What is PCB Impedance Control and Why is it Important?
PCB impedance control refers to the process of designing and manufacturing printed circuit boards (PCBs) to achieve specific impedance values for the transmission lines on the board. Impedance is the measure of opposition to the flow of electric current in a circuit. In high-speed digital circuits, it is crucial to control the impedance of the transmission lines to ensure signal integrity and minimize signal reflections, crosstalk, and electromagnetic interference (EMI).
Proper PCB impedance control is essential for several reasons:
-
Signal Integrity: Controlling the impedance of transmission lines helps maintain the quality and integrity of high-speed signals by minimizing reflections and distortions.
-
Reduced EMI: Impedance-controlled PCBs minimize electromagnetic interference, which can cause signal degradation and affect the performance of nearby electronic devices.
-
Improved Timing: Consistent impedance helps maintain precise timing and synchronization of signals, which is critical in high-speed digital systems.
-
Reliability: PCBs with well-controlled impedance are more reliable and have a lower risk of signal integrity issues, leading to improved overall system performance.
Understanding Impedance Basics
Before diving into the tips for advanced requirements impedance control PCB, it’s essential to understand some basic concepts related to impedance.
Characteristic Impedance
Characteristic impedance (Z0) is the impedance of a transmission line when it is infinitely long or perfectly terminated. It is determined by the physical properties of the transmission line, such as the width, thickness, and spacing of the conductors, as well as the dielectric constant of the insulating material.
The most common characteristic impedance values for PCBs are:
- 50 ohms: Used in high-speed digital circuits, RF, and microwave applications.
- 75 ohms: Used in video and cable television applications.
- 100 ohms: Used in differential signaling, such as Ethernet and USB.
Impedance Matching
Impedance matching is the practice of designing the impedance of the source, transmission line, and load to be equal to minimize signal reflections. When the impedances are matched, the maximum power transfer occurs, and signal integrity is maintained.
Differential and Single-Ended Signaling
There are two main types of signaling used in PCBs:
-
Single-Ended Signaling: In single-ended signaling, a single conductor carries the signal, and the return path is a ground plane or a common reference plane.
-
Differential Signaling: Differential signaling uses two conductors to carry a signal, with each conductor having equal but opposite currents. This type of signaling is more immune to noise and EMI compared to single-ended signaling.
10 Tips for Designing Advanced Requirements Impedance Control PCB
Now that we have covered the basics, let’s explore ten tips for designing advanced requirements impedance control PCBs.
Tip 1: Choose the Right Dielectric Material
The choice of dielectric material is crucial in achieving the desired impedance on a PCB. The dielectric constant (Dk) of the material determines the speed of signal propagation and affects the characteristic impedance of the transmission lines.
Some common dielectric materials used in PCBs include:
Material | Dielectric Constant (Dk) | Dissipation Factor (Df) | Applications |
---|---|---|---|
FR-4 | 4.3-4.7 | 0.02 | General-purpose, cost-effective |
Rogers 4003C | 3.38 | 0.0027 | High-frequency, low-loss |
Rogers 4350B | 3.48 | 0.0037 | High-frequency, low-loss |
Isola I-Tera MT | 3.45 | 0.0031 | High-speed digital, low-loss |
When selecting a dielectric material, consider the following factors:
- Required impedance and frequency range
- Cost and availability
- Manufacturing process compatibility
- Environmental conditions (temperature, humidity, etc.)
Tip 2: Use Appropriate Trace Widths and Spacing
The width and spacing of traces on a PCB have a significant impact on the characteristic impedance of the transmission lines. To achieve the desired impedance, it is essential to use appropriate trace widths and spacing based on the dielectric material and thickness of the PCB.
Some general guidelines for trace widths and spacing:
- Wider traces have lower impedance, while narrower traces have higher impedance.
- Increasing the spacing between traces increases the impedance.
- Thicker dielectric layers result in higher impedance for a given trace width.
Use PCB design software or impedance calculators to determine the optimal trace widths and spacing for your specific requirements.
Tip 3: Maintain Consistent Dielectric Thickness
Consistent dielectric thickness is essential for maintaining uniform impedance throughout the PCB. Variations in dielectric thickness can cause impedance discontinuities, leading to signal reflections and degraded signal integrity.
