Introduction to Customized adhesives in Medical Electronics
The medical electronics industry is rapidly evolving, with new technologies and devices being developed to improve patient care and outcomes. One critical component of these devices is the adhesive used to bond various materials together. Customized adhesives play a crucial role in ensuring the reliability, durability, and performance of medical electronic devices.
Adhesives used in medical electronics must meet stringent requirements, including biocompatibility, chemical resistance, and the ability to withstand sterilization processes. They must also provide strong and reliable bonds to a wide range of substrates, including plastics, metals, and ceramics. Customized adhesives are designed to meet these specific requirements, offering tailored solutions for various medical electronic applications.
The Importance of Customized Adhesives in Medical Electronics
Customized adhesives are essential in medical electronics for several reasons:
-
Biocompatibility: Medical devices that come into contact with the human body must be made from materials that are safe and non-toxic. Customized adhesives can be formulated to meet biocompatibility standards, ensuring that they do not cause adverse reactions or harm to patients.
-
Reliability: Medical electronic devices must function reliably and consistently, even in challenging environments. Customized adhesives can provide strong and durable bonds that can withstand the rigors of use, including exposure to moisture, chemicals, and temperature fluctuations.
-
Performance: Customized adhesives can be engineered to provide specific performance characteristics, such as electrical conductivity, thermal conductivity, or optical clarity. These properties can be critical in certain medical electronic applications, such as sensors, displays, or imaging devices.
-
Sterilization compatibility: Medical devices often require sterilization to prevent the spread of infection. Customized adhesives can be formulated to withstand various sterilization methods, such as autoclaving, gamma irradiation, or ethylene oxide sterilization.
Types of Customized Adhesives Used in Medical Electronics
There are several types of customized adhesives used in medical electronics, each with its own unique properties and advantages. Some of the most common types include:
Epoxy Adhesives
Epoxy adhesives are widely used in medical electronics due to their excellent strength, durability, and chemical resistance. They consist of a resin and a hardener that, when mixed together, create a strong and permanent bond. Epoxy adhesives can be customized to provide specific properties, such as high thermal conductivity or low outgassing.
Property | Description |
---|---|
Strength | High shear and tensile strength |
Durability | Resistant to moisture, chemicals, and temperature fluctuations |
Chemical Resistance | Excellent resistance to a wide range of chemicals |
Customization | Can be formulated for specific properties, such as thermal conductivity or low outgassing |
Silicone Adhesives
Silicone adhesives are another popular choice for medical electronics due to their excellent biocompatibility, flexibility, and stability. They are often used in applications where a soft, flexible bond is required, such as in wearable devices or implantable sensors. Silicone adhesives can be customized to provide specific properties, such as high tear strength or low compression set.
Property | Description |
---|---|
Biocompatibility | Non-toxic and safe for use in medical applications |
Flexibility | Can provide a soft, flexible bond |
Stability | Resistant to moisture, UV light, and extreme temperatures |
Customization | Can be formulated for specific properties, such as high tear strength or low compression set |
Polyurethane Adhesives
Polyurethane adhesives offer a combination of strength, flexibility, and durability, making them suitable for a wide range of medical electronic applications. They can bond to various substrates, including plastics, metals, and fabrics, and can withstand exposure to moisture, chemicals, and temperature fluctuations. Polyurethane adhesives can be customized to provide specific properties, such as high elongation or low modulus.
Property | Description |
---|---|
Strength | Good shear and tensile strength |
Flexibility | Can provide a flexible bond |
Durability | Resistant to moisture, chemicals, and temperature fluctuations |
Substrate Compatibility | Can bond to various substrates, including plastics, metals, and fabrics |
Customization | Can be formulated for specific properties, such as high elongation or low modulus |
UV-Curable Adhesives
UV-curable adhesives offer fast curing times and high strength, making them ideal for high-volume production of medical electronic devices. They consist of a liquid resin that cures rapidly when exposed to UV light, forming a strong and durable bond. UV-curable adhesives can be customized to provide specific properties, such as high optical clarity or low shrinkage.
