Introduction to Microwave-assisted PCB coating
Printed Circuit Boards (PCBs) are essential components in modern electronics, providing a platform for interconnecting electronic components. To protect these boards from environmental factors such as moisture, dust, and chemical contaminants, various coating materials are applied to the surface of the PCBs. Traditionally, the curing process of these coating materials involves heating the coated PCBs in conventional ovens, which can be time-consuming and energy-intensive. However, recent advancements in microwave technology have led to the development of microwave-assisted curing processes for PCB coatings.
Microwave-assisted curing of PCB coatings offers several advantages over traditional methods, including faster curing times, reduced energy consumption, and improved coating quality. By using microwave energy to heat the coating material directly, the curing process can be completed in a matter of minutes, compared to hours in conventional ovens. Additionally, the selective heating nature of microwaves allows for more uniform and efficient curing of the coating material, resulting in better adhesion and protection for the PCB.
Principles of Microwave Heating in PCB Coating Applications
Microwave heating is based on the ability of certain materials to absorb microwave energy and convert it into heat. In the case of PCB coatings, the coating materials typically contain polar molecules or conductive fillers that interact with the oscillating electric field of the microwaves. This interaction causes the molecules to rotate and vibrate, generating heat through friction and dielectric loss mechanisms.
The efficiency of microwave heating depends on several factors, including the dielectric properties of the coating material, the frequency and power of the microwave energy, and the design of the microwave applicator. The dielectric properties, such as the dielectric constant and loss factor, determine how well the material absorbs and converts microwave energy into heat. Higher dielectric constants and loss factors generally result in more efficient heating.
Microwave frequency is another important factor in PCB coating applications. Most industrial microwave systems operate at either 915 MHz or 2.45 GHz, with the latter being more common due to its wider availability and compatibility with smaller applicator designs. The choice of frequency can impact the depth of penetration of the microwave energy into the coating material, as well as the heating uniformity.
The design of the microwave applicator also plays a crucial role in the efficiency and uniformity of heating. Applicators can be designed as single-mode or multi-mode cavities, with single-mode cavities offering more focused and controlled heating, while multi-mode cavities provide a larger heating area and higher throughput. The design must also consider factors such as the size and shape of the PCBs, the thickness and composition of the coating material, and the desired heating pattern.
Effects of Microwave Curing on PCB Coating Properties
Microwave curing can have significant effects on the properties of PCB coatings, both during and after the curing process. One of the primary effects is the rapid and volumetric heating of the coating material, which can lead to faster cross-linking and polymerization reactions. This can result in shorter curing times and improved coating quality, with better adhesion, hardness, and chemical resistance.
However, the rapid heating can also introduce challenges, such as the potential for thermal stress and deformation of the PCB substrate. If the heating rate is too high or uneven, it can cause the PCB to warp or delaminate, compromising its structural integrity and reliability. Therefore, careful control of the microwave power, frequency, and exposure time is necessary to optimize the curing process and minimize adverse effects.
Another important consideration is the compatibility of the coating material with microwave curing. Not all coating formulations are suitable for microwave processing, as some may contain ingredients that are transparent to microwaves or that can cause arcing or other undesirable effects. In some cases, the coating formulation may need to be modified or optimized for microwave curing, such as by adding microwave-absorbing fillers or adjusting the resin-to-hardener ratio.