To ensure consistent dielectric thickness:
- Specify tight tolerances for the dielectric thickness in your PCB fabrication requirements.
- Use a sufficient number of PCB layers to minimize the impact of thickness variations on impedance.
- Consider using high-quality, low-loss dielectric materials with consistent thickness.
Tip 4: Implement Proper Grounding Techniques
Proper grounding is crucial for maintaining signal integrity and controlling impedance in PCBs. A well-designed ground plane provides a low-impedance return path for signals and helps reduce EMI.
Some grounding techniques to consider:
- Use uninterrupted ground planes on adjacent layers to provide a continuous return path for signals.
- Avoid splitting ground planes, as it can create impedance discontinuities and increase EMI.
- Use stitching vias to connect ground planes on different layers, minimizing impedance mismatch.
- Implement ground vias near signal vias to provide a local low-impedance return path.
Tip 5: Minimize Impedance Discontinuities
Impedance discontinuities occur when there is a sudden change in the characteristic impedance of a transmission line. These discontinuities can cause signal reflections, leading to signal integrity issues and EMI.
To minimize impedance discontinuities:
- Avoid abrupt changes in trace width or spacing.
- Use smooth transitions (tapers) when changing trace widths.
- Minimize the use of vias, as they introduce impedance discontinuities.
- If vias are necessary, use a sufficient number of ground vias near signal vias to minimize the impedance mismatch.
Tip 6: Consider Differential Signaling for High-Speed Designs
Differential signaling offers several advantages over single-ended signaling, particularly in high-speed designs. Differential pairs have better noise immunity, lower EMI, and can achieve higher data rates.
When designing differential pairs:
- Route differential traces close together to maintain a consistent differential impedance.
- Keep the length of differential traces matched to avoid skew and maintain signal integrity.
- Use a tight coupling between differential traces to minimize the impact of external noise.
- Avoid routing differential pairs near board edges or through connectors, as this can introduce impedance discontinuities.
Tip 7: Simulate and Optimize Your Design
Simulation tools can help you analyze and optimize your PCB design for impedance control before fabrication. These tools allow you to model transmission lines, predict impedance values, and identify potential signal integrity issues.
Some popular simulation tools for PCB impedance control include:
- Ansys HFSS: A full-wave electromagnetic field simulator for high-frequency and high-speed electronic designs.
- Mentor Graphics HyperLynx: A suite of tools for signal integrity, power integrity, and EMI analysis.
- Cadence Sigrity: A set of tools for signal and power integrity analysis, including impedance modeling and simulation.
By simulating your design, you can optimize trace widths, spacing, and routing to achieve the desired impedance and minimize signal integrity issues.
Tip 8: Collaborate with Your PCB Fabricator
Working closely with your PCB fabricator is essential for ensuring that your impedance control requirements are met. Provide clear and detailed specifications for your PCB, including:
- Required impedance values and tolerances
- Dielectric material and thickness
- Trace widths and spacing
- Copper weight and thickness
- Any special requirements, such as controlled impedance testing
Engage with your fabricator early in the design process to discuss your requirements and ensure that they can be met within your budget and timeline.
Tip 9: Specify Controlled Impedance Testing
To verify that your PCB meets the specified impedance requirements, request controlled impedance testing from your PCB fabricator. This testing measures the actual impedance of the transmission lines on the fabricated board and compares it to your specified values.
Controlled impedance testing methods include:
- Time Domain Reflectometry (TDR): Measures the impedance of a transmission line by sending a fast-rising pulse and analyzing the reflections.
- Time Domain Transmissometry (TDT): Measures the impedance of a transmission line by analyzing the transmitted signal at the far end of the line.
- Impedance Test Coupons: Special test structures placed on the PCB that can be used to measure impedance using TDR or TDT techniques.
Specify the required impedance testing method, sample size, and acceptance criteria in your PCB fabrication requirements.
Tip 10: Document and Communicate Your Requirements
Clear documentation and communication are crucial for ensuring that your impedance control requirements are understood and met by all stakeholders involved in the PCB design and fabrication process.