Property | Description |
---|---|
Fast Curing | Cures rapidly when exposed to UV light |
High Strength | Provides a strong and durable bond |
Production Efficiency | Ideal for high-volume production |
Customization | Can be formulated for specific properties, such as high optical clarity or low shrinkage |
Factors to Consider When Selecting Customized Adhesives for Medical Electronics
When selecting customized adhesives for medical electronic applications, several key factors must be considered to ensure optimal performance and reliability:
Biocompatibility
Adhesives used in medical devices that come into contact with the human body must be biocompatible, meaning they must not cause adverse reactions or harm to patients. Adhesive manufacturers can provide biocompatibility testing data to demonstrate that their products meet the necessary standards, such as ISO 10993.
Sterilization Compatibility
Medical devices often require sterilization to prevent the spread of infection. The adhesive used in these devices must be able to withstand the sterilization process without degrading or losing its bonding properties. Different sterilization methods, such as autoclaving, gamma irradiation, or ethylene oxide sterilization, can have varying effects on adhesives, so it is essential to select an adhesive that is compatible with the intended sterilization method.
Substrate Compatibility
Medical electronic devices can be made from a wide range of materials, including plastics, metals, ceramics, and composites. The adhesive selected must be able to bond effectively to the specific substrates used in the device. Adhesive manufacturers can provide data on the bond strength and durability of their products on various substrates to help guide the selection process.
Performance Requirements
Customized adhesives can be engineered to provide specific performance characteristics, such as electrical conductivity, thermal conductivity, or optical clarity. These properties can be critical in certain medical electronic applications, such as sensors, displays, or imaging devices. It is essential to clearly define the performance requirements of the adhesive and work with the manufacturer to develop a customized formulation that meets those needs.
Processing and Curing Requirements
The processing and curing requirements of the adhesive must be compatible with the manufacturing process for the medical electronic device. Factors to consider include the viscosity of the adhesive, the curing time and temperature, and the equipment required for dispensing and curing the adhesive. Adhesive manufacturers can provide guidance on the processing and curing requirements of their products to ensure a smooth and efficient manufacturing process.
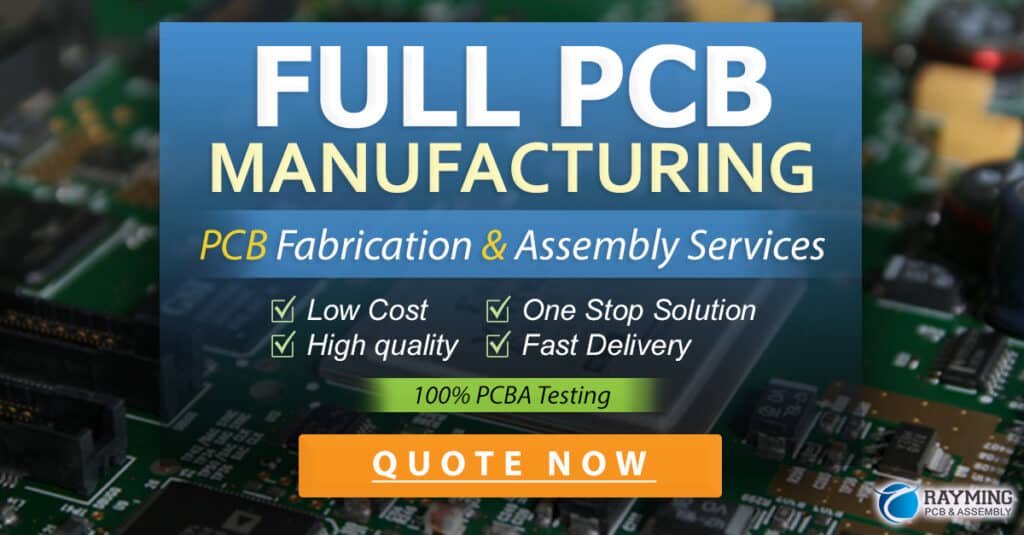
Case Studies: Customized Adhesives in Action
To better understand the role of customized adhesives in medical electronics, let’s look at a few real-world examples:
Case Study 1: Wearable Glucose Monitoring Device
A manufacturer of wearable glucose monitoring devices needed a biocompatible adhesive that could bond the device’s sensor to the patient’s skin for extended periods. The adhesive needed to be gentle on the skin, yet strong enough to maintain the bond through normal daily activities, including showering and exercise.
