Introduction to Flex PCB soldering
Flexible printed circuit boards (Flex PCBs) have gained tremendous popularity in recent years due to their ability to conform to various shapes and sizes, making them ideal for applications where space is limited or where the device needs to be flexible. However, soldering surface-mount devices (SMDs) on flex PCBs can be challenging, as the flexible nature of the substrate requires special considerations. In this article, we’ll discuss five crucial aspects you need to pay attention to when soldering SMDs on flex PCBs to ensure a successful and reliable assembly.
1. Substrate Preparation and Handling
1.1 Cleaning the Flex PCB
Before starting the soldering process, it is essential to ensure that the flex PCB is clean and free from any contaminants. Contaminants such as dust, oil, or moisture can adversely affect the soldering quality and lead to defects. To clean the flex PCB, use a soft brush or compressed air to remove any loose particles, followed by wiping the surface with isopropyl alcohol (IPA) and a lint-free cloth.
1.2 Handling Flex PCBs
Flex PCBs are more delicate than rigid PCBs due to their thin and flexible nature. Improper handling can cause damage to the substrate or the copper traces. When handling flex PCBs, consider the following:
- Use clean, lint-free gloves to avoid contaminating the surface with oils from your skin.
- Avoid sharp bends or creases, as they can damage the copper traces or the substrate.
- Store flex PCBs in a clean, dry environment, preferably in a protective sleeve or container.
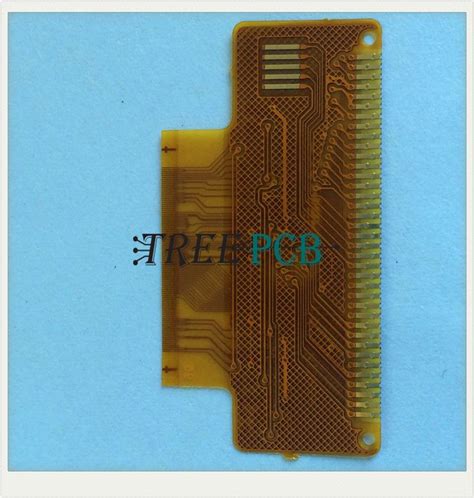
2. Solder Paste Application
2.1 Choosing the Right Solder Paste
Selecting the appropriate solder paste is crucial for achieving reliable solder joints on flex PCBs. The solder paste should have the following properties:
- Compatible with the surface finish of the flex PCB (e.g., ENIG, OSP, or HASL)
- Suitable for the SMD package size and pitch
- Appropriate melting temperature range
- Good printability and tackiness
Some commonly used solder pastes for flex PCB soldering include lead-free alloys such as SAC305 (Sn96.5Ag3.0Cu0.5) or SN100C (Sn99.3Cu0.7 + Ni).
2.2 Solder Paste Printing
Solder paste can be applied to the flex PCB using a stencil or syringe. When using a stencil, ensure that it is designed specifically for the flex PCB, taking into account the substrate’s flexibility and the required solder paste volume. If using a syringe, apply the solder paste carefully to avoid bridging or insufficient paste deposition.
