What is a BGA Package?
A BGA package is a surface-mount package that utilizes an array of solder balls on the bottom side of the package to establish electrical connections with a printed circuit board (PCB). The solder balls are arranged in a grid pattern, allowing for a higher number of interconnections compared to other SMT packages like Quad Flat Packages (QFPs) or Small Outline Packages (SOPs).
BGA packages offer several advantages, including:
- High-density interconnections
- Improved electrical and thermal performance
- Smaller package size
- Better signal integrity
- Reduced lead inductance
Common BGA Package Types
There are several types of BGA packages, each with its own unique characteristics and benefits. Let’s explore some of the most common BGA package types:
Plastic BGA (PBGA)
Plastic BGA (PBGA) packages are the most widely used type of BGA package. They consist of a plastic substrate with a die attached to the top side and solder balls on the bottom side. PBGAs offer a cost-effective solution for high-density applications and are available in various sizes and ball counts.
Characteristic | Description |
---|---|
Substrate Material | Plastic (BT, FR-4, or polyimide) |
Die Attachment | Wire bonding or flip-chip |
Ball Count | Varies (typically 64 to 1024) |
Ball Pitch | 0.5mm to 1.27mm |
Thermal Performance | Moderate |
Cost | Low to moderate |
Ceramic BGA (CBGA)
Ceramic BGA (CBGA) packages use a ceramic substrate instead of a plastic one. CBGAs offer better thermal and electrical performance compared to PBGAs, making them suitable for high-reliability applications. However, they are more expensive and have a limited ball count due to the brittle nature of the ceramic substrate.
Characteristic | Description |
---|---|
Substrate Material | Ceramic (alumina or low-temperature co-fired ceramic) |
Die Attachment | Wire bonding or flip-chip |
Ball Count | Typically less than 1000 |
Ball Pitch | 0.8mm to 1.27mm |
Thermal Performance | High |
Cost | High |
Tape BGA (TBGA)
Tape BGA (TBGA) packages utilize a flexible tape substrate, which is typically made of polyimide. TBGAs offer a thinner profile and better electrical performance compared to PBGAs. They are often used in applications that require flexibility or have limited vertical space.
Characteristic | Description |
---|---|
Substrate Material | Polyimide tape |
Die Attachment | Wire bonding or flip-chip |
Ball Count | Varies |
Ball Pitch | 0.5mm to 0.8mm |
Thermal Performance | Moderate |
Cost | Moderate to high |
Cavity-Down BGA (CDBGA)
Cavity-Down BGA (CDBGA) packages have the die attached to the bottom side of the substrate, facing the PCB. This configuration allows for better thermal dissipation and reduces the package height. CDBGAs are commonly used in applications that require low profile and high thermal performance.
Characteristic | Description |
---|---|
Substrate Material | Plastic or ceramic |
Die Attachment | Flip-chip |
Ball Count | Varies |
Ball Pitch | 0.5mm to 1.27mm |
Thermal Performance | High |
Cost | Moderate to high |
Flip-Chip BGA (FCBGA)
Flip-Chip BGA (FCBGA) packages use a flip-chip die attachment method, where the die is directly connected to the substrate using solder bumps. FCBGAs offer the highest interconnection density and best electrical performance among BGA packages. They are often used in high-performance applications such as microprocessors and graphics processors.
Characteristic | Description |
---|---|
Substrate Material | Plastic, ceramic, or silicon |
Die Attachment | Flip-chip |
Ball Count | High (up to several thousand) |
Ball Pitch | 0.3mm to 0.8mm |
Thermal Performance | High |
Cost | High |
Factors to Consider When Choosing a BGA Package Type
When selecting a BGA package type for your application, consider the following factors:
-
Application Requirements: Determine the specific requirements of your application, such as thermal performance, electrical performance, package size, and reliability.
-
Ball Count and Pitch: Consider the number of interconnections required and the available PCB space. Higher ball counts and smaller ball pitches allow for higher-density interconnections but may increase manufacturing complexity and cost.
-
Thermal Management: Assess the thermal dissipation requirements of your application. Packages with better thermal performance, such as CBGAs and CDBGAs, may be necessary for applications with high power dissipation.
-
Cost: Evaluate the cost implications of different BGA package types. PBGAs are generally the most cost-effective, while CBGAs and FCBGAs are more expensive due to their advanced features and materials.