The following table summarizes some of the key effects of microwave curing on PCB coating properties:
Property | Effect of Microwave Curing |
---|---|
Curing Time | Significantly reduced compared to conventional oven curing |
Adhesion | Improved due to faster cross-linking and better substrate wetting |
Hardness | Increased due to higher degree of cure and cross-link density |
Chemical Resistance | Enhanced due to more complete polymerization and fewer unreacted species |
Thermal Stress | Potential for increased stress and deformation if heating is too rapid or uneven |
Compatibility | Some coating formulations may require modification for optimal microwave curing performance |
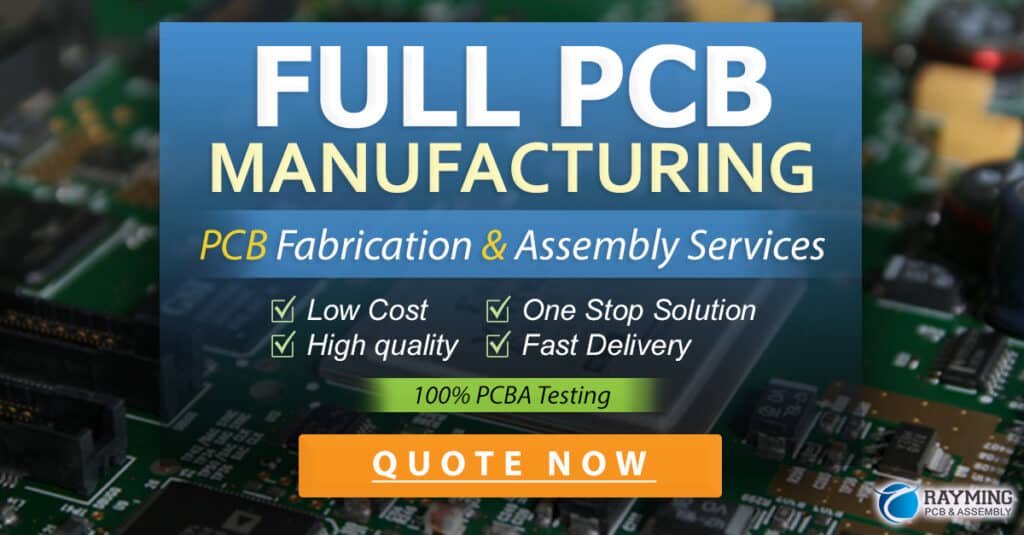
Challenges and Limitations of Microwave-Assisted PCB Coating
While microwave-assisted curing offers many benefits for PCB coating applications, there are also several challenges and limitations that must be considered. One of the primary challenges is the complexity of the microwave heating process itself, which requires careful design and optimization of the microwave applicator, as well as precise control of the processing parameters. This can be more challenging than traditional oven curing, which relies on simple conductive and convective heating mechanisms.
Another challenge is the potential for uneven heating and hot spots within the PCB and coating material. Microwaves can preferentially heat certain areas or components of the PCB, such as metal traces or components with high dielectric loss factors. This can lead to localized overheating and thermal stress, which can damage the PCB or compromise the coating quality. To mitigate this issue, techniques such as mode stirring, sample rotation, and hybrid heating (combining microwave with convective or infrared heating) can be employed.
The limited penetration depth of microwaves can also be a limitation in some applications. Microwaves typically penetrate only a few centimeters into most materials, depending on their dielectric properties and the frequency of the microwaves. This means that microwave curing may not be suitable for very thick coatings or large PCBs, where the heating may be insufficient or uneven. In such cases, alternative curing methods or a combination of techniques may be necessary.
Finally, the cost and availability of microwave equipment can be a barrier to adoption for some manufacturers. Industrial microwave systems can be expensive to purchase and maintain, and they may require specialized training and expertise to operate effectively. Additionally, not all facilities may have the necessary infrastructure or utilities to support microwave processing, such as high-power electrical supply or adequate ventilation and cooling systems.
Despite these challenges and limitations, microwave-assisted PCB coating remains a promising technology with significant potential for improving the efficiency, quality, and performance of PCB manufacturing processes.
Future Trends and Research Directions
As the demand for high-performance electronics continues to grow, so does the need for advanced PCB coating technologies that can provide better protection, reliability, and functionality. Microwave-assisted curing is one area of active research and development, with several emerging trends and future directions that could shape the industry in the coming years.
One trend is the development of new coating materials that are specifically designed for microwave processing. These materials may incorporate novel fillers, resins, or additives that enhance their microwave absorption, curing speed, and final properties. For example, researchers are exploring the use of carbon nanotubes, graphene, and other nanomaterials as microwave-absorbing fillers that can improve the thermal and electrical conductivity of PCB coatings.
Another trend is the integration of microwave curing with other advanced manufacturing technologies, such as 3D printing, inkjet printing, and roll-to-roll processing. By combining these technologies, it may be possible to create highly customized and multifunctional PCB coatings that are tailored to specific applications or environments. For example, 3D-printed coatings could be used to create complex geometries or gradients that enhance the thermal management or electromagnetic shielding of PCBs.
There is also growing interest in the use of microwave curing for sustainable and eco-friendly PCB manufacturing. Microwave processing can reduce energy consumption and greenhouse gas emissions compared to conventional oven curing, and it may also enable the use of more environmentally benign coating materials and solvents. Researchers are exploring the use of bio-based resins, water-based solvents, and other sustainable chemistry approaches that could make PCB coating more environmentally friendly.
Finally, there is a need for continued research and development of microwave equipment and process control technologies. This includes the design of more efficient and versatile microwave applicators, as well as advanced sensors, monitoring systems, and machine learning algorithms that can optimize the curing process in real-time. By improving the reliability, reproducibility, and scalability of microwave-assisted PCB coating, these technologies could help to accelerate the adoption and commercialization of this promising approach.
