Introduction to Automated Medical Manufacturing
Automated medical manufacturing is transforming the way medical devices and components are produced. By leveraging advanced technologies like robotics, artificial intelligence, and machine learning, automated manufacturing systems enable faster, more precise, and more cost-effective production of critical medical products. This article will explore the benefits, applications, and future outlook for automated medical manufacturing.
Key Benefits of Automated Medical Manufacturing
There are several compelling advantages to automating medical manufacturing processes:
1. Increased Efficiency and Productivity
Automated systems can operate 24/7 with minimal downtime, significantly increasing output compared to manual production methods. Robotics and computer-controlled equipment execute manufacturing tasks with speed and precision. This boosts overall productivity and allows medical device companies to scale up production to meet rising demand.
2. Enhanced Precision and Quality Control
Medical devices and components often have extremely tight tolerances and stringent quality requirements. Automated manufacturing excels at consistently producing parts to exact specifications, reducing errors, defects and variations between batches. Advanced vision systems, sensors and AI algorithms can inspect parts in real-time to identify any quality issues. This level of accuracy and reliability is essential for safety-critical medical products.
3. Cost Savings
While there are upfront costs to implementing automated manufacturing solutions, the long-term savings can be substantial. Automated systems reduce labor costs, minimize material waste, improve yield rates, and can operate more efficiently in terms of energy consumption. Streamlined, optimized automated processes ultimately lower the cost-per-unit and boost profitability.
4. Flexibility and Quick Changeovers
Modern automated manufacturing systems are designed for flexibility. Modular equipment and robotics can be quickly reconfigured and reprogrammed to switch between different products and handle shorter production runs. This agility allows manufacturers to keep pace with evolving product designs and dynamic market demands.
5. Improved Worker Safety
Many medical manufacturing processes involve hazardous materials, repetitive motions, and other occupational risks for workers. Automating these tasks with robotics takes human operators out of harm’s way, reducing workplace accidents and injuries. Automated systems can handle dangerous substances and perform strenuous activities that could cause strain for human workers.
Applications of Automation in Medical Manufacturing
Automation is being applied across a wide range of medical manufacturing operations, such as:
Process | Description |
---|---|
CNC Machining | Computer numerical control (CNC) machines automatically cut, drill, and shape raw materials into precise components based on digital CAD models. |
Injection Molding | Automated injection molding machines melt and inject plastic into molds to mass-produce parts like housings, connectors, and disposable items. |
3D Printing | Additive manufacturing systems automatically fabricate complex geometries directly from digital files, enabling rapid prototyping and production of patient-specific implants. |
Electronics Assembly | Surface-mount technology (SMT) machines automatically place and solder electronic components onto printed circuit boards (PCBs) for medical diagnostic and monitoring devices. |
Welding & Joining | Laser welding and automated adhesive application systems bond plastics and metals together to create assembled products while providing strong, sterile seals. |
Inspection & Testing | Machine vision cameras and sensors integrated with AI software can automatically verify the dimensions, appearance, and performance of medical components inline during production. |
