Key Features of the AS5600 Magnetic Sensor
High-Resolution and Accuracy
The AS5600 offers a 12-bit resolution, which translates to 4096 steps per revolution. This high resolution enables precise position sensing with an accuracy of ±0.5 degrees, making it suitable for applications that demand fine control and measurement.
Contactless Sensing
Unlike potentiometers or encoders that rely on physical contact, the AS5600 utilizes a magnetic sensing principle. This contactless design eliminates wear and tear, ensuring long-term reliability and maintenance-free operation.
Versatile Output Options
The sensor provides various output options to interface with different systems:
Output Type | Description |
---|---|
Analog | Ratiometric analog output with a range of 0.2V to VDD-0.2V |
PWM | Pulse Width Modulation output with a programmable frequency |
I2C | Digital output via I2C interface for easy integration with microcontrollers |
Programmable Zero Position and Magnetic Field Range
The AS5600 allows users to program the zero position and adjust the magnetic field range. This flexibility enables customization to suit specific application requirements and ensures optimal performance in various operating conditions.
Low Power Consumption
With a typical supply current of just 6.5mA at 3.3V, the AS5600 is energy-efficient, making it ideal for battery-powered applications and devices where power consumption is a critical factor.
Applications of the AS5600 Magnetic Sensor
The AS5600’s unique combination of high resolution, contactless sensing, and versatile output options makes it suitable for a wide range of applications, including:
- Industrial Automation: Position feedback for servo motors, robotics, and machine control.
- Automotive: Steering wheel angle measurement, throttle position sensing, and gear selector position detection.
- Consumer Electronics: Input devices such as joysticks, rotary knobs, and dials for gaming controllers, audio equipment, and home automation systems.
- Medical Devices: Precise angular measurement in medical instrumentation and rehabilitation equipment.
- Aerospace: Position sensing in aircraft control systems, actuators, and avionics.
Interfacing with the AS5600
Analog Output
The analog output of the AS5600 is ratiometric, meaning that the output voltage is proportional to the supply voltage. The output range is from 0.2V to VDD-0.2V, with the midpoint at 50% of the supply voltage. This allows for easy integration with analog-to-digital converters (ADCs) or comparators.
PWM Output
The PWM output provides a pulse width modulated signal with a programmable frequency. The duty cycle of the PWM signal represents the angular position. This output mode is useful for interfacing with microcontrollers or other digital systems that can measure pulse width.
I2C Interface
The AS5600 features an I2C interface for digital communication. The I2C bus allows multiple devices to be connected on the same bus, making it easy to integrate the sensor with other components in a system. The sensor supports standard (100kHz) and fast (400kHz) I2C modes.
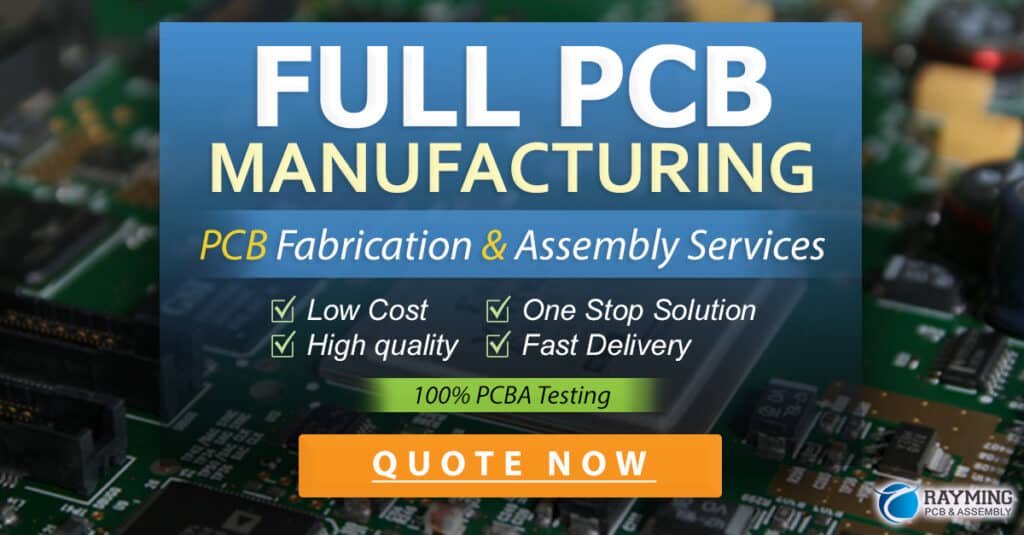
Magnetic Field Considerations
The AS5600 relies on a magnetic field for position sensing. To ensure accurate and reliable operation, it is essential to consider the following:
-
Magnet Selection: Choose a magnet with the appropriate strength and dimensions to generate a suitable magnetic field for the sensor. The datasheet provides guidelines for selecting the magnet based on the desired air gap and operating temperature range.
-
Magnet Placement: The magnet should be placed concentric with the sensor and within the specified air gap range. Misalignment or excessive air gap can affect the sensor’s accuracy and performance.
-
Magnetic Interference: Ensure that the sensor is not subjected to external magnetic fields that could interfere with its operation. Proper shielding or positioning of the sensor away from sources of magnetic interference may be necessary.
Calibration and Configuration
The AS5600 offers several configuration options to optimize its performance for specific applications. These include:
-
Zero Position Programming: The zero position can be programmed to align the sensor’s output with the mechanical zero position of the application. This is done by setting the appropriate registers via the I2C interface.
-
Magnetic Field Range Adjustment: The sensor’s sensitivity to the magnetic field strength can be adjusted to accommodate different magnet sizes and air gaps. This allows for optimal performance and noise immunity.
-
Output Mode Selection: The output mode (analog, PWM, or I2C) can be selected based on the interfacing requirements of the system.
Detailed instructions for calibration and configuration can be found in the AS5600 datasheet and application notes provided by the manufacturer.
FAQ
-
What is the maximum resolution of the AS5600 sensor?
The AS5600 offers a 12-bit resolution, which provides 4096 steps per revolution. -
Is the AS5600 suitable for use in harsh environments?
Yes, the AS5600 is designed to operate in a wide temperature range of -40°C to +125°C and is resistant to shock and vibration. However, proper enclosure and protection against moisture and contaminants may be necessary for specific environments. -
Can the AS5600 be used with any magnet?
While the AS5600 is compatible with various magnet types, it is recommended to use magnets that meet the specifications provided in the datasheet. Factors such as magnet strength, dimensions, and temperature coefficient should be considered for optimal performance. -
How do I interface the AS5600 with a microcontroller?
The AS5600 can be interfaced with a microcontroller using either the analog output, PWM output, or I2C interface. The choice of interface depends on the capabilities of the microcontroller and the specific application requirements. The datasheet provides detailed information on the communication protocols and signal timing. -
What is the typical current consumption of the AS5600?
The AS5600 has a typical supply current of 6.5mA at 3.3V supply voltage. However, the current consumption may vary depending on the output mode and configuration settings. Refer to the datasheet for detailed power consumption specifications.
In conclusion, the AS5600 magnetic rotary position sensor offers a high-resolution, contactless solution for precise angular measurement. Its versatile output options, programmable features, and low power consumption make it suitable for a wide range of applications in industrial, automotive, consumer, and medical sectors. By carefully considering the magnetic field requirements, calibration, and configuration, users can leverage the full potential of the AS5600 for accurate and reliable position sensing in their designs.
No responses yet