What is a Single-Layer PCB?
A single-layer PCB, also known as a Single-sided PCB, is a printed circuit board that has conductive traces on only one side of the board. The other side of the board is typically left bare, although it may have a silk screen printing for component labels or other markings. Single-layer PCBs are the simplest and most cost-effective type of PCB, making them a popular choice for low-complexity electronic projects and prototypes.
Advantages of Single-Layer PCBs
Single-layer PCBs offer several advantages over other types of PCBs:
- Cost-effective: Single-layer PCBs are the most affordable type of PCB due to their simple design and manufacturing process.
- Easy to design: With only one layer to work with, designing a single-layer PCB is relatively straightforward and can be done using basic PCB design software.
- Quick turnaround: The manufacturing process for single-layer PCBs is faster than that of multi-layer PCBs, resulting in shorter lead times.
- Suitable for low-complexity projects: Single-layer PCBs are ideal for simple electronic projects that do not require a high component density or complex routing.
Disadvantages of Single-Layer PCBs
Despite their advantages, single-layer PCBs also have some limitations:
- Limited routing options: With only one layer available for routing, single-layer PCBs may require jumper wires to complete connections that cannot be routed on the board itself.
- Lower component density: Single-layer PCBs cannot accommodate as many components as multi-layer PCBs due to the limited space available for routing.
- Reduced signal integrity: Single-layer PCBs are more susceptible to electromagnetic interference (EMI) and crosstalk compared to multi-layer PCBs with dedicated ground and power planes.
- Limited power handling: The single layer of copper on a single-layer PCB may not be sufficient for high-current applications, which can lead to excessive heat generation and reduced reliability.
Single-Layer PCB Manufacturing Process
The manufacturing process for single-layer PCBs involves several steps:
- PCB Design: The first step is to create a PCB layout using PCB design software. The layout includes the component placement, routing, and any necessary markings or labels.
- Film Generation: Once the PCB layout is complete, a photographic film or photomask is created based on the design. This film is used to transfer the PCB layout onto the copper-clad board.
- Copper Etching: The copper-clad board is coated with a photoresist material and exposed to UV light through the photomask. The exposed areas of the photoresist are then removed, leaving the desired copper traces protected. The board is then immersed in an etching solution, which removes the unprotected copper, leaving only the desired traces.
- Drilling: Holes are drilled through the board for through-hole components and vias.
- Solder Mask Application: A solder mask is applied to the board to protect the copper traces and prevent solder bridging during assembly. The solder mask also provides insulation and improves the board’s appearance.
- Silk Screen Printing: If desired, a silk screen printing process is used to add component labels, logos, or other markings to the board.
- Surface Finish: A surface finish, such as HASL (Hot Air Solder Leveling) or ENIG (Electroless Nickel Immersion Gold), is applied to the exposed copper to protect it from oxidation and improve solderability.
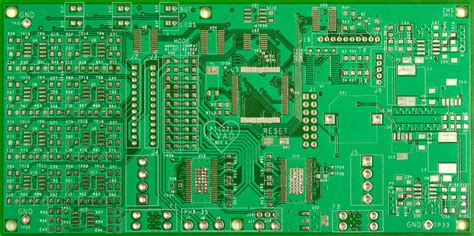
Designing Single-Layer PCBs
When designing a single-layer PCB, there are several best practices to follow:
- Component Placement: Place components in a logical and organized manner, minimizing the distance between connected components to reduce the amount of routing required.
- Routing: Route traces as directly as possible, avoiding sharp angles and minimizing trace lengths to reduce signal integrity issues. Use appropriate trace widths based on the current requirements of the circuit.
- Jumper Wires: When necessary, use jumper wires to complete connections that cannot be routed on the board itself. Keep jumper wires as short as possible and avoid crossing them over other traces or components.
- Ground Plane: If possible, include a ground plane on the component side of the board to improve signal integrity and reduce EMI. This can be achieved by using a large copper pour connected to the ground points of the circuit.
- Solder Mask and Silk Screen: Use solder mask and silk screen printing to protect the board and improve its appearance. Ensure that the solder mask openings are large enough to accommodate the component pads and that the silk screen markings are clear and accurate.
