The Importance of PCB Cleanliness
Printed Circuit Boards (PCBs) are the backbone of modern electronic devices. They are responsible for connecting and supporting various components that make up a system. However, the cleanliness of a PCB can have a significant impact on its performance and reliability. Dirt, dust, and other contaminants can compromise the integrity of the circuitry, leading to malfunctions and even complete system failure.
In this article, we will explore the various aspects of PCB cleanliness and how it affects system performance. We will discuss the sources of contamination, the effects of dirt on PCBs, and the methods used to ensure PCB cleanliness.
Sources of PCB Contamination
PCBs can become contaminated during various stages of manufacturing, assembly, and use. Some of the common sources of contamination include:
-
Dust and Debris: Dust particles and debris can accumulate on the surface of PCBs during manufacturing, storage, or transportation. These contaminants can interfere with the electrical connections and cause short circuits or signal degradation.
-
Flux Residue: During the soldering process, flux is used to remove oxides and improve the wettability of the solder. However, if the flux residue is not properly cleaned, it can leave behind a corrosive and conductive layer on the PCB surface.
-
Oils and Greases: Fingerprints, oils from handling, and lubricants used in the manufacturing process can leave behind a thin film on the PCB. This film can attract dust and other contaminants, leading to further issues.
-
Moisture: Exposure to humid environments can cause moisture to accumulate on the PCB surface. This moisture can lead to corrosion, short circuits, and other reliability issues.
Effects of Dirt on PCB Performance
Dirty PCBs can have a range of negative effects on system performance. Some of the common issues caused by contamination include:
-
Increased Resistance: Dust, debris, and other contaminants can increase the resistance between electrical contacts on the PCB. This increased resistance can lead to signal degradation, power loss, and reduced system efficiency.
-
Short Circuits: Conductive contaminants, such as flux residue or metal particles, can create unintended electrical paths between components on the PCB. These short circuits can cause system malfunctions, overheating, and even permanent damage to the components.
-
Corrosion: Moisture and certain contaminants can react with the metal traces on the PCB, causing corrosion. Corrosion can lead to increased resistance, open circuits, and degradation of the PCB over time.
-
Signal Integrity Issues: Dirt and contamination can affect the high-frequency signals transmitted through the PCB. This can result in signal reflections, crosstalk, and other signal integrity issues that degrade system performance.
Case Study: The Impact of Flux Residue on PCB Performance
To illustrate the effects of contamination on PCB performance, let’s consider a case study involving flux residue. In this study, a batch of PCBs was manufactured using a water-soluble flux. However, due to inadequate cleaning, some of the PCBs had remnants of flux residue on their surface.
The performance of the contaminated PCBs was compared to that of clean PCBs from the same batch. The results are summarized in the table below:
Parameter | Clean PCBs | Contaminated PCBs |
---|---|---|
Signal Integrity (Eye Diagram) | Good | Degraded |
Insulation Resistance (MΩ) | >1000 | <100 |
Failure Rate (%) | 0.5 | 5 |
As evident from the data, the presence of flux residue had a significant impact on the performance of the PCBs. The contaminated PCBs exhibited degraded signal integrity, reduced insulation resistance, and a higher failure rate compared to the clean PCBs.
This case study highlights the importance of thorough cleaning and the potential consequences of leaving contaminants on the PCB surface.
Methods for Ensuring PCB Cleanliness
To maintain the performance and reliability of PCBs, it is essential to implement proper cleaning methods during the manufacturing and assembly process. Some of the common techniques used to ensure PCB cleanliness include:
-
Solvent Cleaning: Solvents, such as isopropyl alcohol (IPA) or specialized cleaning agents, can be used to remove flux residue, oils, and other contaminants from the PCB surface. Solvent cleaning can be performed manually or using automated cleaning systems.
-
Aqueous Cleaning: Aqueous cleaning involves the use of water-based solutions to remove contaminants from the PCB. This method is particularly effective for removing water-soluble flux residues. Aqueous cleaning can be done using ultrasonic tanks, spray systems, or immersion processes.
-
Plasma Cleaning: Plasma cleaning is a dry cleaning method that uses ionized gas to remove organic contaminants from the PCB surface. This method is highly effective and leaves no residue, making it suitable for high-precision applications.
-
Conformal Coating: Applying a conformal coating to the PCB can provide an additional layer of protection against contamination. Conformal coatings, such as acrylic, silicone, or polyurethane, can prevent moisture, dust, and other contaminants from reaching the PCB surface.
