What is a Flexible PCB?
A flexible PCB, also known as a flex circuit or flexible printed wiring, is a type of printed circuit board that is made from flexible materials such as polyimide or polyester. Unlike rigid PCBs, which are made from a solid substrate, flexible PCBs can bend and twist without breaking or losing their electrical properties.
Flexible PCBs consist of a thin, flexible substrate with conductive traces and components mounted on one or both sides. They can be single-sided, double-sided, or multi-layered, depending on the complexity of the circuit design.
Characteristics of Flexible PCBs
1. Flexibility and Durability
One of the most significant characteristics of flexible PCBs is their ability to bend and flex without breaking. This flexibility allows them to be used in applications where traditional rigid PCBs would not be suitable, such as in wearable devices, medical implants, and aerospace systems.
Flexible PCBs are also highly durable and can withstand repeated bending and twisting without losing their electrical properties. They are resistant to vibration, shock, and extreme temperatures, making them ideal for use in harsh environments.
2. Lightweight and Thin
Another characteristic that makes flexible PCBs popular is their lightweight and thin profile. Flexible PCBs are typically much thinner than rigid PCBs, with thicknesses ranging from 0.05mm to 0.25mm. This makes them ideal for use in compact and portable devices, such as smartphones, tablets, and smartwatches.
The lightweight nature of flexible PCBs also makes them easier to transport and install, reducing overall system weight and size.
3. High-Density Interconnects
Flexible PCBs allow for high-density interconnects, meaning that more components can be packed into a smaller space. This is achieved through the use of fine-pitch traces and small vias, which enable the routing of complex circuits in a compact form factor.
High-density interconnects are particularly useful in applications where space is limited, such as in medical devices, aerospace systems, and consumer electronics.
4. Improved Signal Integrity
Flexible PCBs offer improved signal integrity compared to rigid PCBs. The flexible substrate material has a lower dielectric constant than the FR-4 material used in rigid PCBs, which reduces signal loss and improves signal quality.
Additionally, the ability to route traces in three dimensions allows for shorter signal paths and reduced crosstalk, further enhancing signal integrity.
5. Cost-Effective
Despite their advanced features and benefits, flexible PCBs can be cost-effective in many applications. The use of flexible PCBs can reduce the overall system cost by eliminating the need for connectors and cables, which are often required when using rigid PCBs.
Flexible PCBs also enable the integration of multiple functions into a single board, reducing the number of components and assembly steps required. This can lead to significant cost savings in high-volume production.
Applications of Flexible PCBs
Flexible PCBs find applications in a wide range of industries due to their unique characteristics. Some of the most common applications include:
1. Consumer Electronics
Flexible PCBs are extensively used in consumer electronics, such as smartphones, tablets, laptops, and wearable devices. Their flexibility and thin profile allow for the creation of compact and lightweight devices with advanced features.
2. Medical Devices
Flexible PCBs are ideal for use in medical devices, such as implantable sensors, hearing aids, and pacemakers. Their flexibility and biocompatibility make them suitable for use in the human body, while their high-density interconnects enable the integration of complex functions in a small form factor.
3. Automotive Electronics
Flexible PCBs are increasingly used in automotive electronics, such as in-vehicle infotainment systems, dashboard displays, and driver assistance systems. Their flexibility and durability make them suitable for use in the harsh automotive environment, while their lightweight nature helps reduce overall vehicle weight.
4. Aerospace and Defense
Flexible PCBs are used in various aerospace and defense applications, such as in satellites, aircraft, and military equipment. Their ability to withstand extreme temperatures, vibration, and shock makes them ideal for use in these demanding environments.
5. Industrial Electronics
Flexible PCBs are used in industrial electronics, such as in robotics, automation systems, and process control equipment. Their flexibility and durability enable them to be used in moving parts and harsh industrial environments.
