What is a Bill of Materials (BOM)?
A Bill of Materials (BOM) is a comprehensive list of components, parts, raw materials, assemblies, and other items required to manufacture a product, along with the quantities of each needed. It serves as a centralized source of information for everyone involved in the production process, from design and engineering to procurement and assembly.
BOMs are essential for several reasons:
- They provide a clear, organized view of all the components needed to produce a product.
- They help ensure that the right materials are ordered in the correct quantities.
- They facilitate communication between different departments and teams involved in the production process.
- They help in cost estimation and inventory management.
Types of Bill of Materials
There are several types of BOMs, each serving a specific purpose:
1. Engineering BOM (EBOM)
An Engineering BOM is created by the design team and includes all the components and parts required to build a product as designed. It focuses on the product’s functional requirements and design specifications.
2. Manufacturing BOM (MBOM)
A Manufacturing BOM is derived from the EBOM and is tailored for the production process. It considers the actual manufacturing sequence, assembly instructions, and packaging requirements.
3. Sales BOM (SBOM)
A Sales BOM is a customer-facing document that lists the components and options available for a product. It is often used in configure-to-order (CTO) or assemble-to-order (ATO) scenarios.
4. Service BOM
A Service BOM lists all the components, parts, and materials required to maintain, repair, or service a product. It is essential for after-sales support and product maintenance.
How to Create a Bill of Materials
Creating a BOM involves several steps:
1. Gather Product Information
Start by collecting all the necessary information about the product, including design specifications, drawings, and component lists. This information can come from various sources, such as CAD files, engineering documents, and supplier datasheets.
2. Determine BOM Level and Structure
Decide on the level of detail required for your BOM and create a hierarchical structure. A single-level BOM lists all components and parts in a flat structure, while a multi-level BOM organizes components into subassemblies and parent-child relationships.
Example of a multi-level BOM structure:
- Product A
- Subassembly 1
- Component 1
- Component 2
- Subassembly 2
- Component 3
- Component 4
3. Assign Part Numbers and Descriptions
Assign unique part numbers and clear descriptions to each component and subassembly in the BOM. This helps in identification and tracking of parts throughout the production process.
4. Specify Quantities
For each component and subassembly, specify the quantity required to produce one unit of the finished product. This information is crucial for material planning and procurement.
5. Include Additional Information
Depending on your specific needs, you may want to include additional information in your BOM, such as:
- Part dimensions and specifications
- Supplier information
- Lead times
- Cost data
- Revision history
6. Review and Approve
Once the BOM is complete, it should be reviewed and approved by the relevant stakeholders, such as engineering, manufacturing, and quality control teams. This ensures that the BOM is accurate, complete, and meets all requirements.
BOM Example
Here’s a simplified example of a BOM for a desktop computer:
Level | Part Number | Description | Quantity |
---|---|---|---|
0 | PC-001 | Desktop Computer | 1 |
1 | MB-001 | Motherboard | 1 |
