What are Gold Fingers Used For?
Gold fingers are used in a wide range of applications, including:
- Printed Circuit Boards (PCBs)
- Expansion Cards
- Memory Modules
- SIM Cards
- USB Connectors
- Game Cartridges
Printed Circuit Boards (PCBs)
PCBs are the backbone of most eLectronic devices, and gold fingers are often used to connect these boards to other components or devices. The gold-plated contacts on the edge of the PCB allow for a secure and reliable connection, ensuring that electrical signals are transmitted efficiently between the board and other parts of the device.
Expansion Cards
Expansion cards, such as graphics cards, sound cards, and network cards, use gold fingers to connect to a computer’s motherboard. The gold-plated connectors on these cards fit into corresponding slots on the motherboard, allowing the card to communicate with the rest of the system.
Memory Modules
Memory modules, such as RAM sticks, also utilize gold fingers to connect to a computer’s motherboard. The gold-plated contacts on the bottom edge of the module insert into the memory slots on the motherboard, enabling the transfer of data between the memory and the processor.
SIM Cards
SIM cards, which are used in mobile phones to store user information and connect to cellular networks, have gold-plated contacts that allow them to communicate with the phone’s internal components. The gold fingers on the SIM card ensure a reliable connection and help prevent corrosion.
USB Connectors
USB connectors, which are used to connect various peripherals to computers and other devices, often feature gold-plated contacts. The gold fingers in USB connectors help to maintain a stable connection and resist wear and tear over time.
Game Cartridges
Many older gaming consoles, such as the Nintendo Entertainment System (NES) and Super Nintendo Entertainment System (SNES), used game cartridges with gold fingers. These gold-plated contacts allowed the cartridge to communicate with the console, enabling the game to load and play.
Advantages of Gold Fingers
Gold fingers offer several advantages over other types of electrical connectors:
- Corrosion Resistance
- High Conductivity
- Durability
- Low Contact Resistance
Corrosion Resistance
One of the primary reasons gold is used for plating connector fingers is its excellent resistance to corrosion. Gold does not readily react with other elements, which means that gold-plated connectors are less likely to deteriorate over time due to exposure to air, moisture, or other environmental factors.
High Conductivity
Gold is an excellent conductor of electricity, which makes it ideal for use in electrical connectors. The high conductivity of gold ensures that electrical signals can be transmitted efficiently between components without significant losses.
Durability
Gold-plated connectors are more durable than connectors made from other materials, such as tin or nickel. The hardness and wear resistance of gold help to protect the underlying metal from damage, ensuring a long-lasting and reliable connection.
Low Contact Resistance
Gold fingers have a low contact resistance, which means that they require less force to establish a connection. This low contact resistance also helps to minimize signal loss and ensure that electrical signals are transmitted efficiently between components.
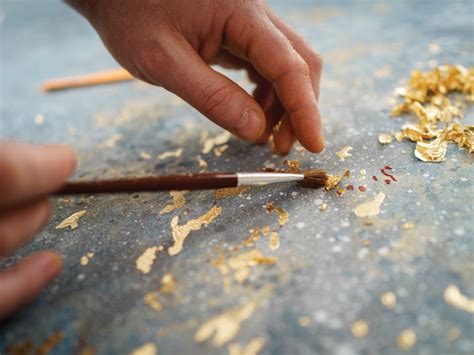
Manufacturing Process
The manufacturing process for gold fingers involves several steps:
- Base Metal Selection
- Plating Process
- Thickness Control
- Inspection and Testing
Base Metal Selection
The first step in manufacturing gold fingers is selecting the appropriate base metal. The base metal is typically copper or a copper alloy, chosen for its high conductivity and relatively low cost.
Plating Process
Once the base metal has been selected, it undergoes a plating process to apply the gold layer. The most common plating method is electroplating, which involves immersing the base metal in a gold solution and applying an electrical current. The current causes the gold ions in the solution to adhere to the base metal, forming a thin, even layer of gold on the surface.
Thickness Control
The thickness of the gold plating is carefully controlled during the manufacturing process to ensure optimal performance and cost-effectiveness. The typical thickness of gold plating on connector fingers ranges from 0.05 micrometers (μm) to 2.54 μm, depending on the specific application and requirements.
