Introduction to FR4 and Its Thermal Properties
FR4, or Flame Retardant 4, is a widely used glass-reinforced epoxy laminate material in the electronics industry. It is the primary substrate material for printed circuit boards (PCBs) due to its excellent mechanical, electrical, and thermal properties. One of the critical aspects of FR4 is its thermal conductivity, which plays a vital role in the performance and reliability of electronic devices.
What is Thermal Conductivity?
Thermal conductivity is a material property that describes the ability of a substance to conduct heat. It is defined as the rate of heat transfer through a material per unit thickness, per unit area, and per unit temperature difference. The SI unit for thermal conductivity is watts per meter-kelvin (W/mK).
Importance of Thermal Conductivity in PCBs
In electronic devices, heat generation is an inevitable byproduct of electrical current flow. As components become more compact and power-dense, effective heat dissipation becomes increasingly crucial to ensure optimal performance and longevity. The thermal conductivity of the PCB substrate material, such as FR4, directly impacts the board’s ability to transfer heat away from components and prevent overheating.
Factors Affecting FR4 Thermal Conductivity
Several factors influence the thermal conductivity of FR4 Laminates:
Glass Fiber Content
FR4 is a composite material consisting of woven glass fabric impregnated with an epoxy resin matrix. The glass fiber content in FR4 laminates typically ranges from 40% to 70% by weight. Higher glass fiber content generally results in better mechanical properties but may slightly reduce thermal conductivity due to the lower thermal conductivity of glass compared to epoxy resin.
Resin Composition
The epoxy resin used in FR4 laminates plays a significant role in determining the material’s thermal properties. Different resin formulations can exhibit varying levels of thermal conductivity. Some specialized FR4 variants, such as high thermal conductivity (HTC) laminates, incorporate thermally conductive fillers or modified resin systems to enhance heat transfer capabilities.
Laminate Thickness
The thickness of the FR4 laminate can also affect its thermal conductivity. Thicker laminates provide more cross-sectional area for heat conduction, allowing for better heat spreading and dissipation. However, thicker boards may also introduce challenges related to manufacturing, cost, and signal integrity.
Copper Cladding
FR4 laminates are often clad with copper foil on one or both sides to create conductive layers for electrical connections. The thickness and coverage of the copper cladding can influence the overall thermal conductivity of the PCB. Copper has a much higher thermal conductivity than FR4, so increasing the copper content can improve heat dissipation.
Measuring FR4 Thermal Conductivity
Several methods are used to measure the thermal conductivity of FR4 laminates:
Guarded Hot Plate Method
The guarded hot plate method is a steady-state technique that measures the thermal conductivity of a material by establishing a temperature gradient across a sample sandwiched between two plates. The method is widely used for materials with low to medium thermal conductivity, such as FR4.
Laser Flash Method
The laser flash method is a transient technique that determines thermal conductivity by measuring the temperature rise on the opposite face of a sample after a short laser pulse. This method is suitable for a wide range of materials, including thin films and composites.
Thermal Conductivity Meters
Thermal conductivity meters are commercial instruments that use various techniques, such as the transient plane source method or the modified transient plane source method, to measure the thermal conductivity of materials. These meters provide quick and reliable results and are commonly used in industry for quality control and material characterization.
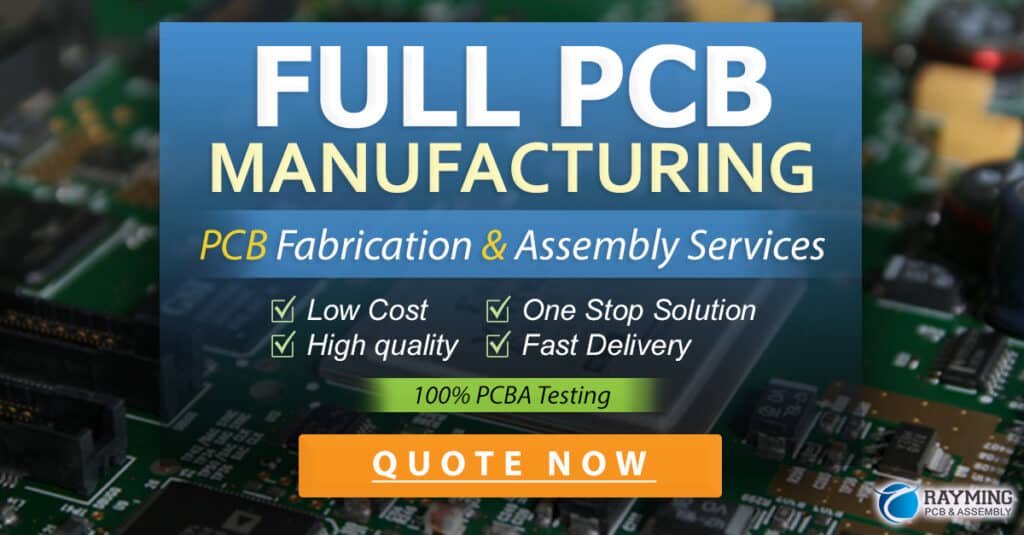
Typical FR4 Thermal Conductivity Values
The thermal conductivity of standard FR4 laminates generally falls within the range of 0.25 to 0.40 W/mK. However, the exact value can vary depending on the specific composition, glass fiber content, and manufacturing process. Some common FR4 grades and their thermal conductivity values are listed in the table below:
FR4 Grade | Thermal Conductivity (W/mK) |
---|---|
Standard FR4 | 0.25 – 0.40 |
High Tg FR4 | 0.30 – 0.45 |
Halogen-free FR4 | 0.25 – 0.35 |
High thermal conductivity FR4 | 0.60 – 1.00 |
It is important to note that these values are indicative and may vary between manufacturers and specific product lines. Always consult the material datasheet provided by the laminate supplier for accurate thermal conductivity information.
