Introduction
In recent years, additive manufacturing (AM), also known as 3D printing, has revolutionized the manufacturing industry. Many companies have embraced this technology due to its numerous advantages, such as design flexibility, rapid prototyping, and cost-effectiveness. However, outsourcing AM services can have its drawbacks, including longer lead times, limited control over the process, and potential intellectual property risks. As a result, more and more companies are considering bringing their additive manufacturing capabilities in-house. In this article, we will explore seven key benefits of implementing an in-house AM strategy.
1. Faster Turnaround Times
Streamlining the Manufacturing Process
One of the most significant advantages of in-house AM is the ability to drastically reduce turnaround times. By having direct access to 3D printers, companies can streamline their manufacturing process and eliminate the need for outsourcing. This allows for quicker iterations and faster product development cycles.
Case Study: GE Aviation
GE Aviation, a leading manufacturer of aircraft engines, has successfully implemented in-house AM to accelerate its production process. By 3D printing fuel nozzles for their LEAP engine, GE Aviation has reduced the lead time from several months to just a few weeks. This has enabled them to bring products to market faster and stay ahead of the competition.
Comparison of Lead Times: In-House AM vs. Outsourcing
Manufacturing Method | Lead Time |
---|---|
In-House AM | 1-2 weeks |
Outsourced AM | 4-8 weeks |
Traditional Manufacturing | 8-16 weeks |
As the table above illustrates, in-house AM can significantly reduce lead times compared to outsourcing or traditional manufacturing methods. This allows companies to respond more quickly to market demands and customer needs.
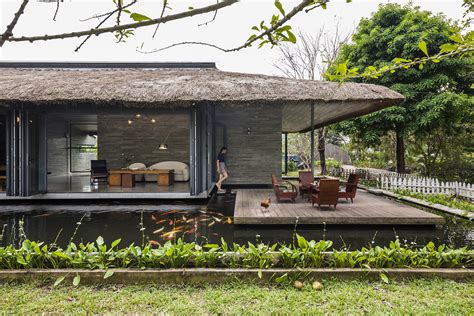
2. Enhanced Design Flexibility
Unlocking New Possibilities with AM
Another key benefit of in-house AM is the enhanced design flexibility it offers. With 3D printing, designers and engineers can create complex geometries and intricate structures that would be impossible or cost-prohibitive to produce using traditional manufacturing methods. This opens up new possibilities for product innovation and optimization.
Example: Topology Optimization
Topology optimization is a design technique that uses algorithms to optimize the distribution of material within a given design space. By combining topology optimization with in-house AM, companies can create lightweight, high-performance components that are tailored to specific applications. This can lead to improved product performance, reduced material usage, and lower production costs.
Comparison of Design Capabilities: AM vs. Traditional Manufacturing
Design Feature | Additive Manufacturing | Traditional Manufacturing |
---|---|---|
Complex Geometries | Yes | Limited |
Internal Structures | Yes | No |
Customization | High | Low |
Tooling Required | No | Yes |
As the table above shows, AM offers significant advantages over traditional manufacturing in terms of design flexibility. In-house AM allows companies to fully leverage these capabilities and push the boundaries of product design.
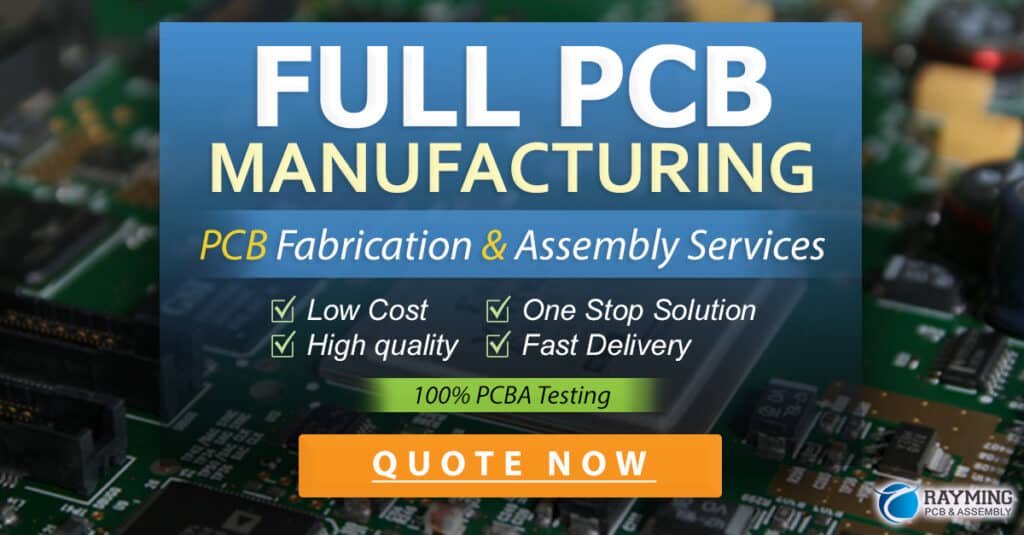
3. Cost Savings
Reducing Production Costs with In-House AM
Bringing additive manufacturing in-house can also lead to significant cost savings. By eliminating the need for outsourcing, companies can reduce their reliance on external suppliers and avoid markup costs. Additionally, AM enables the production of parts on-demand, which can help minimize inventory costs and reduce waste.