Create a comprehensive PCB design specification document that includes:
- Impedance requirements and tolerances
- Layer stackup and dielectric materials
- Trace width and spacing rules
- Grounding and shielding requirements
- Controlled impedance testing specifications
Share this document with your design team, PCB fabricator, and any other relevant stakeholders. Regular communication and collaboration throughout the design and fabrication process can help identify and resolve any issues related to impedance control.
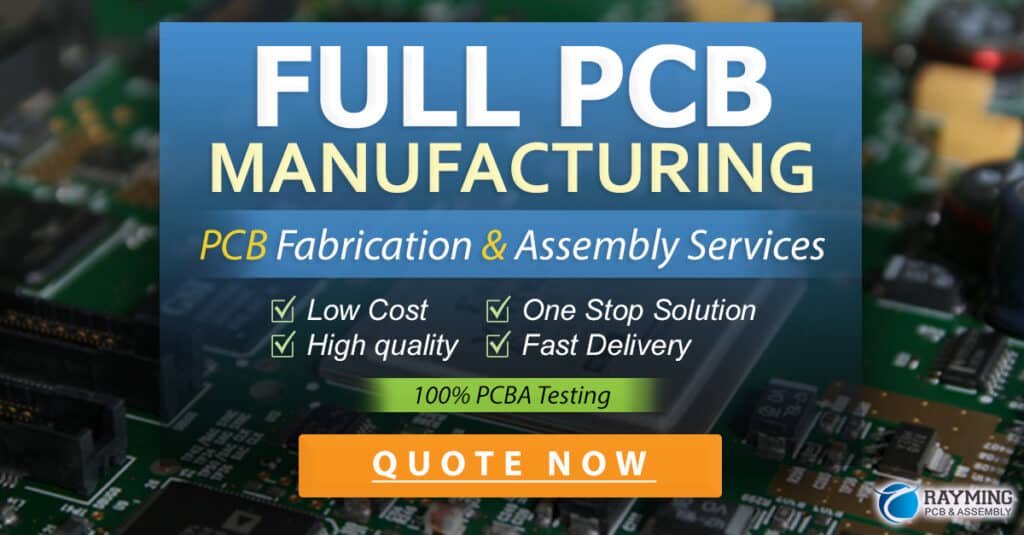
Frequently Asked Questions (FAQ)
- What is the difference between characteristic impedance and differential impedance?
-
Characteristic impedance (Z0) refers to the impedance of a single-ended transmission line, while differential impedance (Zdiff) refers to the impedance between two coupled traces in a differential pair.
-
How does the dielectric constant of a material affect impedance?
-
A higher dielectric constant results in lower impedance for a given trace geometry. Conversely, a lower dielectric constant leads to higher impedance.
-
What is the purpose of a ground plane in impedance control?
-
A ground plane provides a low-impedance return path for signals, minimizing impedance discontinuities and reducing EMI. It also helps maintain a consistent reference plane for impedance calculations.
-
Can vias be used in high-speed, impedance-controlled designs?
-
While vias introduce impedance discontinuities, they can be used in high-speed designs with proper techniques. Use a sufficient number of ground vias near signal vias to minimize the impedance mismatch, and consider using blind or buried vias to reduce the impact on impedance.
-
What is the importance of controlled impedance testing?
- Controlled impedance testing verifies that the fabricated PCB meets the specified impedance requirements. It helps ensure signal integrity and reduces the risk of problems related to impedance mismatch, such as signal reflections and EMI.
Conclusion
Designing advanced requirements impedance control PCBs requires careful consideration of various factors, including dielectric materials, trace geometry, grounding techniques, and simulation. By following the ten tips outlined in this article and working closely with your PCB fabricator, you can achieve the desired impedance values, maintain signal integrity, and minimize EMI in your high-speed PCB designs.
Remember to document your requirements clearly, communicate with all stakeholders, and specify controlled impedance testing to verify that your PCB meets the specified impedance targets. With proper planning, execution, and collaboration, you can successfully design and manufacture advanced requirements impedance control PCBs for your high-speed applications.
No responses yet