The solution was a customized silicone adhesive that was formulated to provide a soft, flexible bond with excellent adhesion to both the sensor material and human skin. The adhesive was also designed to be breathable, allowing moisture to escape and preventing skin irritation. The result was a reliable and comfortable wearable device that could be worn for up to 14 days at a time.
Case Study 2: Implantable Cardiac Pacemaker
An implantable cardiac pacemaker required a reliable and durable adhesive to bond the device’s electronic components to its titanium casing. The adhesive needed to withstand the harsh environment inside the human body, including exposure to bodily fluids and constant motion.
The manufacturer worked with an adhesive supplier to develop a customized epoxy adhesive that could meet these challenging requirements. The adhesive was formulated to provide excellent adhesion to both the electronic components and the titanium casing, as well as high resistance to moisture and chemicals. The adhesive was also designed to have a low ionic content to minimize the risk of corrosion.
The customized epoxy adhesive enabled the manufacturer to produce a reliable and long-lasting implantable cardiac pacemaker that could improve the quality of life for patients with heart conditions.
Case Study 3: Disposable Medical Sensors
A manufacturer of disposable medical sensors needed an adhesive that could bond the sensor’s conductive traces to its plastic substrate. The adhesive needed to provide excellent electrical conductivity, while also being compatible with the high-volume production process used to manufacture the sensors.
The solution was a customized UV-curable adhesive that was formulated to provide high electrical conductivity and fast curing times. The adhesive was designed to be easily dispensed using automated equipment and to cure rapidly when exposed to UV light, enabling high-volume production of the sensors.
The customized UV-curable adhesive allowed the manufacturer to produce high-quality disposable medical sensors efficiently and cost-effectively.
Frequently Asked Questions (FAQ)
-
Q: What is a customized adhesive?
A: A customized adhesive is an adhesive that is specifically formulated to meet the unique requirements of a particular application. Customized adhesives can be engineered to provide specific properties, such as biocompatibility, chemical resistance, or electrical conductivity, depending on the needs of the application. -
Q: Why are customized adhesives important in medical electronics?
A: Customized adhesives are important in medical electronics because they can be engineered to meet the strict requirements of medical devices, including biocompatibility, sterilization compatibility, and reliability. They can also provide specific performance characteristics that are critical in certain medical electronic applications, such as sensors, displays, or imaging devices. -
Q: What are some common types of customized adhesives used in medical electronics?
A: Some common types of customized adhesives used in medical electronics include epoxy adhesives, silicone adhesives, polyurethane adhesives, and UV-curable adhesives. Each type of adhesive has its own unique properties and advantages, and can be customized to meet specific application requirements. -
Q: How do I select the right customized adhesive for my medical electronic application?
A: When selecting a customized adhesive for a medical electronic application, several key factors must be considered, including biocompatibility, sterilization compatibility, substrate compatibility, performance requirements, and processing and curing requirements. It is important to work closely with an experienced adhesive manufacturer to develop a customized formulation that meets the specific needs of the application. -
Q: Can customized adhesives be used in implantable medical devices?
A: Yes, customized adhesives can be used in implantable medical devices, such as pacemakers, cochlear implants, and drug delivery systems. However, these adhesives must meet even stricter requirements for biocompatibility, durability, and reliability, as they will be exposed to the harsh environment inside the human body for extended periods. Specialized testing and regulatory approvals may be required for adhesives used in implantable devices.
Conclusion
Customized adhesives play a critical role in the development and manufacture of medical electronic devices. They offer tailored solutions to meet the unique requirements of these devices, including biocompatibility, reliability, performance, and sterilization compatibility. By working closely with experienced adhesive manufacturers, medical device companies can develop customized adhesives that enable them to produce innovative and high-quality products that improve patient care and outcomes.
As the medical electronics industry continues to evolve, the demand for customized adhesives will only continue to grow. Adhesive manufacturers that can provide expertise, innovation, and customization will be well-positioned to support the development of the next generation of medical electronic devices.
No responses yet