What is Automated Optical Inspection (AOI)?
Automated Optical Inspection is a computerized visual inspection system that uses high-resolution cameras, advanced image processing software, and machine learning algorithms to detect and identify defects in manufactured products. AOI systems compare the captured images of the products with a pre-defined set of design specifications and quality standards to determine if the product meets the required criteria.
AOI Testing is widely used in the electronics industry for inspecting PCBs, surface-mounted devices (SMDs), and other electronic components. However, its applications extend to various other industries, such as automotive, aerospace, medical devices, and packaging.
How Does AOI Testing Work?
The AOI testing process involves several key steps:
-
Image Acquisition: High-resolution cameras capture detailed images of the product from multiple angles and lighting conditions. The cameras used in AOI systems typically have a resolution of 1-5 megapixels and can capture images at high speeds.
-
Image Processing: The captured images are then processed using advanced image processing algorithms to enhance the image quality, remove noise, and highlight the relevant features of the product. This step ensures that the defects are clearly visible and can be easily detected by the system.
-
Defect Detection: The processed images are compared with a pre-defined set of design specifications and quality standards using machine learning algorithms. These algorithms are trained to identify specific types of defects, such as missing components, incorrect component placement, solder bridges, and insufficient solder joints.
-
Defect Classification: Once the defects are detected, the AOI system classifies them based on their type, severity, and location. This information is then used to generate a detailed report of the inspection results, which can be used by the manufacturing team to identify the root cause of the defects and take corrective action.
Benefits of AOI Testing
AOI testing offers several significant benefits over traditional manual inspection methods:
-
Increased Accuracy: AOI systems are highly accurate and can detect even the smallest defects that may be missed by human inspectors. This increased accuracy helps to reduce the number of defective products that reach the end-users, thereby improving customer satisfaction and reducing warranty claims.
-
Faster Inspection Speeds: AOI systems can inspect products at much faster speeds compared to manual inspection methods. This increased speed enables manufacturers to inspect a larger number of products in a shorter amount of time, thereby increasing production throughput and reducing lead times.
-
Reduced Labor Costs: AOI testing eliminates the need for manual inspection, which can be time-consuming and labor-intensive. By automating the inspection process, manufacturers can reduce labor costs and redeploy their workforce to other value-added tasks.
-
Improved Traceability: AOI systems generate detailed reports of the inspection results, which can be used to track the quality of the products throughout the manufacturing process. This improved traceability helps manufacturers to identify the root cause of defects and take corrective action to prevent their recurrence.
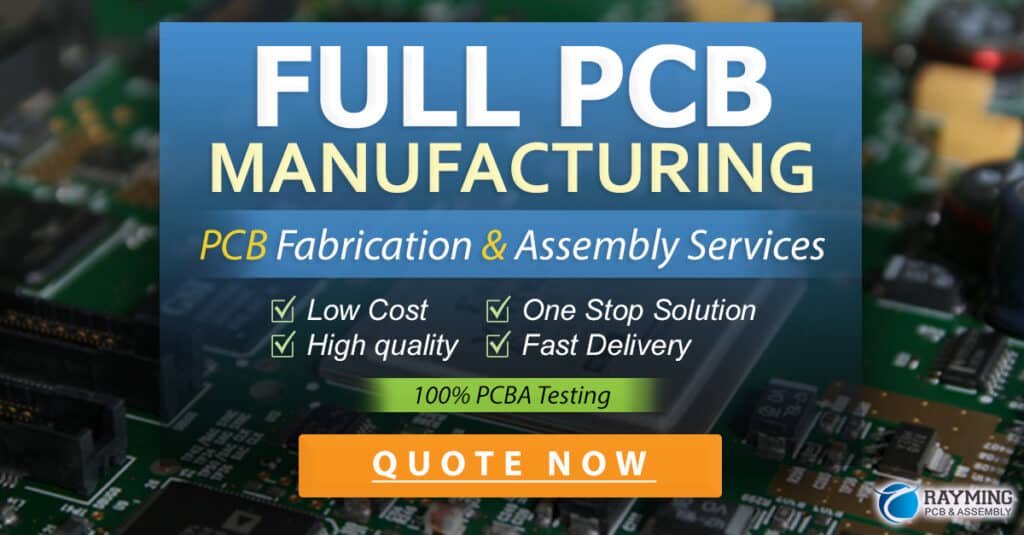
Applications of AOI Testing
AOI testing is used in a wide range of industries for various applications, including:
PCB Inspection
AOI testing is widely used in the electronics industry for inspecting PCBs at various stages of the manufacturing process, such as:
-
Solder Paste Inspection (SPI): AOI systems are used to inspect the solder paste deposition on the PCB before the components are placed. SPI helps to ensure that the solder paste is applied correctly and in the right amount, which is critical for ensuring a reliable solder joint.
-
Pre-Reflow Inspection: AOI systems are used to inspect the PCB after the components are placed but before the solder reflow process. Pre-reflow inspection helps to ensure that the components are placed correctly and that there are no missing or misaligned components.
-
Post-Reflow Inspection: AOI systems are used to inspect the PCB after the solder reflow process to ensure that the solder joints are formed correctly and that there are no defects, such as solder bridges or insufficient solder.