1 | CPU-001 | CPU | 1 |
1 | RAM-001 | RAM (8GB) | 2 |
1 | SSD-001 | SSD (500GB) | 1 |
1 | PSU-001 | Power Supply Unit | 1 |
1 | CASE-001 | Computer Case | 1 |
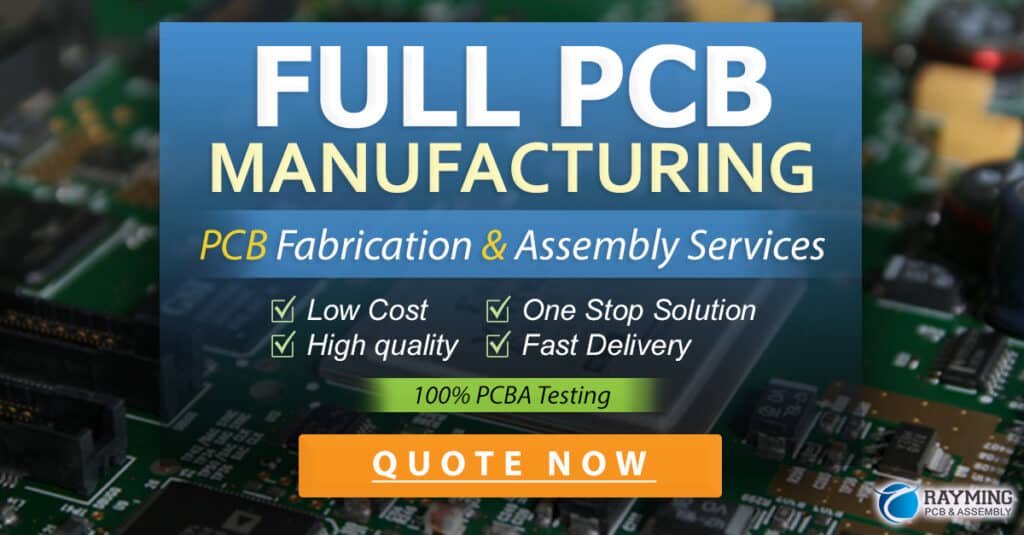
BOM Management Software
As products become more complex and supply chains more global, managing BOMs manually can become challenging. BOM management software helps streamline the process by providing a centralized platform for creating, managing, and sharing BOMs.
Some popular BOM management software options include:
- Autodesk Fusion 360
- OpenBOM
- Arena BOM & Item Management
- Teamcenter BOM Management
- Upchain BOM Management
These software solutions offer features like version control, change management, integration with CAD and ERP systems, and collaboration tools.
Best Practices for BOM Management
To ensure effective BOM management, follow these best practices:
- Maintain a consistent naming and numbering convention for parts and assemblies.
- Regularly review and update BOMs to reflect changes in design, suppliers, or manufacturing processes.
- Establish clear ownership and responsibility for BOM maintenance and updates.
- Integrate BOM management with other systems, such as ERP, MRP, and PLM, to ensure data consistency and accuracy.
- Provide training and support to all stakeholders involved in BOM creation and management.
Frequently Asked Questions (FAQ)
1. What is the difference between a BOM and a parts list?
A BOM is a structured, hierarchical list of all the components, parts, and materials required to produce a product, along with their quantities. A parts list, on the other hand, is a simple list of all the parts used in a product, without the hierarchical structure or quantities.
2. How often should BOMs be updated?
BOMs should be updated whenever there are changes in the product design, components, suppliers, or manufacturing processes. The frequency of updates depends on the complexity of the product and the dynamics of the industry.
3. Who is responsible for creating and maintaining BOMs?
The responsibility for creating and maintaining BOMs typically lies with the engineering or design team. However, other stakeholders, such as manufacturing, procurement, and quality control, should also be involved in the process to ensure accuracy and completeness.
4. Can a product have multiple BOMs?
Yes, a product can have multiple BOMs, each serving a different purpose. For example, a product may have an Engineering BOM (EBOM) for design purposes, a Manufacturing BOM (MBOM) for production, and a Service BOM for maintenance and repair.
5. How does a BOM relate to inventory management?
A BOM provides the foundation for inventory management by specifying the components and quantities required to produce a product. This information is used to plan material requirements, schedule production, and manage inventory levels. Accurate BOMs help ensure that the right materials are available at the right time, reducing the risk of stockouts or excess inventory.
Conclusion
A Bill of Materials (BOM) is a critical tool for any manufacturing organization, providing a structured and comprehensive view of all the components and materials required to produce a product. By creating and managing BOMs effectively, companies can streamline their production processes, improve communication between teams, and optimize inventory management. Implementing best practices and leveraging BOM management software can further enhance the benefits of BOMs, ultimately leading to increased efficiency, cost savings, and better product quality.
No responses yet