What is a Buried Via PCB?
A Buried Via PCB, also known as a Buried Via Printed Circuit Board, is a type of multi-layer PCB where the vias are buried in the inner layers and do not extend to the outer layers of the board. This is in contrast to through-hole vias which go through all layers of the PCB from top to bottom.
Buried vias allow for more compact and efficient PCB designs by freeing up space on the outer layers for components and traces. They enable higher component density and can reduce electromagnetic interference (EMI).
How are Buried Vias Manufactured?
The manufacturing process for buried via PCBs involves several key steps:
-
Inner layer processing: The inner layers of the PCB are etched and laminated together. Holes are drilled in specific spots where the buried vias will be placed.
-
Via filling: The drilled holes are filled with conductive material, typically copper, to create the buried vias. This is done through electroplating.
-
Outer layer processing: The outer layers of the PCB are added on top of the inner layers with the buried vias. Additional drilling is done for any through-hole vias or components.
-
Finishing: The PCB goes through final finishing steps such as solder mask application, silkscreen, and surface finishing (e.g. ENIG, HASL).
The manufacturing process requires precise alignment and registration between the layers to ensure the buried vias connect properly. Specialized equipment and strict process controls are necessary.
Advantages of Buried Via PCBs
Increased Design Flexibility
By burying vias in the inner layers, space is freed up on the outer layers for components and routing. This allows for more compact and complex designs. PCB designers have greater flexibility in component placement and trace routing.
Improved Signal Integrity
Through-hole vias that span the entire board thickness can act as antennas and cause electromagnetic interference (EMI). Buried vias are shorter and contained within the board, which reduces EMI. This improves signal integrity, especially for high-frequency signals.
Higher Component Density
With buried vias, components can be placed closer together on both sides of the board without interfering with vias. This enables higher component density and smaller form factors. PCBs can pack more functionality in a smaller space.
Better Thermal Management
Buried vias can be used to transfer heat from hot components on the surface to inner ground planes or heat sinks. This improves thermal management and helps dissipate heat more efficiently. Thermal vias are often used under high-power components like FPGAs and processors.
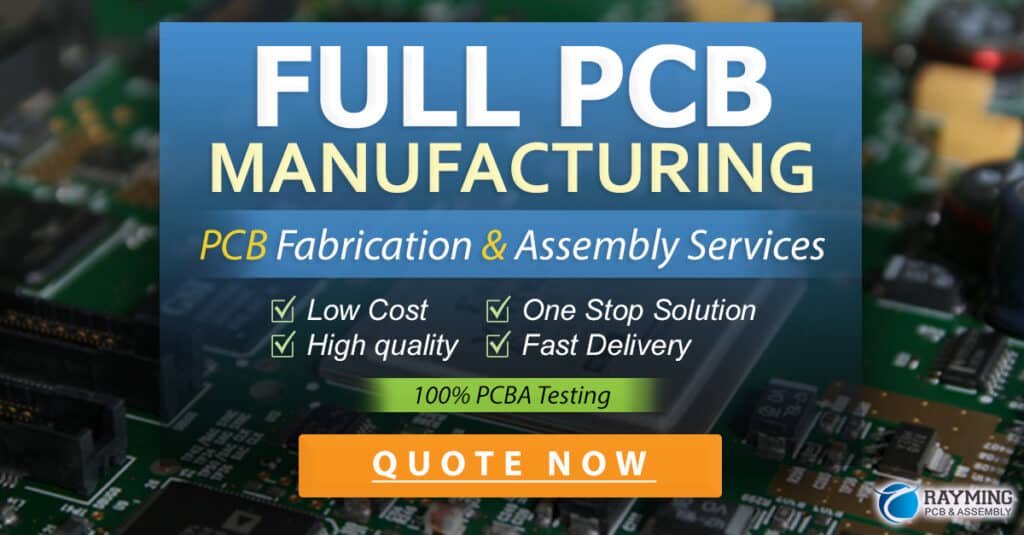
Disadvantages of Buried Via PCBs
Higher Cost
The manufacturing process for buried via PCBs is more complex and requires specialized equipment. The additional processing steps and materials increase the cost compared to standard through-hole PCBs. However, the cost may be justified for the improved performance and space savings.
Longer Lead Times
Due to the more involved manufacturing process, buried via PCBs typically have longer lead times than standard PCBs. The extra processing steps and the need for precise alignment and registration add time to the manufacturing cycle.
Design Complexity
Designing with buried vias adds complexity to the PCB layout process. Careful planning is required to determine the optimal placement of buried vias and ensure proper connectivity between layers. PCB design tools with 3D modeling capabilities are often necessary to visualize and verify the buried via structures.
Limited Repairability
Buried vias are not accessible from the surface of the PCB, which makes repairs and modifications difficult or impossible. If a buried via fails, the entire board may need to be scrapped and replaced. This is in contrast to through-hole vias which can be accessed and repaired from the surface.
Applications of Buried Via PCBs
High-Density Interconnect (HDI) PCBs
Buried vias are a key technology used in HDI PCBs. HDI PCBs have fine pitch components, small vias, and high layer counts. Buried vias enable the high density and complex routing required for these advanced designs. HDI PCBs are used in smartphones, tablets, and other compact electronics.
