Introduction to PCB Routing
PCB routing is the process of creating electrical connections between components on a printed circuit board (PCB). It involves designing the copper traces that carry signals and power between the various components on the board. Proper PCB routing is crucial for ensuring the reliability, performance, and integrity of the electronic device.
Key Considerations in PCB Routing
When routing a PCB, several key factors must be taken into account:
1. Signal integrity
2. Power integrity
3. Electromagnetic compatibility (EMC)
4. Manufacturing constraints
5. Cost-effectiveness
PCB Bus Routing
PCB bus routing refers to the process of routing multiple related signals together as a group, or bus. Buses are commonly used in digital systems to transfer data, address, and control signals between components such as microprocessors, memory devices, and peripherals.
Types of PCB Buses
There are several types of buses used in PCB design:
1. Parallel bus
2. Serial bus
3. Address bus
4. Data bus
5. Control bus
Bus Type | Description |
---|---|
Parallel Bus | Multiple signals transmitted simultaneously |
Serial Bus | Data transmitted sequentially, one bit at a time |
Address Bus | Carries memory addresses for read and write operations |
Data Bus | Transfers data between components |
Control Bus | Carries control signals for coordinating system operations |
PCB Bus Routing Techniques
To ensure proper signal integrity and minimize crosstalk, several techniques are used in PCB bus routing:
1. Impedance matching
2. Termination
3. Differential pair routing
4. Length matching
5. Shielding
Impedance Matching
Impedance matching involves designing the PCB traces to have a specific characteristic impedance, typically 50 ohms or 100 ohms. This helps to minimize reflections and ensure proper signal transmission.
Termination
Termination techniques, such as series termination and parallel termination, are used to reduce reflections and ringing on the bus lines. Proper termination helps to maintain signal integrity and prevent false triggering of receivers.
Differential Pair Routing
Differential signaling involves using two complementary signals to transmit data, which helps to cancel out common-mode noise. When routing differential pairs, it is essential to maintain equal length and spacing between the traces to ensure proper signal integrity.
Length Matching
Length matching is the process of ensuring that all traces in a bus have equal electrical lengths. This helps to minimize skew and ensure that signals arrive at their destinations simultaneously.
Shielding
Shielding techniques, such as ground planes and guard traces, are used to minimize crosstalk and electromagnetic interference (EMI) between bus lines and other signals on the PCB.
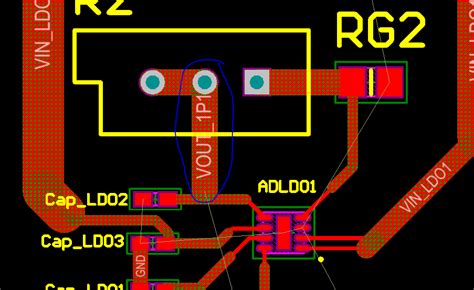
PCB Layout Basics
In addition to proper bus routing, several other aspects of PCB layout are critical for ensuring the performance and reliability of the electronic device.
Component Placement
Component placement is the process of determining the optimal location for each component on the PCB. Factors to consider include:
1. Functionality
2. Signal integrity
3. Power distribution
4. Thermal management
5. Manufacturing constraints
Power Distribution Network (PDN) Design
The power distribution network (PDN) is responsible for delivering clean, stable power to all components on the PCB. Key considerations in PDN design include:
1. Power plane design
2. Decoupling capacitor placement
3. Voltage regulation
4. Current carrying capacity
Grounding Strategies
Proper grounding is essential for minimizing noise, ensuring safety, and preventing ground loops. Common grounding strategies include:
1. Star grounding
2. Multi-point grounding
