How AXI Works
The AXI process involves the use of an X-ray source and a detector array. The object to be inspected is placed between the X-ray source and the detector. As the X-rays pass through the object, they are attenuated based on the material’s density and thickness. The detector captures the attenuated X-rays and converts them into a digital image, which can be analyzed using specialized software.
X-ray Sources
There are two main types of X-ray sources used in AXI systems:
-
Sealed tube X-ray sources: These are the most common type of X-ray sources used in AXI. They consist of a vacuum tube with a cathode and an anode. When a high voltage is applied between the cathode and anode, electrons are emitted from the cathode and accelerated towards the anode, producing X-rays upon impact.
-
Micro-focus X-ray sources: These sources offer higher resolution and better image quality compared to sealed tube sources. They use a smaller focal spot size, which allows for sharper images and improved defect detection capabilities.
Detectors
AXI systems use digital detectors to capture the attenuated X-rays and convert them into digital images. There are two main types of detectors:
-
Flat panel detectors: These detectors consist of a large array of pixels that directly convert X-rays into electrical signals. They offer high resolution, fast image acquisition, and a large field of view.
-
Line scan detectors: These detectors use a linear array of pixels that scan across the object to create an image. They offer high scanning speeds and are well-suited for inspecting objects with a constant cross-section, such as wires or pipes.
Image Analysis Software
Once the digital image is acquired, specialized software is used to analyze the image and detect defects. The software uses algorithms to compare the captured image to a reference image or CAD model of the object, identifying any deviations or anomalies. The software can also measure dimensions, check for proper assembly, and verify the presence of required components.
Benefits of AXI
AXI offers several advantages over traditional inspection methods:
-
Non-destructive testing: AXI allows for the inspection of objects without damaging or altering them, making it ideal for quality control in manufacturing.
-
High-speed inspection: AXI systems can inspect objects quickly, enabling high throughput and reducing production time.
-
Improved defect detection: AXI can detect defects that may not be visible to the naked eye or other inspection methods, such as hidden cracks, voids, or inclusions.
-
Automated process: AXI systems can be fully automated, reducing the need for manual inspection and minimizing the risk of human error.
-
Cost-effective: While the initial investment in an AXI system may be high, the long-term cost savings from improved quality control and reduced scrap rates can be significant.
Applications of AXI
AXI is used in various industries for quality control and defect detection:
Electronics Industry
In the electronics industry, AXI is primarily used for inspecting PCBs. It can detect a wide range of defects, including:
- Missing components
- Incorrect component placement
- Solder joint defects (e.g., voids, bridges, insufficient solder)
- Broken or damaged components
- Short circuits
- Counterfeit components
AXI is particularly useful for inspecting high-density PCBs with small components, such as ball grid arrays (BGAs) and quad flat no-leads (QFNs), which are difficult to inspect using other methods.
Automotive Industry
In the automotive industry, AXI is used for inspecting various components, such as:
- Castings and forgings
- Welded assemblies
- Electrical connectors
- Airbag inflators
- Fuel injectors
AXI can detect defects such as cracks, porosity, inclusions, and dimensional inconsistencies, ensuring the safety and reliability of automotive components.
Aerospace Industry
The aerospace industry relies on AXI for inspecting critical components, such as:
- Turbine blades
- Composite structures
- Fasteners
- Wiring harnesses
- Hydraulic components
AXI helps ensure the integrity and performance of these components, which are subject to extreme conditions during flight.
Medical Device Industry
AXI is used in the medical device industry to inspect implantable devices, surgical instruments, and other critical components for defects that could compromise patient safety. Examples include:
- Orthopedic implants
- Pacemakers
- Catheters
- Stents
- Syringes
AXI can detect defects such as cracks, voids, and dimensional inconsistencies, ensuring the quality and reliability of medical devices.
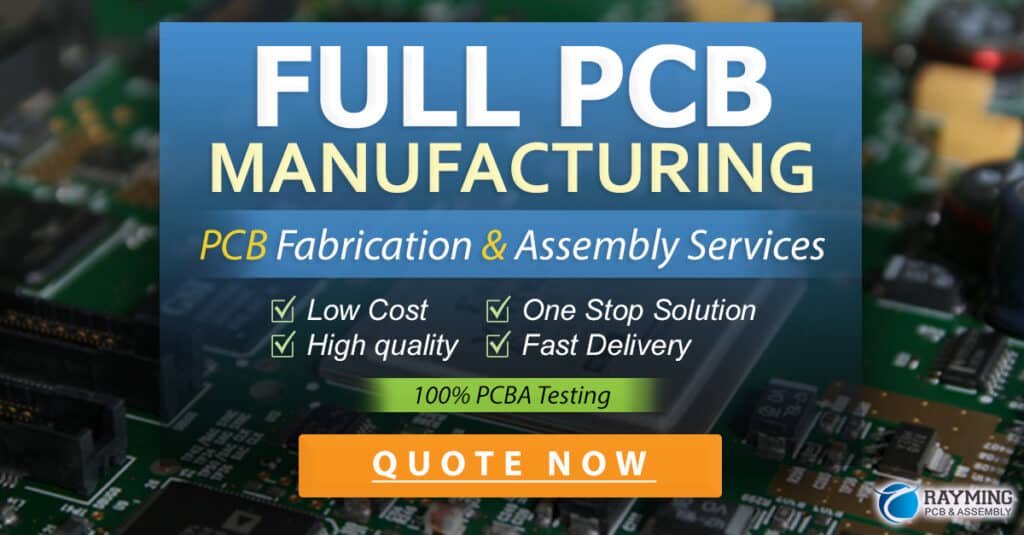
Challenges and Limitations of AXI
While AXI offers numerous benefits, there are some challenges and limitations to consider:
-
Initial investment: AXI systems can be expensive, requiring a significant upfront investment in equipment and software.
