What is an AOI Test?
An Automated Optical Inspection (AOI) test is a visual inspection method used in manufacturing to quickly detect defects, errors or deviations in printed circuit board assemblies (PCBAs). It uses cameras and image processing software to scan the PCBAs and compare them against a “golden sample” or known good board.
AOI tests are a critical part of ensuring quality control in electronics manufacturing. They help identify issues such as:
- Missing components
- Misaligned or rotated components
- Solder defects (bridges, insufficient solder, etc.)
- Incorrect part placement
- Damaged or skewed components
By catching these defects early in the production process, manufacturers can minimize scrap, rework and repair costs down the line. AOI is usually performed right after the solder paste and component placement steps, before the PCBAs go into the reflow oven.
How Does an AOI Test Work?
A typical inline AOI test system consists of:
- Conveyor belt to transport PCBAs
- Top-view and/or angled cameras to image the boards
- Lighting system to illuminate boards for imaging
- Image processing hardware and software
- Interface to alert operators of failures
Here’s a simplified overview of how an AOI test is performed:
- A bare or populated PCB is placed on the conveyor belt
- It is transported into the AOI machine enclosure
- Cameras capture images of the board from various angles
- Lighting illuminates key areas for accurate defect detection
- Image processing software analyzes the captured images
- The PCBA is compared to pre-programmed inspection criteria
- Any defects or deviations are flagged and reported
- The PCBA is diverted for rework if it fails the AOI test
- Good boards continue down the assembly line for further processing
The entire AOI test process is automatic and can be completed in seconds per board, enabling high-volume inspection. Advanced AOI systems may use multiple cameras, colored lighting, and 3D imaging to better detect defects on high-density, double-sided boards.
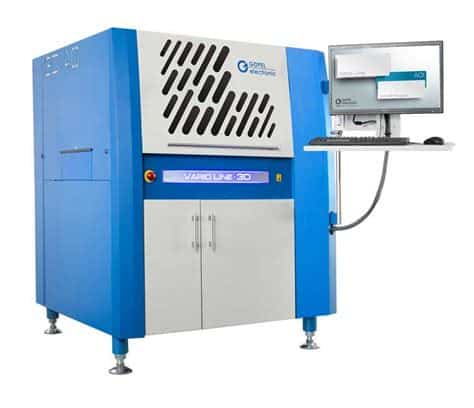
Benefits of AOI Testing
Implementing AOI testing provides electronics manufacturers with several key advantages:
1. Early Defect Detection
AOI allows defects to be caught early in the production process, before more value is added to the PCBA. This prevents good parts from being wasted on a faulty board. Identifying defects sooner also simplifies rework and repair.
2. Improved Quality and Reliability
By screening out defective boards, AOI helps ensure that only good quality products make it to later stages of production and to the customer. This improves overall PCBA quality, reliability and customer satisfaction.
3. Increased Throughput
AOI systems can inspect PCBAs much faster than human operators, often in a matter of seconds. This high-speed automated inspection increases production throughput without compromising quality.
4. Reduced Costs
While there is an initial investment in AOI equipment, it quickly pays for itself by reducing scrap, rework and warranty claims. AOI also frees up human operators for other tasks, improving productivity.
5. Consistent and Objective Inspection
Unlike human inspectors, AOI systems don’t get fatigued, distracted or make subjective judgments. They provide consistent, objective and repeatable inspection results based on pre-defined criteria.
6. Traceable Quality Data
AOI systems generate traceable quality data that can be used to monitor process performance, identify problem areas, and drive continuous improvement efforts. This data also provides a quality audit trail.
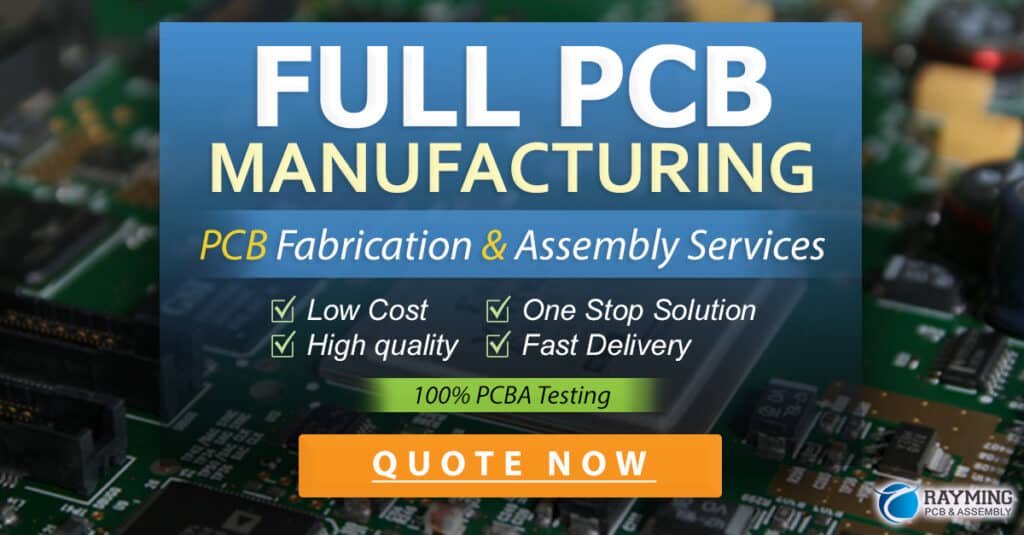
Limitations of AOI Testing
While AOI testing provides significant benefits, it’s important to understand its limitations:
1. Limited Defect Coverage
AOI is primarily a visual inspection method. It cannot detect defects that are hidden under components or not visible on the surface of the PCBA. For example, AOI cannot check for opens and shorts in the PCB itself. It is often used in conjunction with other inspection methods like in-circuit testing (ICT), x-ray inspection, and functional testing for more comprehensive defect coverage.
