Understanding the Differences Between Immersion Gold and Gold Plating
When it comes to protecting and enhancing the appearance of various metal surfaces, particularly in the electronics industry, two popular methods are often employed: immersion gold and gold plating. While both techniques involve the application of a thin layer of gold, they differ in their processes, properties, and applications. In this article, we will delve into the key distinctions between immersion gold and gold plating, helping you make informed decisions for your specific needs.
What is Immersion Gold?
Immersion gold, also known as electroless gold or chemical gold, is a process that involves depositing a thin layer of gold onto a metal surface through a chemical reaction. Unlike electroplating, immersion gold does not require an external electrical current. Instead, it relies on a chemical exchange between the gold ions in the solution and the metal substrate.
The immersion gold process typically consists of the following steps:
- Surface preparation: The metal surface is cleaned and activated to ensure proper adhesion of the gold layer.
- Immersion: The metal substrate is immersed in a solution containing gold ions and a reducing agent.
- Chemical reaction: The reducing agent causes the gold ions to precipitate onto the metal surface, forming a thin, uniform layer of gold.
- Rinsing and drying: The coated surface is rinsed with water to remove any excess solution and then dried.
Immersion gold is commonly used in the electronics industry for coating printed circuit boards (PCBs), connectors, and other components. It provides excellent solderability, corrosion resistance, and electrical conductivity.
What is Gold Plating?
Gold plating, also referred to as electrolytic gold plating or electroplating, is a process that involves depositing a layer of gold onto a metal surface using an electric current. The metal substrate to be plated serves as the cathode, while a gold anode is used as the source of gold ions.
The gold plating process typically involves the following steps:
- Surface preparation: The metal surface is cleaned, degreased, and activated to ensure proper adhesion of the gold layer.
- Electrolytic bath: The metal substrate is immersed in an electrolytic solution containing gold ions and other additives.
- Electrodeposition: An electric current is applied, causing the gold ions to migrate from the anode to the cathode, depositing a layer of gold on the metal surface.
- Rinsing and drying: The plated surface is rinsed with water to remove any excess solution and then dried.
Gold plating offers a range of benefits, including improved corrosion resistance, enhanced electrical conductivity, and a lustrous, decorative appearance. It is widely used in various industries, such as jewelry, automotive, aerospace, and electronics.
Key Differences Between Immersion Gold and Gold Plating
While both immersion gold and gold plating result in a layer of gold on a metal surface, there are several key differences between the two processes:
Thickness and Uniformity
One of the primary differences between immersion gold and gold plating lies in the thickness and uniformity of the gold layer.
Process | Thickness | Uniformity |
---|---|---|
Immersion Gold | Typically 0.05-0.2 microns | Highly uniform, even on complex geometries |
Gold Plating | Can range from 0.1-100 microns or more | May have variations in thickness, especially on intricate shapes |
Immersion gold deposits a very thin, highly uniform layer of gold, usually in the range of 0.05 to 0.2 microns. This thin layer is sufficient for providing excellent solderability and corrosion resistance. The chemical nature of the immersion gold process ensures a consistent thickness, even on complex geometries and hard-to-reach areas.
On the other hand, gold plating can produce thicker layers of gold, ranging from 0.1 microns to 100 microns or more, depending on the application requirements. However, the thickness of the gold layer may vary, particularly on intricate shapes or in recessed areas, due to the limitations of the electroplating process.
Adhesion and Durability
The adhesion and durability of the gold layer are important considerations when choosing between immersion gold and gold plating.
Process | Adhesion | Durability |
---|---|---|
Immersion Gold | Excellent adhesion due to chemical bonding | Limited durability due to thin layer |
Gold Plating | Good adhesion, but may require additional surface preparation | Higher durability, especially with thicker layers |
Immersion gold offers excellent adhesion to the metal substrate due to the chemical bonding that occurs during the deposition process. The gold atoms form a strong, intimate connection with the metal surface, resulting in a highly adherent layer. However, the thin nature of the immersion gold layer limits its durability, particularly in applications that involve high wear or abrasion.
Gold plating, on the other hand, relies on mechanical bonding between the gold layer and the metal substrate. To achieve good adhesion, proper surface preparation, such as cleaning and activation, is crucial. The durability of gold plating is generally higher than that of immersion gold, especially when thicker layers are applied. Thicker gold plating can withstand more wear and tear, making it suitable for applications that require enhanced durability.
Cost and Processing Time
Cost and processing time are important factors to consider when selecting between immersion gold and gold plating.
Process | Cost | Processing Time |
---|---|---|
Immersion Gold | Relatively low cost due to thin layer and simple process | Short processing time, typically a few minutes |
Gold Plating | Higher cost, especially for thicker layers | Longer processing time, depending on desired thickness |
Immersion gold is generally considered a cost-effective option compared to gold plating. The thin layer of gold required for immersion gold reduces the overall material cost. Additionally, the simplicity of the immersion gold process, which does not require complex equipment or external power sources, contributes to its lower cost.
Gold plating, on the other hand, can be more expensive, particularly when thicker layers of gold are required. The cost of gold plating is directly proportional to the thickness of the gold layer and the size of the surface area to be plated. The need for specialized equipment, such as rectifiers and plating baths, also adds to the overall cost of gold plating.
