The Importance of Custom Medical Electronic Design and Manufacturing
Addressing Unique Medical Challenges
Custom medical electronic design and manufacturing allows healthcare providers and medical device companies to tackle unique medical challenges head-on. By developing specialized devices and systems, MedTech“>MedTech professionals can cater to specific patient needs, rare diseases, or niche medical applications that may not be adequately addressed by off-the-shelf solutions.
Enhancing Patient Outcomes
Tailored medical electronic devices and systems can significantly improve patient outcomes by providing more accurate diagnoses, targeted treatments, and personalized monitoring. Custom solutions can integrate advanced sensors, data analytics, and connectivity features to enable real-time monitoring, remote patient management, and data-driven decision-making, ultimately leading to better patient care.
Driving Innovation in Healthcare
Custom medical electronic design and manufacturing serves as a catalyst for innovation in the healthcare industry. By pushing the boundaries of technology and exploring novel approaches to medical challenges, MedTech professionals contribute to the development of groundbreaking medical devices, diagnostic tools, and treatment methods. This drive for innovation fuels continuous advancements in healthcare delivery and patient care.
The Custom Medical Electronic Design and Manufacturing Process
Concept Development and Feasibility Assessment
The custom medical electronic design and manufacturing process begins with concept development, where healthcare providers or medical device companies identify a specific medical need or challenge. This stage involves brainstorming ideas, researching existing solutions, and assessing the feasibility of developing a custom device or system.
Requirements Gathering and Specification Definition
Once a concept is deemed feasible, the next step is to gather detailed requirements and define specifications for the custom medical electronic device or system. This involves collaborating with healthcare professionals, patients, and other stakeholders to understand their needs, preferences, and constraints. The requirements and specifications serve as a roadmap for the design and development process.
Design and Prototyping
With the requirements and specifications in place, the design phase commences. This stage involves creating detailed schematics, 3D models, and prototypes of the custom medical electronic device or system. Engineers and designers work closely together to ensure that the device meets the specified requirements while optimizing its functionality, usability, and manufacturability.
Regulatory Compliance and Certification
Medical electronic devices and systems must comply with stringent regulatory requirements to ensure patient safety and effectiveness. Custom medical electronic design and manufacturing processes must adhere to relevant regulations, such as those set by the FDA (Food and Drug Administration) in the United States or the European Medical Device Regulation (MDR) in Europe. This involves conducting thorough testing, risk assessments, and documentation to demonstrate compliance and obtain necessary certifications.
Manufacturing and Quality Assurance
Once the design is finalized and regulatory compliance is achieved, the custom medical electronic device or system enters the manufacturing phase. This stage involves setting up production lines, sourcing components, and implementing quality control processes to ensure consistent and reliable manufacturing. Rigorous testing and quality assurance procedures are employed to guarantee that each device meets the required specifications and performance standards.
Post-Market Surveillance and Maintenance
After the custom medical electronic device or system is deployed in the market, ongoing post-market surveillance and maintenance are crucial. This involves monitoring the device’s performance, gathering user feedback, and addressing any issues or adverse events that may arise. Regular software updates, device calibration, and preventive maintenance ensure the longevity and optimal performance of the custom medical electronic solution.
Challenges in Custom Medical Electronic Design and Manufacturing
Regulatory Complexities
Navigating the complex regulatory landscape is one of the major challenges in custom medical electronic design and manufacturing. The ever-evolving nature of medical device regulations, coupled with regional variations, requires MedTech professionals to stay up-to-date with the latest requirements and guidelines. Ensuring compliance throughout the design and manufacturing process can be time-consuming and resource-intensive.
Balancing Innovation and Safety
Custom medical electronic design and manufacturing often involves pushing the boundaries of technology to develop innovative solutions. However, this drive for innovation must be balanced with the paramount importance of patient safety. MedTech professionals must carefully assess the risks and benefits of new technologies, materials, or approaches, and implement robust safety measures to mitigate any potential hazards.
