Introduction
Solder balls, also known as solder beads or spheres, are a common defect in surface mount technology (SMT) manufacturing. These tiny balls of solder can cause short circuits, poor electrical connections, and reliability issues in electronic assemblies. Avoiding solder balls is crucial for ensuring high-quality and reliable SMT products. In this article, we will discuss 11 easy steps you can take to prevent solder ball formation during the SMT manufacturing process.
Understanding Solder Balls
What are solder balls?
Solder balls are small, spherical particles of solder that form during the reflow soldering process in SMT manufacturing. They can range in size from a few microns to several millimeters in diameter. Solder balls can occur on the surface of the printed circuit board (PCB), on component leads, or within the solder joints themselves.
Why do solder balls form?
Solder balls form due to various factors, including:
- Improper solder paste application
- Incorrect reflow profile
- Contamination on the PCB or components
- Unsuitable solder paste chemistry
- Inadequate stencil design or maintenance
The impact of solder balls on SMT manufacturing
Solder balls can have a significant impact on the quality and reliability of SMT assemblies. Some of the issues caused by solder balls include:
- Short circuits between adjacent pins or pads
- Poor electrical connections
- Intermittent failures
- Reduced mechanical strength of solder joints
- Aesthetic defects
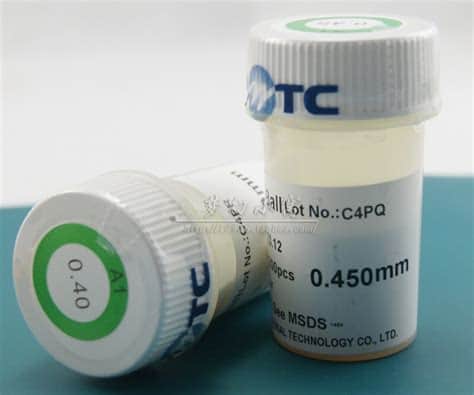
11 Steps to Avoid Solder Balls in SMT Manufacturing
Step 1: Optimize solder paste printing
Proper solder paste application is critical for preventing solder ball formation. Ensure that the solder paste is printed evenly and accurately on the PCB pads. Use a high-quality stencil with the appropriate aperture size and shape for your components. Regularly inspect and maintain the stencil to ensure consistent paste deposition.
Step 2: Control solder paste properties
Use solder paste with the appropriate chemistry and particle size distribution for your application. The solder paste should have good printability, minimal slump, and consistent tackiness. Avoid using expired or contaminated solder paste, as this can lead to solder ball formation and other defects.
Step 3: Maintain proper reflow profile
The reflow profile plays a crucial role in preventing solder ball formation. Ensure that the reflow oven is calibrated and the temperature profile is optimized for your solder paste and components. Avoid excessive peak temperatures, long soak times, and rapid cooling rates, as these can contribute to solder ball formation.
Step 4: Keep PCBs and components clean
Contamination on the PCB surface or component leads can promote solder ball formation. Ensure that the PCBs and components are clean and free from dirt, dust, oils, and other contaminants before solder paste application. Use appropriate cleaning methods, such as isopropyl alcohol or specialized cleaning agents, to remove any residues.
Step 5: Use nitrogen reflow
Nitrogen reflow can help reduce solder ball formation by minimizing oxidation during the soldering process. Nitrogen displaces oxygen in the reflow oven, creating an inert atmosphere that prevents the formation of oxides on the solder surface. This results in cleaner, more reliable solder joints with fewer solder balls.
Step 6: Implement proper component placement
Accurate component placement is essential for preventing solder ball formation. Ensure that the pick-and-place machine is calibrated and the placement pressure is optimized for your components. Avoid excessive placement force, as this can cause solder paste to squeeze out from under the component leads, leading to solder ball formation.
Step 7: Control PCB warpage
PCB warpage can contribute to solder ball formation by creating uneven contact between the component leads and the solder paste. Minimize PCB warpage by using appropriate PCB materials, thickness, and design. Ensure that the PCB is properly supported during the reflow process to prevent excessive warpage.
Step 8: Optimize pad design
Pad design can influence solder ball formation. Use appropriate pad sizes and shapes for your components, taking into account the component dimensions, lead pitch, and solder paste volume. Avoid using oversized or undersized pads, as these can lead to solder ball formation or poor solder joint reliability.
Step 9: Implement solder mask alignment
Proper solder mask alignment is crucial for preventing solder ball formation. Ensure that the solder mask openings are accurately aligned with the PCB pads, providing adequate clearance for the solder paste and component leads. Misaligned solder mask can cause solder paste to spread onto unintended areas, leading to solder ball formation.
Step 10: Monitor and control environment
Environmental factors, such as temperature, humidity, and airborne contaminants, can affect solder ball formation. Maintain a controlled environment in the SMT manufacturing area, with appropriate temperature and humidity levels. Use air filtration systems to minimize airborne contaminants, such as dust and particulates, which can contaminate the solder paste or PCB surface.
Step 11: Perform regular maintenance and inspection
Regular maintenance and inspection of SMT equipment and materials are essential for preventing solder ball formation. Perform routine calibration and maintenance of solder paste printers, pick-and-place machines, and reflow ovens to ensure consistent performance. Inspect incoming materials, such as PCBs, components, and solder paste, for quality and conformance to specifications.
