Fact 1: Proper Planning is Crucial for Successful PCB Design
One of the most critical aspects of PCB design is proper planning. Before beginning any project, it’s essential to gather all the necessary information and requirements. This includes:
- Schematic diagrams
- Bill of Materials (BOM)
- Component datasheets
- Design constraints (size, shape, and layer count)
- Manufacturing specifications
By taking the time to plan and organize this information upfront, you can avoid costly mistakes and delays down the line. Your boss should understand that investing in proper planning can save time, money, and resources in the long run.
The Benefits of Proper Planning
Benefit | Description |
---|---|
Cost Savings | Proper planning helps identify potential issues early, reducing the need for expensive redesigns or rework. |
Time Savings | By having all the necessary information upfront, designers can work more efficiently and avoid delays. |
Improved Quality | Thorough planning ensures that all requirements are met, resulting in higher-quality PCBs. |
Fact 2: Component Selection Impacts PCB Performance and Cost
The components you choose for your PCB design can significantly impact its performance and cost. When selecting components, consider the following factors:
- Functionality: Ensure that the chosen components meet the required specifications and perform as expected.
- Availability: Select components that are readily available to avoid supply chain issues and delays.
- Cost: Balance the cost of components with the overall budget for the project.
- Footprint: Choose components with footprints that are compatible with your PCB layout and manufacturing process.
Your boss should understand that investing in high-quality, reliable components can lead to better PCB performance and lower overall costs by reducing the need for rework or replacements.
Common Component Selection Mistakes
Mistake | Consequence |
---|---|
Choosing outdated components | Difficulty finding replacements, leading to obsolescence issues |
Overspecifying components | Increased cost without significant performance improvements |
Neglecting component availability | Project delays due to supply chain issues |
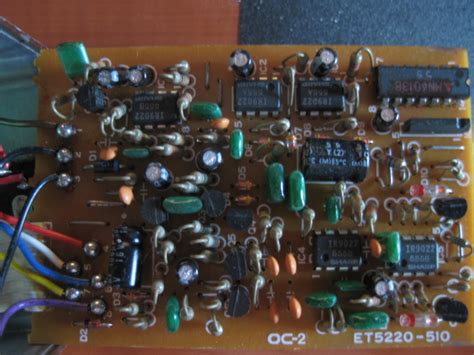
Fact 3: PCB Layer Stackup Affects Signal Integrity and Manufacturability
The PCB layer stackup refers to the arrangement of copper layers and insulating materials within the board. An optimized layer stackup is crucial for maintaining signal integrity and ensuring manufacturability. When designing the layer stackup, consider:
- Signal integrity: Proper layer arrangement and spacing can minimize crosstalk, electromagnetic interference (EMI), and signal reflections.
- Power distribution: Dedicate layers for power and ground planes to provide stable power distribution and reduce noise.
- Manufacturing constraints: Consult with your manufacturer to ensure that your layer stackup is compatible with their processes and capabilities.
Your boss should understand that investing time in optimizing the PCB layer stackup can lead to better signal integrity, reduced EMI, and improved manufacturability.
Example PCB Layer Stackup
Layer | Material | Thickness (mm) |
---|---|---|
Top Overlay | Solder Mask | 0.025 |
Top Copper | Copper | 0.035 |
Dielectric 1 | FR-4 | 0.2 |
Inner Copper 1 | Copper | 0.035 |
Dielectric 2 | FR-4 | 0.7 |
Inner Copper 2 | Copper | 0.035 |
Dielectric 3 | FR-4 | 0.2 |
Bottom Copper | Copper | 0.035 |
Bottom Overlay | Solder Mask | 0.025 |
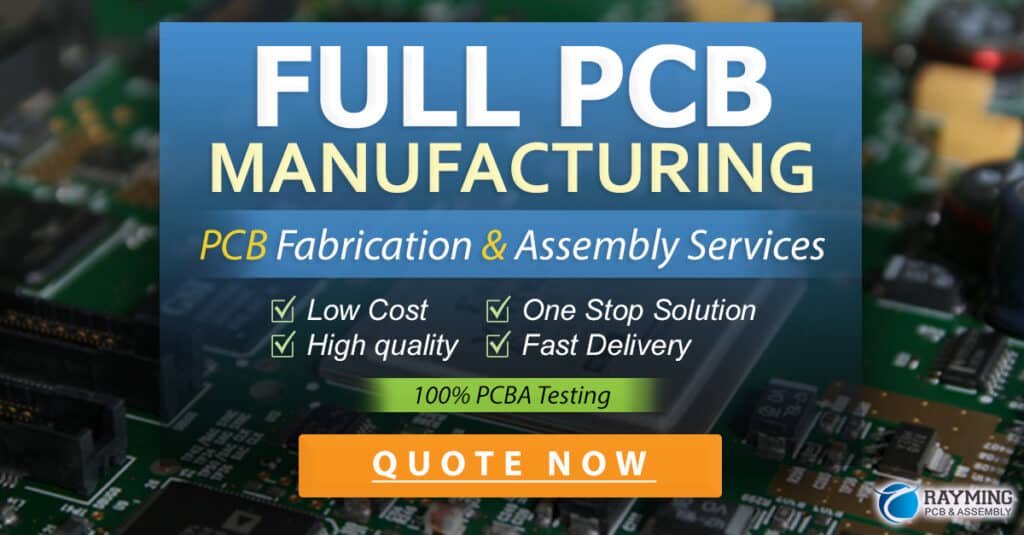
Fact 4: Design for Manufacturing (DFM) Reduces Costs and Improves Yield
Design for Manufacturing (DFM) is the practice of designing PCBs with the manufacturing process in mind. By considering manufacturing constraints and guidelines early in the design process, you can reduce costs, improve yield, and minimize the risk of production issues. Some key DFM considerations include:
- Minimum trace width and spacing
- Hole sizes and pad dimensions
- Solder mask and silkscreen clearances
- Component placement and orientation
- Testability and accessibility
Your boss should understand that incorporating DFM principles into your PCB design process can lead to lower manufacturing costs, higher yields, and faster time-to-market.