Packaging & Labeling | Automated packaging lines fill, seal, and label products using high-speed equipment, with serialization and traceability codes printed and verified for compliance. |
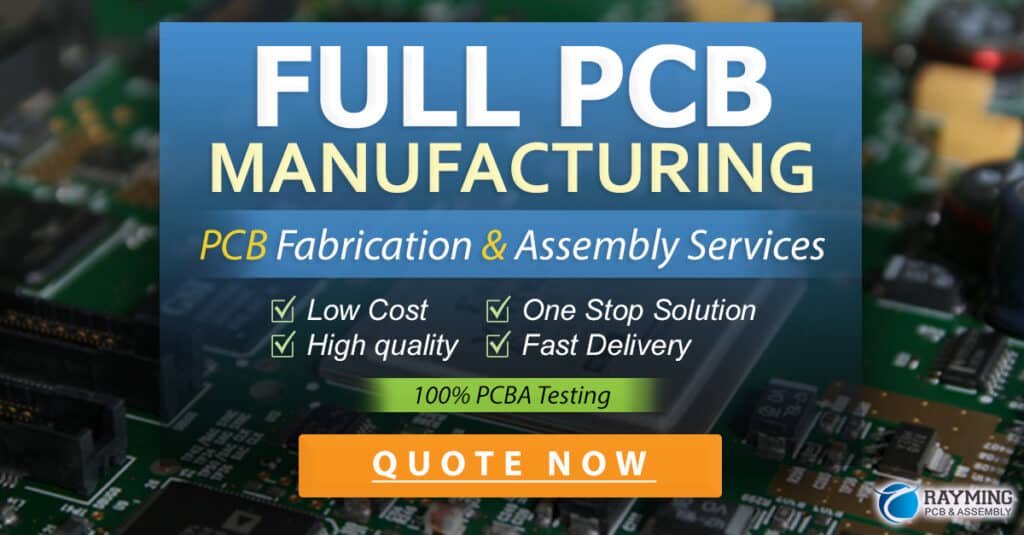
Implementing Automated Manufacturing Systems
Transitioning to an automated manufacturing environment requires careful planning and execution. Key steps include:
- Assess current processes and identify opportunities for automation
- Develop a phased implementation roadmap aligned with business objectives
- Engage with an experienced automation solution provider
- Design and simulate the automated system, incorporating safety and ergonomics
- Procure and install equipment, including any facility modifications
- Perform rigorous testing and validation
- Train personnel on operating and maintaining the new system
- Continuously monitor performance and optimize over time
Partnering with the right automation expert is crucial for success. Look for a provider that understands the unique requirements of the medical industry and has a proven track record of delivering compliant, validated automation solutions.
Ensuring Compliance and Validation
Medical manufacturing is heavily regulated to ensure the safety and efficacy of products. Automated systems must be designed, implemented, and documented in accordance with applicable regulations and standards, such as:
- FDA 21 CFR Part 820 Quality System Regulation
- ISO 13485 Medical Device Quality Management Systems
- IEC 62304 Medical Device Software Lifecycle Processes
- ISO 14971 Risk Management for Medical Devices
Validation is the process of establishing documented evidence that an automated system consistently produces a result or product meeting its predetermined specifications and quality attributes. Validation activities may include:
Validation Activity | Description |
---|---|
Design Qualification (DQ) | Verifying that the proposed design of the automated system meets all specified requirements. |
Installation Qualification (IQ) | Confirming that the equipment is installed correctly and safely per the manufacturer’s instructions and design specifications. |
Operational Qualification (OQ) | Demonstrating that the system operates as intended throughout all anticipated operating ranges. |
Performance Qualification (PQ) | Proving that the automated system consistently produces an acceptable product under normal operating conditions. |
A comprehensive validation strategy should be established early in the project, with all validation activities and documentation managed within a quality system. Engaging with a knowledgeable validation partner can streamline the process and ensure all regulatory expectations are met.
The Future of Automated Medical Manufacturing
As technology continues to advance, the future of automated medical manufacturing looks increasingly promising. Some key trends and developments to watch include:
Artificial Intelligence and Machine Learning
AI and ML algorithms will become more integrated into automated systems, enabling real-time process optimization, predictive maintenance, and adaptive control. AI-powered quality inspection systems will detect defects with even greater accuracy, while generative design tools will help optimize part geometries and production efficiency.
Collaborative Robotics
The use of collaborative robots (cobots) that can safely work alongside human operators will expand. Cobots will take on more complex and delicate tasks, such as intricate assembly operations and even surgical procedures.
Additive Manufacturing
3D printing technologies will continue to mature and see greater adoption for production parts. Metal 3D printing will allow intricate, high-strength components to be produced on-demand. Bioprinting will enable fabrication of living tissues and organs, revolutionizing regenerative medicine.
