Introduction to Automotive PCBs
Automotive Printed Circuit Boards (PCBs) are essential components in modern vehicles, playing a crucial role in enabling various electronic systems and features. As the automotive industry continues to evolve and integrate more advanced technologies, the demand for high-quality, reliable, and durable automotive PCBs has skyrocketed. In this comprehensive guide, we will delve into the world of automotive PCBs, discussing their importance, design considerations, manufacturing processes, testing methods, and future trends.
What are Automotive PCBs?
Automotive PCBs are specialized printed circuit boards designed to withstand the harsh environmental conditions and demanding performance requirements of vehicles. These PCBs are found in various electronic systems within a vehicle, such as:
- Engine control units (ECUs)
- Infotainment systems
- Advanced driver assistance systems (ADAS)
- Body control modules
- Powertrain control modules
Unlike PCBs used in consumer electronics, automotive PCBs must adhere to stringent quality and reliability standards to ensure optimal performance and safety in the challenging automotive environment.
Importance of Automotive PCBs
Automotive PCBs play a vital role in the functioning and performance of modern vehicles. They enable the integration of various electronic systems, sensors, and actuators, allowing for the implementation of advanced features and functionalities. Some key benefits of automotive PCBs include:
- Enhanced vehicle performance
- Improved fuel efficiency
- Increased safety features
- Better driver experience
- Reduced emissions
As vehicles become more complex and reliant on electronics, the importance of automotive PCBs continues to grow, driving innovation and shaping the future of the automotive industry.
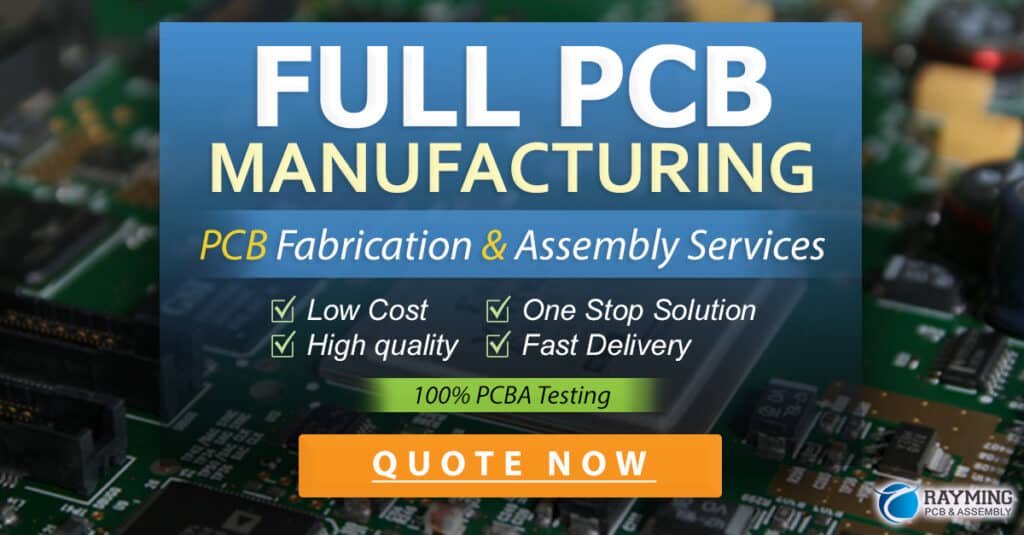
Automotive PCB Design Considerations
Designing automotive PCBs requires careful consideration of various factors to ensure optimal performance, reliability, and durability. Some key design considerations include:
1. Environmental Factors
Automotive PCBs must withstand extreme temperatures, vibrations, shocks, and exposure to moisture, dust, and chemicals. Designers must select appropriate materials, components, and manufacturing techniques to ensure the PCBs can operate reliably in these harsh conditions.
2. EMI/EMC Compliance
Electromagnetic interference (EMI) and electromagnetic compatibility (EMC) are critical concerns in automotive electronics. PCBs must be designed to minimize EMI emissions and maintain proper functioning in the presence of external electromagnetic fields.
3. Size and Weight Constraints
As vehicles become more compact and lightweight, automotive PCBs must be designed to fit within limited spaces while minimizing weight. This often requires the use of high-density interconnect (HDI) technologies and advanced packaging techniques.