-
Manufacturing Capabilities: Consider your manufacturing capabilities and the complexity of assembling different BGA package types. Some packages may require specialized equipment or processes, which can impact manufacturing costs and yields.
-
Reliability: Assess the reliability requirements of your application and choose a package type that meets those needs. Factors such as thermal cycling, mechanical stress, and moisture resistance should be considered.
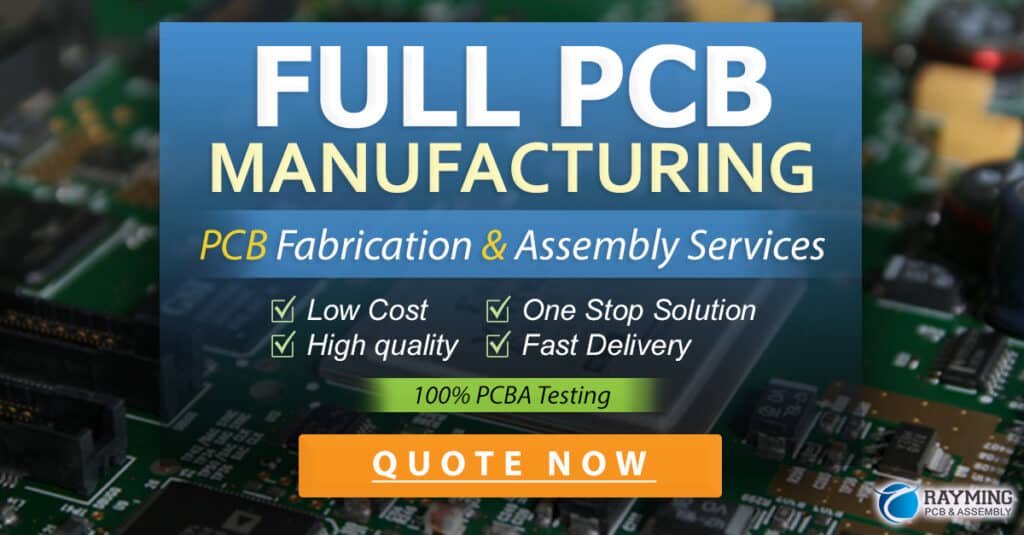
Frequently Asked Questions (FAQ)
-
Q: What is the difference between a BGA and a QFP package?
A: BGA packages have solder balls arranged in a grid pattern on the bottom side of the package, while QFP packages have leads extending from the sides of the package. BGAs offer higher interconnection density and better electrical performance compared to QFPs. -
Q: Can BGA packages be reworked or repaired?
A: Yes, BGA packages can be reworked or repaired using specialized equipment and techniques. However, the process is more complex compared to other SMT packages and requires skilled operators to ensure proper alignment and solder joint integrity. -
Q: What is the advantage of using a flip-chip BGA package?
A: Flip-chip BGA packages offer the highest interconnection density and best electrical performance among BGA packages. They allow for direct connection between the die and substrate, reducing signal path length and improving signal integrity. -
Q: How does the ball pitch affect the manufacturability of BGA packages?
A: Smaller ball pitches (e.g., 0.3mm or 0.4mm) allow for higher interconnection density but increase the manufacturing complexity and require more precise alignment and control during assembly. Larger ball pitches (e.g., 0.8mm or 1.0mm) are easier to manufacture but may limit the package density. -
Q: What is the role of the substrate material in BGA packages?
A: The substrate material in BGA packages serves as a mechanical support and provides electrical connectivity between the die and solder balls. Different substrate materials, such as plastic, ceramic, or tape, offer varying thermal, electrical, and mechanical properties, which can impact the package’s performance and reliability.
Conclusion
Selecting the right BGA package type is crucial for ensuring optimal performance, reliability, and cost-effectiveness in your electronic application. By understanding the characteristics, advantages, and considerations of different BGA package types, you can make an informed decision based on your specific requirements.
Consider factors such as application needs, ball count and pitch, thermal management, cost, manufacturing capabilities, and reliability when choosing a BGA package type. Additionally, consult with your package supplier, PCB manufacturer, and assembly partner to ensure compatibility and manufacturability.
As technology advances and new packaging solutions emerge, staying up-to-date with the latest BGA package types and their capabilities will help you stay competitive in the ever-evolving world of electronics manufacturing.
No responses yet