What is an Absolute Pressure Sensor?
An absolute pressure sensor is a device that measures the pressure of a system relative to a perfect vacuum (zero pressure). Unlike gauge pressure sensors, which measure pressure relative to atmospheric pressure, absolute pressure sensors provide a true pressure reading that is independent of external conditions. This makes them ideal for applications where accurate and consistent pressure measurements are critical, such as in barometric pressure monitoring, altitude sensing, and vacuum control.
The working principle of an absolute pressure sensor is based on the deformation of a diaphragm or membrane in response to the applied pressure. The sensor contains a sealed reference chamber with a known pressure (usually a vacuum), and the diaphragm separates this reference chamber from the process pressure being measured. As the process pressure changes, the diaphragm deflects, and this deformation is converted into an electrical signal using various transduction methods, such as piezoresistive, capacitive, or resonant sensing.
Types of Absolute Pressure Sensors
There are several types of absolute pressure sensors available, each with its own advantages and limitations. The choice of sensor depends on factors such as the pressure range, accuracy, size, and environmental conditions. Some of the most common types of absolute pressure sensors include:
Piezoresistive Absolute Pressure Sensors
Piezoresistive absolute pressure sensors utilize the piezoresistive effect, where the electrical resistance of a material changes when subjected to mechanical stress. In these sensors, the diaphragm is typically made of silicon and has piezoresistive elements embedded in it. When the diaphragm deflects due to the applied pressure, the resistance of the piezoresistive elements changes, and this change is measured using a Wheatstone Bridge circuit. Piezoresistive sensors offer high sensitivity, wide pressure ranges, and good linearity, making them suitable for a wide range of applications.
Capacitive Absolute Pressure Sensors
Capacitive absolute pressure sensors rely on the change in capacitance between the diaphragm and a fixed electrode. As the diaphragm deflects under the applied pressure, the distance between the diaphragm and the electrode changes, resulting in a corresponding change in capacitance. This change is then detected and converted into an electrical signal. Capacitive sensors offer high sensitivity, low power consumption, and good long-term stability, making them ideal for precision measurements in low-pressure applications.
Resonant Absolute Pressure Sensors
Resonant absolute pressure sensors use the principle of resonance frequency shift to measure pressure. In these sensors, the diaphragm is typically a vibrating element, such as a quartz crystal or a silicon resonator. The resonance frequency of the diaphragm is sensitive to the applied pressure, and as the pressure changes, the frequency shifts accordingly. Resonant sensors offer high accuracy, excellent long-term stability, and low temperature sensitivity, making them suitable for demanding applications in harsh environments.
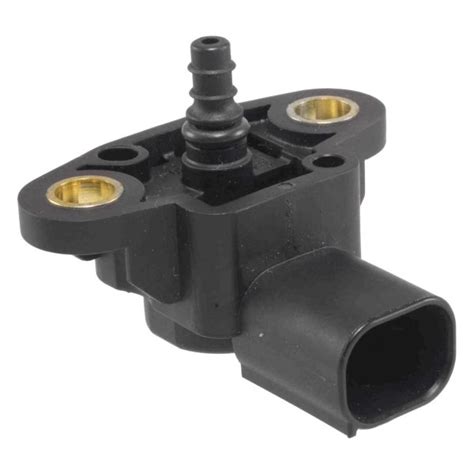
Applications of Absolute Pressure Sensors
Absolute pressure sensors find applications in a wide range of industries and fields, from automotive and aerospace to medical and meteorology. Some of the key applications include:
-
Barometric Pressure Monitoring: Absolute pressure sensors are used in weather stations and meteorological equipment to measure atmospheric pressure accurately. This data is essential for weather forecasting, climate studies, and aviation.
-
Altitude Sensing: In aerospace and automotive applications, absolute pressure sensors are used to determine the altitude of an aircraft or vehicle based on the atmospheric pressure. This information is crucial for navigation, engine control, and safety systems.
-
Vacuum Control: Absolute pressure sensors are used in vacuum systems to monitor and control the pressure levels. This is important in applications such as semiconductor manufacturing, thin film deposition, and scientific research.
-
Medical Devices: Absolute pressure sensors are used in various medical devices, such as blood pressure monitors, respirators, and anesthesia machines, to ensure accurate and reliable pressure measurements for patient safety and treatment efficacy.
-
Industrial Process Control: In industrial settings, absolute pressure sensors are used to monitor and control the pressure in various processes, such as hydraulic systems, pneumatic equipment, and gas pipelines. This helps optimize process efficiency, ensure product quality, and maintain safety.