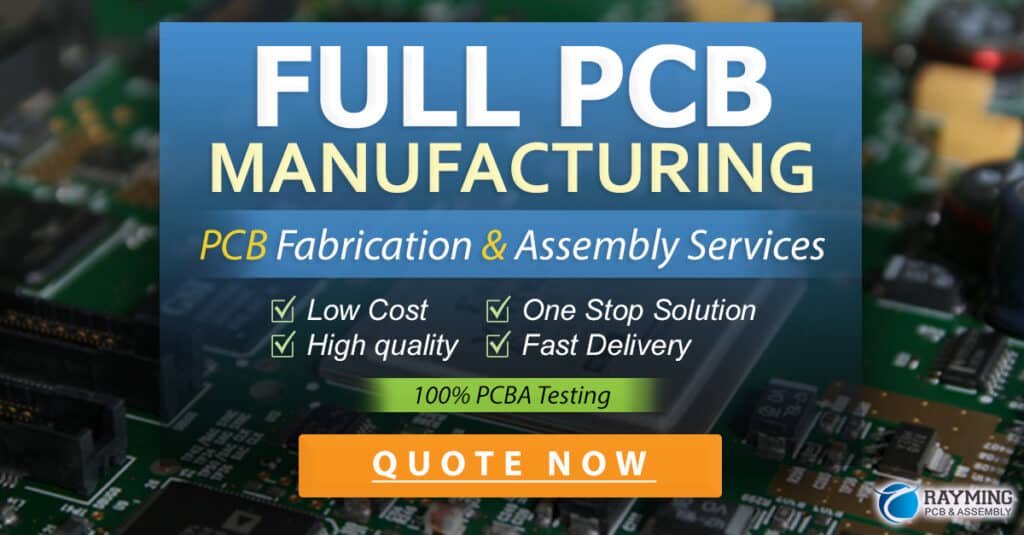
Frequently Asked Questions (FAQ)
1. Can solder balls be reworked?
Yes, solder balls can be reworked, but it is a delicate and time-consuming process. Small solder balls can be removed using a soldering iron with a fine tip or specialized solder ball removal tools. Larger solder balls may require desoldering and cleaning of the affected area before resoldering the component.
2. How can I inspect for solder balls?
Solder balls can be detected using various inspection methods, including:
- Visual inspection using magnification or microscopes
- Automated optical inspection (AOI) systems
- X-ray inspection for hidden solder balls within the solder joints
- Electrical testing to identify short circuits caused by solder balls
3. Can solder ball formation be completely eliminated?
While it may not be possible to completely eliminate solder ball formation, following the 11 steps outlined in this article can significantly reduce their occurrence. Consistent process control, material selection, and adherence to best practices are key to minimizing solder ball defects in SMT manufacturing.
4. How does solder paste quality affect solder ball formation?
Solder paste quality plays a significant role in solder ball formation. Poor quality solder paste with incorrect particle size distribution, inconsistent viscosity, or contamination can lead to solder ball formation during the reflow process. Always use high-quality solder paste from reputable manufacturers and store it according to the manufacturer’s recommendations.
5. Can solder ball formation be influenced by component quality?
Yes, component quality can influence solder ball formation. Components with poor lead coplanarity, contamination, or incorrect dimensions can contribute to solder ball formation. Ensure that the components used in your SMT assembly are of high quality and meet the required specifications. Incoming inspection and supplier quality control are essential for maintaining component quality.
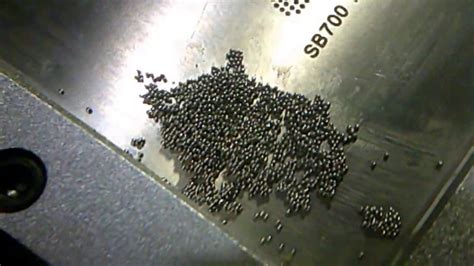
Conclusion
Avoiding solder balls in SMT manufacturing is crucial for ensuring the quality, reliability, and performance of electronic assemblies. By following the 11 easy steps outlined in this article, you can significantly reduce the occurrence of solder ball defects in your SMT process. These steps include optimizing solder paste printing, controlling solder paste properties, maintaining proper reflow profiles, keeping PCBs and components clean, using nitrogen reflow, implementing proper component placement, controlling PCB warpage, optimizing pad design, implementing solder mask alignment, monitoring and controlling the environment, and performing regular maintenance and inspection.
By understanding the causes and impact of solder balls and implementing these preventive measures, you can improve the yield, reliability, and customer satisfaction of your SMT products. Remember, consistency and attention to detail are key to achieving a solder ball-free SMT manufacturing process.
Step | Action | Benefit |
---|---|---|
1 | Optimize solder paste printing | Ensures even and accurate solder paste deposition |
2 | Control solder paste properties | Maintains consistent solder paste performance |
3 | Maintain proper reflow profile | Prevents solder ball formation during reflow |
4 | Keep PCBs and components clean | Minimizes contamination-related solder ball formation |
5 | Use nitrogen reflow | Reduces oxidation and improves solder joint quality |
6 | Implement proper component placement | Ensures accurate and consistent component positioning |
7 | Control PCB warpage | Prevents uneven contact between components and solder paste |
8 | Optimize pad design | Provides appropriate solder paste volume and component fit |
9 | Implement solder mask alignment | Prevents solder paste spreading to unintended areas |
10 | Monitor and control environment | Minimizes environmental factors that contribute to solder ball formation |
11 | Perform regular maintenance and inspection | Ensures consistent performance of SMT equipment and materials |
By implementing these steps and continually monitoring and improving your SMT process, you can effectively avoid solder balls and achieve high-quality, reliable electronic assemblies.
No responses yet