Introduction to BGA and LGA packaging Technologies
In the world of electronics packaging, Ball Grid Array (BGA) and Land Grid Array (LGA) are two widely used packaging technologies for integrated circuits (ICs). These packaging methods are designed to provide reliable electrical connections between the IC and the printed circuit board (PCB) while ensuring optimal performance and durability.
What is BGA Packaging?
BGA is a surface-mount packaging technology that uses a grid of solder balls to connect the IC to the PCB. The solder balls are arranged in a matrix on the bottom side of the package, allowing for a high density of interconnects in a relatively small area. BGA packages are known for their excellent electrical and thermal performance, as well as their ability to accommodate high pin counts.
What is LGA Packaging?
LGA, on the other hand, is a packaging technology that uses a grid of flat contact pads instead of solder balls. The IC is placed on top of the LGA socket, which contains a corresponding grid of pins that make contact with the pads on the IC. LGA packages offer several advantages, such as lower cost, easier installation, and better resistance to mechanical stress compared to BGA packages.
Differences between BGA and LGA Packaging
While both BGA and LGA packaging technologies serve the purpose of connecting ICs to PCBs, they have several key differences that set them apart. Let’s explore these differences in detail.
Connection Method
The primary difference between BGA and LGA packaging lies in their connection method.
- BGA: Uses solder balls to establish electrical connections between the IC and PCB. The solder balls are reflowed during the assembly process, creating a permanent connection.
- LGA: Uses flat contact pads on the IC that mate with pins on the LGA socket. The connection is established through mechanical pressure, allowing for easy installation and removal of the IC.
Solder Reflow Process
The solder reflow process is another significant difference between BGA and LGA packaging.
- BGA: Requires a solder reflow process to melt the solder balls and create a permanent connection between the IC and PCB. This process involves precise temperature control and can be more complex than LGA assembly.
- LGA: Does not require a solder reflow process, as the connection is established through mechanical pressure. This simplifies the assembly process and reduces the risk of solder-related defects.
Mechanical Stress Resistance
The ability to withstand mechanical stress is an important consideration when choosing between BGA and LGA packaging.
- BGA: More susceptible to mechanical stress due to the rigid nature of the solder ball connections. Thermal expansion mismatches between the IC and PCB can lead to solder joint failures over time.
- LGA: Offers better resistance to mechanical stress, as the contact pads and pins allow for some degree of movement and flexibility. This helps to mitigate the effects of thermal expansion mismatches and improves overall reliability.
Cost Comparison
Cost is often a deciding factor when selecting a packaging technology for a particular application.
- BGA: Generally more expensive than LGA due to the higher complexity of the package and the need for precise solder ball placement and reflow processes.
- LGA: Typically lower in cost compared to BGA, as the package structure is simpler and does not require solder balls or a reflow process.
Reworkability
Reworkability refers to the ease with which an IC can be removed and replaced on a PCB.
- BGA: More difficult to rework due to the permanent nature of the solder ball connections. Removing a BGA package often requires specialized equipment and can potentially damage the PCB.
- LGA: Easier to rework, as the IC can be easily removed from the LGA socket without the need for solder reflow. This allows for quick replacement of faulty ICs and simplifies the debugging process.
Applications of BGA and LGA Packaging
BGA and LGA packaging technologies find applications in a wide range of electronic devices and systems. Let’s explore some common use cases for each packaging type.
BGA Applications
- High-performance computing: BGA packages are commonly used in microprocessors, GPUs, and other high-performance ICs that require a large number of interconnects and excellent electrical and thermal performance.
- Mobile devices: BGA packages are widely used in smartphones, tablets, and other portable devices due to their compact size and ability to accommodate high pin counts in a small footprint.
- Networking equipment: BGA packages are often used in routers, switches, and other networking equipment that require high-speed data transmission and reliable performance.
LGA Applications
- Desktop computers: LGA sockets are commonly used in desktop CPUs, as they allow for easy installation and upgrades without the need for soldering.
- Servers: LGA sockets are often used in server-grade CPUs, as they provide a reliable and cost-effective solution for high-performance computing applications.