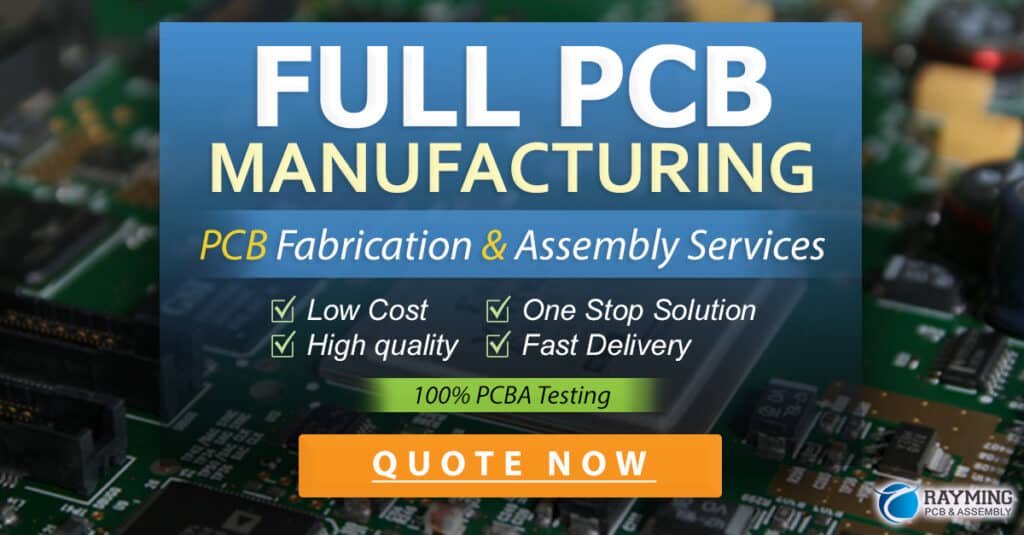
Single-Layer PCB Applications
Single-layer PCBs are suitable for a wide range of applications, including:
- Prototyping: Single-layer PCBs are often used for prototyping electronic projects due to their low cost and quick turnaround time.
- Low-complexity projects: Simple electronic projects, such as LED displays, basic sensors, and low-power microcontroller circuits, can often be implemented using single-layer PCBs.
- Educational purposes: Single-layer PCBs are an excellent choice for educational projects and workshops, as they allow students to learn about PCB design and assembly without the complexity of multi-layer boards.
- Hobby projects: Many hobbyists use single-layer PCBs for their personal projects, as they are easy to design and manufacture at home or through low-cost PCB fabrication services.
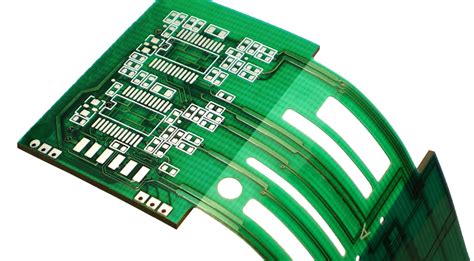
Frequently Asked Questions (FAQ)
-
What is the minimum trace width for a single-layer PCB?
The minimum trace width for a single-layer PCB depends on the PCB manufacturer’s capabilities and the current requirements of the circuit. Generally, a minimum trace width of 0.2mm (8 mil) is achievable for most PCB manufacturers, but it is always best to consult with the manufacturer for their specific guidelines. -
Can single-layer PCBs have through-hole components?
Yes, single-layer PCBs can have through-hole components. The component leads are inserted through drilled holes in the board and soldered on the opposite side. -
What is the maximum size of a single-layer PCB?
The maximum size of a single-layer PCB depends on the PCB manufacturer’s capabilities. Most manufacturers can produce single-layer PCBs up to 500mm x 500mm (19.7″ x 19.7″), but larger sizes may be available upon request. -
How much does a single-layer PCB cost?
The cost of a single-layer PCB varies depending on the size, quantity, and complexity of the design. Generally, single-layer PCBs are the most affordable type of PCB, with prices starting at around $5 per board for small quantities. -
Can single-layer PCBs be used for high-frequency applications?
Single-layer PCBs are not ideal for high-frequency applications due to their limited ability to control impedance and reduce crosstalk. For high-frequency applications, multi-layer PCBs with dedicated ground and power planes are recommended to ensure better signal integrity and reduced EMI.
Characteristic | Single-Layer PCB | Double-Layer PCB | Multi-Layer PCB |
---|---|---|---|
Layers | 1 | 2 | 4 or more |
Cost | Low | Medium | High |
Complexity | Low | Medium | High |
Density | Low | Medium | High |
Signal Integrity | Low | Medium | High |
Power Handling | Low | Medium | High |
Applications | Simple projects, prototypes, hobbyists | Medium-complexity projects, commercial products | High-complexity projects, advanced commercial products, high-frequency applications |
In conclusion, single-layer PCBs are an essential tool for anyone working with electronics. They offer a cost-effective and straightforward solution for low-complexity projects, prototyping, and educational purposes. By understanding the advantages, limitations, and best practices for designing single-layer PCBs, you can create reliable and functional electronic circuits for a wide range of applications.
No responses yet