2. Programming Complexity
AOI systems need to be programmed with inspection criteria for each new PCBA design. This involves creating a “golden board” with the correct component placement and solder joints, and teaching the AOI software what a good board looks like. For complex boards with many components, AOI programming can be time-consuming.
3. False Failures
AOI systems may occasionally flag good boards as defective, known as false failures or false positives. This can happen if the inspection criteria are too strict or if there are slight variations in the appearance of good boards. False failures require additional manual inspection, which reduces productivity.
4. Sensitivity to Design Changes
AOI programs are specific to each PCBA design. Any changes to the design, such as moving a component or changing a part number, require the AOI program to be updated. This makes AOI testing less flexible than manual inspection.
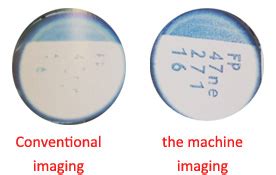
Types of AOI Systems
There are several types of AOI systems used in electronics manufacturing:
AOI System Type | Description |
---|---|
2D AOI | Uses top-view and/or angled cameras to capture 2D images of the PCBA surface. Ideal for inspecting component presence, position and solder joints. |
3D AOI | Uses multiple cameras or laser scanners to create a 3D reconstruction of the PCBA surface. Provides better defect detection for tall components, lead coplanarity and solder volume. |
Inline AOI | Installed directly in the production line, often after solder paste inspection (SPI) and automated pick-and-place. Inspects every board in real-time. |
Offline AOI | Standalone system used for batch inspection of PCBAs. Often used for low-volume production or sample audits. |
Desktop AOI | Benchtop system used for manual inspection of small batches or individual boards. Suitable for prototyping, rework and failure analysis. |
The choice of AOI system depends on factors such as production volume, PCBA complexity, defect types, floor space and budget.
Implementing AOI Testing
To successfully implement AOI testing, electronics manufacturers should follow these best practices:
1. Define Inspection Requirements
Clearly define what defects need to be detected by the AOI system, and to what level of accuracy. This will guide the selection of an appropriate AOI system and the development of inspection programs.
2. Optimize PCBA Design for AOI
Design PCBAs with AOI testing in mind. This includes providing adequate spacing between components, using fiducials for board registration, and avoiding component shadowing. Collaborate with AOI vendors to ensure the design can be effectively inspected.
3. Develop Robust AOI Programs
Create comprehensive AOI programs that cover all critical defects for each PCBA. Use a golden board to teach the AOI system what a good board looks like. Validate the program on a representative sample of boards to ensure it can detect real defects without false failures.
4. Establish a Defect Review Process
Set up a process for reviewing boards that fail AOI testing. This includes verifying true defects, identifying false failures, and providing feedback to improve the AOI program. Use defect data to track process performance and drive corrective actions.
5. Train Operators and Maintenance Personnel
Provide adequate training to AOI operators and maintenance personnel. Operators should understand how to load boards, interpret results, and handle defective boards. Maintenance staff should know how to calibrate the system, update programs, and troubleshoot issues.
6. Monitor and Optimize Performance
Regularly monitor AOI system performance metrics such as first pass yield, defect escape rate, and false failure rate. Use this data to identify opportunities for improving the AOI program, upstream processes, and board design. Continuously update and optimize AOI programs as new products are introduced.
AOI Test Standards and Guidelines
Several industry standards and guidelines are available to help electronics manufacturers implement effective AOI testing:
- IPC-A-610: Acceptability of Electronic Assemblies
- IPC-A-600: Acceptability of Printed Boards
- IPC-7912: Surface Mount Design and Land Pattern Standard
- IPC-SM-782: Surface Mount Design and Land Pattern Standard
- JEDEC JESD-609: Marking, Symbols, and Labels for Identification of Lead-Free Assemblies, Components, and Devices
These standards provide criteria for component placement, solder joint quality, and board markings that can be used to develop AOI inspection programs. They also promote consistency and compatibility across the electronics industry.
Frequently Asked Questions (FAQ)
1. Is AOI testing suitable for all types of PCBAs?
AOI testing is suitable for most types of PCBAs, including through-hole, surface mount, and mixed technology assemblies. However, it may not be effective for inspecting hidden or obstructed areas, such as under BGAs or connectors. In these cases, AOI should be combined with other inspection methods like x-ray or boundary scan testing.
2. Can AOI replace visual inspection by human operators?
AOI can replace most routine visual inspection tasks performed by human operators, such as checking component presence, position, and solder joint quality. However, some complex defects or cosmetic issues may still require human judgment. AOI is often used to screen out obvious defects, while human operators perform a final visual inspection on a sample of boards.
3. How much does an AOI system cost?
The cost of an AOI system varies widely depending on factors such as the type of system, camera resolution, lighting options, and software features. Entry-level desktop AOI systems may cost around $50,000, while high-end inline 3D AOI systems can exceed $500,000. The total cost of ownership should also consider expenses for installation, training, maintenance, and programming.
4. How long does it take to program an AOI system for a new PCBA?
The time required to program an AOI system for a new PCBA depends on the complexity of the board, the number of components, and the experience of the programmer. Simple boards with a few dozen components may take a few hours to program, while complex boards with thousands of components can take several days. Some AOI systems offer automated programming features that can reduce programming time.
5. Can AOI detect counterfeit components?
AOI systems are not specifically designed to detect counterfeit components, as they primarily inspect the physical appearance of components and solder joints. However, some advanced AOI systems may be able to detect inconsistencies in component markings or packages that could indicate counterfeits. To fully mitigate the risk of counterfeits, AOI should be combined with other measures such as supply chain management, incoming inspection, and electrical testing.
No responses yet