What is IoT in Manufacturing?
IoT in manufacturing refers to the integration of connected devices, sensors, and software into the production process. These connected devices collect and exchange data in real-time, allowing manufacturers to monitor, control, and optimize their operations. IoT enables manufacturers to create smart factories where machines, devices, and systems are interconnected and can communicate with each other.
Benefits of IoT in Manufacturing
1. Increased Efficiency and Productivity
IoT in manufacturing can significantly increase efficiency and productivity by automating processes, reducing downtime, and optimizing resource utilization. Connected devices and sensors can monitor machine performance in real-time, predicting maintenance needs and preventing breakdowns. This reduces unplanned downtime and increases overall equipment effectiveness (OEE).
Benefit | Description |
---|---|
Automated processes | IoT enables the automation of repetitive tasks, reducing human error and increasing speed. |
Reduced downtime | Predictive maintenance using IoT sensors helps prevent machine breakdowns and reduces unplanned downtime. |
Optimized resource utilization | Real-time data from IoT devices allows manufacturers to optimize resource allocation and minimize waste. |
2. Enhanced Quality Control
IoT sensors can monitor product quality throughout the manufacturing process, detecting defects and anomalies in real-time. This allows manufacturers to identify and address quality issues early, reducing scrap and rework. IoT-enabled quality control systems can also provide traceability, enabling manufacturers to track products from raw materials to finished goods.
3. Improved Supply Chain Management
IoT can revolutionize supply chain management by providing real-time visibility into inventory levels, shipment tracking, and demand forecasting. Connected devices can monitor inventory levels and automate replenishment orders, reducing stockouts and overstocking. IoT-enabled tracking systems can provide end-to-end visibility of shipments, allowing manufacturers to optimize routes and improve delivery times.
4. Predictive Maintenance
Predictive maintenance is one of the most significant benefits of IoT in manufacturing. By using sensors to monitor machine health and performance, manufacturers can predict when maintenance is needed before a breakdown occurs. This reduces unplanned downtime, extends equipment lifespan, and reduces maintenance costs.
Traditional Maintenance | Predictive Maintenance with IoT |
---|---|
Reactive approach | Proactive approach |
Unplanned downtime | Planned downtime |
Higher maintenance costs | Lower maintenance costs |
Shorter equipment lifespan | Extended equipment lifespan |
5. Data-Driven Decision Making
IoT generates vast amounts of data that can be analyzed to gain insights into production processes, machine performance, and customer demand. By leveraging big data analytics and machine learning, manufacturers can make data-driven decisions to optimize operations, improve product quality, and respond to market trends.
Challenges of Implementing IoT in Manufacturing
While IoT offers numerous benefits to manufacturing, there are also challenges that manufacturers must address when implementing IoT solutions.
1. Security Concerns
IoT devices and networks can be vulnerable to cyber-attacks, which can compromise sensitive data and disrupt production processes. Manufacturers must implement robust security measures, such as encryption, access control, and network segmentation, to protect their IoT systems.
2. Integration with Legacy Systems
Many manufacturing facilities have legacy systems and equipment that may not be compatible with IoT technologies. Integrating IoT solutions with existing infrastructure can be challenging and may require significant investment in hardware and software upgrades.
3. Skill Gap
Implementing and managing IoT systems requires specialized skills in areas such as data analytics, cybersecurity, and network management. Manufacturers may struggle to find workers with the necessary skills, leading to a skill gap that can hinder IoT adoption.
