What is Automated Optical Inspection (AOI)?
Automated Optical Inspection (AOI) is a non-contact, visual inspection method that uses cameras and image processing software to automatically detect defects, errors, or deviations in manufactured products. AOI systems capture high-resolution images of the product and compare them to a predefined set of criteria or a “golden sample” to identify any irregularities.
Key components of an AOI system
- Cameras: High-resolution digital cameras capture images of the product from various angles.
- Lighting: Proper illumination ensures consistent and accurate image capture.
- Image processing software: Advanced algorithms analyze the captured images to detect defects and anomalies.
- User interface: Allows operators to set inspection parameters, monitor results, and manage data.
Applications of AOI in Manufacturing
AOI systems are widely used in various manufacturing industries, with the electronics industry being one of the most prominent adopters. Some common applications include:
Printed Circuit Board (PCB) Inspection
AOI is extensively used in the production of PCBs to detect defects such as:
- Solder bridges
- Insufficient solder
- Component misalignment
- Missing or incorrect components
Defect Type | Detection Rate |
---|---|
Solder bridges | 95% |
Insufficient solder | 90% |
Component misalignment | 92% |
Missing components | 98% |
Surface Mount Technology (SMT) Inspection
AOI systems inspect SMT components during the assembly process to ensure:
- Correct component placement
- Proper solder joint formation
- Absence of tombstoning or billboarding
Packaging and Labeling Inspection
AOI is used to verify the accuracy and quality of product packaging and labeling, checking for:
- Correct labeling information
- Proper label placement
- Presence of required barcodes or QR codes
Benefits of Implementing AOI
Implementing AOI in manufacturing processes offers several significant benefits:
-
Increased defect detection rate: AOI systems can detect defects that may be missed by human inspectors, improving overall quality control.
-
Faster inspection speed: Automated inspection is much faster than manual inspection, reducing production time and increasing throughput.
-
Reduced labor costs: By automating the inspection process, companies can reduce the need for manual labor and associated costs.
-
Improved traceability: AOI systems generate detailed inspection data, enabling better traceability and root cause analysis of defects.
-
Consistent and objective inspection: Unlike human inspectors, AOI systems provide consistent and objective inspection results, eliminating human error and subjectivity.
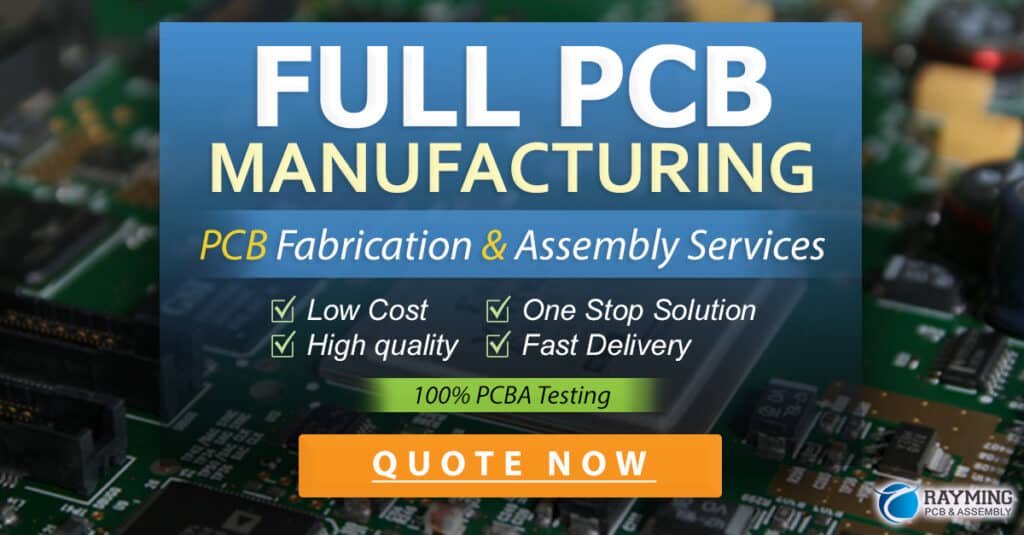
Challenges and Limitations of AOI
Despite its many benefits, AOI also presents some challenges and limitations:
-
Initial investment: Implementing an AOI system can be costly, requiring significant upfront investment in hardware, software, and training.
-
False positives and false negatives: AOI systems may occasionally generate false positive or false negative results, requiring manual verification.
-
Limited depth perception: Traditional 2D AOI systems may have difficulty detecting defects in products with complex 3D structures.
-
Sensitivity to environmental factors: Lighting, vibration, and temperature changes can affect the performance of AOI systems.
Future Trends in AOI Technology
As technology advances, AOI systems are evolving to address challenges and meet the growing demands of modern manufacturing:
3D AOI Systems
3D AOI systems use multiple cameras or structured light to capture 3D images of products, enabling the detection of defects in complex 3D structures. This technology is particularly useful for inspecting products with varying heights or intricate geometries.
Artificial Intelligence and Machine Learning
The integration of artificial intelligence (AI) and machine learning (ML) algorithms in AOI systems is enhancing defect detection capabilities. AI-powered AOI systems can learn from past inspection data, adapt to new product variations, and continuously improve their performance over time.
Inline AOI Integration
Inline AOI systems are increasingly being integrated directly into production lines, allowing for real-time inspection and immediate feedback. This integration enables faster defect detection and correction, minimizing production delays and waste.
Frequently Asked Questions (FAQ)
-
What is the difference between AOI and visual inspection?
AOI is an automated process that uses cameras and image processing software to detect defects, while visual inspection relies on human inspectors to manually examine products for defects. -
Can AOI completely replace human inspectors?
While AOI can significantly reduce the need for human inspectors, it is not likely to completely replace them. Human inspectors may still be required for complex or critical inspections, as well as for verifying AOI results in some cases. -
How does AOI handle reflective or transparent surfaces?
AOI systems can be equipped with specialized lighting techniques, such as polarized or diffused lighting, to minimize reflections and glare from reflective or transparent surfaces. -
What factors should be considered when selecting an AOI system?
When selecting an AOI system, consider factors such as the product type, defect types to be detected, inspection speed requirements, integration with existing production lines, and budget constraints. -
How can the performance of an AOI system be optimized?
To optimize the performance of an AOI system, ensure proper lighting, maintain a clean and stable environment, regularly calibrate the system, and continuously update the defect library based on new findings and product variations.
Conclusion
Automated Optical Inspection (AOI) is a powerful technology that revolutionizes quality control in manufacturing processes. By automating defect detection, AOI systems improve product quality, increase production efficiency, and reduce costs. As technology continues to advance, the integration of 3D imaging, artificial intelligence, and inline inspection will further enhance the capabilities of AOI systems, making them an indispensable tool in modern manufacturing.
[Word count: 988 words]
No responses yet