Why Does PCB Color Matter?
The color of a PCB is not just a cosmetic choice; it can have a direct impact on the board’s performance and reliability. Here are some reasons why PCB color matters:
Reflection and Absorption of Light
Different colors of PCBs have varying levels of light reflection and absorption. This can be particularly important in applications where the PCB is exposed to light, such as in optical sensors or displays. The color of the PCB can affect the accuracy and sensitivity of these components.
Heat Dissipation
The color of a PCB can also influence its ability to dissipate heat. Darker colors, such as black, tend to absorb more heat, while lighter colors, like white, reflect more heat. This can be a crucial consideration in high-power applications where efficient heat dissipation is necessary to prevent component failure.
Aesthetics and Branding
In some cases, the color of a PCB may be chosen for purely aesthetic reasons. Many consumer electronics, such as smartphones and laptops, feature PCBs that are color-coordinated with the device’s overall design. Additionally, some companies may choose to use a specific PCB color as part of their branding strategy.
Common PCB Colors and Their Properties
There are several standard colors available for PCBs, each with its own unique properties and advantages. Here are some of the most common PCB colors and their characteristics:
Green
Green is the most widely used color for PCBs. It is the default color for most PCB manufacturers and is often the most cost-effective option. Green PCBs offer good contrast for white silkscreen legends, making them easy to read and inspect.
Black
Black PCBs are growing in popularity, particularly in consumer electronics. They offer a sleek, modern appearance and can help to hide proprietary circuit designs. Black PCBs also have excellent heat absorption properties, making them suitable for high-power applications. However, they can be more difficult to inspect and may require specialized lighting during the manufacturing process.
Red
Red PCBs are less common than green or black boards, but they offer some unique advantages. They provide excellent contrast for white silkscreen legends and are often used in applications where visual inspection is critical, such as in aerospace or military equipment.
Blue
Blue PCBs are relatively rare but can be used in certain applications where color-coding is important. They offer good contrast for white silkscreen legends and can help to distinguish different types of boards in a complex system.
White
White PCBs are becoming more popular in LED lighting applications. They offer excellent reflectivity, which can help to increase the efficiency and brightness of LED components. However, white PCBs can be more expensive than other colors and may require specialized manufacturing processes.
Color | Advantages | Disadvantages |
---|---|---|
Green | Cost-effective, good contrast for white legends | Limited heat dissipation |
Black | Sleek appearance, excellent heat absorption | Difficult to inspect, may require specialized lighting |
Red | Excellent contrast for white legends, suitable for critical visual inspection | Less common, may be more expensive |
Blue | Good contrast for white legends, useful for color-coding | Relatively rare, limited availability |
White | Excellent reflectivity for LED applications | More expensive, may require specialized manufacturing |
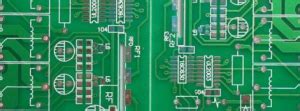
Factors to Consider When Choosing PCB Color
When selecting the color for your PCB, there are several factors to consider. These include:
Application Requirements
The specific requirements of your application should be the primary driver in choosing a PCB color. Consider factors such as light sensitivity, heat dissipation needs, and visual inspection requirements.
Manufacturing Capabilities
Not all PCB manufacturers offer the same range of color options. Before selecting a color, ensure that your chosen manufacturer can accommodate your request and that the color is compatible with their manufacturing processes.
Cost
The cost of a PCB can vary depending on the color chosen. Some colors, such as green, are generally more cost-effective than others, like white or black. Consider your budget constraints when selecting a PCB color.
Aesthetics and Branding
If your PCB will be visible in the final product, aesthetics and branding may play a role in your color choice. Select a color that complements your device’s overall design and aligns with your company’s branding guidelines.