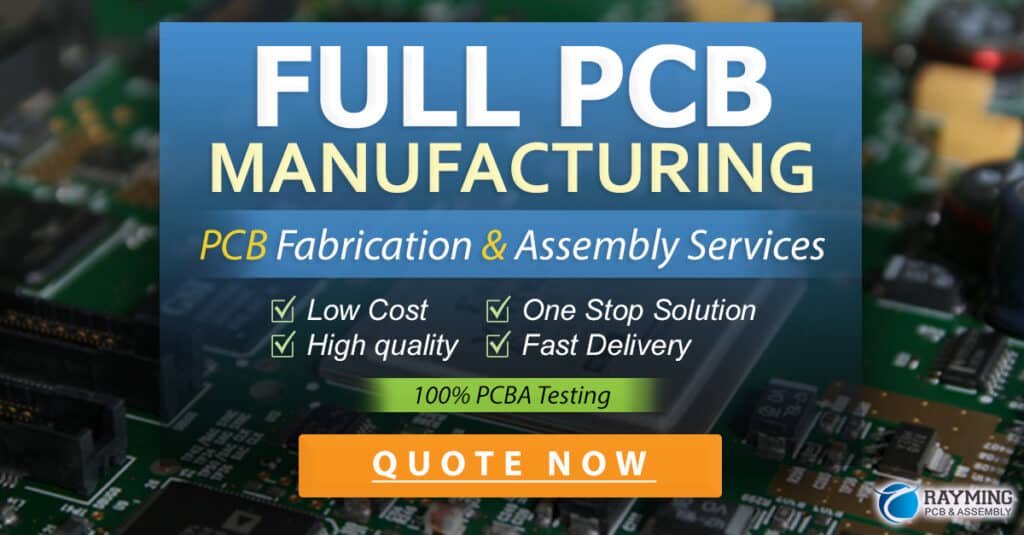
Examples of IoT in Manufacturing
1. Smart Factory
A smart factory is a fully connected and automated manufacturing facility that leverages IoT technologies to optimize production processes. Smart factories use sensors, robots, and automated systems to monitor and control production in real-time, enabling faster, more efficient, and more flexible manufacturing.
2. Predictive Maintenance in Automotive Manufacturing
Automotive manufacturers are using IoT sensors to monitor the health and performance of production equipment, such as robots and conveyor systems. By analyzing sensor data, manufacturers can predict when maintenance is needed and schedule repairs during planned downtime, reducing unplanned stoppages and increasing overall equipment effectiveness.
3. Connected Supply Chain in Aerospace Manufacturing
Aerospace manufacturers are using IoT to create connected supply chains that provide end-to-end visibility of parts and materials. By tracking parts from suppliers to assembly lines using IoT sensors, manufacturers can optimize inventory levels, reduce lead times, and improve quality control.
Future of IoT in Manufacturing
The future of IoT in manufacturing is promising, with new technologies and applications emerging rapidly. Some of the key trends shaping the future of IoT in manufacturing include:
- Edge computing: Processing data closer to the source, reducing latency and bandwidth requirements.
- 5G networks: Enabling faster, more reliable, and more secure connectivity for IoT devices.
- Artificial intelligence: Leveraging machine learning and deep learning to analyze IoT data and optimize production processes.
- Digital twins: Creating virtual replicas of physical assets and processes to simulate and optimize performance.
As these technologies mature, IoT in manufacturing will become even more powerful, enabling manufacturers to create smarter, more efficient, and more agile production processes.
Frequently Asked Questions (FAQ)
- What is the difference between IoT and Industry 4.0?
-
IoT refers to the interconnection of devices and machines through the internet, while Industry 4.0 is a broader concept that encompasses IoT, as well as other technologies such as artificial intelligence, robotics, and cloud computing, to create smart factories and optimize manufacturing processes.
-
How does IoT improve energy efficiency in manufacturing?
-
IoT sensors can monitor energy consumption in real-time, allowing manufacturers to identify inefficiencies and optimize energy usage. By automating energy management systems and implementing smart lighting and HVAC controls, manufacturers can reduce energy waste and costs.
-
Can IoT be used for remote monitoring and control of manufacturing processes?
-
Yes, IoT enables remote monitoring and control of manufacturing processes through connected devices and sensors. Manufacturers can access real-time data and control systems from anywhere, allowing them to respond quickly to issues and optimize operations remotely.
-
How does IoT enable predictive maintenance in manufacturing?
-
IoT sensors can monitor machine health and performance in real-time, collecting data on vibration, temperature, pressure, and other parameters. By analyzing this data using machine learning algorithms, manufacturers can predict when maintenance is needed before a breakdown occurs, reducing unplanned downtime and maintenance costs.
-
What are the key considerations when implementing IoT in manufacturing?
- When implementing IoT in manufacturing, key considerations include security, scalability, interoperability, and data management. Manufacturers must ensure that their IoT systems are secure, can scale to accommodate growth, can integrate with existing systems, and can handle the vast amounts of data generated by connected devices.
Conclusion
IoT in manufacturing is transforming the industrial landscape, enabling smarter, more efficient, and more connected production processes. By leveraging IoT technologies, manufacturers can increase efficiency, enhance quality control, improve supply chain management, and enable predictive maintenance. While there are challenges to implementing IoT in manufacturing, such as security concerns and integration with legacy systems, the benefits far outweigh the risks. As IoT technologies continue to evolve, the future of manufacturing looks bright, with the potential for even greater innovation and optimization.
No responses yet