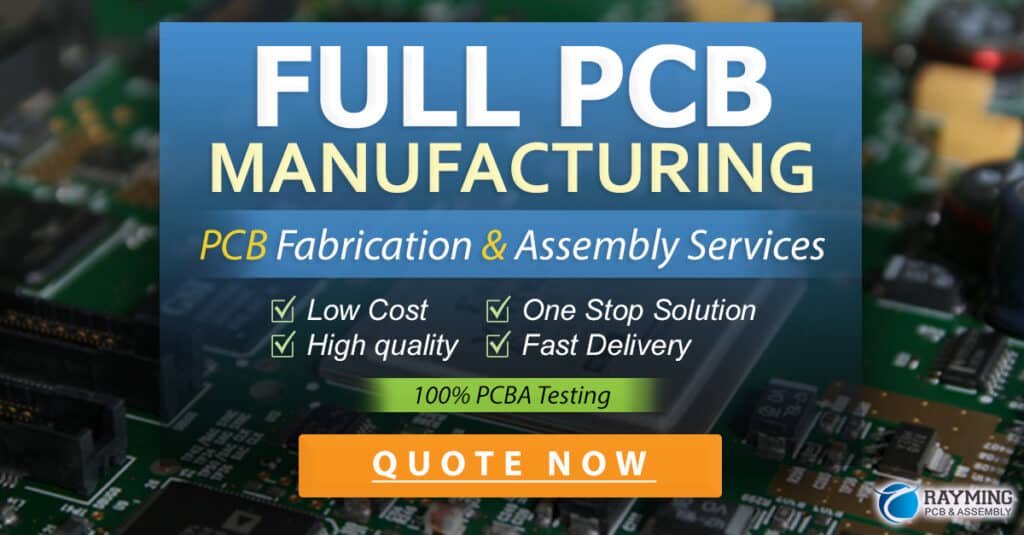
Advantages of Flexible PCBs
Flexible PCBs offer several advantages over traditional rigid PCBs, including:
- Increased design flexibility and freedom
- Reduced system size and weight
- Improved reliability and durability
- Enhanced signal integrity and reduced signal loss
- Cost-effectiveness in high-volume production
- Elimination of connectors and cables
- Integration of multiple functions into a single board
Challenges and Considerations
While flexible PCBs offer numerous benefits, there are also some challenges and considerations to keep in mind when designing and manufacturing them:
- Material selection: Choosing the right flexible substrate material is crucial for ensuring the desired flexibility, durability, and electrical properties.
- Manufacturing process: Flexible PCBs require specialized manufacturing processes and equipment, which can increase production costs and lead times.
- Assembly and handling: The flexibility of the PCBs can make assembly and handling more challenging, requiring specialized tools and techniques.
- Thermal management: Flexible PCBs have limited heat dissipation capabilities compared to rigid PCBs, which can impact the thermal management of the overall system.
- Reliability testing: Ensuring the reliability of flexible PCBs requires specialized testing methods that account for the unique stresses and strains they experience during use.
Future Trends in Flexible PCBs
As technology continues to advance, the demand for flexible PCBs is expected to grow in the coming years. Some of the future trends in flexible PCBs include:
- Increased adoption in wearable devices and Internet of Things (IoT) applications
- Development of new materials with improved flexibility, durability, and electrical properties
- Advancements in manufacturing processes to reduce costs and lead times
- Integration of flexible PCBs with other technologies, such as printed electronics and 3D printing
- Expansion into new application areas, such as healthcare, energy, and environmental monitoring
Frequently Asked Questions (FAQ)
1. What is the difference between a flexible PCB and a rigid PCB?
Flexible PCBs are made from flexible materials and can bend and twist without breaking, while rigid PCBs are made from a solid substrate and cannot flex. Flexible PCBs offer increased design freedom, reduced system size and weight, and improved reliability compared to rigid PCBs.
2. What materials are used to make flexible PCBs?
Flexible PCBs are typically made from polyimide or polyester substrates, which provide the desired flexibility and durability. Conductive traces are usually made from copper, and components are mounted using surface-mount technology (SMT) or chip-on-flex (COF) techniques.
3. Can flexible PCBs be used in high-temperature applications?
Yes, flexible PCBs can be designed to withstand high temperatures by using specialized materials and manufacturing processes. Polyimide substrates, for example, can withstand temperatures up to 300°C, making them suitable for use in harsh environments.
4. How are flexible PCBs manufactured?
Flexible PCBs are manufactured using a process similar to that used for rigid PCBs, but with some additional steps to account for the flexible substrate. The process typically involves printing the circuit pattern on the substrate, etching away the unwanted copper, and laminating the layers together. Specialized equipment and techniques are used to ensure the desired flexibility and durability of the final product.
5. What are the challenges in designing flexible PCBs?
Designing flexible PCBs can be challenging due to the unique mechanical and electrical properties of the flexible substrate. Some of the key challenges include selecting the right materials, optimizing the circuit layout for flexibility and reliability, and ensuring adequate thermal management. Additionally, the assembly and handling of flexible PCBs require specialized tools and techniques to prevent damage and ensure proper functionality.
Conclusion
Flexible PCBs have become increasingly popular due to their unique characteristics, which offer numerous advantages over traditional rigid PCBs. Their flexibility, durability, lightweight nature, high-density interconnects, improved signal integrity, and cost-effectiveness make them ideal for use in a wide range of applications, from consumer electronics to aerospace and defense.
As technology continues to advance, the demand for flexible PCBs is expected to grow, driven by the increasing adoption of wearable devices, IoT applications, and other emerging technologies. With ongoing advancements in materials, manufacturing processes, and design techniques, flexible PCBs are poised to play a crucial role in shaping the future of electronics.
No responses yet