What is Soldering Flux?
Soldering flux is a chemical cleaning agent used in the soldering process to promote the wetting of a surface to be soldered by removing oxidation films or impurities from the surface. It is designed to improve electrical contact and mechanical strength in solder joints. Soldering flux also acts as a temporary adhesive, holding components in place until the solder solidifies.
Key Functions of Soldering Flux
Soldering flux serves several important functions in the soldering process:
-
Cleaning: Flux removes surface oxidation and other contaminants from the metals being soldered, allowing the molten solder to properly wet and adhere to the surfaces.
-
Protection: During soldering, flux protects the cleaned metal surfaces from re-oxidation by shielding them from oxygen in the air.
-
Improving Flow: Flux lowers the surface tension of molten solder, enabling it to flow and spread more easily over the joint surfaces.
-
Adhesion: Some fluxes act as a temporary adhesive, holding components in position until the solder solidifies.
Types of Soldering Flux
There are several types of soldering flux available, each with its own properties and uses. The main categories of flux are:
Rosin Flux
Rosin flux is the most common type of flux used in electronics soldering. It is made from refined pine sap (rosin) and is available in several grades based on the level of activator it contains:
- R (Rosin): Plain rosin flux with no activators. Used for clean metals that are easy to solder.
- RMA (Rosin Mildly Activated): Contains a small amount of activator. Suitable for most general-purpose electronics soldering.
- RA (Rosin Activated): Has a higher activator content for improved cleaning action. Used for tarnished or oxidized surfaces.
Rosin flux is electrically non-conductive and can be left on the PCB after soldering, although cleaning is recommended for high-reliability applications.
Water-Soluble Flux
Water-soluble flux, also known as organic acid flux, uses organic activators that are highly effective at removing metal oxides. This type of flux is more aggressive than rosin flux and is typically used in wave soldering or other automated soldering processes.
The key advantage of water-soluble flux is that it can be easily cleaned off with water after soldering. However, it is essential to thoroughly remove all residue, as the activators can cause corrosion if left on the PCB.
No-Clean Flux
No-clean flux is designed to leave minimal, non-corrosive residue that does not require cleaning after soldering. This type of flux is popular in commercial electronics manufacturing as it eliminates the cleaning step, saving time and cost.
No-clean fluxes can be rosin-based or water-based and contain a low level of activator. While they don’t strictly require post-soldering cleaning, removing the residue is still recommended for critical applications or to improve the appearance of the solder joint.
Flux Form Factors
Soldering flux is available in several different form factors, each with its own application method:
Flux Pen
A flux pen is a convenient, marker-like dispenser that allows you to apply flux directly and precisely to the soldering area. Flux pens are ideal for small-scale or rework soldering tasks.
Flux Paste
Flux paste is a thick, gel-like formulation that can be applied using a syringe, brush, or spatula. It is useful for pre-applying flux to specific areas or components before soldering.
Liquid Flux
Liquid flux has a thin consistency and is typically applied using a brush or bottle dispenser. It is well-suited for covering larger areas or for dipping components prior to soldering.
Flux-Cored Solder Wire
Flux-cored solder wire has a core of flux running through the center of the solder. As the solder melts, the flux is released directly into the joint. This eliminates the need for a separate flux application step and is convenient for manual soldering.
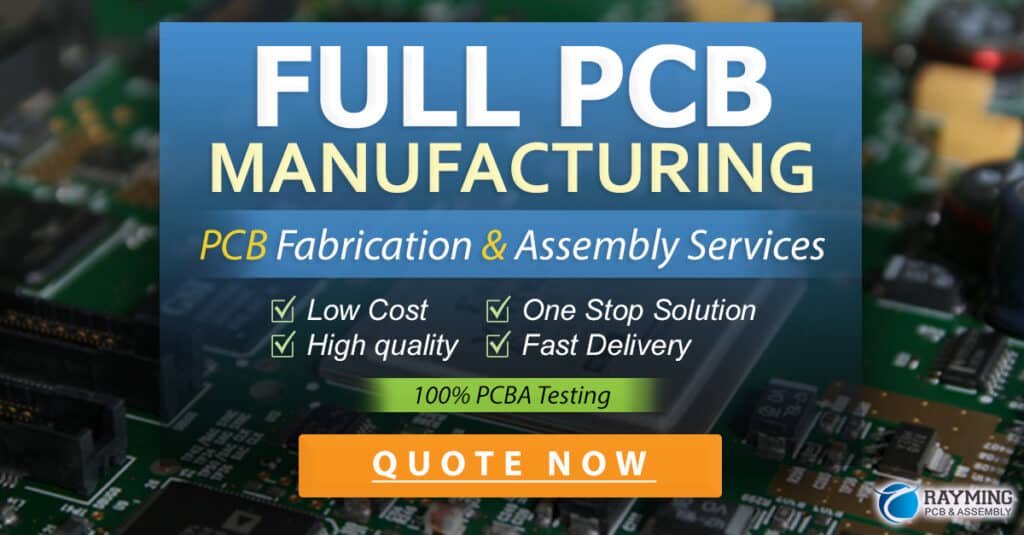
How to Apply Soldering Flux
The method for applying soldering flux depends on the form factor and the specific soldering task at hand. Here are some general guidelines:
-
Clean the surfaces: Before applying flux, ensure that the surfaces to be soldered are clean and free of dirt, grease, or old solder residue.
