What is an Air-Core Inductor?
An air-core inductor is a passive electronic component that consists of a coil of wire wound around a non-magnetic core, typically air or a non-conductive material. The inductor’s primary function is to store energy in its magnetic field when an electric current passes through it. The stored energy is then released back into the circuit when the current changes.
Key Characteristics of Air-Core Inductors
- Inductance: The inductance of an air-core inductor depends on the number of turns, the coil diameter, and the length of the coil.
- Quality Factor (Q): The quality factor is a measure of the inductor’s efficiency in storing energy. Air-core inductors generally have lower Q values compared to inductors with ferromagnetic cores.
- Self-Resonant Frequency (SRF): The SRF is the frequency at which the inductor’s distributed capacitance resonates with its inductance, causing the inductor to behave like a parallel resonant circuit.
Advantages and Disadvantages of Air-Core Inductors
Advantages
- Low loss: Air-core inductors have lower losses compared to inductors with ferromagnetic cores, especially at high frequencies.
- Linear behavior: The absence of a ferromagnetic core results in a linear relationship between current and magnetic field, making air-core inductors suitable for applications requiring linearity.
- No saturation: Air-core inductors do not suffer from core saturation, which can occur in inductors with ferromagnetic cores when the magnetic field strength exceeds a certain limit.
Disadvantages
- Lower inductance: For a given size, air-core inductors have lower inductance values compared to inductors with ferromagnetic cores.
- Larger size: To achieve the same inductance value as an inductor with a ferromagnetic core, an air-core inductor requires more turns and a larger diameter, resulting in a larger physical size.
- Electromagnetic interference (EMI): Air-core inductors can be more susceptible to EMI due to the absence of a magnetic core that can provide shielding.
Designing an Air-Core Inductor
Coil Geometry
The geometry of the coil plays a crucial role in determining the inductance and performance of an air-core inductor. The most common coil geometries include:
- Solenoid: A solenoid is a cylindrical coil with a uniform diameter and pitch (distance between turns). Solenoids are the most common type of air-core inductor.
- Toroid: A toroidal coil is wound around a donut-shaped form, providing better magnetic field confinement and reduced EMI compared to solenoids.
- Flat spiral: Flat spiral coils are often used in printed circuit board (PCB) designs, where the inductor is created by etching a spiral pattern on the PCB.
Inductance Calculation
The inductance of an air-core inductor can be calculated using various formulas depending on the coil geometry. For a single-layer solenoid, the inductance can be approximated using the following formula:
L = (μ₀ × N² × A) / l
Where:
– L is the inductance in henries (H)
– μ₀ is the permeability of free space (4π × 10⁻⁷ H/m)
– N is the number of turns
– A is the cross-sectional area of the coil in square meters (m²)
– l is the length of the coil in meters (m)
For more complex geometries, such as multi-layer solenoids or toroidal coils, more sophisticated formulas or simulation tools may be required to accurately calculate the inductance.
Wire Selection
The choice of wire for an air-core inductor depends on several factors, including the desired inductance, current carrying capacity, and operating frequency. Some key considerations include:
- Wire gauge: Thicker wire (lower gauge) can carry more current and has lower DC resistance, but it also results in a larger coil size.
- Wire material: Copper is the most common choice due to its low resistivity and cost. However, for high-frequency applications, silver-plated copper or Litz wire may be used to reduce skin effect losses.
- Insulation: The wire insulation must withstand the expected voltage levels and environmental conditions. Common insulation materials include enamel, polyurethane, and Teflon.
Winding Techniques
The way in which the coil is wound can affect the inductor’s performance, particularly at high frequencies. Some common winding techniques include:
- Single-layer: A single-layer winding is the simplest and most common technique, where the wire is wound in a single layer around the coil former.
- Multi-layer: In a multi-layer winding, the wire is wound in multiple layers to increase the inductance without increasing the coil diameter. However, multi-layer windings can have higher inter-turn capacitance, which lowers the SRF.
- Bank winding: Bank winding involves winding the coil in sections, with each section having a specific number of turns. This technique can help reduce the distributed capacitance and improve the SRF.
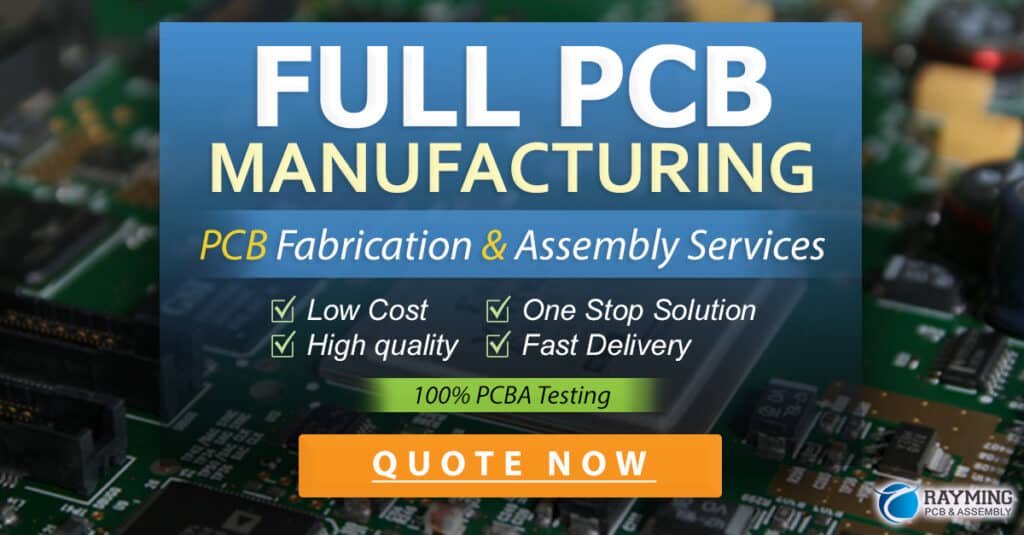
Practical Applications of Air-Core Inductors
Radio Frequency (RF) Circuits
Air-core inductors are widely used in RF circuits, such as:
- Tuned circuits: Air-core inductors are used in parallel with capacitors to create resonant circuits for frequency selection in radio receivers and transmitters.
