Introduction
Designing a radio frequency (RF) printed circuit board (PCB) can be a challenging task, especially for those who are new to the field. Unlike traditional PCB design, RF PCB design requires a deep understanding of high-frequency signal behavior, material properties, and layout techniques. In this article, we will dive into five essential tips that every RF PCB designer should know to ensure optimal performance and reliability.
Tip 1: Choose the Right Substrate Material
The Importance of Substrate Material Selection
The substrate material is the foundation of your RF PCB, and choosing the right one is crucial for achieving the desired performance. The substrate material affects the signal integrity, loss, and impedance of your board. It also determines the manufacturability and cost of your PCB.
Common Substrate Materials for RF PCBs
There are several substrate materials commonly used in RF PCB design, each with its own advantages and disadvantages. Some of the most popular options include:
- FR-4: A cost-effective and widely available material, suitable for low-frequency applications up to a few gigahertz.
- Rogers RO4000 Series: A high-performance laminate with low loss and stable dielectric constant, ideal for applications up to 20 GHz.
- Teflon (PTFE): Known for its excellent electrical properties and low loss, Teflon is often used in high-frequency applications above 20 GHz.
Material | Dielectric Constant | Loss Tangent | Frequency Range |
---|---|---|---|
FR-4 | 4.3-4.7 | 0.02 | Up to 2 GHz |
Rogers RO4000 | 3.3-3.5 | 0.0037 | Up to 20 GHz |
Teflon (PTFE) | 2.1 | 0.0004 | Above 20 GHz |
Factors to Consider When Selecting a Substrate Material
When choosing a substrate material for your RF PCB, consider the following factors:
- Frequency range of your application
- Required signal integrity and loss performance
- Cost and availability of the material
- Manufacturability and processing requirements
By selecting the appropriate substrate material based on these factors, you can ensure that your RF PCB performs optimally and meets your design goals.
Tip 2: Optimize Impedance Matching
The Role of Impedance Matching in RF PCB Design
Impedance matching is a critical aspect of RF PCB design, as it ensures maximum power transfer and minimizes signal reflections. When the impedance of the source, transmission line, and load are matched, the signal can propagate with minimal loss and distortion.
Techniques for Achieving Impedance Matching
There are several techniques you can use to achieve impedance matching in your RF PCB design:
- Microstrip Lines: Adjust the width and thickness of the microstrip lines to match the desired characteristic impedance.
- Coplanar Waveguides: Use coplanar waveguides with appropriate dimensions to achieve the target impedance.
- Impedance Matching Networks: Implement L-networks, Pi-networks, or T-networks using lumped components or distributed elements to transform impedances.
Calculating Characteristic Impedance
To calculate the characteristic impedance of a transmission line, you can use the following formulas:
Microstrip Line:
Z0 = (87 / sqrt(εr + 1.41)) * ln(5.98 * h / (0.8 * w + t))
Coplanar Waveguide:
Z0 = (30π / sqrt(εeff)) * K(k) / K(k')
Where:
– Z0
is the characteristic impedance
– εr
is the relative dielectric constant of the substrate
– h
is the substrate thickness
– w
is the width of the microstrip line
– t
is the thickness of the conductor
– εeff
is the effective dielectric constant
– K(k)
and K(k')
are complete elliptic integrals
By optimizing impedance matching, you can minimize signal reflections, reduce insertion loss, and improve the overall performance of your RF PCB.