Integration with Existing Healthcare Systems
Custom medical electronic devices and systems must seamlessly integrate with existing healthcare infrastructure, including electronic health records (EHRs), hospital information systems (HIS), and other medical devices. Ensuring interoperability and data exchange between custom solutions and established systems can be challenging, requiring close collaboration with healthcare providers and IT teams.
Cost and Time Constraints
Developing custom medical electronic solutions can be costly and time-consuming compared to off-the-shelf alternatives. The need for specialized expertise, rigorous testing, and regulatory compliance adds to the overall expenses and development timelines. Balancing cost-effectiveness and timely delivery while maintaining the highest quality standards is a significant challenge for MedTech companies.
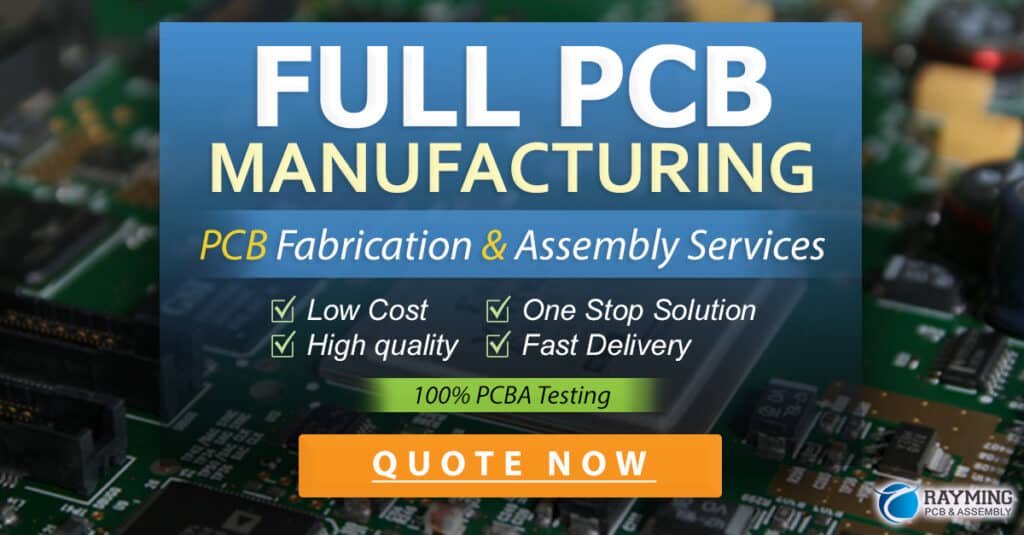
Future Trends in Custom Medical Electronic Design and Manufacturing
Internet of Medical Things (IoMT)
The Internet of Medical Things (IoMT) is a rapidly growing trend in custom medical electronic design and manufacturing. IoMT involves the integration of connected devices, sensors, and software to enable seamless data exchange and remote monitoring of patients. Custom medical electronic solutions that leverage IoMT technologies can improve patient engagement, enable personalized care, and facilitate remote disease management.
Artificial Intelligence and Machine Learning
Artificial intelligence (AI) and machine learning (ML) are increasingly being incorporated into custom medical electronic devices and systems. AI and ML algorithms can analyze vast amounts of medical data, assist in diagnostic decision-making, and predict patient outcomes. Custom medical electronic solutions that harness the power of AI and ML have the potential to revolutionize healthcare delivery, improve accuracy, and optimize resource allocation.
Wearable and Implantable Devices
Wearable and implantable medical devices are gaining traction in custom medical electronic design and manufacturing. These devices provide continuous monitoring, real-time data collection, and targeted therapy delivery. Custom wearable and implantable solutions can enhance patient comfort, enable remote monitoring, and improve treatment adherence. As technology advances, the integration of wearable and implantable devices with custom medical electronic systems will become more prevalent.
3D Printing and Personalized Medicine
3D printing technology is transforming custom medical electronic design and manufacturing by enabling the creation of personalized medical devices and implants. Custom 3D-printed devices can be tailored to individual patient anatomy, improving fit, comfort, and functionality. Additionally, 3D printing allows for rapid prototyping and iterative design, accelerating the development process of custom medical electronic solutions.