SMT Inspection
Surface-mount technology (SMT) is a method of assembling electronic components onto PCBs. AOI testing is used to inspect SMT components at various stages of the assembly process, such as:
-
Component Placement Inspection: AOI systems are used to inspect the placement of SMT components on the PCB to ensure that they are placed correctly and in the right orientation.
-
Solder Joint Inspection: AOI systems are used to inspect the solder joints of SMT components to ensure that they are formed correctly and that there are no defects, such as solder bridges or insufficient solder.
Packaging Inspection
AOI testing is also used in the packaging industry to inspect various types of packaging materials, such as:
-
Label Inspection: AOI systems are used to inspect the placement, alignment, and quality of labels on packaging materials to ensure that they meet the required specifications.
-
Print Inspection: AOI systems are used to inspect the print quality of packaging materials, such as barcodes, logos, and text, to ensure that they are legible and meet the required specifications.
-
Seal Inspection: AOI systems are used to inspect the seals of packaging materials, such as blister packs and clamshell packaging, to ensure that they are sealed correctly and that there are no leaks or defects.
Limitations of AOI Testing
While AOI testing offers several significant benefits, it also has some limitations that need to be considered:
-
Limited Depth Perception: AOI systems rely on 2D imaging technology, which means that they have limited depth perception. This limitation can make it difficult to detect certain types of defects, such as lifted leads or bent pins, which require 3D imaging technology.
-
False Positives and False Negatives: AOI systems can sometimes generate false positives (detecting defects that are not actually present) or false negatives (failing to detect actual defects). These errors can be caused by various factors, such as poor image quality, incorrect lighting conditions, or inadequate programming of the machine learning algorithms.
-
High Initial Cost: AOI systems can be expensive to purchase and implement, especially for small and medium-sized manufacturers. The high initial cost can be a barrier to adoption for some companies.
-
Need for Skilled Operators: While AOI systems are automated, they still require skilled operators to set up, program, and maintain the system. The need for skilled operators can be a challenge for some companies, especially those with limited resources or expertise in the field.
Future Trends in AOI Testing
As technology continues to advance, AOI testing is expected to evolve and improve in several key areas:
-
3D AOI: The development of 3D AOI technology is expected to address some of the limitations of 2D imaging, such as limited depth perception. 3D AOI systems use multiple cameras and advanced image processing algorithms to create a 3D model of the product, which can be used to detect defects that are difficult to detect using 2D imaging.
-
AI and Machine Learning: The integration of artificial intelligence (AI) and machine learning technologies into AOI systems is expected to improve the accuracy and efficiency of defect detection. AI-powered AOI systems can learn from past inspection data to improve their defect detection capabilities over time.
-
Inline AOI: Inline AOI systems are expected to become more prevalent in the future, as they enable manufacturers to inspect products in real-time as they move through the production line. Inline AOI can help to identify defects early in the manufacturing process, thereby reducing the number of defective products that reach the end-users.
-
Cloud-Based AOI: The development of cloud-based AOI systems is expected to make AOI technology more accessible and affordable for small and medium-sized manufacturers. Cloud-based AOI systems can be accessed remotely, which eliminates the need for expensive hardware and infrastructure.
Frequently Asked Questions (FAQs)
-
What is the difference between AOI and visual inspection?
AOI is an automated inspection process that uses advanced imaging technology and machine learning algorithms to detect defects, while visual inspection is a manual process that relies on human inspectors to identify defects using their eyes and experience. -
Can AOI replace visual inspection entirely?
While AOI can greatly reduce the need for manual visual inspection, it may not be able to replace it entirely. Some types of defects, such as cosmetic defects or defects that require subjective judgment, may still require manual inspection. -
How much does an AOI system cost?
The cost of an AOI system can vary depending on the size, complexity, and features of the system. Small desktop AOI systems can cost around $50,000, while large inline AOI systems can cost upwards of $500,000. -
What are the most common defects that AOI can detect?
AOI systems can detect a wide range of defects, including missing components, incorrect component placement, solder bridges, insufficient solder joints, and print defects. -
Can AOI be used for inspecting products other than PCBs and electronic components?
Yes, AOI can be used for inspecting a wide range of products, including automotive parts, medical devices, packaging materials, and consumer goods.
Conclusion
Automated Optical Inspection (AOI) is a powerful tool for ensuring the quality and reliability of manufactured products. By using advanced imaging technology and machine learning algorithms, AOI systems can detect defects that are difficult or impossible to detect using manual inspection methods. While AOI has some limitations, such as limited depth perception and high initial costs, the benefits of increased accuracy, faster inspection speeds, and reduced labor costs make it an attractive option for manufacturers across a wide range of industries.
As technology continues to evolve, AOI testing is expected to become even more powerful and accessible, with the development of 3D AOI, AI and machine learning, inline AOI, and cloud-based AOI systems. By staying up-to-date with the latest trends and technologies in AOI testing, manufacturers can ensure that they are producing the highest quality products possible while minimizing costs and maximizing efficiency.
Aspect | Manual Inspection | AOI Inspection |
---|---|---|
Accuracy | Low to Moderate | High |
Speed | Slow | Fast |
Labor Cost | High | Low |
Consistency | Variable | Consistent |
Subjectivity | High | Low |
Defect Detection Range | Limited | Wide |
Scalability | Limited | High |
Initial Investment Cost | Low | High |
Training Required | Moderate | High (for setup) |
Fatigue Factor | High | Low |
Table 1: Comparison of Manual Inspection and AOI Inspection
No responses yet