Understanding Polygon Pour Breaks in Altium Designer
When designing Rigid-flex PCBs in Altium Designer, one of the common issues encountered is the breaking of polygon pours along the split lines between the rigid and flexible sections. This can lead to unintended electrical disconnections and potential manufacturing problems. In this article, we will explore the causes of polygon pour breaks, discuss best practices for avoiding them, and provide step-by-step solutions to ensure proper continuity of your polygon pours across rigid-flex split lines.
What are Polygon Pours?
Polygon pours, also known as copper fills or copper pours, are large areas of copper used to provide a low-impedance connection to ground or power planes on a PCB. They help to reduce electromagnetic interference (EMI), improve signal integrity, and dissipate heat. In Altium Designer, polygon pours are created using the “Pour” command and can be customized with various settings such as net name, layer, and clearance rules.
Rigid-Flex PCB Design Considerations
Rigid-flex PCBs combine the benefits of both rigid and flexible substrates, allowing for more compact and versatile designs. However, designing rigid-flex PCBs comes with its own set of challenges, particularly when it comes to maintaining continuity of copper features across the rigid-flex boundaries.
Defining Split Lines
Split lines are used to define the boundaries between the rigid and flexible sections of a rigid-flex PCB. They are typically represented by a special layer in the PCB design software, such as the “Mechanical 1” layer in Altium Designer. It is essential to properly define and position the split lines to ensure accurate manufacturing and avoid issues like polygon pour breaks.
Bend Radius and Flexibility
When designing rigid-flex PCBs, it is crucial to consider the bend radius and flexibility requirements of the flexible sections. The bend radius refers to the minimum radius that the flexible portion can be bent without causing damage to the copper traces or the substrate. The flexibility of the material used for the flexible sections also plays a role in determining the acceptable bend radius.
Causes of Polygon Pour Breaks
There are several factors that can contribute to the breaking of polygon pours along rigid-flex split lines. Understanding these causes is the first step in preventing and resolving the issue.
Incorrect Split Line Definition
One of the most common causes of polygon pour breaks is the incorrect definition of split lines in the PCB design software. If the split lines are not properly placed or do not accurately represent the intended boundaries between the rigid and flexible sections, it can lead to discontinuities in the polygon pours.
Insufficient Clearance
Another potential cause of polygon pour breaks is insufficient clearance between the polygon pour and the split line. If the clearance is too small, the polygon pour may not extend far enough into the flexible section, resulting in a break along the split line.
Incompatible Bend Radius
If the bend radius of the flexible section is too small for the chosen material or copper thickness, it can cause the polygon pour to break or crack along the split line. This is because the copper may not be able to withstand the stress of the tight bend, leading to mechanical failure.
Manufacturing Limitations
In some cases, polygon pour breaks can occur due to limitations in the manufacturing process. For example, if the PCB fabricator does not have the capability to properly handle and process Rigid-Flex Designs, it may result in issues like poor lamination or misalignment of the layers, which can cause breaks in the polygon pours.
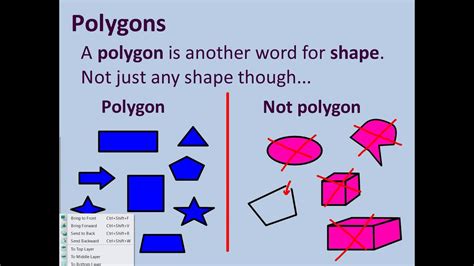
Best Practices for Avoiding Polygon Pour Breaks
To minimize the occurrence of polygon pour breaks in your rigid-flex PCB designs, consider the following best practices:
Proper Split Line Placement
Ensure that the split lines are accurately placed and properly defined in your PCB design software. Pay close attention to the positioning of the split lines relative to the rigid and flexible sections, and make sure they align with the intended manufacturing process.
Adequate Clearance Rules
Set appropriate clearance rules for your polygon pours, taking into account the specific requirements of your rigid-flex design. Provide sufficient clearance between the polygon pour and the split line to ensure proper extension of the pour into the flexible section.
Material Selection
Choose materials that are suitable for your specific bend radius and flexibility requirements. Consider factors such as the copper thickness, substrate material, and adhesive properties when selecting materials for your rigid-flex PCB.
Communication with PCB Fabricator
Collaborate closely with your PCB fabricator throughout the design process. Discuss your rigid-flex design requirements, including the desired bend radius, material specifications, and any specific manufacturing constraints. This open communication can help identify potential issues early on and ensure a smoother manufacturing process.