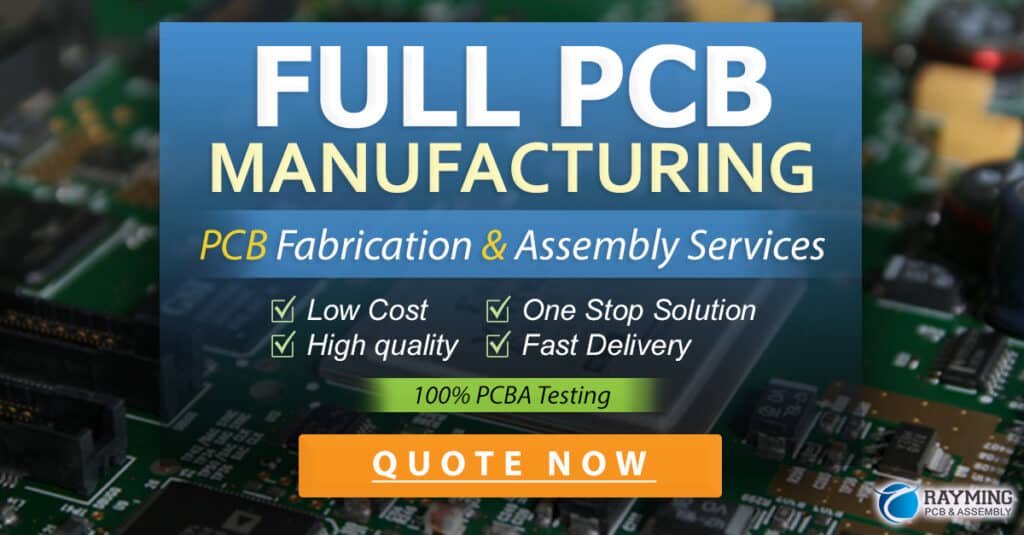
Tip 3: Minimize Parasitics and Losses
The Impact of Parasitics and Losses on RF Performance
Parasitics and losses can significantly degrade the performance of your RF PCB. Parasitic inductances, capacitances, and resistances can cause undesired resonances, coupling, and attenuation, leading to signal distortion and reduced efficiency.
Common Sources of Parasitics and Losses
Some common sources of parasitics and losses in RF PCBs include:
- Component lead inductances
- Trace-to-trace coupling capacitances
- Substrate dielectric losses
- Conductor skin effect and surface roughness
Techniques for Minimizing Parasitics and Losses
To minimize parasitics and losses in your RF PCB design, consider the following techniques:
- Keep trace lengths as short as possible to reduce inductances and resistances.
- Increase trace width to minimize conductor losses due to skin effect.
- Use ground planes and shielding to reduce trace-to-trace coupling and minimize radiation.
- Select low-loss substrate materials to minimize dielectric losses.
- Use surface mount components with minimal lead lengths to reduce parasitic inductances.
Component | Parasitic Effect | Minimization Technique |
---|---|---|
Resistor | Parasitic inductance | Use surface mount, minimize lead length |
Capacitor | Parasitic inductance, ESR | Use surface mount, choose low-ESR types |
Inductor | Parasitic capacitance, resistance | Use high-Q types, minimize lead length |
By carefully designing your layout and selecting appropriate components, you can minimize parasitics and losses, resulting in improved signal integrity and overall RF performance.
Tip 4: Implement Proper Grounding and Shielding
The Importance of Grounding and Shielding in RF PCBs
Proper grounding and shielding are essential for maintaining signal integrity and preventing unwanted interference in RF PCBs. A well-designed grounding scheme provides a low-impedance return path for high-frequency currents, while shielding helps to contain electromagnetic fields and minimize crosstalk.
Grounding Techniques for RF PCBs
Some effective grounding techniques for RF PCBs include:
- Use a solid ground plane to provide a low-impedance return path and minimize inductance.
- Implement a star grounding topology to avoid ground loops and minimize ground bounce.
- Use via stitching to connect ground planes on different layers and maintain a continuous ground reference.
- Separate analog and digital grounds to prevent noise coupling.
Shielding Methods for RF PCBs
Shielding is crucial for preventing electromagnetic interference (EMI) and containing high-frequency signals. Some common shielding methods for RF PCBs include:
- Copper pours: Use copper fills on unused PCB areas to provide additional shielding and reduce radiation.
- Shielding cans: Enclose sensitive components or circuits in metal cans to isolate them from external interference.
- Shielding gaskets: Use conductive gaskets to seal gaps between shielding enclosures and the PCB.
- Via fences: Create a perimeter of closely spaced vias around sensitive areas to provide localizedshielding.
Shielding Method | Effectiveness | Cost | Complexity |
---|---|---|---|
Copper pours | Moderate | Low | Low |
Shielding cans | High | High | High |
Shielding gaskets | High | Moderate | Moderate |
Via fences | Moderate | Low | Moderate |
By implementing proper grounding and shielding techniques, you can ensure the integrity of your RF signals, minimize interference, and improve the overall performance and reliability of your RF PCB.
Tip 5: Perform Thorough Simulation and Testing
The Value of Simulation and Testing in RF PCB Design
Simulation and testing are essential steps in the RF PCB design process, as they help you validate your design decisions, identify potential issues, and optimize performance before committing to fabrication. By performing thorough simulation and testing, you can save time, reduce costs, and ensure that your RF PCB meets the desired specifications.