Case Study: Volkswagen
Volkswagen, a leading automotive manufacturer, has successfully implemented in-house AM to reduce production costs. By 3D printing tooling and fixtures for their assembly lines, Volkswagen has been able to reduce tooling costs by up to 90%. This has allowed them to maintain a lean inventory and adapt quickly to changing production requirements.
Cost Comparison: In-House AM vs. Outsourcing
Cost Factor | In-House AM | Outsourced AM |
---|---|---|
Equipment Investment | High | Low |
Material Costs | Low | High |
Labor Costs | Medium | High |
Shipping Costs | None | High |
Markup Costs | None | High |
While in-house AM requires an initial investment in equipment, it can lead to long-term cost savings through reduced material, labor, shipping, and markup costs. Companies should carefully consider their production volumes and requirements when deciding whether to bring AM in-house.
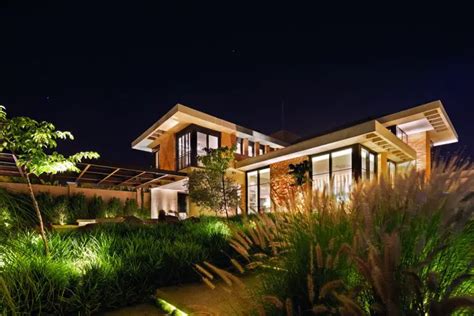
4. Improved Quality Control
Ensuring Consistency and Reliability with In-House AM
In-house AM also enables companies to have greater control over the quality of their 3D printed parts. By managing the entire production process, from design to post-processing, companies can ensure consistency and reliability in their products. This is particularly important for industries such as aerospace and medical devices, where part quality and performance are critical.
Example: In-Process Monitoring
In-process monitoring is a quality control technique that uses sensors and cameras to monitor the 3D printing process in real-time. By detecting defects and anomalies during the printing process, in-process monitoring can help ensure that parts meet the required quality standards. This technique is more easily implemented with in-house AM, as companies have direct access to the printing equipment and can integrate monitoring systems as needed.
Quality Control Measures for In-House AM
Quality Control Measure | Description |
---|---|
Material Selection | Choosing high-quality, consistent materials |
Process Parameter Optimization | Fine-tuning printing parameters for optimal results |
In-Process Monitoring | Real-time monitoring of the printing process |
Post-Process Inspection | Verifying part quality through visual and dimensional inspection |
Certification and Testing | Ensuring parts meet industry standards and regulations |
By implementing a comprehensive quality control strategy, companies can ensure that their in-house AM parts meet the highest standards of quality and performance.
5. Intellectual Property Protection
Safeguarding Proprietary Designs with In-House AM
Intellectual property (IP) protection is a critical concern for many companies, particularly those in competitive industries. By bringing additive manufacturing in-house, companies can better safeguard their proprietary designs and prevent them from falling into the hands of competitors. This is especially important for companies that rely on innovation and unique product designs to maintain their competitive edge.
Case Study: Gillette
Gillette, a leading manufacturer of razor blades, has used in-house AM to protect its IP and maintain its competitive advantage. By 3D printing prototype blades in-house, Gillette can keep its designs confidential and prevent them from being copied by competitors. This has allowed the company to stay ahead of the curve and continue innovating in the highly competitive razor market.
IP Protection Strategies for In-House AM
Strategy | Description |
---|---|
Secure Data Storage | Storing 3D design files on secure, encrypted servers |
Access Control | Limiting access to AM equipment and design files to authorized personnel |
Non-Disclosure Agreements | Requiring employees and contractors to sign NDAs |
Patent Protection | Filing patents for novel designs and inventions |
Trade Secret Protection | Maintaining confidentiality of proprietary processes and techniques |
By implementing a multi-faceted IP protection strategy, companies can ensure that their valuable designs and innovations remain secure when bringing AM in-house.
6. Rapid Prototyping and Iteration
Accelerating Product Development with In-House AM
Rapid prototyping and iteration are essential for companies looking to bring new products to market quickly and efficiently. In-house AM enables companies to create physical prototypes in a matter of hours or days, rather than weeks or months. This allows designers and engineers to test and refine their designs more quickly, leading to faster product development cycles.
