What is a BOM and Why is it Important for PCB Manufacturing Efficiency?
A Bill of Materials (BOM) is a comprehensive list of all the raw materials, sub-components, parts and quantities needed to manufacture a product. For printed circuit board (PCB) manufacturing, the BOM specifies all the components and materials that will be placed and assembled onto the bare PCB.
The BOM is a critical document that drives the entire PCB manufacturing process from start to finish. It impacts everything from material procurement and inventory management to assembly, testing and final quality control. An accurate, complete and well-structured BOM is essential for maximizing PCB manufacturing efficiency in several key ways:
- Ensures all necessary parts are ordered and available when needed to avoid production delays
- Enables optimized procurement of parts to get the best prices and lead times
- Allows the manufacturing process to be properly planned, resourced and scheduled
- Provides a clear blueprint for the manufacturing team to build the PCB to spec
- Acts as the basis for testing, QA and troubleshooting
In short, the BOM is the DNA of the PCB. It contains all the information needed to correctly manufacture the product. Any errors, omissions or lack of clarity in the BOM will propagate throughout the production process, leading to delays, mistakes, quality issues and added costs. A high-quality BOM is foundational to an efficient PCB manufacturing operation.
Key Elements of a PCB BOM
To serve its purpose as the guiding document for PCB manufacturing, a BOM needs to contain specific information presented in a standardized way. While formats can vary, a typical PCB BOM will include the following key elements:
1. BOM Level
BOM Level refers to the hierarchical structure of the BOM, with the top level being the final PCB assembly. Below this are subsequent levels breaking down the sub-components. The BOM level allows the manufacturer to see at a glance what components make up each assembly and sub-assembly.
2. Part Number
Each component will have a unique part number, which is a standardized way to identify and track that part. The part number ensures the right component is selected during assembly.
3. Part Description
The part description is a brief overview of what the component is, providing details like value (e.g. 10k ohm resistor), package type (e.g. 0805), material, and other distinguishing characteristics.
4. Quantity
The quantity specifies how many of each component is needed for the assembly. Getting the quantities right is crucial for ensuring an uninterrupted production run.
5. Unit of Measure
The unit of measure (UoM) defines how the quantity of the component is specified, typically as each, reel, tube, etc.
6. Reference Designators
Reference designators indicate where each component fits on the PCB based on the schematic diagram. They are typically a letter-number code (e.g. R14 = 14th resistor).
7. Manufacturer Name and Part Number
For each component, the manufacturer name and their specific part number should be listed to ensure the correct part is sourced.
Here is an example of how these elements come together in a typical BOM:
BOM Level | Part Number | Description | Qty | UoM | Ref Des | Mfr Name | Mfr Part Number |
---|---|---|---|---|---|---|---|
1 | 123-456 | 10k ohm 0805 resistor | 15 | ea | R14, R21-R35 | Yageo | RC0805FR-0710KL |
How BOM Accuracy Impacts PCB Manufacturing Efficiency
An accurate BOM is essential for an efficient PCB manufacturing process. Errors or omissions in the BOM can cause significant issues, including:
Material Shortages
If the BOM underestimates the quantities needed or misses components entirely, the manufacturer may not have sufficient stock on hand, requiring last-minute orders that delay production. Conversely, overestimating quantities leads to excess inventory tying up cash.
Incorrect Components
Mistakes in the manufacturer name, part number, or description can result in the wrong components being ordered and assembled. This causes quality issues and requires rework to correct.
Mismatched Quantities
If the BOM quantity doesn’t match the schematic, the PCB may be built with too few or too many components. Too few components means the board won’t function properly. Too many wastes parts and assembly time.
Ambiguous References
If reference designators are unclear, missing, or duplicated, the assembly team may place components incorrectly. This leads to mis-builds that have to be diagnosed and reworked.
All of these issues amount to lost time and money in the manufacturing process. The further errors propagate before being caught, the more costly they become to address. An accurate BOM avoids these pitfalls.
