Introduction to PCB Insertion Loss
Printed Circuit Boards (PCBs) are the backbone of modern electronics, providing a reliable and efficient means of interconnecting electronic components. As the demand for high-speed and high-frequency applications continues to grow, the importance of understanding and minimizing insertion loss in PCBs becomes increasingly critical. Insertion loss, a measure of the signal power lost as it traverses through a PCB, is a key factor in determining the performance and reliability of high-frequency electronic systems.
What is Insertion Loss?
Insertion loss is defined as the ratio of the signal power at the output of a PCB to the signal power at its input, expressed in decibels (dB). It represents the attenuation of the signal as it propagates through the PCB, taking into account various factors such as conductor losses, dielectric losses, and reflections. The higher the insertion loss, the more signal power is lost, leading to degraded signal integrity and potentially compromising the functionality of the electronic system.
Factors Affecting PCB Insertion Loss
Several factors contribute to insertion loss in PCBs, including:
-
Conductor Losses: As the signal travels through the copper traces on the PCB, it experiences resistance, which leads to power dissipation in the form of heat. The higher the frequency, the more pronounced the conductor losses become due to the skin effect, where the current tends to flow on the outer surface of the conductor.
-
Dielectric Losses: The dielectric material used in the PCB substrate also contributes to insertion loss. As the signal propagates through the dielectric, some of its energy is absorbed and converted into heat. The dissipation factor (tan δ) of the dielectric material determines the extent of these losses.
-
Reflections: Impedance mismatches along the signal path can cause reflections, leading to signal power being reflected back to the source instead of reaching the intended destination. Proper impedance matching and controlled impedance design techniques are crucial for minimizing reflections and reducing insertion loss.
-
Via Losses: Vias, the conductive pathways that connect different layers of a multi-layer PCB, also contribute to insertion loss. The discontinuity introduced by vias can cause reflections and signal degradation, especially at high frequencies.
Common High Frequency PCB Constructions
To address the challenges of high-frequency PCB design and minimize insertion loss, various PCB constructions have been developed. Each construction has its own advantages and trade-offs in terms of performance, manufacturability, and cost. Let’s explore some of the most common high-frequency PCB constructions:
Microstrip
Microstrip is one of the most widely used PCB constructions for high-frequency applications. It consists of a conductive trace on the top layer of the PCB, with a ground plane on the bottom layer. The dielectric material separates the trace from the ground plane, providing a controlled impedance environment. Microstrip offers several advantages:
- Simplicity in design and fabrication
- Good impedance control
- Relatively low cost
However, microstrip also has some limitations:
- Higher radiation losses compared to other constructions
- Susceptible to crosstalk and electromagnetic interference (EMI)
- Limited bandwidth due to the presence of the ground plane
Stripline
Stripline is another popular high-frequency PCB construction. It consists of a conductive trace embedded between two ground planes, with the dielectric material surrounding the trace. Stripline offers several benefits:
- Excellent isolation and shielding from external interference
- Low radiation losses
- Good impedance control
However, stripline also has some drawbacks:
- Increased complexity in design and fabrication compared to microstrip
- Higher cost due to the additional layers and materials required
- Limited access to the signal trace for probing and troubleshooting
Coplanar Waveguide (CPW)
Coplanar Waveguide (CPW) is a high-frequency PCB construction that consists of a conductive trace with ground planes on either side, all on the same layer. The dielectric material is present both above and below the conductors. CPW offers several advantages:
- Lower dispersion compared to microstrip and stripline
- Easier integration with surface-mount components
- Good isolation and shielding properties
However, CPW also has some limitations:
- Increased complexity in design and fabrication
- Higher conductor losses compared to microstrip and stripline
- Sensitivity to manufacturing tolerances
Grounded Coplanar Waveguide (GCPW)
Grounded Coplanar Waveguide (GCPW) is a variation of the CPW construction, where an additional ground plane is added below the dielectric layer. GCPW combines the benefits of CPW and microstrip:
- Improved isolation and shielding compared to CPW
- Lower radiation losses compared to microstrip
- Good impedance control
However, GCPW also has some drawbacks:
- Increased complexity in design and fabrication
- Higher cost due to the additional ground plane
- Potential for mode conversion and signal integrity issues
Insertion Loss Comparisons
To evaluate the performance of different high-frequency PCB constructions, it is essential to compare their insertion loss characteristics. The following table provides a comparison of the typical insertion loss values for the common constructions discussed earlier:
PCB Construction | Insertion Loss @ 1 GHz (dB/inch) | Insertion Loss @ 10 GHz (dB/inch) |
---|---|---|
Microstrip | 0.1 – 0.3 | 0.3 – 0.8 |
Stripline | 0.05 – 0.2 | 0.2 – 0.6 |
CPW | 0.1 – 0.4 | 0.4 – 1.0 |
GCPW | 0.08 – 0.3 | 0.3 – 0.9 |
Note: The insertion loss values provided are typical ranges and may vary depending on the specific design, materials, and manufacturing processes used.
