Introduction
Printed Circuit Boards (PCBs) are the backbone of modern electronics. They provide a platform for mounting and interconnecting electronic components to create a functional circuit. At the heart of every PCB lies the PCB Controller, a crucial component responsible for managing and controlling the various functions of the board. In this comprehensive article, we will delve into the world of PCB controllers, exploring their types, functions, design considerations, and more.
What is a PCB Controller?
A PCB controller is an integrated circuit (IC) that acts as the brain of the PCB. It is responsible for controlling and coordinating the various functions and operations of the board. The controller receives inputs from sensors, switches, or other components, processes the information, and generates appropriate outputs to control other components or communicate with external devices.
Types of PCB Controllers
PCB controllers come in various types, each designed for specific applications and requirements. Here are some common types of PCB controllers:
-
Microcontrollers (MCUs): Microcontrollers are the most versatile and widely used type of PCB controllers. They are essentially small computers on a single chip, containing a processor, memory, and input/output peripherals. MCUs can be programmed to perform a wide range of tasks, from simple control functions to complex algorithms.
-
Application-Specific Integrated Circuits (ASICs): ASICs are custom-designed controllers tailored for specific applications. They are optimized for performance, power efficiency, and cost-effectiveness in a particular domain. ASICs are commonly used in high-volume products where the development cost can be justified.
-
Field-Programmable Gate Arrays (FPGAs): FPGAs are programmable controllers that consist of an array of configurable logic blocks and interconnects. They offer flexibility and reconfigurability, allowing designers to implement custom digital circuits without the need for a dedicated ASIC. FPGAs are often used in prototyping, low-volume production, or applications that require frequent updates.
-
System-on-Chip (SoC) Controllers: SoC controllers integrate multiple functions onto a single chip, including a processor, memory, peripherals, and even custom logic. They provide a complete system solution in a compact package, reducing the overall footprint and power consumption of the PCB.
Functions of a PCB Controller
PCB controllers perform a variety of functions to ensure the proper operation and functionality of the PCB. Some of the key functions include:
-
Processing and Computation: The controller executes instructions and performs computations based on the programmed firmware or software. It processes data from sensors, performs calculations, and makes decisions based on predefined algorithms.
-
Input/Output (I/O) Management: The controller interfaces with various input and output devices connected to the PCB. It reads inputs from switches, buttons, or sensors and controls outputs such as LEDs, displays, or actuators.
-
Communication: PCB controllers often include communication interfaces like UART, I2C, SPI, or USB to communicate with other devices or systems. They can exchange data, receive commands, or send status updates over these interfaces.
-
Timing and Synchronization: Controllers generate and manage timing signals to synchronize the operation of different components on the PCB. They control the clock signals, generate pulses, and ensure proper timing relationships between various elements.
-
Power Management: PCB controllers can include power management features to optimize power consumption and ensure the efficient operation of the board. They can control power states, enable/disable peripherals, and implement power-saving modes.
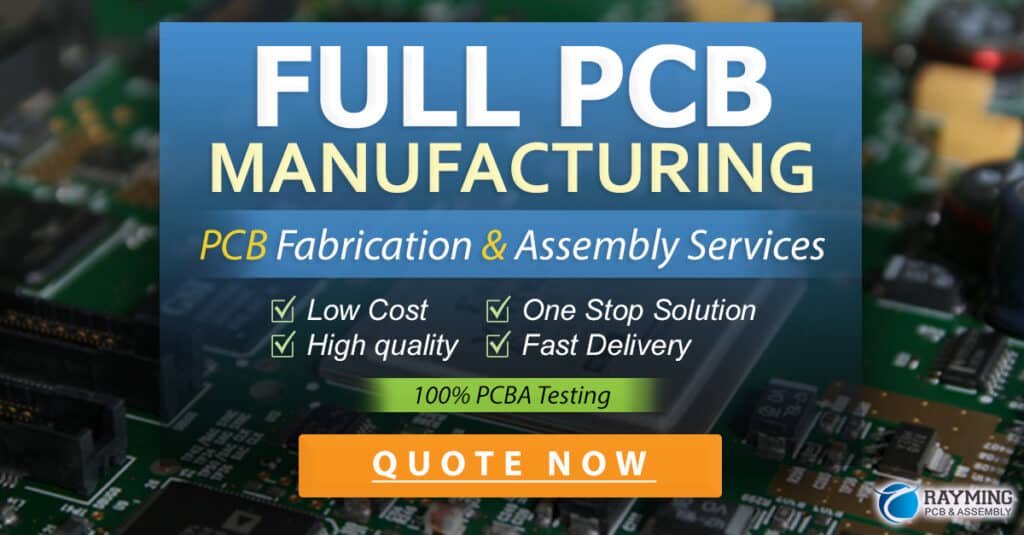
PCB Controller Design Considerations
Designing a PCB with a controller involves several key considerations to ensure optimal performance, reliability, and functionality. Here are some important factors to keep in mind:
-
Selecting the Right Controller: Choose a controller that meets the specific requirements of your application in terms of processing power, memory, peripherals, and power consumption. Consider factors like cost, availability, and development tools when making your selection.
