Introduction to Multilayer PCB
Multilayer PCBs, also known as multilayer printed circuit boards, are essential components in modern electronic devices. They consist of multiple layers of conductive copper foil laminated together with insulating material, allowing for complex circuitry and high component density. As technology advances and devices become more sophisticated, multilayer PCBs play a crucial role in enabling these advancements.
What is a Multilayer PCB?
A multilayer PCB is a printed circuit board that consists of three or more conductive copper layers separated by insulating material. The layers are interconnected through plated holes called vias, which allow electrical signals to pass between layers. This layered structure enables designers to create complex circuits with high component density, improved signal integrity, and reduced electromagnetic interference (EMI).
Advantages of Multilayer PCBs
Multilayer PCBs offer several advantages over single or double-layer PCBs:
-
Increased Density: Multilayer PCBs allow for a higher component density, as circuitry can be spread across multiple layers, reducing the overall board size.
-
Improved Signal Integrity: By separating signal layers with ground and power planes, multilayer PCBs minimize crosstalk and electromagnetic interference, ensuring better signal integrity.
-
Enhanced Reliability: The compact structure of multilayer PCBs reduces the distance between components, minimizing signal propagation delay and improving overall reliability.
-
Reduced EMI: Proper layer arrangement and the use of ground planes help reduce electromagnetic interference, making multilayer PCBs suitable for sensitive electronic applications.
Factors to Consider When Choosing a Multilayer PCB
When determining the type of multilayer PCB for your product, several factors must be considered to ensure optimal performance, reliability, and cost-effectiveness.
Number of Layers
The number of layers in a multilayer PCB directly impacts its functionality, size, and cost. A higher layer count allows for more complex circuitry and better signal integrity but also increases manufacturing complexity and cost. Consider the following when deciding on the number of layers:
- Circuit complexity
- Component density
- Signal integrity requirements
- Board size constraints
- Budget limitations
Number of Layers | Typical Applications | Relative Cost |
---|---|---|
4 | Simple digital devices, low-speed applications | Low |
6-8 | Digital and analog mixed circuits, mid-speed applications | Medium |
10-12 | Complex digital devices, high-speed applications | High |
14+ | Highly complex systems, advanced high-speed applications | Very High |
Material Selection
The choice of PCB material directly affects the board’s performance, durability, and cost. The most common materials used in multilayer PCBs are:
- FR-4: A cost-effective, flame-retardant material suitable for general-purpose applications.
- High-Tg FR-4: An enhanced version of FR-4 with better thermal stability and improved signal integrity.
- Polyimide: A high-temperature material with excellent thermal stability and low dielectric loss, ideal for high-frequency applications.
- PTFE (Teflon): A low-loss material with superior high-frequency performance, suitable for RF and microwave applications.
Consider the following factors when selecting PCB material:
- Dielectric constant (Dk)
- Dissipation factor (Df)
- Thermal stability
- Mechanical strength
- Cost
Copper Thickness
Copper thickness, measured in ounces per square foot (oz/ft²), affects the current-carrying capacity and impedance of the PCB traces. Thicker copper layers allow for higher current carrying capacity and improved heat dissipation but increase the overall board thickness and cost. Common copper thicknesses include:
- 0.5 oz/ft²: Suitable for low-power, high-density designs
- 1 oz/ft²: The most common thickness, suitable for general-purpose applications
- 2 oz/ft²: Used for high-current applications or to improve heat dissipation
- 3 oz/ft² and above: Used for very high-current applications or in power electronics
Trace Width and Spacing
Trace width and spacing determine the current-carrying capacity, impedance, and signal integrity of the PCB. Narrower traces allow for higher component density but have lower current-carrying capacity and may be more susceptible to signal integrity issues. Consider the following when determining trace width and spacing:
- Signal frequency and rise time
- Current requirements
- Impedance control
- Manufacturing capabilities
- PCB design rules and standards (e.g., IPC-2152)
Via Types and Sizes
Vias are plated holes that interconnect layers in a multilayer PCB. The choice of via type and size affects signal integrity, board density, and manufacturing cost. Common via types include:
- Through-hole vias: Extend through the entire board thickness, used for component mounting and layer interconnection.