From the table, we can observe that stripline generally exhibits lower insertion loss compared to the other constructions, especially at higher frequencies. This is due to its excellent isolation and shielding properties, as well as the symmetric field distribution within the structure. Microstrip and GCPW have comparable insertion loss characteristics, while CPW tends to have slightly higher insertion loss due to its higher conductor losses.
It is important to note that the actual insertion loss in a PCB will depend on various factors such as the dielectric material properties, conductor thickness, trace width, and the overall design and layout of the board. Therefore, these comparisons should be used as a general guideline, and detailed simulations and measurements should be performed for accurate insertion loss characterization in specific PCB designs.
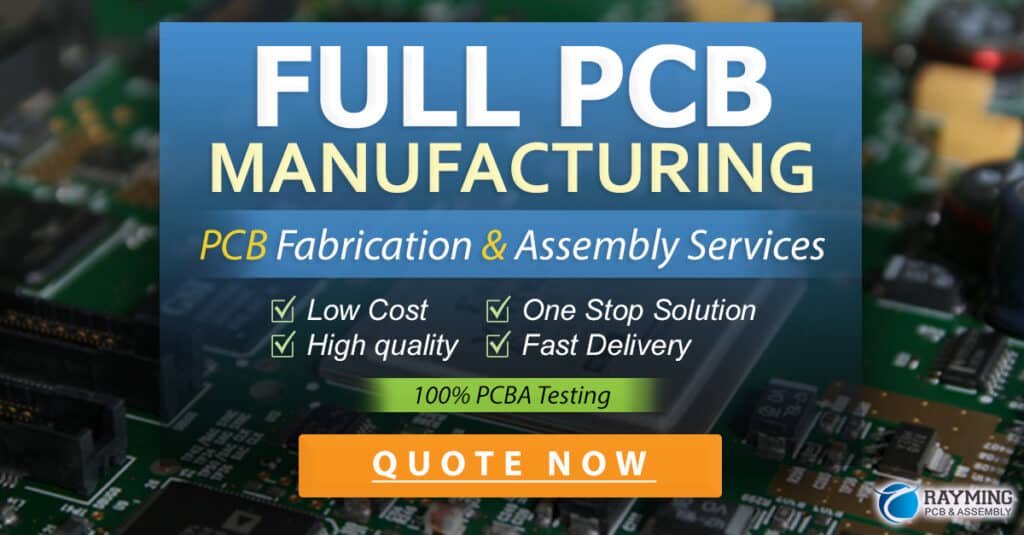
Strategies for Minimizing Insertion Loss
To minimize insertion loss in high-frequency PCBs, several strategies can be employed:
-
Material Selection: Choose low-loss dielectric materials with a low dissipation factor (tan δ) to reduce dielectric losses. Materials such as Rogers RO4000 series, Isola IS680, and Taconic RF-35 are commonly used for high-frequency applications.
-
Conductor Optimization: Use thicker copper traces to reduce conductor losses, especially at higher frequencies. Consider using low-profile copper (LPC) or very low-profile copper (VLPC) foils to minimize the skin effect and improve signal integrity.
-
Impedance Matching: Ensure proper impedance matching throughout the signal path to minimize reflections and reduce insertion loss. Use controlled impedance design techniques and perform simulations to optimize the trace geometry and spacing.
-
Via Optimization: Minimize the use of vias whenever possible, as they introduce discontinuities and can contribute to insertion loss. When vias are necessary, use smaller via sizes, optimize via placement, and consider using blind or buried vias to reduce the impact on signal integrity.