- Embedded systems: LGA packages are used in various embedded systems, such as industrial control modules and automotive electronics, due to their robustness and resistance to mechanical stress.
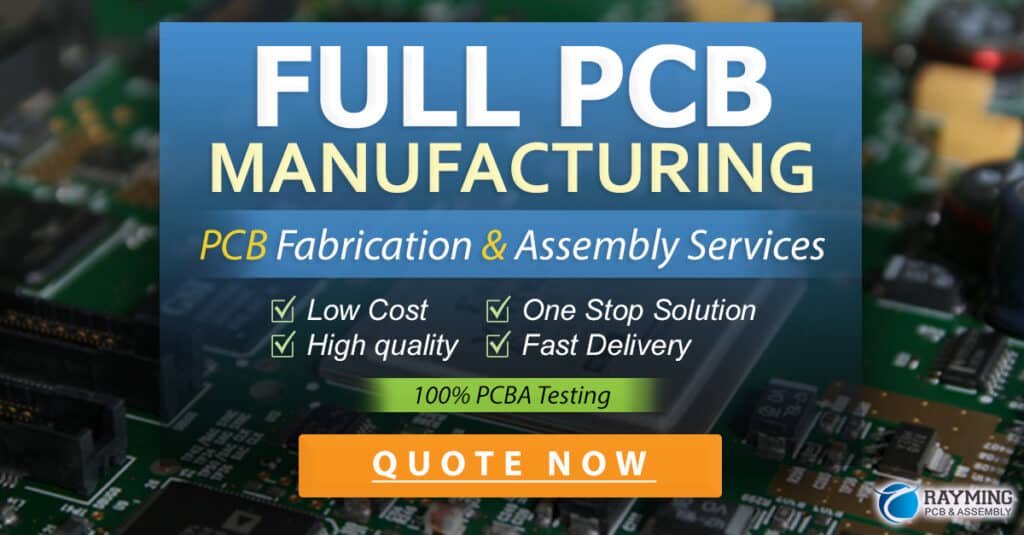
Advantages and Disadvantages of BGA and LGA Packaging
Both BGA and LGA packaging technologies have their own set of advantages and disadvantages, which should be carefully considered when selecting a packaging solution for a specific application.
BGA Advantages
- High pin count: BGA packages can accommodate a large number of interconnects in a small area, making them suitable for complex ICs with high I/O requirements.
- Excellent electrical performance: The short and direct solder ball connections in BGA packages provide low inductance and resistance, enabling high-speed signal transmission.
- Good thermal performance: BGA packages offer efficient heat dissipation due to the large number of solder balls that act as thermal paths between the IC and PCB.
BGA Disadvantages
- Higher cost: BGA packages are generally more expensive than LGA packages due to their complex structure and the need for precise solder ball placement and reflow processes.
- Limited reworkability: Removing and replacing BGA packages can be challenging and may require specialized equipment, making rework processes more time-consuming and costly.
- Susceptibility to mechanical stress: The rigid nature of solder ball connections makes BGA packages more vulnerable to mechanical stress caused by thermal expansion mismatches between the IC and PCB.
LGA Advantages
- Lower cost: LGA packages are typically less expensive than BGA packages, as they have a simpler structure and do not require solder balls or a reflow process.
- Easy installation and removal: LGA sockets allow for easy installation and removal of ICs without the need for soldering, simplifying the assembly and debugging processes.
- Better resistance to mechanical stress: The contact pads and pins in LGA packages provide some degree of flexibility, allowing them to better withstand mechanical stress caused by thermal expansion mismatches.
LGA Disadvantages
- Lower pin density: LGA packages generally have a lower pin density compared to BGA packages, as the contact pads require more space than solder balls.
- Reduced thermal performance: LGA packages may have slightly lower thermal performance compared to BGA packages, as the contact pads do not provide as many thermal paths between the IC and PCB.
- Potential for contact issues: The mechanical pressure-based connection in LGA packages can be susceptible to contact problems if the socket or IC is not properly aligned or if there is excessive wear on the contact pads or pins over time.