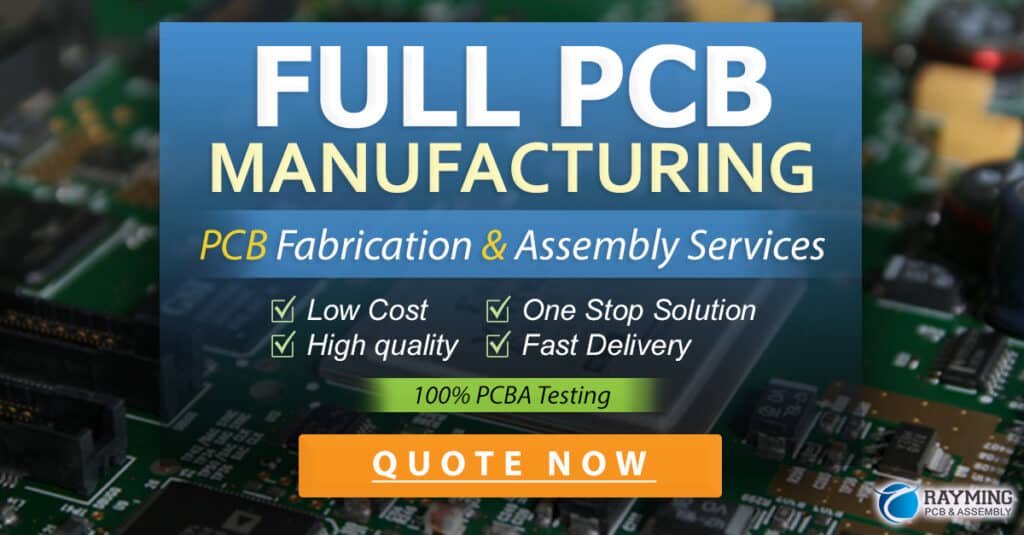
BOM Best Practices for PCB Manufacturing Efficiency
Ensuring an accurate and effective BOM requires following some key best practices:
Establish a Clear BOM Format
Standardizing the BOM format ensures all necessary information is captured consistently. It also allows the BOM to be easily imported into MRP/ERP systems and used across the organization.
Use Automated BOM Tools
PCB design software can automatically generate the BOM from the schematic and layout. This greatly reduces the risk of manual errors. It’s also easy to update the BOM when the design changes.
Include Alternates
Specifying manufacturer-approved substitute parts in the BOM provides flexibility if the primary part is unavailable, without compromising functionality or quality.
Get Early Supplier Input
Collaborating with your key parts suppliers and contract manufacturers in the design stage allows them to validate the BOM. They can identify long lead-time parts, suggest alternates, and help optimize for manufacturability.
Implement Revision Control
Putting the BOM under documented revision control ensures everyone is working from the latest version. Changes can be easily tracked.
Double-Check Before Releasing
Always carefully double-check the BOM against the schematic and layout before releasing it for production. Catching errors at this stage is far more efficient than discovering them on the manufacturing floor.
By implementing these best practices, you can create a BOM optimized for PCB manufacturing efficiency.
FAQs
What happens if a BOM is inaccurate?
An inaccurate BOM can cause significant problems in PCB manufacturing, including material shortages, incorrect component placement, and mis-builds. This leads to production delays, added costs, and quality issues.
How can I ensure my BOM is accurate?
To ensure BOM accuracy, standardize the BOM format, use automated BOM creation tools in your PCB design software, include approved substitute parts, collaborate with suppliers for design validation, implement revision control, and always double-check the BOM before releasing it.
What information needs to be in a PCB BOM?
A PCB BOM should include the BOM level, part number, description, quantity, unit of measure, reference designators, manufacturer name and part number for each component used in the assembly.
Can I use the BOM for other purposes beyond manufacturing?
Yes, the BOM is a versatile document. Beyond guiding manufacturing, it is used for tasks like material planning and procurement, costing, and quality control. The BOM provides a full picture of the product composition.
How often should I update the BOM?
The BOM should be updated any time there is a change to the product design, components, or approved manufacturers. It’s crucial that the BOM stay in sync with the actual product. Disciplined revision control ensures only approved BOM changes are propagated to manufacturing.
I hope this article provides a comprehensive look at how an effective BOM can enhance PCB manufacturing efficiency! Let me know if you would like me to modify or expand the article in any way.
No responses yet