Inspection and Testing
After the plating process, the gold fingers undergo a series of inspections and tests to ensure that they meet the required specifications. These tests may include:
- Visual inspection for surface defects and plating uniformity
- Thickness measurement using X-ray fluorescence (XRF) or other methods
- Adhesion testing to ensure that the gold plating is securely bonded to the base metal
- Electrical resistance testing to verify low contact resistance and high conductivity
Gold Finger Specifications
There are several key specifications to consider when selecting gold fingers for a particular application:
- Thickness
- Purity
- Hardness
- Wear Resistance
Thickness
The thickness of the gold plating is an important consideration, as it affects both the performance and cost of the connector. Thicker gold plating offers better wear resistance and durability but also increases the overall cost of the component. The table below shows some common gold plating thicknesses and their typical applications:
Thickness (μm) | Application |
---|---|
0.05 – 0.10 | Low-cost, short-life applications |
0.25 – 0.50 | General-purpose applications |
1.00 – 1.50 | High-reliability applications |
2.00 – 2.54 | Extreme-durability applications |
Purity
The purity of the gold used in plating is another important factor. Higher purity gold offers better conductivity and corrosion resistance but also comes at a higher cost. The most common gold purity levels used in connector plating are:
- 99.9% (24 karat)
- 99.0% (23 karat)
- 90.0% (21.6 karat)
Hardness
The hardness of the gold plating is a measure of its resistance to indentation and deformation. Harder gold platings are more durable and wear-resistant but may be more brittle and prone to cracking. The hardness of gold plating is typically measured on the Knoop or Vickers scale.
Wear Resistance
Wear resistance is a critical factor in applications where the gold fingers will be subject to frequent insertion and removal cycles. Higher wear resistance ensures a longer service life and more reliable performance over time. Factors that influence wear resistance include the thickness and hardness of the gold plating, as well as the Surface Finish of the base metal.
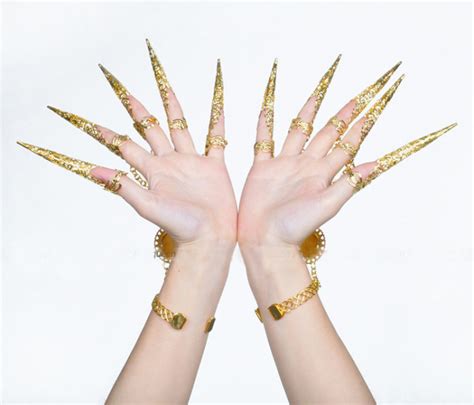
Alternatives to Gold Fingers
While gold fingers are widely used in various electronic applications, there are alternative materials and coatings that can be used in certain situations:
- Palladium-Nickel (Pd-Ni) Plating
- Selective Gold Plating
- Gold Flash Plating
Palladium-Nickel (Pd-Ni) Plating
Palladium-nickel (Pd-Ni) plating is an alternative to gold that offers similar performance characteristics at a lower cost. Pd-Ni plating provides good corrosion resistance, wear resistance, and electrical conductivity, making it suitable for many connector applications.
Selective Gold Plating
Selective gold plating involves applying gold only to specific areas of the connector, such as the contact fingers, rather than the entire surface. This approach reduces the overall cost of the component while still providing the benefits of gold plating where it is needed most.
Gold Flash Plating
Gold flash plating is an ultra-thin layer of gold, typically less than 0.05 μm thick, applied over a base metal. While gold flash plating does not offer the same level of durability and wear resistance as thicker gold platings, it can provide a cost-effective solution for applications with limited service life or low-stress environments.
Frequently Asked Questions (FAQ)
-
What is the purpose of gold fingers in electronics?
Gold fingers are used to establish reliable and efficient electrical connections between different components in electronic devices, such as PCBs, expansion cards, and memory modules. -
Why is gold used for plating connector fingers?
Gold is used for plating connector fingers because of its excellent corrosion resistance, high electrical conductivity, durability, and low contact resistance. -
What is the typical thickness of gold plating on connector fingers?
The typical thickness of gold plating on connector fingers ranges from 0.05 μm to 2.54 μm, depending on the specific application and requirements. -
Are there alternatives to gold fingers in electronic connectors?
Yes, alternatives to gold fingers include palladium-nickel (Pd-Ni) plating, selective gold plating, and gold flash plating. -
How does the purity of gold affect the performance of gold fingers?
Higher purity gold offers better conductivity and corrosion resistance, but also comes at a higher cost. The most common gold purity levels used in connector plating are 99.9% (24 karat), 99.0% (23 karat), and 90.0% (21.6 karat).
In conclusion, gold fingers play a crucial role in ensuring reliable and efficient electrical connections in a wide range of electronic devices. The gold-plated contacts provide excellent corrosion resistance, high conductivity, durability, and low contact resistance, making them an ideal choice for many applications. While there are alternatives to gold fingers, such as Pd-Ni plating and selective gold plating, gold remains the preferred material for high-performance connector applications.
No responses yet