Introduction to PCB-space Technology
In the realm of space exploration and satellite communication, the importance of reliable and high-performance electronic components cannot be overstated. Among these critical components are printed circuit boards (PCBs) designed specifically for RF and microwave applications in space. These PCB-space boards are engineered to withstand the harsh conditions of space while maintaining optimal functionality and signal integrity.
Key Challenges in Space Environment
Space presents a unique set of challenges for electronic components, including:
- Extreme temperature fluctuations
- Radiation exposure
- Vacuum conditions
- Vibration and shock during launch and operation
To overcome these challenges, PCB-space boards are designed with special considerations in mind, such as material selection, layout optimization, and rigorous testing procedures.
Materials Used in PCB-Space Boards
Substrate Materials
The choice of substrate material is crucial for PCB-space boards. Some commonly used materials include:
- Polytetrafluoroethylene (PTFE): Known for its low dielectric constant and low loss tangent, PTFE is an excellent choice for high-frequency applications.
- Rogers materials: Rogers Corporation offers a range of high-performance materials, such as RO4000 and RT/duroid series, which are well-suited for space applications due to their stability and low outgassing properties.
- Ceramic-based materials: Alumina and aluminum nitride are examples of ceramic substrates that offer high thermal conductivity and low dielectric loss, making them suitable for high-power applications.
Conductor Materials
The choice of conductor material is equally important for PCB-space boards. Some common options include:
- Copper: Copper is the most widely used conductor material due to its excellent electrical conductivity and ease of processing.
- Gold: Gold-plated conductors are often used in space applications due to their resistance to oxidation and corrosion.
- Silver: Silver-plated conductors offer high conductivity and are sometimes used in combination with other materials for improved performance.
PCB-Space Board Design Considerations
Signal Integrity
Maintaining signal integrity is critical in RF and microwave PCB-space boards. Some key design considerations include:
- Impedance matching: Ensuring proper impedance matching throughout the signal path is essential to minimize reflections and signal distortion.
- Grounding and shielding: Effective grounding and shielding techniques are employed to reduce electromagnetic interference (EMI) and crosstalk between signals.
- Transmission line design: Microstrip, stripline, and coplanar waveguide structures are carefully designed to optimize signal propagation and minimize losses.
Thermal Management
Managing heat dissipation is crucial for PCB-space boards to ensure reliable operation in the vacuum of space. Some thermal management techniques include:
- Thermal vias: Strategically placed thermal vias help conduct heat away from critical components and into the ground plane or heat sink.
- High thermal conductivity materials: Using substrate materials with high thermal conductivity, such as aluminum nitride, helps efficiently dissipate heat.
- Thermal simulations: Conducting thorough thermal simulations during the design phase helps identify potential hot spots and optimize the board layout for better heat dissipation.
Mechanical Stability
PCB-space boards must be designed to withstand the mechanical stresses encountered during launch and operation. Some key considerations include:
- Vibration and shock resistance: Using reinforced materials and strategic component placement helps minimize the impact of vibrations and shock on the board.
- Coefficient of thermal expansion (CTE) matching: Selecting materials with similar CTEs helps reduce mechanical stress caused by temperature fluctuations.
- Conformal coating: Applying conformal coating to the board provides additional protection against mechanical damage and environmental factors.
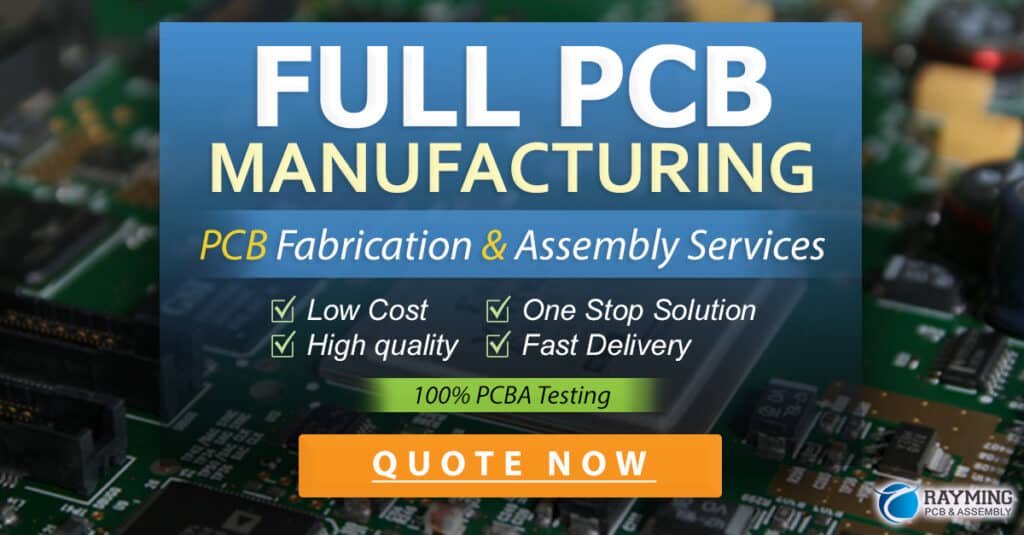
Manufacturing and Testing of PCB-Space Boards
Specialized Manufacturing Processes
Manufacturing PCB-space boards requires specialized processes to ensure the highest level of quality and reliability. Some key aspects include:
- Clean room environment: PCB-space boards are often manufactured in clean room environments to minimize contamination and ensure precise control over the manufacturing process.