-
Apply the flux: Use a flux pen, brush, syringe, or other appropriate applicator to apply a thin, even layer of flux to the surfaces to be soldered. Avoid applying too much flux, as excessive residue can be difficult to clean and may lead to joint defects.
-
Preheat (optional): In some cases, gently preheating the fluxed joint can help activate the flux and improve its effectiveness. Be careful not to overheat the components or the flux.
-
Solder the joint: Apply heat to the joint using a soldering iron and add solder as needed. The flux should help the solder flow and wet the surfaces properly.
-
Clean the joint: After soldering, use an appropriate cleaning method to remove any remaining flux residue. Rosin flux can be cleaned with isopropyl alcohol, while water-soluble flux requires cleaning with distilled water. No-clean flux typically doesn’t require cleaning but can be removed if desired.
Soldering Flux Safety and Handling
When working with soldering flux, it’s essential to follow proper safety and handling procedures to minimize risks to your health and the environment.
Health and Safety Precautions
-
Ventilation: Always solder in a well-ventilated area to avoid inhaling flux fumes, which can be irritating to the eyes, nose, and throat. Use a fume extractor if soldering frequently or for extended periods.
-
Skin protection: Wear gloves and avoid skin contact with flux, as some types can cause irritation or allergic reactions. Wash hands thoroughly after soldering.
-
Eye protection: Use safety glasses to protect your eyes from solder splashes and flux fumes.
-
Ingestion: Keep flux away from food and drinks, and avoid eating or drinking while soldering. If ingested, seek medical attention immediately.
Environmental Considerations
-
Disposal: Follow local regulations for disposing of used flux and cleaning solvents. Many types of flux contain chemicals that can be harmful to the environment if not disposed of properly.
-
Cleaning: When cleaning flux residue, use the minimum amount of solvent necessary and dispose of the waste properly. Avoid pouring solvents down the drain.
Frequently Asked Questions (FAQ)
1. Can I use soldering flux on any metal?
Soldering flux is designed to work with common solderable metals such as copper, brass, tin, lead, and silver. However, some metals, like aluminum or stainless steel, may require specialized flux formulations for proper soldering.
2. How long does soldering flux last?
The shelf life of soldering flux varies depending on the type and storage conditions. Most fluxes will last for several years when stored in a cool, dry place away from direct sunlight. Always check the manufacturer’s guidelines for specific storage and expiration information.
3. Can I mix different types of soldering flux?
Mixing different types of flux is not recommended, as they may have incompatible chemical compositions that could lead to poor soldering results or even hazardous reactions. Stick to one type of flux for each soldering task.
4. How much soldering flux should I use?
Apply only enough flux to cover the surfaces to be soldered. Excessive flux can lead to solder joint defects like bridging or balling and may be difficult to clean off after soldering. A thin, even layer of flux is usually sufficient.
5. Can I reuse soldering flux?
In general, soldering flux should not be reused, as it can become contaminated with solder particles, dirt, or other debris during the soldering process. This contamination can reduce the effectiveness of the flux and lead to poor soldering results. Always use fresh flux for each soldering task.
Conclusion
Soldering flux is an essential component in the soldering process, helping to clean and protect metal surfaces, improve solder flow, and create strong, reliable solder joints. By understanding the different types of flux available and how to use them safely and effectively, you can achieve better soldering results and improve the quality of your electronic projects.
No responses yet