Frequently Asked Questions
- What are the main advantages of microwave-assisted PCB coating compared to conventional oven curing?
Microwave-assisted PCB coating offers several advantages, including faster curing times, reduced energy consumption, and improved coating quality. By using microwave energy to directly heat the coating material, the curing process can be completed much faster than in conventional ovens, often in a matter of minutes instead of hours. This can lead to significant time and energy savings, as well as higher throughput and productivity. Additionally, the selective and volumetric heating nature of microwaves can result in more uniform and efficient curing, with better adhesion, hardness, and chemical resistance of the final coating.
- What factors influence the efficiency and uniformity of microwave heating in PCB coating applications?
Several factors can influence the efficiency and uniformity of microwave heating in PCB coating applications, including the dielectric properties of the coating material, the frequency and power of the microwave energy, and the design of the microwave applicator. The dielectric properties, such as the dielectric constant and loss factor, determine how well the material absorbs and converts microwave energy into heat. The choice of microwave frequency (typically 915 MHz or 2.45 GHz) can impact the depth of penetration and heating uniformity, while the applicator design (single-mode or multi-mode) affects the focusing and control of the heating process. Other factors, such as the size and shape of the PCBs, the thickness and composition of the coating material, and the desired heating pattern, must also be considered for optimal results.
- What are some of the challenges and limitations of microwave-assisted PCB coating?
Microwave-assisted PCB coating presents several challenges and limitations that must be addressed for successful implementation. One challenge is the complexity of the microwave heating process, which requires careful design and optimization of the applicator and precise control of the processing parameters. Uneven heating and hot spots can occur due to the preferential heating of certain PCB components or areas, leading to thermal stress and damage. The limited penetration depth of microwaves can also be a limitation for thick coatings or large PCBs. Additionally, the cost and availability of microwave equipment, as well as the need for specialized training and infrastructure, can be barriers to adoption for some manufacturers.
- How can uneven heating and thermal stress be mitigated in microwave-assisted PCB coating?
To mitigate uneven heating and thermal stress in microwave-assisted PCB coating, several techniques can be employed. Mode stirring, which involves using a rotating metallic fan to distribute the microwave energy more evenly within the applicator, can help to reduce hot spots and improve heating uniformity. Sample rotation, where the PCB is rotated during the curing process, can also promote more uniform heating. Hybrid heating, which combines microwave energy with convective or infrared heating, can provide more gradual and controlled heating that reduces thermal stress. Additionally, careful optimization of the microwave power, frequency, and exposure time, as well as the use of temperature monitoring and feedback control systems, can help to ensure that the heating process remains within safe and effective limits.
- What are some emerging trends and future research directions in microwave-assisted PCB coating?
There are several emerging trends and future research directions in microwave-assisted PCB coating that could shape the industry in the coming years. One trend is the development of new coating materials that are specifically designed for microwave processing, incorporating novel fillers, resins, or additives that enhance microwave absorption, curing speed, and final properties. Another trend is the integration of microwave curing with other advanced manufacturing technologies, such as 3D printing, inkjet printing, and roll-to-roll processing, to create highly customized and multifunctional PCB coatings. There is also growing interest in using microwave curing for sustainable and eco-friendly PCB manufacturing, by reducing energy consumption and enabling the use of more environmentally benign coating materials and solvents. Finally, continued research and development of microwave equipment and process control technologies, including advanced applicators, sensors, monitoring systems, and machine learning algorithms, could help to optimize the curing process and accelerate the adoption and commercialization of microwave-assisted PCB coating.
Conclusion
Microwave-assisted curing of PCB coatings is a promising technology that offers significant benefits over traditional oven curing methods. By using microwave energy to directly heat the coating material, the curing process can be completed faster, with reduced energy consumption and improved coating quality. However, the complexity of the microwave heating process, the potential for uneven heating and thermal stress, and the limitations of microwave penetration depth present challenges that must be addressed for successful implementation.
Emerging trends and future research directions in microwave-assisted PCB coating include the development of new coating materials optimized for microwave processing, the integration of microwave curing with other advanced manufacturing technologies, the pursuit of sustainable and eco-friendly PCB manufacturing, and the continued advancement of microwave equipment and process control technologies.
As the electronics industry continues to evolve and demand higher performance, reliability, and functionality from PCBs, microwave-assisted coating will likely play an increasingly important role in meeting these challenges. By leveraging the unique advantages of microwave heating and addressing the associated challenges and limitations, manufacturers can unlock new possibilities for PCB coating and push the boundaries of what is possible in electronic packaging and protection.
No responses yet