-
Layout Considerations: Follow good PCB layout practices to minimize insertion loss. Keep trace lengths as short as possible, avoid sharp bends and corners, and maintain consistent trace width and spacing. Use ground planes and shielding techniques to reduce crosstalk and EMI.
-
Simulation and Measurement: Perform electromagnetic simulations to predict and optimize the insertion loss performance of the PCB design. Use tools like Ansys HFSS, Keysight ADS, or Mentor Graphics HyperLynx to analyze and fine-tune the design. Validate the simulated results through real-world measurements using a vector network analyzer (VNA) and high-frequency probes.
By applying these strategies and carefully considering the trade-offs between different PCB constructions, designers can effectively minimize insertion loss and ensure optimal performance in high-frequency electronic systems.
Frequently Asked Questions (FAQ)
-
What is the main difference between microstrip and stripline PCB constructions?
The main difference between microstrip and stripline is the location of the conductive trace. In microstrip, the trace is on the top layer of the PCB, with a ground plane on the bottom layer. In stripline, the trace is embedded between two ground planes, with the dielectric material surrounding it. Stripline offers better isolation and shielding compared to microstrip, but it is more complex to design and fabricate. -
How does the choice of dielectric material affect insertion loss in PCBs?
The dielectric material used in PCBs plays a significant role in determining the insertion loss. Materials with a low dissipation factor (tan δ) are preferred for high-frequency applications, as they minimize dielectric losses. Low-loss materials such as Rogers RO4000 series, Isola IS680, and Taconic RF-35 are commonly used to reduce insertion loss in high-frequency PCBs. -
What is the skin effect, and how does it impact insertion loss at high frequencies?
The skin effect is a phenomenon where the current tends to flow on the outer surface of a conductor at high frequencies. As the frequency increases, the effective cross-sectional area of the conductor decreases, leading to higher resistance and increased conductor losses. To mitigate the skin effect and reduce insertion loss, designers can use thicker copper traces or employ low-profile copper (LPC) or very low-profile copper (VLPC) foils. -
Why is impedance matching important for minimizing insertion loss in PCBs?
Impedance matching is crucial for minimizing insertion loss because it ensures that the maximum amount of signal power is transferred from the source to the load. When there are impedance mismatches along the signal path, reflections occur, causing a portion of the signal power to be reflected back to the source instead of reaching the intended destination. By achieving proper impedance matching through controlled impedance design techniques, designers can minimize reflections and reduce insertion loss. -
How can electromagnetic simulations help in evaluating and optimizing insertion loss in PCBs?
Electromagnetic simulations, using tools like Ansys HFSS, Keysight ADS, or Mentor Graphics HyperLynx, allow designers to predict and analyze the insertion loss performance of PCB designs before physical prototyping. These simulations take into account the complex interactions between conductors, dielectrics, and other PCB elements, providing valuable insights into the insertion loss characteristics. By iteratively simulating and optimizing the design, designers can fine-tune various parameters such as trace geometry, spacing, and material properties to minimize insertion loss and ensure optimal performance.
Conclusion
Insertion loss is a critical consideration in the design of high-frequency PCBs, as it directly impacts the signal integrity and overall performance of electronic systems. By understanding the factors that contribute to insertion loss and comparing the performance of common high-frequency PCB constructions, designers can make informed decisions to minimize signal attenuation and ensure reliable operation.
Stripline, microstrip, coplanar waveguide (CPW), and grounded coplanar waveguide (GCPW) are among the most widely used PCB constructions for high-frequency applications, each with its own advantages and trade-offs. Stripline generally offers the lowest insertion loss, while microstrip and GCPW provide a balance between performance and manufacturability. CPW, although having slightly higher insertion loss, offers benefits such as lower dispersion and easier integration with surface-mount components.
To effectively minimize insertion loss, designers should employ strategies such as careful material selection, conductor optimization, impedance matching, via optimization, and good layout practices. Electromagnetic simulations and real-world measurements are essential tools for evaluating and optimizing the insertion loss performance of PCB designs.
By considering the insertion loss characteristics of different PCB constructions and applying appropriate design strategies, engineers can develop high-performance, reliable electronic systems that meet the ever-increasing demands of high-frequency applications in various industries, from telecommunications and aerospace to automotive and consumer electronics.
No responses yet