Introduction to EMI and PCB Design
Electromagnetic interference (EMI) is a common issue faced by electronic devices, particularly those with printed circuit boards (PCBs). EMI can cause unwanted disturbances in the functioning of electronic equipment, leading to reduced performance, malfunctions, and even complete failure. It is crucial to address EMI issues early in the PCB design stage to ensure the proper functioning and reliability of electronic devices.
What is EMI?
EMI is the disruption of the normal operation of an electronic device due to electromagnetic radiation emitted by another device or source. This interference can be caused by a variety of factors, including:
- Radio frequency (RF) emissions from nearby devices
- Power supply noise
- Electrostatic discharge (ESD)
- Crosstalk between adjacent traces on a PCB
The Importance of Addressing EMI Early in PCB Design
Addressing EMI issues early in the PCB design stage is essential for several reasons:
-
Cost Savings: Identifying and resolving EMI problems early in the design process can save significant costs associated with redesigns, rework, and product recalls.
-
Time Savings: By addressing EMI issues early, designers can avoid delays in product development and time-to-market.
-
Improved Performance: Properly designed PCBs with EMI considerations in mind will have better overall performance and reliability.
-
Regulatory Compliance: Many industries have strict EMI regulations that products must meet before they can be sold. Addressing EMI early ensures compliance with these regulations.
EMI Sources and Coupling Mechanisms
Common EMI Sources
There are several common sources of EMI in electronic devices:
-
Switching Power Supplies: The rapid switching of currents in power supplies can generate high-frequency noise that can couple onto nearby traces and components.
-
High-Speed Digital Circuits: Digital circuits with fast rise and fall times can generate significant amounts of EMI.
-
Electrostatic Discharge (ESD): ESD events can generate high-frequency transients that can couple onto nearby traces and components.
-
External Sources: EMI can also come from external sources, such as nearby electronic devices, power lines, and lightning strikes.
EMI Coupling Mechanisms
There are three primary coupling mechanisms through which EMI can propagate:
-
Conducted EMI: This occurs when EMI is transmitted through the power supply lines or other conductors.
-
Radiated EMI: This occurs when EMI is transmitted through the air as electromagnetic waves.
-
Capacitive and Inductive Coupling: This occurs when EMI is transmitted through the electric and magnetic fields between nearby traces and components.
EMI Mitigation Techniques in PCB Design
Grounding and Shielding
Proper grounding and shielding are essential for minimizing EMI in PCB designs. Some key techniques include:
-
Separating Analog and Digital Grounds: Use separate ground planes for analog and digital circuits to minimize noise coupling.
-
Using Ground Planes: Use solid ground planes instead of gridded or hatched planes to provide a low-impedance return path for high-frequency currents.
-
Implementing Shield Traces: Use shield traces around sensitive signals to minimize crosstalk and EMI pickup.
-
Incorporating Shielding Enclosures: Use shielding enclosures around sensitive components or the entire PCB to minimize radiated EMI.
PCB Layout Techniques
Proper PCB layout is crucial for minimizing EMI. Some key techniques include:
-
Minimizing Loop Areas: Minimize the loop areas of high-frequency currents to reduce the amount of radiated EMI.
-
Avoiding 90-Degree Traces: Avoid 90-degree trace turns, as they can cause impedance discontinuities and reflections that can lead to EMI.
-
Providing Adequate Spacing: Provide adequate spacing between traces and components to minimize crosstalk and EMI coupling.
-
Using Differential Signaling: Use differential signaling for high-speed signals to minimize the amount of radiated EMI.
Filtering and Suppression
Filtering and suppression techniques can be used to minimize the amount of EMI that is generated or coupled onto the PCB. Some key techniques include:
-
Using Decoupling Capacitors: Use decoupling capacitors near high-frequency components to minimize power supply noise and EMI.
-
Implementing EMI filters: Use EMI filters on power supply lines and other conductors to attenuate high-frequency noise.
-
Incorporating Ferrite Beads: Use ferrite beads on cables and other conductors to suppress high-frequency noise.
-
Utilizing Transient Voltage Suppressors (TVS): Use TVS diodes to protect sensitive components from ESD and other high-frequency transients.