- Blind vias: Connect an outer layer to an inner layer, terminating within the board.
- Buried vias: Connect inner layers without extending to the outer layers.
- Microvias: Small-diameter vias (typically less than 150 µm) used for high-density interconnects.
Consider the following factors when selecting via types and sizes:
- Signal integrity requirements
- Board density and layer count
- Manufacturing capabilities and cost
- Aspect ratio (hole depth to diameter ratio)
PCB Stackup Design
The PCB stackup refers to the arrangement of conductive and insulating layers in a multilayer PCB. A well-designed stackup ensures proper signal integrity, minimizes EMI, and optimizes manufacturing yields. Consider the following guidelines when designing a PCB stackup:
Signal Layer Arrangement
- Alternate signal layers with ground and power planes to minimize crosstalk and EMI.
- Route critical signals on inner layers to minimize external interference.
- Use stripline or embedded microstrip structures for controlled impedance.
Power and Ground Planes
- Use dedicated power and ground planes to provide low-impedance power distribution and reduce EMI.
- Place power and ground planes close to the associated signal layers to minimize loop area and reduce inductance.
- Use multiple power and ground planes for different voltage levels if required.
Symmetry and Balance
- Design the stackup symmetrically to minimize warpage and improve manufacturing yields.
- Balance copper coverage on each layer to minimize stress and ensure flatness.
- Use the same dielectric material between layers to maintain consistent electrical properties.
Example 8-layer PCB Stackup:
| Layer | Type | Material | Copper Thickness |
|——-|————–|———-|——————|
| 1 | Signal | FR-4 | 1 oz/ft² |
| 2 | Ground Plane | FR-4 | 1 oz/ft² |
| 3 | Signal | FR-4 | 1 oz/ft² |
| 4 | Power Plane | FR-4 | 1 oz/ft² |
| 5 | Power Plane | FR-4 | 1 oz/ft² |
| 6 | Signal | FR-4 | 1 oz/ft² |
| 7 | Ground Plane | FR-4 | 1 oz/ft² |
| 8 | Signal | FR-4 | 1 oz/ft² |
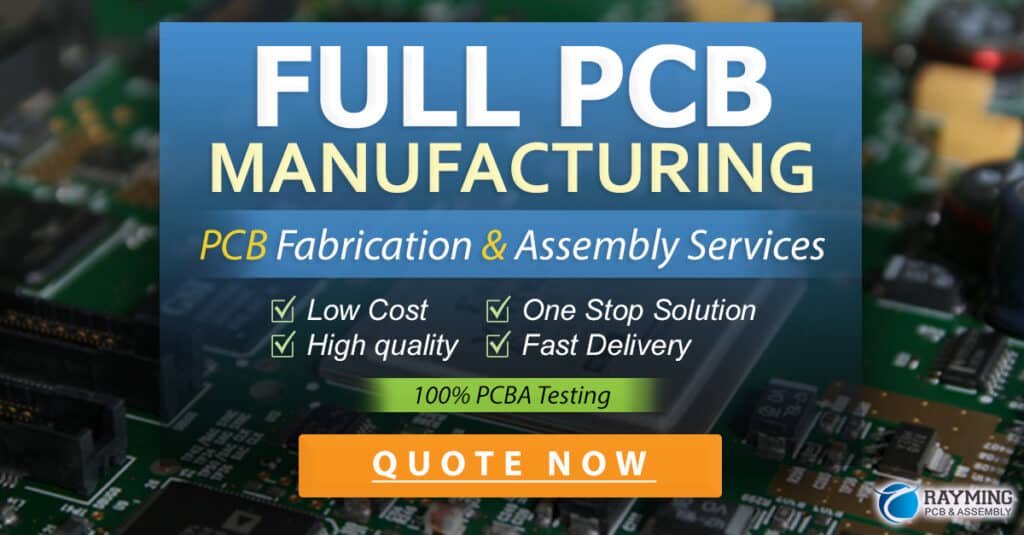
Manufacturing Considerations
When designing a multilayer PCB, it is essential to consider the manufacturing process to ensure the design is feasible, cost-effective, and yields high-quality results.