Internet of Things (IoT) and Industry 4.0
The Internet of Things will further connect automated manufacturing equipment, allowing for seamless data exchange and remote monitoring. Advanced sensors and analytics will provide real-time visibility into production metrics and enable predictive quality and maintenance approaches. This enhanced connectivity and data utilization aligns with the principles of Industry 4.0 smart manufacturing.
Personalized Medicine Manufacturing
Automated manufacturing will play a pivotal role in enabling mass customization of medical products, such as patient-specific implants, prosthetics, and drug formulations. Digital workflows and automated production lines will allow cost-effective manufacturing of bespoke medical solutions at scale.
Frequently Asked Questions (FAQ)
1. What types of medical products can be manufactured using automation?
Automation can be applied to a wide variety of medical products, including:
– Implantable devices (e.g., orthopedic implants, pacemakers, stents)
– Surgical instruments and tools
– Diagnostic equipment and testing kits
– Disposable items (e.g., syringes, catheters, tubing)
– Prosthetics and orthotics
– Medical electronics and wearable devices
– Pharmaceutical packaging and delivery systems
2. How does automated manufacturing impact product quality?
Automated manufacturing systems are designed to produce parts with exceptional precision, consistency, and reliability. By removing human error and variability from the process, automation helps ensure that every product meets the same high-quality standards. Advanced sensors and vision systems can continuously monitor the process and detect any deviations or defects in real-time, enabling quick corrective action. This level of quality control is essential for medical products where patient safety is paramount.
3. Is automated manufacturing cost-effective for low-volume or high-mix production?
Traditionally, automation was best suited for high-volume, low-mix production. However, advancements in flexible and modular automation technologies have made it increasingly viable for lower-volume and higher-mix scenarios. Robotics and CNC equipment can be quickly reconfigured and reprogrammed to handle different parts and processes. Additive manufacturing technologies like 3D printing are also enabling cost-effective production of complex, low-volume components. While the specific cost-benefit analysis will vary depending on the product and production requirements, automation is becoming a more attractive option for a wider range of medical manufacturing applications.
4. How long does it take to implement an automated manufacturing system?
The timeline for implementing an automated manufacturing system can vary widely depending on the complexity of the process, the level of customization required, and the regulatory requirements involved. A simple, off-the-shelf automation solution may be deployed in a matter of weeks, while a highly complex, custom-engineered system may take several months to a year or more to fully design, build, and validate. It’s important to work with an experienced automation partner who can help develop a realistic project timeline and manage the various stages of the implementation process.
5. What are the key challenges in validating automated medical manufacturing systems?
Validating automated manufacturing systems for medical products can be a complex and time-consuming process. Key challenges include:
- Defining and documenting all system requirements and specifications
- Designing and executing comprehensive validation protocols and test cases
- Collecting and analyzing large amounts of data to demonstrate consistent performance
- Ensuring the system is robust and reliable enough to withstand real-world manufacturing conditions
- Maintaining compliance with evolving regulatory standards and guidelines
- Managing the validation process within the broader product development timeline and budget
To overcome these challenges, it’s critical to engage with a validation partner who has deep expertise in the medical industry and a proven track record of successful automation projects. A well-planned and executed validation strategy can help streamline the process, minimize delays, and ensure a compliant and efficient automated manufacturing system.
Conclusion
Automated medical manufacturing is revolutionizing the way medical devices and components are produced, offering significant benefits in terms of efficiency, quality, cost, and safety. As technologies like robotics, AI, and 3D printing continue to advance, the potential applications for automation in the medical industry will only expand. However, implementing automated systems requires careful planning, execution, and compliance with strict regulatory requirements. By partnering with an experienced automation solution provider, medical device manufacturers can successfully navigate the challenges and unlock the full value of automated production. As we look to the future, automated manufacturing will undoubtedly play a vital role in enabling the next generation of medical innovations and personalized healthcare solutions.
No responses yet