DFM Guidelines for PCB Design
Guideline | Recommendation |
---|---|
Minimum trace width | 0.15 mm (6 mil) or greater |
Minimum trace spacing | 0.15 mm (6 mil) or greater |
Minimum hole size | 0.3 mm (12 mil) or greater |
Solder mask clearance | 0.05 mm (2 mil) or greater |
Silkscreen clearance | 0.15 mm (6 mil) or greater |
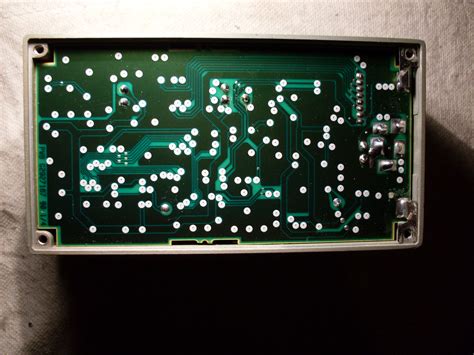
Fact 5: Collaboration and Communication are Essential for Successful PCB Projects
PCB design is a collaborative effort that involves multiple stakeholders, including designers, engineers, manufacturers, and suppliers. Effective communication and collaboration among these parties are essential for ensuring the success of your PCB projects. To foster collaboration and communication:
- Establish clear lines of communication with all stakeholders
- Use version control and data management tools to ensure everyone is working with the most up-to-date information
- Regularly review progress and address any issues or concerns promptly
- Seek feedback and input from stakeholders throughout the design process
Your boss should understand that investing in tools and processes that promote collaboration and communication can lead to better project outcomes, reduced errors, and improved team efficiency.
Tools for Collaboration and Communication
Tool | Purpose |
---|---|
Version Control Systems (e.g., Git) | Manage and track changes to design files |
Project Management Software (e.g., Jira) | Organize tasks, assign responsibilities, and monitor progress |
Communication Platforms (e.g., Slack) | Facilitate real-time communication and information sharing among team members |
Design Review Tools (e.g., Altium 365) | Enable stakeholders to review and provide feedback on designs |
FAQ
-
What is the most important factor in PCB design?
The most important factor in PCB design is proper planning. By gathering all necessary information and requirements upfront, designers can avoid costly mistakes and delays, ultimately leading to higher-quality PCBs. -
How does component selection impact PCB performance and cost?
Component selection can significantly impact PCB performance and cost. Choosing high-quality, reliable components that meet the required specifications and are readily available can lead to better performance and lower overall costs by reducing the need for rework or replacements. -
What is the purpose of optimizing the PCB layer stackup?
Optimizing the PCB layer stackup is crucial for maintaining signal integrity and ensuring manufacturability. Proper layer arrangement and spacing can minimize crosstalk, electromagnetic interference (EMI), and signal reflections while providing stable power distribution and reducing noise. -
How can Design for Manufacturing (DFM) principles benefit PCB projects?
Incorporating DFM principles into the PCB design process can lead to lower manufacturing costs, higher yields, and faster time-to-market. By considering manufacturing constraints and guidelines early in the design process, designers can reduce the risk of production issues and improve overall efficiency. -
Why are collaboration and communication important in PCB design projects?
PCB design is a collaborative effort involving multiple stakeholders. Effective communication and collaboration among designers, engineers, manufacturers, and suppliers are essential for ensuring the success of PCB projects. Investing in tools and processes that promote collaboration and communication can lead to better project outcomes, reduced errors, and improved team efficiency.
In conclusion, by understanding these five essential PCB design facts, your boss can better appreciate the complexities and challenges involved in creating high-quality, reliable printed circuit boards. By supporting proper planning, component selection, layer stackup optimization, DFM principles, and collaboration, your boss can help ensure the success of your PCB projects and contribute to the overall growth and profitability of your organization.
No responses yet