses: Designed for use in medical devices and equipment, these harnesses must meet strict regulatory requirements and ensure patient safety.
- Military and Defense Wire Harnesses: Engineered to withstand extreme conditions and meet stringent military specifications, these harnesses are used in various defense and aerospace applications.
Best Practices for Cable and Wire Harness Assembly
To ensure the quality, reliability, and long-lasting performance of cable and wire harness assemblies, it is crucial to follow best practices throughout the manufacturing process:
- Adherence to Industry Standards and Regulations: Comply with relevant industry standards, such as IPC/WHMA-A-620 for cable and wire harness assemblies, and applicable regulatory requirements specific to the application or industry.
- Robust Quality Control Processes: Implement rigorous quality control measures, including incoming material inspections, in-process checks, and final testing procedures to identify and address any defects or non-conformities.
- Proper Component Selection and Handling: Carefully select components from reputable suppliers and follow proper handling and storage procedures to prevent damage or contamination.
- Electrostatic Discharge (ESD) Protection: Implement appropriate ESD protection measures, such as grounding equipment and workstations, to prevent damage to sensitive electronic components.
- Skilled Workforce and Training: Invest in training and developing a skilled workforce proficient in wire harness assembly techniques, quality control procedures, and safety practices.
- Effective Documentation and Traceability: Maintain detailed documentation and implement traceability systems to track components, processes, and assemblies throughout the manufacturing cycle.
- Continuous Improvement and Process Optimization: Regularly review and optimize processes, incorporating feedback and lessons learned to drive continuous improvement and enhance efficiency and quality.
- Collaboration and Communication: Foster effective communication and collaboration among all stakeholders, including design teams, manufacturers, and end-users, to ensure seamless integration and adherence to requirements.
FAQs
- Q: What are the main advantages of using cable and wire harness assemblies? A: The primary advantages of cable and wire harness assemblies include reliable connectivity, space and weight optimization, ease of installation and maintenance, improved safety, and customization and scalability to meet specific application requirements.
- Q: How are cable and wire harness assemblies tested for quality and reliability? A: Common testing methods for cable and wire harness assemblies include electrical continuity tests, insulation resistance tests, high-voltage tests, and environmental stress testing (e.g., temperature, vibration, and moisture resistance) to ensure proper functioning and durability.
- Q: Can cable and wire harness assemblies be customized for specific applications? A: Yes, cable and wire harness assemblies can be highly customized to meet the unique requirements of various applications. Manufacturers work closely with customers to design and build harnesses that meet specific electrical, mechanical, and environmental specifications.
- Q: What are the typical materials used in cable and wire harness assemblies? A: Common materials used in cable and wire harness assemblies include copper or aluminum conductors, PVC or cross-linked polyethylene insulation, and various types of connectors, terminals, and protective coverings (e.g., braided sleeves, conduits, or heat shrink tubing).
- Q: How can proper cable and wire harness assembly contribute to safety and regulatory compliance? A: Cable and wire harness assemblies that are designed, manufactured, and installed in accordance with industry standards and regulations can significantly improve safety by reducing the risk of electrical hazards, short circuits, and other potential failures. Additionally, they help ensure compliance with applicable safety and environmental regulations in various industries.
Conclusion
Cable and wire harness assemblies are the unsung heroes of electrical and electronic systems, enabling reliable connectivity, efficient power distribution, and seamless integration of components. Their importance cannot be overstated, as they play a crucial role in ensuring the proper functioning and safety of a wide range of applications across diverse industries.
By following best practices in design, manufacturing, and quality control, cable and wire harness assembly companies can deliver high-quality products that meet stringent performance and safety requirements. Continuous innovation, collaboration, and adherence to industry standards will drive the evolution of these assemblies, enabling the development of more sophisticated and reliable electrical and electronic systems.
As technology advances and the demand for efficient and interconnected systems grows, the role of cable and wire harness assemblies will become increasingly vital. Companies that prioritize quality, customization, and customer satisfaction will remain at the forefront of this dynamic industry, shaping the future of electrical and electronic systems integration.
No responses yet