Simulation Tools for RF PCB Design
There are several simulation tools available for RF PCB design, each with its own strengths and capabilities. Some popular options include:
- Ansys HFSS: A full-wave 3D electromagnetic simulator for high-frequency applications.
- Keysight ADS: A comprehensive platform for schematic capture, layout, and simulation of RF and microwave circuits.
- Cadence AWR: An integrated suite of tools for designing and simulating high-frequency electronics.
- CST Studio Suite: A 3D electromagnetic simulation software for analyzing and optimizing RF and microwave devices.
Testing Techniques for RF PCBs
Once your RF PCB is fabricated, it’s crucial to perform thorough testing to validate its performance and ensure compliance with specifications. Some common testing techniques for RF PCBs include:
- S-parameter measurements: Use a vector network analyzer (VNA) to measure the scattering parameters of your RF PCB and evaluate its frequency response, return loss, and insertion loss.
- Spectrum analysis: Employ a spectrum analyzer to assess the frequency content of your RF signals, detect spurious emissions, and verify signal purity.
- Power measurements: Use a power meter to measure the input and output power levels of your RF PCB and calculate its gain and efficiency.
- Noise figure measurements: Determine the noise figure of your RF PCB using a noise figure meter to evaluate its sensitivity and dynamic range.
Test Equipment | Purpose | Frequency Range |
---|---|---|
Vector Network Analyzer | S-parameter measurements | 10 MHz – 100 GHz |
Spectrum Analyzer | Frequency domain analysis | 9 kHz – 90 GHz |
Power Meter | Power measurements | 10 MHz – 40 GHz |
Noise Figure Meter | Noise figure measurements | 10 MHz – 40 GHz |
By performing comprehensive simulation and testing, you can validate your RF PCB design, identify and address any issues, and ensure optimal performance before deploying your product.
Frequently Asked Questions (FAQ)
-
Q: What is the most critical factor in selecting a substrate material for an RF PCB?
A: The most critical factor in selecting a substrate material for an RF PCB is the frequency range of your application. Different substrate materials have varying dielectric constants and loss tangents, which affect their performance at different frequencies. For example, FR-4 is suitable for applications up to a few gigahertz, while Teflon is ideal for high-frequency applications above 20 GHz. -
Q: How can I minimize parasitic inductances in my RF PCB layout?
A: To minimize parasitic inductances in your RF PCB layout, keep trace lengths as short as possible and use surface mount components with minimal lead lengths. Additionally, use a solid ground plane to provide a low-impedance return path and minimize inductance. -
Q: What is the purpose of impedance matching in RF PCB design?
A: The purpose of impedance matching in RF PCB design is to ensure maximum power transfer and minimize signal reflections. When the impedance of the source, transmission line, and load are matched, the signal can propagate with minimal loss and distortion, improving the overall performance of the RF system. -
Q: How can I prevent electromagnetic interference (EMI) in my RF PCB?
A: To prevent electromagnetic interference (EMI) in your RF PCB, implement proper shielding techniques such as using copper pours, shielding cans, shielding gaskets, or via fences. These methods help to contain electromagnetic fields and minimize crosstalk between components and traces. -
Q: Why is simulation important in RF PCB design?
A: Simulation is important in RF PCB design because it allows you to validate your design decisions, identify potential issues, and optimize performance before committing to fabrication. By performing thorough simulations using tools like Ansys HFSS, Keysight ADS, or Cadence AWR, you can save time, reduce costs, and ensure that your RF PCB meets the desired specifications.
Conclusion
Designing an RF PCB requires careful consideration of several key factors, including substrate material selection, impedance matching, minimizing parasitics and losses, proper grounding and shielding, and thorough simulation and testing. By following the five essential tips discussed in this article, you can enhance the performance, reliability, and manufacturability of your RF PCB.
Remember to choose the right substrate material based on your application’s frequency range and performance requirements, optimize impedance matching to ensure maximum power transfer and minimize reflections, minimize parasitics and losses through smart layout techniques and component selection, implement proper grounding and shielding to maintain signal integrity and prevent interference, and perform comprehensive simulation and testing to validate your design and identify potential issues.
By applying these tips and continuously learning about the latest techniques and best practices in RF PCB design, you can create high-performance, reliable, and cost-effective RF systems that meet the demands of today’s increasingly connected world.
No responses yet