Introduction
In the world of electronics and PCB design, ensuring the structural integrity and reliability of printed circuit boards (PCBs) is of utmost importance. One key component that plays a crucial role in achieving this goal is the Board Stiffener. In this comprehensive article, we will dive deep into the concept of board stiffeners, exploring what they are, why they are essential, and how to effectively use them in your PCB designs.
What is a Board Stiffener?
A board stiffener, also known as a PCB Stiffener or a circuit board stiffener, is a mechanical support element used to enhance the rigidity and stability of a printed circuit board. It is typically a flat, rigid material that is attached to the PCB, often made from metal, plastic, or composite materials. The primary purpose of a board stiffener is to prevent the PCB from flexing, warping, or vibrating excessively, which can lead to component damage, solder joint failures, and overall system malfunctions.
Types of Board Stiffeners
There are several types of board stiffeners available, each with its own unique characteristics and applications. Let’s explore some of the most common types:
-
Metallic Stiffeners: These stiffeners are made from metals such as aluminum, steel, or copper. They offer excellent rigidity and thermal conductivity, making them suitable for high-power applications or environments with significant temperature fluctuations.
-
Plastic Stiffeners: Plastic stiffeners, typically made from materials like polycarbonate or polyethylene, provide a lightweight and cost-effective solution for PCB reinforcement. They are ideal for applications where electrical insulation is crucial.
-
Composite Stiffeners: Composite stiffeners combine the benefits of both metallic and plastic materials. They often consist of a metal core with a plastic or epoxy coating, offering a balance of strength, thermal management, and electrical insulation.
-
Customized Stiffeners: In some cases, custom-designed stiffeners may be required to accommodate specific PCB layouts or unique mechanical requirements. These stiffeners can be fabricated using various materials and manufacturing techniques to meet the desired specifications.
Why Use a Board Stiffener?
Now that we understand what a board stiffener is, let’s explore the key reasons why they are essential in PCB design:
1. Improved Mechanical Stability
One of the primary benefits of using a board stiffener is the enhanced mechanical stability it provides to the PCB. By attaching a stiffener to the board, you can significantly reduce the amount of flexing and warping that occurs due to external forces, vibrations, or thermal stresses. This increased stability helps maintain the structural integrity of the PCB and prevents component damage or solder joint failures.
2. Reduced Vibration and Resonance
In applications where the PCB is subjected to vibrations or resonance, a board stiffener can play a vital role in mitigating these effects. By increasing the rigidity of the board, the stiffener helps dampen vibrations and minimize the amplitude of resonant frequencies. This is particularly important in industries such as aerospace, automotive, and industrial automation, where vibration-induced failures can have severe consequences.
3. Improved Thermal Management
Board stiffeners, especially metallic ones, can contribute to improved thermal management of the PCB. By providing a heat-conducting path, the stiffener helps dissipate heat away from critical components and evenly distribute it across the board. This can prevent localized hot spots and enhance the overall thermal performance of the system.
4. Enhanced Electromagnetic Compatibility (EMC)
In some cases, board stiffeners can also serve as EMC shields, helping to reduce electromagnetic interference (EMI) and improve the electromagnetic compatibility of the PCB. By acting as a barrier against unwanted electromagnetic radiation, the stiffener can minimize crosstalk between components and protect sensitive circuits from external interference.
5. Increased Durability and Reliability
By providing additional mechanical support and protection, board stiffeners contribute to the overall durability and reliability of the PCB. They help prevent physical damage during handling, transportation, and installation, ensuring that the board remains functional and reliable throughout its intended lifespan.
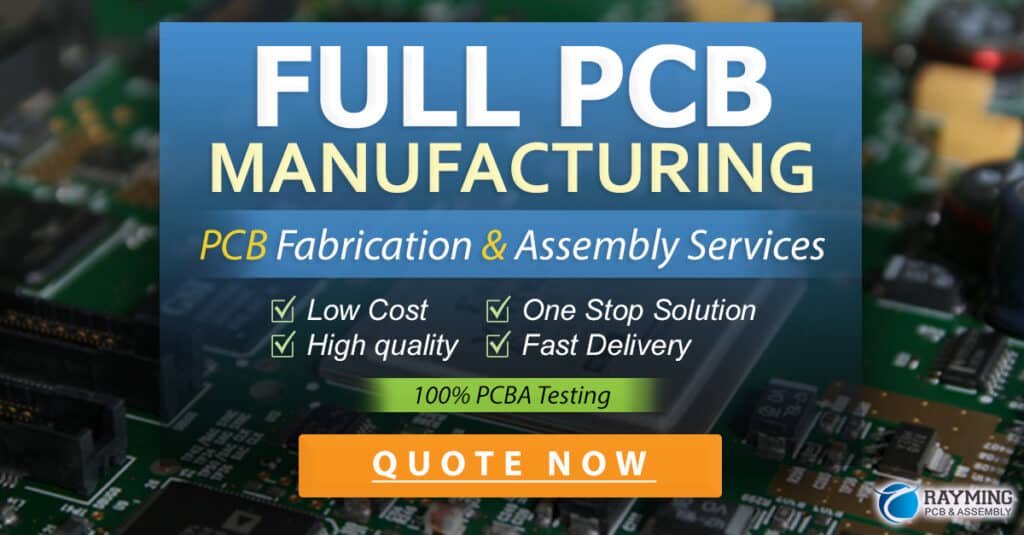
How to Use a Board Stiffener
Now that we understand the importance of board stiffeners, let’s explore the steps involved in effectively using them in your PCB design:
Step 1: Determine the Need for a Stiffener
The first step is to assess whether your PCB requires a stiffener. Consider factors such as the board’s size, thickness, component placement, and the environmental conditions it will be exposed to. If your PCB is large, thin, or subjected to significant mechanical stresses, a stiffener may be necessary to ensure its structural integrity.