Frequently Asked Questions (FAQ)
1. What is the role of custom medical electronic design and manufacturing in MedTech?
Custom medical electronic design and manufacturing plays a crucial role in MedTech by enabling the development of tailored solutions to address specific medical challenges. It allows healthcare providers and medical device companies to tackle unique patient needs, rare diseases, or niche medical applications that may not be adequately addressed by off-the-shelf solutions.
2. How does custom medical electronic design and manufacturing differ from standard medical device development?
Custom medical electronic design and manufacturing focuses on creating specialized devices and systems tailored to specific medical needs or challenges. It involves close collaboration with healthcare professionals, patients, and other stakeholders to gather detailed requirements and define specifications. In contrast, standard medical device development often relies on more generic, off-the-shelf solutions that cater to a broader market.
3. What are the key steps involved in the custom medical electronic design and manufacturing process?
The custom medical electronic design and manufacturing process typically involves the following key steps:
1. Concept development and feasibility assessment
2. Requirements gathering and specification definition
3. Design and prototyping
4. Regulatory compliance and certification
5. Manufacturing and quality assurance
6. Post-market surveillance and maintenance
4. What are the main challenges faced in custom medical electronic design and manufacturing?
The main challenges faced in custom medical electronic design and manufacturing include:
1. Regulatory complexities
2. Balancing innovation and safety
3. Integration with existing healthcare systems
4. Cost and time constraints
5. How are emerging technologies like AI, IoMT, and 3D printing shaping the future of custom medical electronic design and manufacturing?
Emerging technologies such as AI, IoMT, and 3D printing are significantly influencing the future of custom medical electronic design and manufacturing. AI and machine learning enable advanced data analysis, diagnostic decision support, and predictive analytics. IoMT facilitates seamless data exchange, remote monitoring, and personalized care. 3D printing allows for the creation of personalized medical devices and implants tailored to individual patient anatomy. These technologies are driving innovation, improving patient outcomes, and transforming healthcare delivery in the realm of custom medical electronic solutions.
Technology | Impact on Custom Medical Electronic Design and Manufacturing |
---|---|
AI and Machine Learning | – Advanced data analysis – Diagnostic decision support – Predictive analytics |
Internet of Medical Things (IoMT) | – Seamless data exchange – Remote monitoring – Personalized care |
3D Printing | – Personalized medical devices and implants – Rapid prototyping – Iterative design |
Conclusion
Custom medical electronic design and manufacturing is a vital component of the MedTech industry, driving innovation, improving patient outcomes, and addressing unique medical challenges. By leveraging advanced technologies, collaborating closely with healthcare stakeholders, and adhering to rigorous regulatory standards, MedTech professionals can develop tailored solutions that revolutionize healthcare delivery.
As the healthcare landscape continues to evolve, custom medical electronic design and manufacturing will play an increasingly crucial role in shaping the future of medical devices and systems. The integration of emerging technologies such as AI, IoMT, and 3D printing will further accelerate innovation and personalization in custom medical electronic solutions.
However, navigating the complexities of regulatory compliance, balancing innovation with patient safety, and overcoming cost and time constraints remain significant challenges. MedTech companies must adapt to the changing regulatory landscape, invest in robust quality assurance processes, and foster close collaboration with healthcare providers and patients to ensure the success of custom medical electronic design and manufacturing endeavors.
Despite the challenges, the potential benefits of custom medical electronic design and manufacturing are immense. By enabling personalized care, improving diagnostic accuracy, and optimizing treatment outcomes, custom medical electronic solutions have the power to transform lives and revolutionize the healthcare industry.
As we look to the future, it is clear that custom medical electronic design and manufacturing will continue to be at the forefront of MedTech innovation. By embracing emerging technologies, fostering collaboration, and prioritizing patient needs, MedTech professionals can unlock new possibilities and shape a healthier, more personalized future for healthcare delivery.
No responses yet