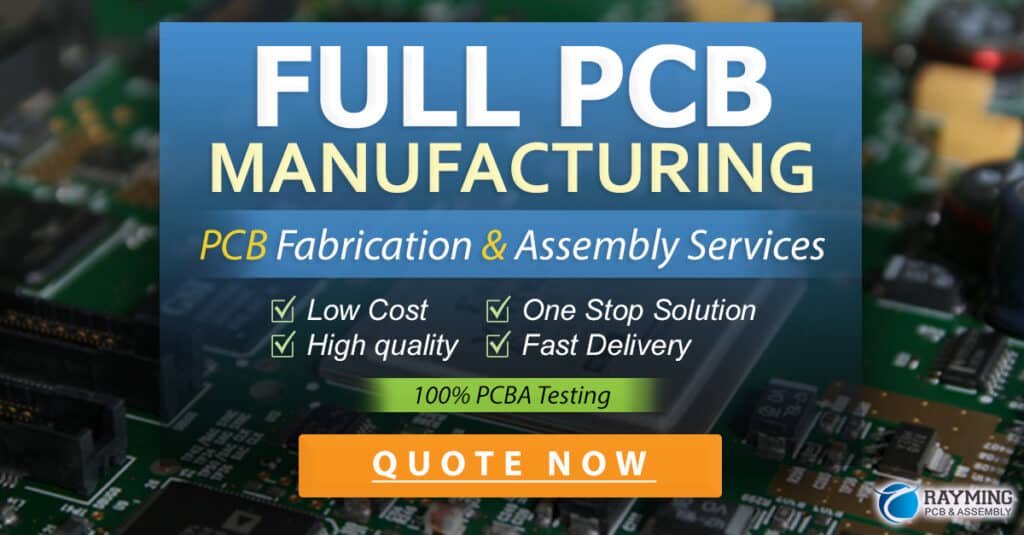
EMI Simulation and Testing
EMI Simulation Tools
EMI simulation tools can be used to predict and analyze the EMI performance of a PCB design before it is fabricated. Some popular EMI simulation tools include:
Tool Name | Vendor | Description |
---|---|---|
ANSYS HFSS | ANSYS | A full-wave 3D electromagnetic field simulator for high-frequency and high-speed electronic components. |
CST Studio Suite | Dassault Systèmes | A suite of electromagnetic simulation tools for designing, analyzing, and optimizing electromagnetic components and systems. |
Keysight EMPro | Keysight Technologies | A 3D electromagnetic simulation software for analyzing the EMI/EMC performance of electronic devices and systems. |
Siemens Simcenter | Siemens | A comprehensive suite of electromagnetic simulation tools for designing and analyzing electronic systems. |
EMI Testing Methods
Once a PCB has been fabricated, it is important to perform EMI testing to ensure that it meets the necessary EMI regulations and performance requirements. Some common EMI testing methods include:
-
Radiated Emissions Testing: This involves measuring the electromagnetic fields emitted by the device under test (DUT) to ensure that they do not exceed the specified limits.
-
Conducted Emissions Testing: This involves measuring the EMI that is conducted through the power supply lines and other conductors to ensure that it does not exceed the specified limits.
-
Immunity Testing: This involves subjecting the DUT to various electromagnetic disturbances to ensure that it can operate properly in the presence of EMI.
-
ESD Testing: This involves subjecting the DUT to ESD events to ensure that it can withstand them without damage or malfunction.
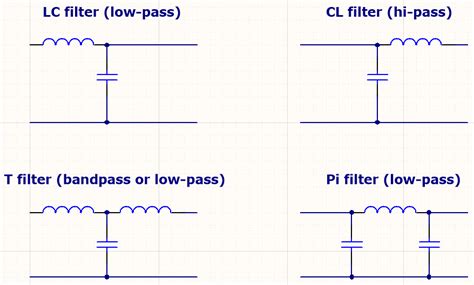
Case Studies and Examples
Example 1: Automotive Infotainment System
An automotive manufacturer was developing a new infotainment system for their vehicles. The system included a high-resolution display, audio amplifier, and various connectivity options. During the development process, the manufacturer encountered EMI issues that were causing the display to flicker and the audio to become distorted.
To address these issues, the manufacturer implemented several EMI mitigation techniques in the PCB design, including:
- Separating the analog and digital grounds
- Using shield traces around sensitive signals
- Implementing EMI filters on the power supply lines
- Utilizing ferrite beads on the audio cables
After implementing these techniques and performing thorough EMI testing, the manufacturer was able to resolve the EMI issues and bring the infotainment system to market.
Example 2: Medical Device
A medical device manufacturer was developing a new patient monitoring system that included various sensors and wireless connectivity options. During the development process, the manufacturer encountered EMI issues that were causing the sensors to provide inaccurate readings and the wireless connectivity to become unreliable.
To address these issues, the manufacturer implemented several EMI mitigation techniques in the PCB design, including:
- Using a shielding enclosure around the sensitive components
- Providing adequate spacing between traces and components
- Implementing differential signaling for the high-speed signals
- Utilizing TVS diodes to protect against ESD events
After implementing these techniques and performing thorough EMI testing, the manufacturer was able to resolve the EMI issues and bring the patient monitoring system to market.
FAQ
- What is the difference between radiated and conducted EMI?
-
Radiated EMI is electromagnetic interference that is transmitted through the air as electromagnetic waves, while conducted EMI is transmitted through power supply lines or other conductors.
-
How can I minimize crosstalk between adjacent traces on a PCB?
-
To minimize crosstalk, you can provide adequate spacing between traces, use guard traces or shield traces around sensitive signals, and use differential signaling for high-speed signals.
-
What is the purpose of decoupling capacitors in EMI mitigation?
-
Decoupling capacitors are used to minimize power supply noise and high-frequency EMI by providing a low-impedance path for high-frequency currents.
-
How can I determine if my PCB design meets EMI regulations?
-
To determine if your PCB design meets EMI regulations, you can perform EMI simulations using specialized software tools and conduct thorough EMI testing on the fabricated PCB.
-
What are some common EMI regulations that PCBs must meet?
- Some common EMI regulations include the FCC Part 15 rules in the United States, the CE marking requirements in the European Union, and the CISPR standards developed by the International Electrotechnical Commission (IEC).
Conclusion
Addressing EMI issues early in the PCB design stage is crucial for ensuring the proper functioning, reliability, and regulatory compliance of electronic devices. By understanding the sources and coupling mechanisms of EMI, implementing appropriate mitigation techniques in PCB design, and performing thorough simulations and testing, designers can effectively minimize EMI and bring successful products to market.
No responses yet