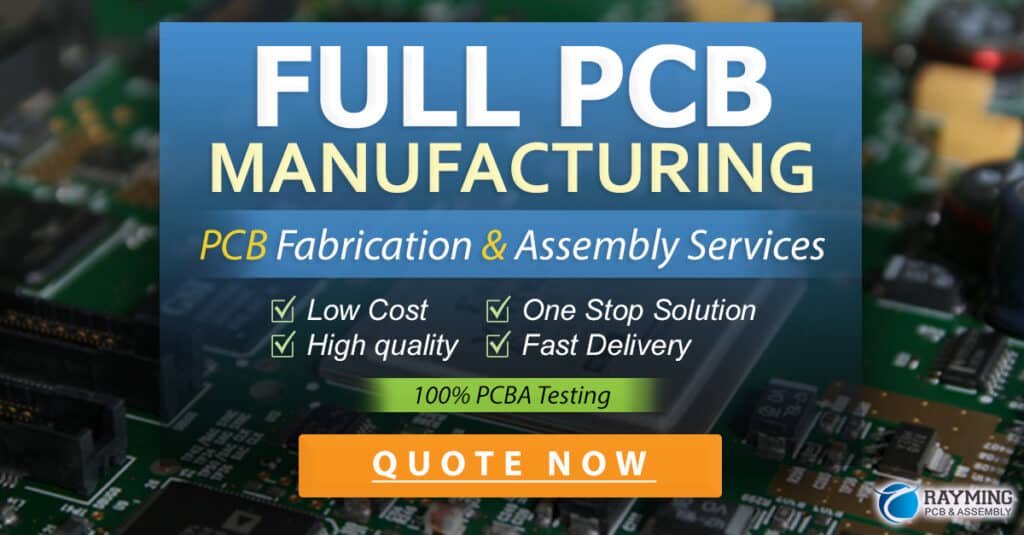
PCB Color and the Manufacturing Process
The color of a PCB can have a significant impact on the manufacturing process. Different colors may require specialized materials, equipment, or techniques, which can affect the overall cost and lead time of the board.
Solder Mask Color
The solder mask is a protective layer applied to the surface of the PCB to prevent short circuits and protect the copper traces from damage. The color of the solder mask is typically the same as the base color of the PCB. However, some manufacturers offer the option to use a different color solder mask for aesthetic or functional purposes.
Legend Color
The legend is the text and symbols printed on the surface of the PCB to identify components, connectors, and other features. The most common legend color is white, which provides good contrast against most PCB colors. However, some applications may require a different legend color for improved readability or to meet specific industry standards.
Specialized Manufacturing Techniques
Some PCB colors, such as black or white, may require specialized manufacturing techniques to achieve the desired appearance and functionality. For example, black PCBs may require a special oxide treatment to enhance their heat absorption properties, while white PCBs may need a special reflective coating to improve their efficiency in LED applications.
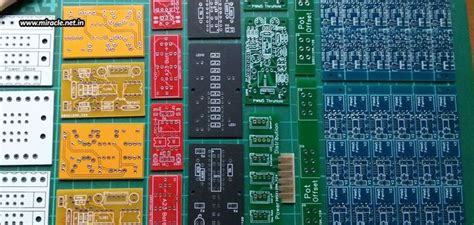
Frequently Asked Questions (FAQ)
1. Can I mix different colors on the same PCB?
Yes, it is possible to use multiple colors on a single PCB. This is often done to create visual contrast between different sections of the board or to color-code specific components or features. However, using multiple colors may increase the cost and complexity of the manufacturing process.
2. Are there any industry standards for PCB color?
There are no universal industry standards for PCB color. However, some industries may have specific color requirements for certain applications. For example, in the aerospace industry, red PCBs are often used for critical components that require frequent visual inspection.
3. How does PCB color affect the assembly process?
The color of a PCB can impact the assembly process in several ways. For example, darker colors like black may require specialized lighting to ensure accurate component placement, while lighter colors like white may reflect more light and improve visibility. Additionally, some colors may require different types of solder or fluxes to ensure proper bonding.
4. Can I change the color of an existing PCB design?
In most cases, changing the color of an existing PCB design is relatively straightforward. However, it is important to consult with your PCB manufacturer to ensure that the new color is compatible with their manufacturing processes and that any necessary adjustments to the design files are made.
5. Do different PCB colors have different lead times?
Lead times for PCBs can vary depending on the color chosen. Some colors, such as green, are more widely available and may have shorter lead times, while others, like black or white, may require specialized materials or processes that can increase lead times. Always check with your PCB manufacturer for specific lead time information based on your chosen color and other design requirements.
Conclusion
Selecting the right color for your PCB is an important decision that can have a significant impact on the board’s performance, reliability, and overall cost. By understanding the available color options, their properties, and the factors to consider when making your choice, you can ensure that your PCB meets the specific needs of your application while also optimizing the manufacturing process.
Remember to consult with your PCB manufacturer early in the design process to discuss your color requirements and ensure that they can accommodate your needs. With careful consideration and planning, you can create a PCB that not only functions flawlessly but also looks great and aligns with your brand identity.
No responses yet