Solder Paste Application Method | Advantages | Disadvantages |
---|---|---|
Stencil Printing | – Fast and efficient for high-volume production – Consistent solder paste deposition |
– Requires a custom stencil for each PCB design – May be challenging to maintain proper stencil alignment on flexible substrates |
Syringe Dispensing | – Suitable for low-volume production or prototyping – Allows for precise solder paste application |
– Time-consuming for large PCBs or high component counts – Requires operator skill to ensure consistent paste deposition |
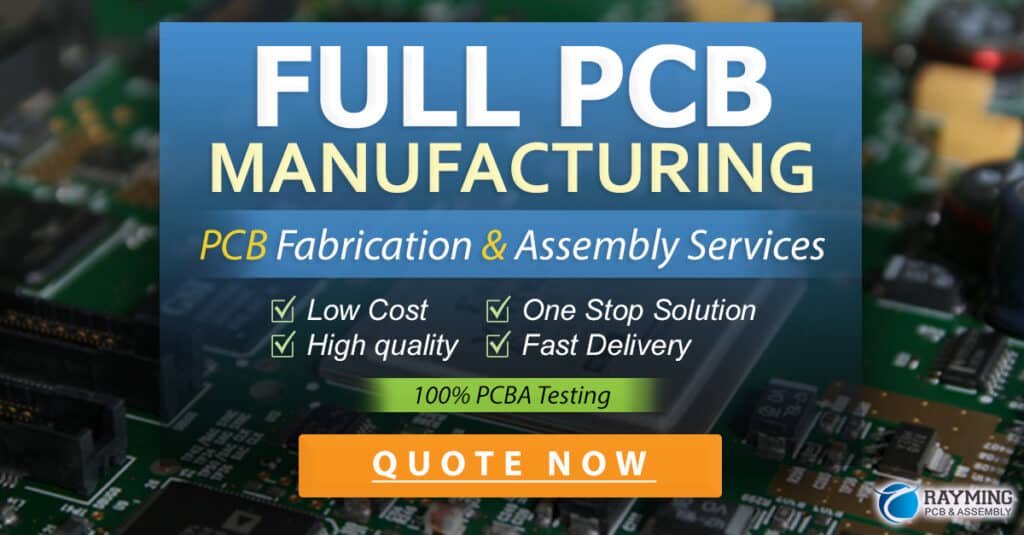
3. Component Placement
3.1 Alignment and Orientation
Accurate component placement is essential for achieving reliable solder joints and preventing defects such as tombstoning or bridging. When placing SMDs on a flex PCB, consider the following:
- Use a pick-and-place machine or a fine-tipped tweezers for precise component placement.
- Ensure that the component is aligned with the solder pads and oriented correctly.
- If using a pick-and-place machine, adjust the placement pressure to account for the flexibility of the substrate.
3.2 Securing Components
Due to the flexible nature of the substrate, components may shift during the soldering process, leading to misalignment or poor solder joint formation. To minimize component movement, consider using one of the following methods:
- Adhesive dots: Apply small dots of adhesive, such as epoxy or silicone, to the PCB before placing the components. The adhesive will help secure the components in place during soldering.
- Solder paste tackiness: Some solder pastes exhibit good tackiness, which can help hold the components in place. Ensure that the solder paste has sufficient tackiness to secure the components.
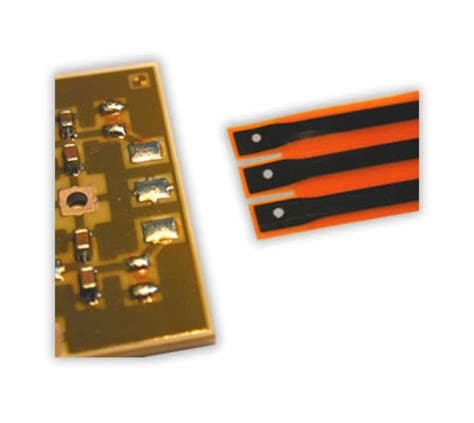
4. Soldering Process
4.1 Reflow Soldering
Reflow soldering is the most common method for soldering SMDs on flex PCBs. The process involves applying heat to the PCB assembly in a controlled manner, allowing the solder paste to melt and form a bond between the component leads and the solder pads. When reflow soldering flex PCBs, consider the following:
- Use a low-temperature solder paste to minimize thermal stress on the flexible substrate.
- Adjust the reflow profile to account for the thermal properties of the flex PCB material (e.g., polyimide or polyester).
- Ensure that the PCB assembly is adequately supported during the reflow process to prevent warping or damage.