-
Operator training: Operating an AXI system requires specialized knowledge and skills. Operators must be trained in X-ray safety, system operation, and image interpretation.
-
Limited material penetration: X-rays have limited penetration through dense materials, such as thick metal components, which can limit the effectiveness of AXI for certain applications.
-
Radiation safety: X-rays are a form of ionizing radiation and can be harmful to human health if not properly controlled. AXI systems must be designed and operated in accordance with strict radiation safety regulations.
Future Trends in AXI
As technology advances, AXI systems are becoming more sophisticated and capable. Some of the future trends in AXI include:
-
Increased automation: The integration of artificial intelligence (AI) and machine learning (ML) algorithms into AXI software will enable more automated defect detection and classification, reducing the need for manual image interpretation.
-
Higher resolution imaging: Advances in X-ray source and detector technology will enable higher resolution imaging, allowing for the detection of smaller defects and improved dimensional measurement capabilities.
-
Integration with other NDT methods: AXI can be combined with other non-destructive testing methods, such as ultrasonic testing or computed tomography (CT), to provide a more comprehensive inspection solution.
-
Portable AXI systems: The development of compact, portable AXI systems will enable on-site inspections, reducing the need to transport components to a dedicated inspection facility.
FAQ
-
What is the difference between 2D and 3D AXI?
2D AXI provides a single planar view of the object being inspected, while 3D AXI uses multiple planar views or a rotating X-ray source and detector to create a three-dimensional representation of the object. 3D AXI offers more comprehensive defect detection and measurement capabilities but is typically more expensive and time-consuming than 2D AXI. -
Can AXI detect all types of defects?
While AXI is a powerful inspection tool, it cannot detect all types of defects. Some limitations include the inability to detect surface defects that do not affect the internal structure of the object, as well as defects in materials that are not well-suited for X-ray inspection, such as low-density plastics or materials with similar densities. -
Is AXI safe for operators?
When properly designed and operated in accordance with radiation safety regulations, AXI systems are safe for operators. Operators must be trained in radiation safety and follow proper procedures, such as wearing dosimetry badges and maintaining a safe distance from the X-ray source during operation. -
How long does an AXI inspection take?
The duration of an AXI inspection depends on various factors, including the size and complexity of the object being inspected, the resolution and number of views required, and the speed of the X-ray source and detector. In general, AXI inspections can range from a few seconds to several minutes per object. -
Can AXI be used for inspecting non-metallic objects?
Yes, AXI can be used for inspecting non-metallic objects, such as composites, ceramics, and plastic components. However, the effectiveness of AXI for non-metallic objects depends on the material’s density and the contrast between the material and any defects present. In some cases, other NDT methods may be more suitable for inspecting non-metallic objects.
Industry | Typical Applications | Common Defects Detected |
---|---|---|
Electronics | Printed Circuit Boards (PCBs) | – Missing components – Incorrect component placement – Solder joint defects – Broken or damaged components – Short circuits – Counterfeit components |
Automotive | – Castings and forgings – Welded assemblies – Electrical connectors – Airbag inflators – Fuel injectors |
– Cracks – Porosity – Inclusions – Dimensional inconsistencies |
Aerospace | – Turbine blades – Composite structures – Fasteners – Wiring harnesses – Hydraulic components |
– Cracks – Voids – Delaminations – Foreign object debris (FOD) – Dimensional inconsistencies |
Medical Device | – Orthopedic implants – Pacemakers – Catheters – Stents – Syringes |
– Cracks – Voids – Inclusions – Dimensional inconsistencies |
Conclusion
Automatic X-ray Inspection (AXI) is a powerful non-destructive testing method that offers numerous benefits for quality control and defect detection in various industries. By utilizing X-rays to create detailed images of an object’s internal structure, AXI can detect hidden flaws, defects, and inconsistencies that may not be visible to the naked eye or other inspection methods. As technology continues to advance, AXI systems are becoming more sophisticated, automated, and capable, enabling manufacturers to improve product quality, reduce scrap rates, and ensure the safety and reliability of their products.
No responses yet