In terms of processing time, immersion gold has an advantage over gold plating. The immersion gold process is relatively quick, typically taking only a few minutes to complete. The chemical reaction occurs rapidly, allowing for efficient production cycles.
Gold plating, however, can be more time-consuming, especially when thicker layers of gold are desired. The electroplating process requires time for the gold ions to migrate and deposit onto the metal surface. The processing time for gold plating can range from several minutes to hours, depending on the desired thickness and the size of the surface area being plated.
Applications and Industry Usage
Immersion gold and gold plating find applications in various industries, each with its specific requirements and preferences.
Process | Common Applications | Industries |
---|---|---|
Immersion Gold | PCBs, connectors, contacts | Electronics, telecommunications |
Gold Plating | Jewelry, decorative items, high-wear components | Jewelry, automotive, aerospace, medical devices |
Immersion gold is widely used in the electronics industry, particularly for coating printed circuit boards (PCBs), connectors, and electrical contacts. Its excellent solderability, corrosion resistance, and electrical conductivity make it ideal for these applications. Immersion gold ensures reliable and consistent performance in electronic devices, making it a preferred choice for manufacturers in the telecommunications and consumer electronics sectors.
Gold plating, with its ability to produce thicker layers of gold, finds applications in a broader range of industries. In the jewelry industry, gold plating is commonly used to enhance the appearance and durability of various decorative items, such as rings, necklaces, and earrings. The automotive and aerospace industries utilize gold plating for high-wear components, taking advantage of its corrosion resistance and tribological properties. Medical device manufacturers also employ gold plating for its biocompatibility and resistance to sterilization processes.
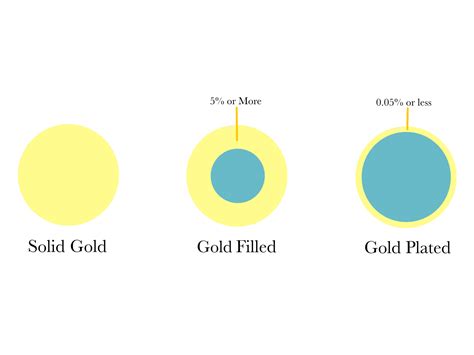
Frequently Asked Questions (FAQ)
-
Q: Can immersion gold be used for decorative purposes?
A: While immersion gold provides a thin, uniform layer of gold, it is primarily used for functional purposes, such as improving solderability and corrosion resistance. For decorative applications, gold plating is generally preferred due to the ability to achieve thicker layers and a more lustrous appearance. -
Q: Is it possible to apply gold plating over immersion gold?
A: Yes, it is possible to apply gold plating over immersion gold. In fact, this combination is sometimes used in the electronics industry to achieve both the benefits of immersion gold (excellent solderability and uniformity) and the added durability and thickness of gold plating. -
Q: How does the corrosion resistance of immersion gold compare to gold plating?
A: Both immersion gold and gold plating offer good corrosion resistance. However, the level of protection may vary depending on the thickness of the gold layer. Thicker gold plating can provide enhanced corrosion resistance compared to the thin layer of immersion gold. -
Q: Can immersion gold be used for high-wear applications?
A: Immersion gold is generally not recommended for high-wear applications due to the thin nature of the gold layer. For applications that involve significant wear or abrasion, gold plating with thicker layers is typically preferred. -
Q: Is it possible to selectively apply immersion gold or gold plating to specific areas of a component?
A: Yes, both immersion gold and gold plating can be selectively applied to specific areas of a component using masking techniques. Masking involves covering the areas that do not require gold deposition with a resist material, allowing the gold to be applied only to the desired regions.
Conclusion
Immersion gold and gold plating are two distinct methods for depositing a layer of gold onto a metal surface. While both processes aim to enhance the properties and appearance of the substrate, they differ in terms of thickness, uniformity, adhesion, durability, cost, and processing time.
Immersion gold offers a thin, highly uniform layer of gold that provides excellent solderability, corrosion resistance, and electrical conductivity. It is commonly used in the electronics industry for coating PCBs, connectors, and contacts. The immersion gold process is relatively simple, cost-effective, and quick, making it suitable for high-volume production.
Gold plating, on the other hand, allows for thicker layers of gold and finds applications in a wider range of industries, including jewelry, automotive, aerospace, and medical devices. It offers good adhesion, enhanced durability, and a lustrous appearance. However, gold plating may have variations in thickness and requires longer processing times compared to immersion gold.
When deciding between immersion gold and gold plating, it is essential to consider the specific requirements of your application, such as the desired thickness, durability, cost, and processing time. Understanding the key differences between these two processes will help you make an informed decision and select the most suitable method for your needs.
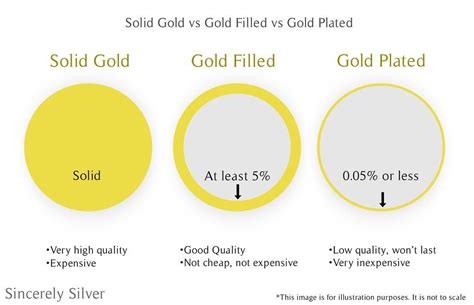
No responses yet