Step 2: Select the Appropriate Stiffener Material
Once you have determined the need for a stiffener, the next step is to choose the appropriate material based on your specific requirements. Consider factors such as the desired rigidity, thermal conductivity, electrical insulation, and cost. Metallic stiffeners offer excellent rigidity and thermal management, while plastic stiffeners provide lightweight and electrically insulating properties. Composite stiffeners offer a balance of both.
Step 3: Design the Stiffener
The design of the stiffener should be tailored to the specific layout and requirements of your PCB. Consider the placement of components, connectors, and mounting holes when designing the stiffener. Ensure that the stiffener does not interfere with the functionality of the board and provides adequate clearance for all components.
Step 4: Attach the Stiffener to the PCB
Once the stiffener is designed and fabricated, it needs to be attached to the PCB. There are several methods for attaching stiffeners, depending on the materials and design:
- Adhesive Bonding: Use a strong, thermally conductive adhesive to bond the stiffener to the PCB. This method provides a secure and permanent attachment.
- Mechanical Fastening: Use screws, bolts, or rivets to mechanically fasten the stiffener to the PCB. This method allows for easy removal and replacement of the stiffener if needed.
- Soldering: In some cases, metallic stiffeners can be soldered directly to the PCB using a reflow or wave soldering process. This method ensures a robust electrical and mechanical connection.
Step 5: Verify the Stiffener’s Effectiveness
After attaching the stiffener to the PCB, it is crucial to verify its effectiveness. Conduct thorough testing and analysis to ensure that the stiffener provides the desired level of mechanical stability, vibration reduction, and thermal management. Perform stress tests, vibration analysis, and thermal imaging to validate the performance of the stiffened PCB.
Best Practices for Using Board Stiffeners
To maximize the benefits of board stiffeners and ensure optimal performance, consider the following best practices:
-
Proper Sizing: Ensure that the stiffener is appropriately sized for your PCB. It should provide sufficient coverage and support without adding unnecessary weight or bulk to the board.
-
Material Selection: Choose the stiffener material based on the specific requirements of your application. Consider factors such as rigidity, thermal conductivity, electrical insulation, and compatibility with the PCB material.
-
Placement and Orientation: Position the stiffener strategically to provide maximum support to critical areas of the PCB. Consider the placement of heavy components, connectors, and areas subjected to high mechanical stress.
-
Thermal Management: If using a metallic stiffener for thermal management, ensure proper thermal interface materials (TIMs) are used between the stiffener and the PCB to facilitate efficient heat transfer.
-
Compatibility with Manufacturing Processes: Consider the compatibility of the stiffener with your PCB manufacturing processes. Ensure that the stiffener can withstand the temperatures and conditions of soldering, reflow, or other assembly processes.
-
Testing and Validation: Conduct thorough testing and validation of the stiffened PCB to ensure it meets the desired performance criteria. Perform mechanical, thermal, and electrical tests to verify the effectiveness of the stiffener.
Frequently Asked Questions (FAQ)
-
Q: Can board stiffeners be used with flexible PCBs?
A: Yes, board stiffeners can be used with flexible PCBs to provide localized rigidity in specific areas while allowing other parts of the board to remain flexible. This is commonly known as a “rigid-flex” PCB design. -
Q: How do I determine the thickness of the board stiffener?
A: The thickness of the board stiffener depends on factors such as the size and thickness of the PCB, the expected mechanical stresses, and the desired level of rigidity. Typically, stiffeners range from 0.5mm to 3mm in thickness. It is recommended to consult with a PCB design expert or use simulation tools to determine the optimal thickness for your specific application. -
Q: Can board stiffeners be used for EMI shielding?
A: Yes, metallic board stiffeners can provide some level of EMI shielding by acting as a barrier against electromagnetic radiation. However, for more effective EMI shielding, dedicated shielding materials and techniques, such as conductive coatings or shielding cans, are often used in conjunction with stiffeners. -
Q: Are there any limitations or drawbacks to using board stiffeners?
A: While board stiffeners offer numerous benefits, there are a few limitations to consider. Adding a stiffener increases the overall thickness and weight of the PCB Assembly, which may be a concern in space-constrained or weight-sensitive applications. Additionally, stiffeners may increase the cost and complexity of the PCB manufacturing process. -
Q: Can board stiffeners be retrofitted to an existing PCB design?
A: In some cases, it may be possible to retrofit a board stiffener to an existing PCB design. However, it is generally recommended to incorporate the stiffener into the initial design process to ensure optimal integration and performance. Retrofitting a stiffener may require modifications to the PCB layout and component placement.
Conclusion
Board stiffeners play a crucial role in ensuring the structural integrity, reliability, and performance of printed circuit boards. By providing mechanical support, reducing vibrations, enhancing thermal management, and improving electromagnetic compatibility, stiffeners contribute to the overall robustness and longevity of electronic systems.
When incorporating board stiffeners into your PCB design, it is essential to carefully consider factors such as material selection, sizing, placement, and compatibility with manufacturing processes. By following best practices and conducting thorough testing and validation, you can maximize the benefits of board stiffeners and create PCBs that can withstand the rigors of their intended applications.
As the complexity of electronic systems continues to increase, the use of board stiffeners will remain an important aspect of PCB design. By understanding the principles and techniques involved in using board stiffeners effectively, engineers and designers can create more robust, reliable, and high-performing electronic products.
No responses yet