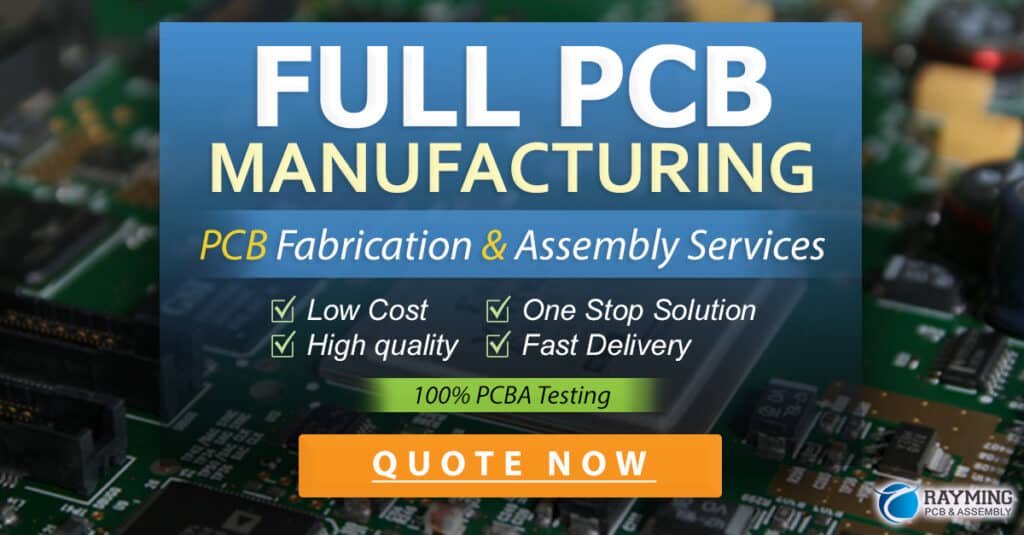
Selecting the Right Absolute Pressure Sensor
When choosing an absolute pressure sensor for your application, there are several key factors to consider:
-
Pressure Range: Determine the pressure range your application requires and select a sensor that covers this range with sufficient margin. Absolute pressure sensors are available in various ranges, from low vacuum to high pressure.
-
Accuracy and Precision: Consider the accuracy and precision requirements of your application. Higher accuracy sensors may be necessary for critical measurements, but they also come at a higher cost.
-
Environmental Conditions: Evaluate the environmental conditions the sensor will be exposed to, such as temperature, humidity, and vibration. Choose a sensor that is designed to withstand these conditions and maintain its performance.
-
Size and Packaging: Consider the size and packaging constraints of your application. Absolute pressure sensors come in various form factors, from surface-mount devices to threaded and flanged packages, to accommodate different installation requirements.
-
Output and Interface: Determine the output and interface requirements for your system. Absolute pressure sensors can provide analog or digital outputs, such as voltage, current, or I2C/SPI communication protocols.
-
Cost and Reliability: Balance the cost and reliability factors based on your application needs. Higher-end sensors may offer better performance and long-term stability but at a higher cost. Consider the total cost of ownership, including maintenance and calibration requirements.
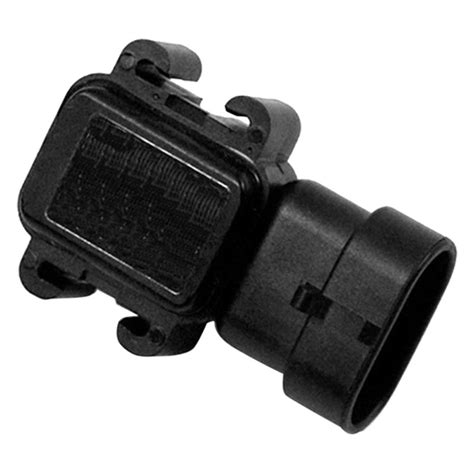
FAQ
-
What is the difference between absolute pressure and gauge pressure?
Absolute pressure is measured relative to a perfect vacuum (zero pressure), while gauge pressure is measured relative to the ambient atmospheric pressure. Absolute pressure sensors provide a true pressure reading independent of external conditions, while gauge pressure sensors measure the pressure difference between the system and the atmosphere. -
Can absolute pressure sensors be used for measuring vacuum?
Yes, absolute pressure sensors are commonly used for measuring vacuum levels. They can accurately measure pressures below atmospheric pressure, making them suitable for vacuum control applications in industries such as semiconductor manufacturing and scientific research. -
How do I calibrate an absolute pressure sensor?
Calibrating an absolute pressure sensor typically involves applying known reference pressures to the sensor and adjusting its output to match the corresponding pressure values. This can be done using a precision pressure calibrator or a dead-weight tester. It is important to follow the manufacturer’s recommended calibration procedures and intervals to ensure the sensor’s accuracy and reliability. -
What is the typical accuracy of an absolute pressure sensor?
The accuracy of an absolute pressure sensor varies depending on the type and grade of the sensor. Typical accuracies range from ±0.1% to ±1% of the full-scale output, with higher-end sensors offering better accuracy. It is important to select a sensor with an accuracy that meets the requirements of your application. -
How do temperature changes affect absolute pressure sensors?
Temperature changes can affect the performance of absolute pressure sensors, causing shifts in offset, sensitivity, and linearity. To minimize these effects, many sensors incorporate temperature compensation techniques, such as using temperature-sensitive elements or applying mathematical corrections based on temperature measurements. It is important to consider the temperature range your sensor will be exposed to and choose a sensor with appropriate compensation methods.
Sensor Type | Pressure Range | Accuracy | Output | Key Features |
---|---|---|---|---|
Piezoresistive | 0.1 to 1000 bar | ±0.1% to ±1% FS | Analog (mV) | High sensitivity, wide pressure range |
Capacitive | 0.1 to 10 bar | ±0.1% to ±0.5% FS | Analog (mV) or Digital (I2C/SPI) | High sensitivity, low power consumption |
Resonant | 0.1 to 100 bar | ±0.01% to ±0.1% FS | Digital (Frequency) | High accuracy, excellent long-term stability |
In conclusion, absolute pressure sensors are essential tools for precise barometric pressure measurement in various applications. By understanding the working principles, types, and key considerations for selecting the right sensor, you can ensure accurate and reliable pressure monitoring in your system. Whether you are working on weather monitoring, aerospace, medical devices, or industrial process control, choosing the appropriate absolute pressure sensor is crucial for optimizing performance and maintaining safety.
No responses yet