Design for Manufacturability (DFM)
- Follow the manufacturer’s design guidelines and rules to ensure compatibility with their processes.
- Use standard via sizes and pad dimensions to minimize manufacturing costs.
- Avoid unnecessary complexity, such as tight tolerances or unconventional features.
Panelization
- Group multiple PCBs on a single panel to optimize material usage and reduce manufacturing costs.
- Use proper spacing and routing between boards to ensure clean separation during depaneling.
- Include fiducial marks and tooling holes for accurate registration during assembly.
Testing and Inspection
- Specify appropriate electrical tests, such as continuity, isolation, and high-potential (HiPot) tests, to ensure board functionality and reliability.
- Use automated optical inspection (AOI) and X-ray inspection to detect manufacturing defects, such as shorts, opens, and voids.
- Consider in-circuit testing (ICT) or functional testing to verify the assembled board’s performance.
Cost Optimization Strategies
Multilayer PCBs can be expensive, especially for high-layer-count designs. To optimize costs without compromising performance, consider the following strategies:
Design Optimization
- Minimize the number of layers while meeting performance requirements.
- Use standard materials, sizes, and tolerances whenever possible.
- Optimize component placement and routing to reduce board size and layer count.
Volume Pricing
- Higher order quantities often result in lower per-unit costs due to economies of scale.
- Consider future demand and plan production volumes accordingly.
Vendor Selection
- Compare quotes from multiple PCB manufacturers to find the best value.
- Consider the manufacturer’s capabilities, quality, and reputation in addition to price.
- Establish long-term relationships with reliable vendors to secure better pricing and support.
Frequently Asked Questions (FAQ)
-
Q: How do I determine the number of layers needed for my multilayer PCB?
A: The number of layers required depends on factors such as circuit complexity, component density, signal integrity requirements, and board size constraints. Start by evaluating your design’s needs and consult with experienced PCB designers or manufacturers for guidance. -
Q: What is the most common PCB material for multilayer boards?
A: FR-4 is the most common material for multilayer PCBs due to its cost-effectiveness, good mechanical and electrical properties, and wide availability. However, high-performance applications may require specialized materials like high-Tg FR-4, polyimide, or PTFE. -
Q: How do I ensure proper signal integrity in a multilayer PCB?
A: To ensure proper signal integrity, use a well-designed stackup that alternates signal layers with ground and power planes, minimizing crosstalk and EMI. Route critical signals on inner layers, use controlled impedance structures, and follow best practices for trace routing and termination. -
Q: What is the difference between blind, buried, and through-hole vias?
A: Through-hole vias extend through the entire board thickness and are used for component mounting and layer interconnection. Blind vias connect an outer layer to an inner layer, while buried vias connect inner layers without extending to the outer layers. Blind and buried vias are used for higher density designs and improved signal integrity. -
Q: How can I optimize the cost of my multilayer PCB?
A: To optimize the cost of your multilayer PCB, minimize the number of layers while meeting performance requirements, use standard materials and sizes, optimize component placement and routing, and consider volume pricing. Additionally, compare quotes from multiple manufacturers and establish long-term relationships with reliable vendors.
Conclusion
Multilayer PCBs are essential components in modern electronic devices, offering increased density, improved signal integrity, and enhanced reliability. When determining the type of multilayer PCB for your product, consider factors such as the number of layers, material selection, copper thickness, trace width and spacing, and via types and sizes. A well-designed PCB stackup, proper manufacturing considerations, and cost optimization strategies are crucial for ensuring the success of your multilayer PCB project.
By understanding the key aspects of multilayer PCB design and manufacturing, you can make informed decisions and create high-quality, reliable, and cost-effective products. Engage with experienced PCB designers, manufacturers, and industry experts to leverage their knowledge and ensure the best possible outcome for your multilayer PCB project.
No responses yet