Choosing the Right Cleaning Method
The choice of cleaning method depends on various factors, such as the type of contaminants, the PCB materials, and the specific application requirements. The table below provides a comparison of the different cleaning methods:
Cleaning Method | Effectiveness | Residue-Free | Suitable for |
---|---|---|---|
Solvent Cleaning | High | Yes | General purpose |
Aqueous Cleaning | High | Yes | Water-soluble flux |
Plasma Cleaning | Very High | Yes | High-precision applications |
Conformal Coating | Moderate | No | Environmental protection |
It is important to consider the compatibility of the cleaning method with the PCB materials and components to avoid any damage during the cleaning process.
Frequently Asked Questions (FAQ)
-
What are the most common contaminants found on PCBs?
The most common contaminants found on PCBs include dust, flux residue, oils, greases, and moisture. These contaminants can accumulate during manufacturing, assembly, storage, or use. -
How does flux residue affect PCB performance?
Flux residue can leave behind a corrosive and conductive layer on the PCB surface. This residue can increase resistance, cause short circuits, and lead to signal integrity issues. Proper cleaning is essential to remove flux residue and maintain PCB performance. -
Can contamination cause permanent damage to PCBs?
Yes, contamination can cause permanent damage to PCBs. For example, corrosion caused by moisture or flux residue can eat away at the metal traces on the PCB, leading to open circuits and irreparable damage. Short circuits caused by conductive contaminants can also destroy components on the PCB. -
What is conformal coating, and how does it help protect PCBs?
Conformal coating is a protective layer applied to the surface of a PCB. It can be made of materials such as acrylic, silicone, or polyurethane. Conformal coating helps protect the PCB from moisture, dust, and other environmental contaminants, thereby improving its reliability and longevity. -
How often should PCBs be cleaned to maintain optimal performance?
The frequency of PCB cleaning depends on the specific application and the environment in which the PCB operates. In general, PCBs should be cleaned whenever there is visible contamination or when performance issues are detected. Regular inspections and preventive maintenance can help identify and address contamination issues before they lead to serious problems.
Conclusion
PCB cleanliness is a critical factor in ensuring the performance and reliability of electronic systems. Contamination from dust, flux residue, oils, and moisture can have detrimental effects on PCB performance, leading to signal integrity issues, short circuits, corrosion, and even permanent damage.
To maintain PCB cleanliness, it is essential to implement proper cleaning methods during manufacturing and assembly. Solvent cleaning, aqueous cleaning, plasma cleaning, and conformal coating are some of the common techniques used to remove contaminants and protect PCBs from further contamination.
By understanding the sources and effects of PCB contamination and adopting appropriate cleaning methods, manufacturers can ensure the optimal performance and longevity of their electronic systems.
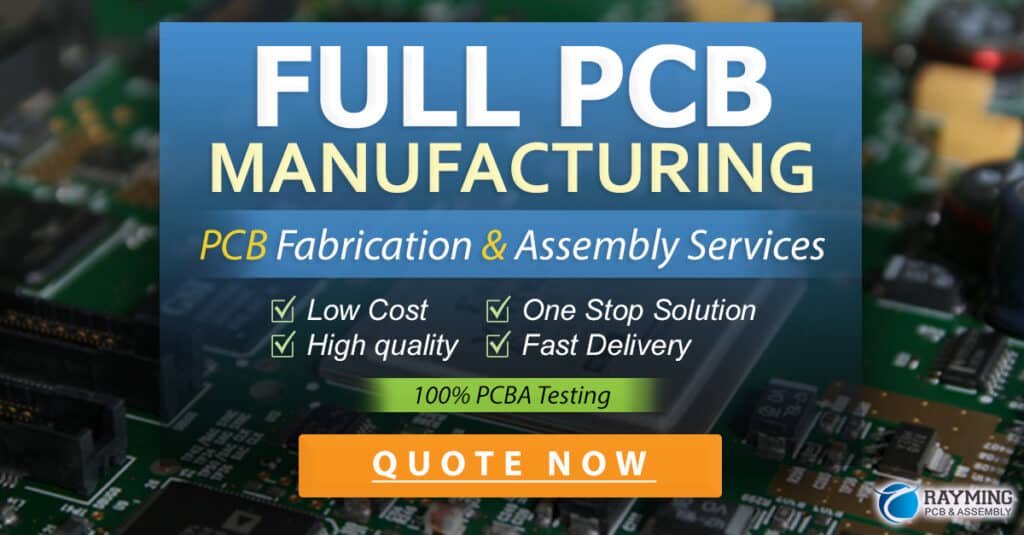
No responses yet