RF and High-Speed Digital PCBs
Buried vias are commonly used in PCBs for RF and high-speed digital applications. The improved signal integrity and reduced EMI of buried vias are beneficial for these sensitive circuits. Examples include PCBs for wireless communication devices, radar systems, and high-speed networking equipment.
Medical Devices
Medical devices often require compact and reliable PCBs with high functionality. Buried via PCBs are used in medical applications such as implantable devices, diagnostic equipment, and monitoring systems. The space savings and signal integrity improvements of buried vias are valuable in these critical applications.
Aerospace and Defense Electronics
PCBs for aerospace and defense applications often have stringent requirements for reliability, signal integrity, and space efficiency. Buried via PCBs are used in avionics systems, satellite electronics, and military communications equipment. The robustness and performance benefits of buried vias are important in these demanding environments.
Designing with Buried Via PCBs
Designing PCBs with buried vias requires consideration of several key factors:
Via Placement and Routing
Careful planning is necessary to determine the optimal placement of buried vias and ensure proper connectivity between layers. The size and spacing of the vias must be considered to maintain signal integrity and manufacturability. PCB design tools with 3D modeling capabilities are helpful for visualizing and verifying the buried via structures.
Layer Stack-up
The layer stack-up of the PCB must be designed to accommodate the buried vias. The number and arrangement of layers, as well as the dielectric materials and thicknesses, must be chosen to support the desired electrical and mechanical properties. Consideration must be given to the via drilling and filling processes to ensure reliable connections.
Signal Integrity Analysis
Signal integrity analysis is important when designing with buried vias. The impact of the vias on signal propagation, impedance, and crosstalk must be evaluated. Simulation tools can be used to model the behavior of signals passing through buried vias and optimize the design for performance.
Thermal Management
Buried vias can be used for thermal management by transferring heat from hot components to inner layers or heat sinks. Thermal analysis should be performed to determine the optimal placement and size of thermal vias. The thermal conductivity of the PCB materials and the effectiveness of the heat dissipation paths must be considered.
Design for Manufacturing (DFM)
Designing for manufacturability is crucial when working with buried via PCBs. The design must adhere to the capabilities and constraints of the manufacturing process. Factors such as via size, spacing, and aspect ratio must be within the limits of the fabrication equipment. Clear communication with the PCB manufacturer is necessary to ensure the design is viable and can be reliably produced.
FAQ
What is the difference between buried vias and blind vias?
Buried vias are contained entirely within the inner layers of the PCB and do not extend to either the top or bottom surface. Blind vias start on an outer layer and terminate on an inner layer, but do not go through the entire board. Blind vias are visible on one surface of the PCB, while buried vias are not visible on either surface.
Can buried vias be used in combination with other via types?
Yes, buried vias can be used in combination with other via types such as through-hole vias and blind vias. This allows for even greater design flexibility and the ability to create complex interconnect structures. The different via types can be used strategically in different parts of the PCB to optimize space utilization, signal integrity, and manufacturability.
Are there any limitations on the number of buried via layers in a PCB?
The number of buried via layers that can be incorporated in a PCB is limited by the manufacturing capabilities of the PCB fabricator. Most fabricators can produce PCBs with up to 4-6 buried via layers. Beyond that, the complexity and cost increase significantly. The practical limit depends on the specific design requirements and the capabilities of the chosen manufacturer.
How do buried vias affect the cost of PCB fabrication?
Buried vias add cost to PCB fabrication due to the additional processing steps and materials required. The cost increase depends on factors such as the number of buried via layers, the via density, and the overall complexity of the design. In general, buried via PCBs can cost 20-50% more than standard through-hole PCBs. However, the cost may be justified for the improved performance and space savings.
Are there any reliability concerns with buried via PCBs?
Buried via PCBs can be just as reliable as standard PCBs when designed and manufactured properly. However, there are some potential reliability concerns to be aware of. The buried vias rely on precise alignment and registration between the layers during fabrication. Any misalignment or poor connectivity can lead to reliability issues. Thermal stress and expansion mismatches between the via fill material and the surrounding PCB can also cause reliability problems over time. Careful design, material selection, and process control are necessary to ensure the long-term reliability of buried via PCBs.
Conclusion
Buried via PCBs offer numerous advantages over traditional through-hole PCBs, including increased design flexibility, improved signal integrity, higher component density, and better thermal management. They enable the creation of more compact and complex electronic devices with enhanced performance.
However, buried via PCBs also come with trade-offs such as higher cost, longer lead times, and limited repairability. Designers must carefully consider these factors and weigh the benefits against the drawbacks for each specific application.
When designing with buried vias, attention must be paid to via placement, routing, layer stack-up, signal integrity, thermal management, and manufacturability. Close collaboration with the PCB manufacturer is essential to ensure a robust and reliable design.
As electronic devices continue to push the boundaries of performance and miniaturization, buried via PCBs will play an increasingly important role. They are a key enabling technology for advanced applications in industries such as consumer electronics, telecommunications, medical devices, and aerospace.
By understanding the capabilities and limitations of buried via PCBs, designers can leverage this technology to create innovative and high-performance electronic products that meet the demands of today’s market.
No responses yet