- Impedance matching networks: Air-core inductors are used in impedance matching networks to maximize power transfer between stages in RF amplifiers.
- RF chokes: Air-core inductors with high impedance at the operating frequency are used as RF chokes to block RF currents while allowing DC currents to pass.
Filters
Air-core inductors are used in various filter circuits, including:
- Low-pass filters: Air-core inductors are used in series with resistors to create low-pass filters that attenuate high-frequency signals while allowing low-frequency signals to pass.
- High-pass filters: Air-core inductors are used in parallel with capacitors to create high-pass filters that attenuate low-frequency signals while allowing high-frequency signals to pass.
- Band-pass filters: Air-core inductors are used in combination with capacitors to create band-pass filters that allow a specific range of frequencies to pass while attenuating frequencies outside that range.
Oscillators
Air-core inductors are used in oscillator circuits to generate sinusoidal signals at a specific frequency. Some common oscillator circuits that use air-core inductors include:
- Hartley oscillator: A Hartley oscillator uses a tapped air-core inductor in parallel with a capacitor to create a resonant circuit, with the tapping point determining the feedback ratio.
- Colpitts Oscillator: A Colpitts oscillator uses an air-core inductor in series with two capacitors to create a resonant circuit, with the capacitor ratio determining the feedback.
Measuring and Testing Air-Core Inductors
Inductance Measurement
Inductance can be measured using various methods, including:
- LCR meter: An LCR meter is an instrument that directly measures the inductance, capacitance, and resistance of a component.
- Impedance analyzer: An impedance analyzer measures the complex impedance of a component over a range of frequencies, from which the inductance can be derived.
- Resonant method: The inductance can be determined by creating a resonant circuit with a known capacitance and measuring the resonant frequency.
Quality Factor (Q) Measurement
The quality factor of an air-core inductor can be measured using the following methods:
- Impedance analyzer: An impedance analyzer can directly measure the Q of an inductor over a range of frequencies.
- Bandwidth method: The Q can be calculated by measuring the bandwidth of a resonant circuit containing the inductor and a known capacitance.
- Voltage divider method: The Q can be determined by measuring the voltage across the inductor and a series resistor in a voltage divider circuit.
Self-Resonant Frequency (SRF) Measurement
The SRF of an air-core inductor can be measured using an impedance analyzer or by observing the frequency at which the inductor’s impedance reaches a maximum in a resonant circuit.
Frequently Asked Questions (FAQ)
-
Q: What is the difference between an air-core inductor and an inductor with a ferromagnetic core?
A: Air-core inductors have no magnetic core material, relying solely on the magnetic field generated by the current flowing through the coil. Inductors with ferromagnetic cores use materials such as iron or ferrite to increase the magnetic field strength and inductance. Air-core inductors have lower losses and are more suitable for high-frequency applications, while inductors with ferromagnetic cores can achieve higher inductance values in a smaller physical size. -
Q: How do I choose the right wire gauge for my air-core inductor?
A: The choice of wire gauge depends on the desired inductance, current carrying capacity, and operating frequency. Thicker wire (lower gauge) can carry more current and has lower DC resistance but results in a larger coil size. For high-frequency applications, consider using Litz wire or silver-plated copper to reduce skin effect losses. -
Q: What is the purpose of bank winding in air-core inductors?
A: Bank winding involves winding the coil in sections, with each section having a specific number of turns. This technique helps reduce the distributed capacitance between turns, which can improve the self-resonant frequency (SRF) of the inductor. Bank winding is particularly useful in high-frequency applications where a high SRF is required. -
Q: How do I calculate the inductance of a multi-layer air-core inductor?
A: Calculating the inductance of a multi-layer air-core inductor is more complex than for a single-layer inductor. You can use specialized formulas or simulation tools, such as finite element analysis (FEA) software, to accurately determine the inductance. Alternatively, you can measure the inductance using an LCR meter or impedance analyzer. -
Q: Can I use an air-core inductor in a switching power supply?
A: Air-core inductors are generally not suitable for use in switching power supplies due to their lower inductance and higher losses compared to inductors with ferromagnetic cores. Switching power supplies typically require inductors with high inductance values and low losses to ensure efficient power conversion and regulation. Ferromagnetic core materials, such as ferrite or iron powder, are preferred in these applications.
Conclusion
Air-core inductors are essential components in many electronic applications, particularly in high-frequency circuits where low losses and linear behavior are required. By understanding the fundamentals of air-core inductor design, including coil geometry, inductance calculation, wire selection, and winding techniques, engineers and hobbyists can create custom inductors tailored to their specific needs.
When designing an air-core inductor, it is essential to consider the trade-offs between inductance, physical size, and performance at the desired operating frequency. Proper measurement and testing techniques, such as inductance, quality factor, and self-resonant frequency measurements, are crucial for verifying the inductor’s performance and ensuring it meets the application requirements.
As technology advances and the demand for high-frequency electronics grows, air-core inductors will continue to play a vital role in enabling innovative designs and pushing the boundaries of electronic performance.
No responses yet