4.2 Hand Soldering
In some cases, hand soldering may be necessary for rework or for soldering components that are not compatible with reflow soldering. When hand soldering SMDs on flex PCBs, keep the following points in mind:
- Use a fine-tipped soldering iron with a low wattage (e.g., 20-30 watts) to minimize heat exposure to the substrate.
- Apply heat to the component lead and solder pad simultaneously, ensuring that both are heated evenly.
- Use a soldering iron with a flexible tip or a tip specifically designed for soldering on flexible substrates to prevent damage to the PCB.
5. Inspection and Quality Control
5.1 Visual Inspection
After the soldering process, visually inspect the solder joints for any defects or anomalies. Common issues to look for include:
- Bridging: Solder connecting adjacent solder pads or component leads
- Insufficient solder: Solder joint appears concave or does not fully cover the component lead
- Tombstoning: One end of the component is lifted off the solder pad
- Solder balls: Small spheres of solder adhering to the PCB surface or component leads
Use a magnifying glass or microscope to perform a thorough visual inspection of the solder joints.
5.2 Automated Optical Inspection (AOI)
For high-volume production, automated optical inspection (AOI) systems can be used to detect soldering defects quickly and accurately. AOI systems use cameras and image processing algorithms to compare the soldered assembly to a predefined set of criteria, identifying any deviations or anomalies.
Inspection Method | Advantages | Disadvantages |
---|---|---|
Visual Inspection | – Can identify a wide range of defects – Does not require specialized equipment |
– Time-consuming for large PCBs or high component counts – Relies on operator skill and attention to detail |
Automated Optical Inspection (AOI) | – Fast and efficient for high-volume production – Provides consistent and objective results |
– Requires specialized equipment and software – May have difficulty detecting certain types of defects (e.g., insufficient solder under components) |
Frequently Asked Questions (FAQ)
1. What are the most common challenges when soldering SMDs on flex PCBs?
The most common challenges when soldering SMDs on flex PCBs include:
– Handling and securing the flexible substrate during the soldering process
– Applying the appropriate amount of heat to prevent damage to the substrate
– Ensuring accurate component placement and alignment
– Minimizing thermal stress on the substrate during reflow soldering
2. Can I use the same solder paste for flex PCBs as I do for rigid PCBs?
While some solder pastes may be suitable for both rigid and flex PCBs, it is generally recommended to use a low-temperature solder paste specifically designed for flexible substrates. These solder pastes typically have a lower melting point and are formulated to minimize thermal stress on the flex PCB material.
3. How can I prevent component shifting during reflow soldering?
To prevent component shifting during reflow soldering, you can use adhesive dots or take advantage of the solder paste’s tackiness to secure the components in place. Additionally, ensure that the PCB assembly is adequately supported during the reflow process to minimize warping or movement.
4. What type of soldering iron tip should I use for hand soldering on flex PCBs?
When hand soldering on flex PCBs, use a fine-tipped soldering iron with a low wattage (20-30 watts) to minimize heat exposure to the substrate. A flexible tip or a tip specifically designed for soldering on flexible substrates can also help prevent damage to the PCB.
5. How can I ensure the quality of solder joints on flex PCBs?
To ensure the quality of solder joints on flex PCBs, perform a thorough visual inspection using a magnifying glass or microscope, looking for defects such as bridging, insufficient solder, tombstoning, or solder balls. For high-volume production, consider using an automated optical inspection (AOI) system to detect soldering defects quickly and accurately.
Conclusion
Soldering SMDs on flex PCBs requires careful attention to substrate preparation, solder paste application, component placement, the soldering process, and quality control. By following the guidelines outlined in this article and paying attention to the five key aspects discussed, you can achieve reliable and high-quality solder joints on your flex PCB assemblies.
Remember to handle flex PCBs with care, choose the appropriate solder paste and soldering methods, and thoroughly inspect the soldered assembly for any defects. With practice and attention to detail, you can master the art of soldering SMDs on flex PCBs and create functional and durable electronic devices.
No responses yet