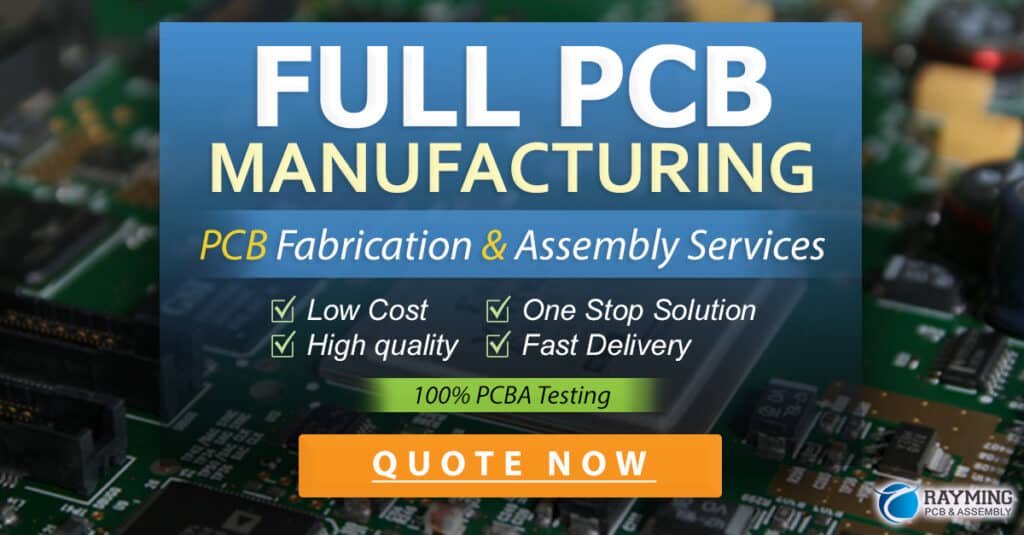
Resolving Polygon Pour Breaks in Altium Designer
If you encounter polygon pour breaks in your Altium Designer projects, follow these steps to resolve the issue:
-
Check Split Line Definition: Verify that the split lines are correctly defined and positioned in your PCB design. Make sure they accurately represent the boundaries between the rigid and flexible sections.
-
Adjust Clearance Rules: Review and adjust the clearance rules for your polygon pours. Increase the clearance between the polygon pour and the split line to ensure proper extension of the pour into the flexible section.
-
Modify Bend Radius: If the bend radius is too small for the chosen material or copper thickness, consider increasing the bend radius or selecting a more suitable material. Consult with your PCB fabricator to determine the appropriate bend radius for your specific design.
-
Update Polygon Pour Settings: In Altium Designer, select the affected polygon pour and access its properties. Verify that the net name, layer, and other settings are correctly configured. If necessary, update the settings to ensure proper continuity across the split line.
-
Regenerate Polygon Pours: After making the necessary adjustments, regenerate the polygon pours in your design. In Altium Designer, you can do this by right-clicking on the polygon pour and selecting “Repour All” from the context menu.
-
Perform Design Rule Check: Run a Design Rule Check (DRC) to identify any remaining issues or violations in your PCB design. Address any flagged problems and ensure that your design complies with the specified rules and constraints.
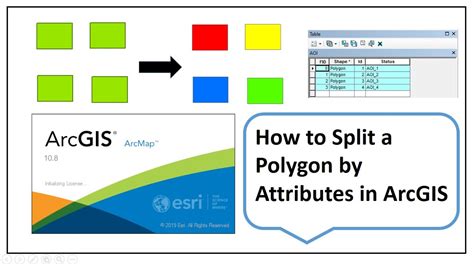
FAQs
1. What causes polygon pour breaks in rigid-flex PCB designs?
Polygon pour breaks in rigid-flex PCB designs can be caused by various factors, including incorrect split line definition, insufficient clearance between the polygon pour and the split line, incompatible bend radius, and manufacturing limitations.
2. How can I prevent polygon pour breaks in my rigid-flex PCB designs?
To prevent polygon pour breaks, ensure proper split line placement, set adequate clearance rules, select suitable materials for your bend radius and flexibility requirements, and maintain close communication with your PCB fabricator.
3. What steps can I take to resolve polygon pour breaks in Altium Designer?
To resolve polygon pour breaks in Altium Designer, check the split line definition, adjust clearance rules, modify the bend radius if necessary, update polygon pour settings, regenerate polygon pours, and perform a Design Rule Check (DRC).
4. How important is the bend radius in rigid-flex PCB design?
The bend radius is crucial in rigid-flex PCB design as it determines the minimum radius that the flexible portion can be bent without causing damage to the copper traces or the substrate. Choosing an appropriate bend radius is essential to ensure the integrity of your polygon pours and overall PCB reliability.
5. Can the choice of materials affect the occurrence of polygon pour breaks?
Yes, the choice of materials can significantly impact the occurrence of polygon pour breaks in rigid-flex PCB designs. Selecting materials that are compatible with your desired bend radius and flexibility requirements can help minimize the risk of polygon pour breaks and ensure proper functionality of your PCB.
Conclusion
Polygon pour breaks along rigid-flex split lines can be a frustrating issue in Altium Designer, but by understanding the causes and following best practices, you can effectively prevent and resolve these breaks. Proper split line definition, adequate clearance rules, suitable material selection, and close collaboration with your PCB fabricator are key to ensuring the continuity of your polygon pours across rigid-flex boundaries.
By applying the techniques and guidelines discussed in this article, you can optimize your rigid-flex PCB designs, minimize the occurrence of polygon pour breaks, and achieve reliable and manufacturable results. Remember to carefully review your design, make necessary adjustments, and leverage the powerful features of Altium Designer to streamline your rigid-flex PCB design process.
Factors Contributing to Polygon Pour Breaks | Prevention Strategies |
---|---|
Incorrect Split Line Definition | Proper Split Line Placement |
Insufficient Clearance | Adequate Clearance Rules |
Incompatible Bend Radius | Material Selection |
Manufacturing Limitations | Communication with PCB Fabricator |
By addressing these factors and implementing the corresponding prevention strategies, you can significantly reduce the occurrence of polygon pour breaks in your rigid-flex PCB designs and ensure the integrity of your copper features across the split lines.
No responses yet