3. Hybrid grounding
Thermal Management
Thermal management involves designing the PCB to efficiently dissipate heat generated by components. Techniques for thermal management include:
1. Proper component placement
2. Thermal vias
3. Heat sinks
4. Airflow considerations
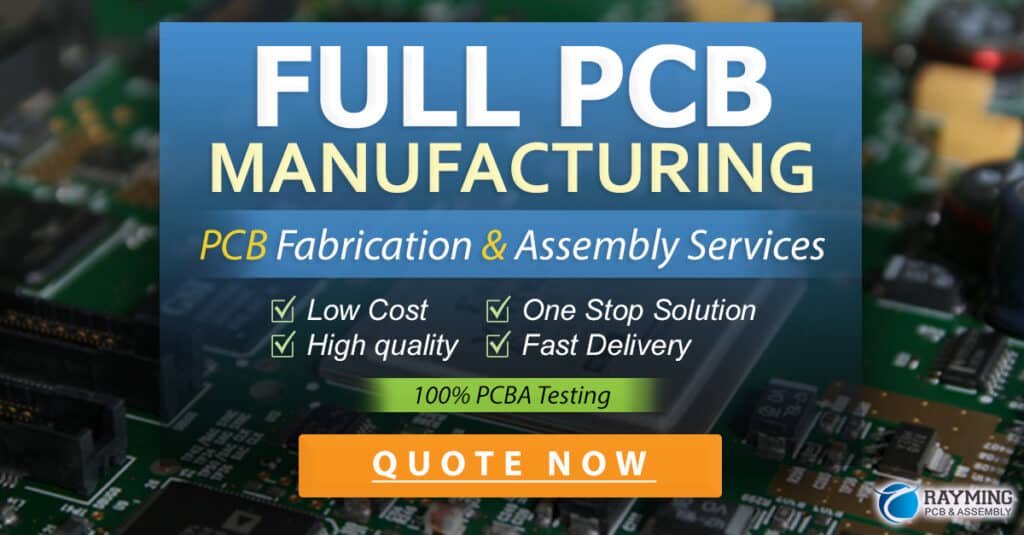
Best Practices for PCB Bus Routing and Layout
To ensure optimal performance and reliability, follow these best practices when routing buses and designing PCB layouts:
1. Use appropriate routing techniques for each bus type
2. Minimize crosstalk and EMI through proper spacing and shielding
3. Match trace lengths and impedances within each bus
4. Use appropriate termination techniques to minimize reflections
5. Carefully plan component placement for functionality, signal integrity, and thermal management
6. Design a robust power distribution network with adequate decoupling and voltage regulation
7. Implement appropriate grounding strategies to minimize noise and ensure safety
8. Consider manufacturing constraints and cost-effectiveness throughout the design process
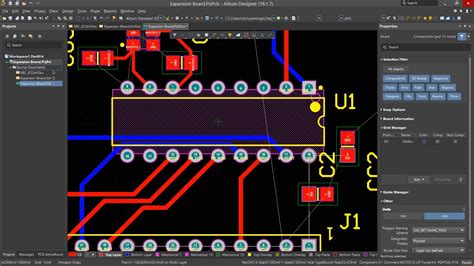
Conclusion
PCB bus routing and layout design are critical aspects of creating reliable, high-performance electronic devices. By understanding the various types of buses, routing techniques, and layout considerations, designers can create PCBs that meet the desired functionality while ensuring signal integrity, power integrity, and electromagnetic compatibility.
Frequently Asked Questions (FAQ)
1. What is the difference between a parallel bus and a serial bus?
A parallel bus transmits multiple signals simultaneously, while a serial bus transmits data sequentially, one bit at a time. Parallel buses offer higher data transfer rates but require more PCB traces and are more susceptible to crosstalk. Serial buses, on the other hand, require fewer traces and are less prone to crosstalk but have lower data transfer rates.
2. Why is impedance matching important in PCB bus routing?
Impedance matching is essential for minimizing reflections and ensuring proper signal transmission. When the impedance of the PCB traces matches the impedance of the source and destination devices, signal reflections are minimized, leading to better signal integrity and reduced noise.
3. What is the purpose of length matching in PCB bus routing?
Length matching ensures that all traces in a bus have equal electrical lengths. This helps to minimize skew, which is the difference in arrival times of signals at their destinations. By ensuring that all signals arrive simultaneously, length matching improves signal integrity and reduces the likelihood of data errors.
4. How can shielding techniques help in PCB bus routing?
Shielding techniques, such as ground planes and guard traces, help to minimize crosstalk and electromagnetic interference (EMI) between bus lines and other signals on the PCB. Ground planes provide a low-impedance return path for signals and help to reduce EMI, while guard traces isolate sensitive signals from neighboring traces, reducing crosstalk.
5. What are some common thermal management techniques used in PCB layout design?
Common thermal management techniques in PCB layout design include:
1. Proper component placement to distribute heat evenly and avoid hot spots
2. Using thermal vias to transfer heat from components to other layers or to heat sinks
3. Incorporating heat sinks to dissipate heat from high-power components
4. Considering airflow and ventilation when designing the enclosure and component placement
By implementing these thermal management techniques, designers can ensure that components operate within their specified temperature ranges, improving reliability and longevity.
No responses yet