Example: Rapid Tooling
Rapid tooling is a process where AM is used to create molds, dies, and other tooling for traditional manufacturing processes. By 3D printing tooling in-house, companies can significantly reduce the lead time and cost associated with producing new tools. This enables faster iteration and optimization of production processes, ultimately leading to better products and shorter time-to-market.
Benefits of Rapid Prototyping with In-House AM
Benefit | Description |
---|---|
Faster Iteration | Quickly create and test multiple design variations |
Early Error Detection | Identify and correct design flaws early in the development process |
Improved Communication | Facilitate better communication between design, engineering, and manufacturing teams |
Reduced Tooling Costs | Create affordable, custom tooling for low-volume production runs |
Faster Time-to-Market | Bring new products to market more quickly and efficiently |
By leveraging the rapid prototyping capabilities of in-house AM, companies can accelerate their product development processes and gain a competitive edge in their respective markets.
7. Increased Agility and Responsiveness
Adapting to Changing Market Demands with In-House AM
In today’s fast-paced business environment, companies need to be agile and responsive to changing market demands. In-house AM enables companies to quickly adapt their production processes and product offerings to meet evolving customer needs. By having direct control over their AM capabilities, companies can make real-time adjustments to their manufacturing strategies and capitalize on new opportunities as they arise.
Case Study: Ford Motor Company
Ford Motor Company has successfully used in-house AM to increase its agility and responsiveness. During the COVID-19 pandemic, Ford quickly pivoted its AM capabilities to produce personal protective equipment (PPE) for healthcare workers. By 3D printing face shields and ventilator components in-house, Ford was able to rapidly respond to the urgent need for medical supplies and make a positive impact on the community.
Strategies for Increasing Agility with In-House AM
Strategy | Description |
---|---|
On-Demand Production | Produce parts and products as needed, reducing inventory and waste |
Flexible Manufacturing | Quickly switch between different products and designs |
Distributed Manufacturing | Produce parts closer to the point of use, reducing shipping costs and lead times |
Mass Customization | Offer personalized products and services without sacrificing efficiency |
Rapid Response | Quickly adapt to changing market conditions and customer needs |
By embracing the agility and responsiveness afforded by in-house AM, companies can stay ahead of the curve and maintain a competitive advantage in their industries.
Frequently Asked Questions (FAQ)
- What types of companies can benefit from bringing additive manufacturing in-house?
-
Companies across a wide range of industries can benefit from in-house AM, including aerospace, automotive, medical devices, consumer products, and more. In general, companies that rely on complex designs, rapid prototyping, or low-volume production are well-suited for in-house AM.
-
What are the upfront costs associated with implementing in-house AM?
-
The upfront costs of implementing in-house AM can vary depending on the scale and scope of the operation. Key costs include equipment acquisition, facility setup, material costs, and employee training. However, these costs can be offset by long-term savings in production costs and increased efficiency.
-
How does in-house AM compare to traditional manufacturing methods in terms of cost and lead time?
-
In-house AM can offer significant cost and lead time advantages over traditional manufacturing methods, particularly for low-volume production runs and complex designs. By reducing tooling costs and enabling on-demand production, in-house AM can help companies save money and bring products to market faster.
-
What are the key considerations for ensuring the quality of in-house AM parts?
-
To ensure the quality of in-house AM parts, companies should implement a comprehensive quality control strategy that includes material selection, process parameter optimization, in-process monitoring, post-process inspection, and certification and testing. By following best practices and industry standards, companies can produce high-quality AM parts that meet or exceed customer requirements.
-
How can companies protect their intellectual property when bringing AM in-house?
- Companies can protect their intellectual property when bringing AM in-house by implementing a multi-faceted IP protection strategy. This may include secure data storage, access control, non-disclosure agreements, patent protection, and trade secret protection. By taking proactive steps to safeguard their proprietary designs and processes, companies can maintain their competitive edge in the market.
Conclusion
Bringing additive manufacturing in-house offers numerous benefits for companies looking to streamline their production processes, reduce costs, and stay ahead of the competition. From faster turnaround times and enhanced design flexibility to improved quality control and increased agility, in-house AM can help companies unlock new opportunities and drive innovation in their industries.
By carefully considering the upfront costs and long-term benefits of in-house AM, companies can make informed decisions about whether to invest in this transformative technology. With the right strategy and implementation plan, companies can successfully integrate AM into their operations and reap the rewards of faster, more efficient, and more responsive manufacturing.
As the additive manufacturing landscape continues to evolve, companies that embrace in-house AM will be well-positioned to adapt to changing market demands and maintain their competitive edge. By staying at the forefront of this exciting technology, companies can drive innovation, reduce costs, and deliver greater value to their customers in the years to come.
No responses yet