Strategies for Improving Thermal Management with FR4
While standard FR4 laminates have limited thermal conductivity, several strategies can be employed to enhance thermal management in PCB designs:
Thermal Vias
Thermal vias are copper-plated holes drilled through the PCB to provide a low-resistance thermal path between layers. By strategically placing thermal vias near heat-generating components, heat can be efficiently transferred to other layers or to an external heatsink.
Heatsinks and Thermal Interface Materials
Attaching heatsinks to critical components and using thermal interface materials (TIMs) can significantly improve heat dissipation. Heatsinks increase the surface area for heat exchange with the surrounding air, while TIMs fill the gaps between components and heatsinks, ensuring efficient thermal transfer.
High Thermal Conductivity Laminates
For applications with demanding thermal requirements, high thermal conductivity (HTC) FR4 laminates can be used. These specialized laminates incorporate thermally conductive fillers or modified resin systems that enhance heat transfer properties. HTC FR4 laminates can have thermal conductivity values ranging from 0.6 to 1.0 W/mK or higher.
PCB Layout Optimization
Optimizing the PCB layout can also contribute to better thermal management. This includes proper component placement, minimizing heat-generating component clustering, providing adequate copper coverage for heat spreading, and designing efficient power and ground planes.
Frequently Asked Questions (FAQ)
1. What is the difference between thermal conductivity and thermal resistance?
Thermal conductivity is a material property that describes the ability of a substance to conduct heat, while thermal resistance is a measure of a material’s opposition to heat flow. Thermal resistance is the reciprocal of thermal conductivity and is expressed in kelvin per watt (K/W).
2. How does the thermal conductivity of FR4 compare to other PCB materials?
FR4 has a relatively low thermal conductivity compared to other PCB materials. For example, aluminum has a thermal conductivity of around 200 W/mK, while copper has a thermal conductivity of about 400 W/mK. Some specialized PCB materials, such as metal core PCBs (MCPCBs) or ceramic substrates, offer significantly higher thermal conductivity than FR4.
3. Can the thermal conductivity of FR4 be increased?
Yes, the thermal conductivity of FR4 can be increased by using high thermal conductivity (HTC) laminates that incorporate thermally conductive fillers or modified resin systems. These specialized FR4 variants can achieve thermal conductivity values ranging from 0.6 to 1.0 W/mK or higher.
4. How does the thermal conductivity of FR4 affect PCB design?
The low thermal conductivity of standard FR4 laminates can limit the PCB’s ability to dissipate heat effectively. This can lead to higher component temperatures, reduced performance, and decreased reliability. PCB designers must consider the thermal conductivity of FR4 and employ appropriate thermal management strategies, such as using thermal vias, heatsinks, and optimized layouts, to ensure adequate heat dissipation.
5. What are the challenges associated with using high thermal conductivity FR4 laminates?
High thermal conductivity FR4 laminates may present some challenges, such as increased material cost, potential impact on signal integrity due to the presence of thermally conductive fillers, and possible changes in manufacturing processes. It is essential to carefully evaluate the specific requirements of the application and consult with the laminate supplier to determine the most suitable HTC FR4 grade.
Conclusion
FR4 thermal conductivity is a critical property that significantly influences the thermal management of PCBs and electronic devices. Understanding the factors affecting FR4 thermal conductivity, such as glass fiber content, resin composition, and laminate thickness, is essential for designers and engineers to make informed decisions when selecting PCB materials.
While standard FR4 laminates have limited thermal conductivity, various strategies can be employed to enhance heat dissipation, including the use of thermal vias, heatsinks, high thermal conductivity laminates, and optimized PCB layouts. By carefully considering the thermal requirements of the application and implementing appropriate thermal management techniques, designers can ensure the performance, reliability, and longevity of electronic devices.
As electronic systems continue to push the boundaries of power density and miniaturization, the importance of effective thermal management cannot be overstated. A comprehensive understanding of FR4 thermal conductivity and its impact on PCB design is crucial for engineers and manufacturers to develop innovative and thermally efficient solutions in the ever-evolving electronics industry.
No responses yet