- Automated assembly: Automated pick-and-place machines and reflow soldering processes are used to ensure consistent and reliable component placement and soldering.
- Inspection and quality control: Rigorous inspection and quality control procedures, including automated optical inspection (AOI) and X-ray inspection, are employed to detect and rectify any manufacturing defects.
Testing and Qualification
Before deployment in space, PCB-space boards undergo extensive testing and qualification processes to ensure they can withstand the harsh space environment. Some common tests include:
- Thermal cycling: Boards are subjected to multiple cycles of extreme temperature variations to evaluate their performance and reliability under thermal stress.
- Vibration and shock testing: Boards are exposed to simulated launch conditions to assess their ability to withstand mechanical stresses.
- Vacuum testing: Boards are tested in a vacuum chamber to ensure they can operate reliably in the vacuum of space.
- Radiation testing: Boards are exposed to simulated space radiation to evaluate their resistance to radiation-induced damage.
Applications of PCB-Space Boards
PCB-space boards find applications in various aspects of space technology, including:
- Satellite communication systems: RF and microwave PCB-space boards are used in the transmit and receive chains of satellite communication systems, enabling reliable and high-speed data transmission.
- Radar systems: PCB-space boards are used in space-based radar systems for Earth observation, weather monitoring, and scientific research.
- Navigation and positioning: PCB-space boards are used in global navigation satellite systems (GNSS) and other positioning systems to provide accurate location information.
- Space exploration: PCB-space boards are used in various instruments and subsystems of space exploration missions, including rovers, landers, and probes.
Future Trends in PCB-Space Technology
As space technology continues to advance, so do the requirements for PCB-space boards. Some future trends in this field include:
- Higher frequencies: The demand for higher data rates and bandwidth is driving the development of PCB-space boards that can operate at higher frequencies, such as millimeter-wave and terahertz ranges.
- Miniaturization: The need for smaller and lighter spacecraft is driving the miniaturization of PCB-space boards, with a focus on high-density interconnect (HDI) and 3D packaging technologies.
- Advanced materials: Researchers are exploring novel materials, such as graphene and carbon nanotubes, for potential use in PCB-space boards to enhance performance and reliability.
- Additive manufacturing: 3D printing technologies are being investigated for the fabrication of PCB-space boards, offering the potential for more complex geometries and faster prototyping.
Frequently Asked Questions (FAQ)
-
What makes PCB-space boards different from standard PCBs?
PCB-space boards are designed to withstand the harsh conditions of space, including extreme temperature fluctuations, radiation exposure, vacuum conditions, and mechanical stresses. They use specialized materials, design techniques, and manufacturing processes to ensure reliable operation in space. -
Why are RF and microwave frequencies important for space applications?
RF and microwave frequencies are used for various space applications, such as satellite communication, radar systems, and navigation. These frequencies offer the bandwidth and penetration required for long-distance communication and remote sensing in space. -
How are PCB-space boards tested for space qualification?
PCB-space boards undergo rigorous testing and qualification processes to ensure they can withstand the space environment. These tests include thermal cycling, vibration and shock testing, vacuum testing, and radiation testing, among others. The boards must pass these tests to be deemed space-qualified. -
What are some common materials used in PCB-space boards?
Common substrate materials used in PCB-space boards include PTFE, Rogers materials, and ceramic-based materials like alumina and aluminum nitride. Copper, gold, and silver are often used as conductor materials. These materials are chosen for their electrical, thermal, and mechanical properties that are well-suited for space applications. -
What are the future trends in PCB-space technology?
Future trends in PCB-space technology include the development of boards that can operate at higher frequencies, miniaturization of boards using HDI and 3D packaging technologies, exploration of advanced materials like graphene and carbon nanotubes, and the potential use of additive manufacturing techniques for board fabrication.
Conclusion
RF and microwave PCB-space boards are critical components in the field of space technology, enabling reliable and high-performance communication, navigation, and remote sensing systems. These boards are designed to withstand the unique challenges of the space environment, using specialized materials, design techniques, and manufacturing processes. As space technology continues to advance, so does the development of PCB-space boards, with trends towards higher frequencies, miniaturization, advanced materials, and innovative manufacturing methods. By pushing the boundaries of PCB-space technology, we can enable more ambitious space exploration missions and improve our understanding of the universe.
No responses yet