Comparison Table: BGA vs. LGA
Feature | BGA | LGA |
---|---|---|
Connection Method | Solder balls | Flat contact pads and pins |
Solder Reflow Process | Required | Not required |
Mechanical Stress Resistance | Lower | Higher |
Cost | Higher | Lower |
Reworkability | More difficult | Easier |
Pin Density | Higher | Lower |
Electrical Performance | Excellent | Good |
Thermal Performance | Excellent | Good |
Common Applications | High-performance computing, mobile devices, networking equipment | Desktop computers, servers, embedded systems |
Future Trends in BGA and LGA Packaging
As electronic devices continue to evolve and become more complex, packaging technologies must keep pace to meet the ever-increasing demands for performance, reliability, and cost-effectiveness. Some of the future trends in BGA and LGA packaging include:
Advanced Materials
The development of advanced materials, such as low-k dielectrics and high-conductivity metals, will help to improve the electrical and thermal performance of both BGA and LGA packages. These materials will enable faster signal transmission, better heat dissipation, and improved overall package reliability.
3D Packaging
3D packaging technologies, such as package-on-package (PoP) and through-silicon via (TSV), are becoming increasingly popular for high-density and high-performance applications. These technologies allow for the vertical stacking of multiple ICs, enabling greater functionality and performance in a smaller footprint. Both BGA and LGA packages can be used in 3D packaging configurations, depending on the specific requirements of the application.
Hybrid Packaging Solutions
The combination of BGA and LGA packaging technologies in a single package, known as a hybrid package, is another emerging trend. Hybrid packages leverage the strengths of both BGA and LGA technologies to provide a solution that offers the best balance of performance, reliability, and cost for a given application.
Increased Focus on Reliability
As electronic devices are used in increasingly harsh environments and mission-critical applications, there will be a greater focus on package reliability. This will drive the development of more robust BGA and LGA packages that can withstand extreme temperatures, mechanical stress, and other environmental factors.
Frequently Asked Questions (FAQ)
-
Q: Can BGA packages be reworked?
A: While BGA packages can be reworked, the process is more difficult and time-consuming compared to LGA packages. Specialized equipment and skilled technicians are required to remove and replace BGA packages without damaging the PCB or adjacent components. -
Q: Are LGA packages suitable for high-speed applications?
A: Yes, LGA packages can be used in high-speed applications, although they may have slightly lower electrical performance compared to BGA packages. The contact pads and pins in LGA packages provide good signal integrity and can support high-speed data transmission. -
Q: Which packaging technology is better for high-density applications?
A: BGA packaging is generally better suited for high-density applications, as it offers a higher pin count and smaller pitch compared to LGA packaging. The use of solder balls in BGA packages allows for a greater number of interconnects in a given area. -
Q: Can LGA packages be used in mobile devices?
A: While LGA packages are not as common as BGA packages in mobile devices, they can still be used in certain applications. LGA packages are more often found in larger devices, such as desktop computers and servers, where their advantages in terms of cost and reworkability are more significant. -
Q: Are there any environmental concerns associated with BGA or LGA packaging?
A: Both BGA and LGA packaging technologies use materials that may have some environmental impact, such as lead in solder balls (for non-RoHS compliant packages) and various plastics in the package substrate. However, the electronics industry is continually working to develop more eco-friendly materials and processes to minimize the environmental footprint of these packaging technologies.
Conclusion
BGA and LGA packaging technologies are essential for connecting ICs to PCBs in a wide range of electronic devices and systems. While both technologies serve the same basic purpose, they have distinct differences in terms of connection method, solder reflow process, mechanical stress resistance, cost, and reworkability.
BGA packaging offers high pin density, excellent electrical and thermal performance, and is commonly used in high-performance computing, mobile devices, and networking equipment. LGA packaging, on the other hand, provides lower cost, easier installation and removal, and better resistance to mechanical stress, making it well-suited for desktop computers, servers, and embedded systems.
When selecting between BGA and LGA packaging for a specific application, engineers must carefully consider the trade-offs between performance, cost, reliability, and manufacturability. As electronic devices continue to advance, it is likely that both BGA and LGA technologies will evolve to meet the growing demands for faster, smaller, and more reliable packaging solutions.
No responses yet