4. Signal Integrity and Power Management
Automotive PCBs must ensure proper signal integrity and power management to maintain reliable communication between electronic components and prevent signal degradation or power fluctuations.
5. Thermal Management
Effective thermal management is crucial for automotive PCBs to prevent overheating and ensure optimal performance. Designers must incorporate appropriate thermal management techniques, such as heat sinks, thermal vias, and proper component placement.
Automotive PCB Manufacturing Processes
Manufacturing automotive PCBs requires specialized processes and techniques to meet the stringent quality and reliability requirements of the automotive industry. Some key manufacturing processes include:
- Material selection
- PCB layout and routing
- Solder mask and silkscreen application
- Surface finish (e.g., ENIG, HASL, OSP)
- Automated optical inspection (AOI)
- Electrical testing
- Conformal coating
These processes must be carefully controlled and monitored to ensure consistent quality and reliability across all manufactured PCBs.
Automotive PCB Testing and Validation
To ensure automotive PCBs meet the required performance and reliability standards, rigorous testing and validation processes are employed. Some common testing methods include:
- Environmental stress testing (e.g., temperature cycling, thermal shock, vibration, humidity)
- Functional testing
- In-circuit testing (ICT)
- Boundary scan testing (BST)
- Burn-in testing
- Accelerated life testing (ALT)
These tests help identify potential issues and validate the PCB’s performance under various operating conditions, ensuring the final product meets the necessary automotive standards.
Automotive PCB Standards and Certifications
Automotive PCBs must comply with various industry standards and certifications to ensure safety, reliability, and compatibility. Some key standards and certifications include:
- ISO/TS 16949 (Quality management system for automotive production)
- AEC-Q100 (Stress test qualification for integrated circuits)
- IPC-6012 (Qualification and performance specification for rigid printed boards)
- IPC-A-610 (Acceptability of electronic assemblies)
- IATF 16949 (Quality management system for automotive production)
Compliance with these standards demonstrates a manufacturer’s commitment to producing high-quality automotive PCBs that meet the industry’s stringent requirements.
Future Trends in Automotive PCBs
As the automotive industry continues to evolve, several trends are shaping the future of automotive PCBs:
- Miniaturization and increased functionality
- Adoption of advanced technologies (e.g., 5G, AI, IoT)
- Emphasis on sustainability and eco-friendly materials
- Increased focus on cybersecurity
- Growing demand for electric and autonomous vehicles
These trends are driving innovation in automotive PCB design, manufacturing, and testing, leading to the development of more advanced, reliable, and efficient electronic systems in vehicles.
Frequently Asked Questions (FAQ)
1. What is the difference between automotive PCBs and regular PCBs?
Automotive PCBs are designed to withstand the harsh environmental conditions and demanding performance requirements of vehicles, while regular PCBs are used in less demanding applications, such as consumer electronics.
2. What materials are commonly used in automotive PCBs?
Common materials used in automotive PCBs include FR-4, polyimide, and high-Tg laminates, which offer excellent thermal stability, mechanical strength, and electrical properties.
3. How do automotive PCBs ensure reliability in harsh environments?
Automotive PCBs ensure reliability through careful design considerations, selection of appropriate materials, and rigorous testing and validation processes that simulate the harsh operating conditions found in vehicles.
4. What are some key standards and certifications for automotive PCBs?
Key standards and certifications for automotive PCBs include ISO/TS 16949, AEC-Q100, IPC-6012, IPC-A-610, and IATF 16949, which ensure quality, reliability, and compatibility with automotive industry requirements.
5. How are automotive PCBs evolving to meet future needs?
Automotive PCBs are evolving to meet future needs through miniaturization, integration of advanced technologies, adoption of sustainable materials, increased focus on cybersecurity, and support for electric and autonomous vehicles.
Conclusion
Automotive PCBs are critical components in modern vehicles, enabling the integration of advanced electronic systems and features. As the automotive industry continues to evolve, the demand for high-quality, reliable, and durable automotive PCBs will only increase. By understanding the importance of automotive PCBs, their design considerations, manufacturing processes, testing methods, and future trends, manufacturers and designers can ensure the development of cutting-edge electronic systems that meet the stringent requirements of the automotive industry.
No responses yet