-
Power Supply and Decoupling: Ensure a clean and stable power supply to the controller by using appropriate voltage regulators and decoupling capacitors. Follow the manufacturer’s recommendations for power supply decoupling and layout guidelines.
-
Signal Integrity: Pay attention to signal integrity when routing traces to and from the controller. Minimize crosstalk, reflections, and electromagnetic interference (EMI) by following best practices for trace routing, impedance matching, and shielding.
-
Timing and Clock Distribution: Carefully design the clock distribution network to ensure proper timing and synchronization of the controller and other components. Use appropriate clock sources, buffering, and termination techniques to maintain signal integrity.
-
Firmware Development: Develop efficient and reliable firmware for the controller, taking into account the specific requirements of your application. Use a structured development process, including version control, testing, and debugging, to ensure the quality and reliability of the firmware.
-
Thermal Management: Consider the thermal characteristics of the controller and ensure adequate heat dissipation. Use thermal simulation tools to analyze the thermal profile of the PCB and implement appropriate cooling solutions, such as heatsinks or thermal vias, if necessary.
-
EMC Compliance: Ensure that the PCB design complies with electromagnetic compatibility (EMC) standards to minimize interference and ensure reliable operation in the intended environment. Follow guidelines for grounding, shielding, and filtering to mitigate EMI issues.
PCB Controller Interfaces and Protocols
PCB controllers communicate with other components and devices using various interfaces and protocols. Understanding these interfaces is crucial for designing an effective PCB. Here are some common interfaces and protocols used by PCB controllers:
Interface/Protocol | Description |
---|---|
UART | Universal Asynchronous Receiver-Transmitter, used for serial communication between devices |
I2C | Inter-Integrated Circuit, a multi-master, multi-slave serial communication protocol |
SPI | Serial Peripheral Interface, a synchronous serial communication protocol |
USB | Universal Serial Bus, a widely used interface for communication between devices |
CAN | Controller Area Network, a robust serial communication protocol commonly used in automotive systems |
Ethernet | A widely adopted networking protocol for communication between devices |
Debugging and Testing PCB Controllers
Debugging and testing are critical steps in the development of PCB controllers. They help identify and resolve issues, ensure proper functionality, and validate the performance of the controller. Here are some techniques and tools commonly used for debugging and testing PCB controllers:
-
In-Circuit Debugging: Use in-circuit debugging tools, such as JTAG or SWD, to access the controller’s internal registers, memory, and peripherals in real-time. This allows you to step through the firmware, set breakpoints, and analyze the controller’s behavior.
-
Logic Analyzers: Logic analyzers are powerful tools for capturing and analyzing digital signals on the PCB. They can help troubleshoot timing issues, protocol violations, or communication problems between the controller and other components.
-
Oscilloscopes: Oscilloscopes are used to visualize and measure analog signals on the PCB. They are essential for analyzing signal integrity, detecting noise or distortion, and verifying the proper functioning of analog circuits interfacing with the controller.
-
Firmware Debugging: Utilize the debugging features provided by the controller’s development environment, such as breakpoints, watchpoints, and memory inspection. Use serial communication or debug output to print valuable information for monitoring the controller’s state and behavior.
-
Automated Testing: Develop automated test scripts or use test automation frameworks to validate the functionality and performance of the controller. This can include unit tests for individual functions, integration tests for system-level behavior, and stress tests to evaluate the controller’s reliability under various conditions.
PCB Controller Development Tools and Resources
Developing firmware for PCB controllers requires a set of tools and resources to streamline the process and ensure efficient development. Here are some essential tools and resources for PCB controller development:
-
Integrated Development Environments (IDEs): IDEs provide a comprehensive environment for writing, debugging, and compiling firmware for PCB controllers. Popular IDEs include Keil MDK, IAR Embedded Workbench, and Eclipse-based IDEs.
-
Compilers and Toolchains: Compilers convert the high-level programming language (such as C or C++) into machine code that can be executed by the controller. Toolchains include the compiler, assembler, linker, and other tools necessary for building the firmware.
-
Hardware Debuggers: Hardware debuggers, such as JTAG or SWD debuggers, allow you to connect to the controller and perform in-circuit debugging. They provide features like breakpoints, memory access, and real-time monitoring of the controller’s behavior.
-
Evaluation Boards and Development Kits: Manufacturers often provide evaluation boards or development kits for their PCB controllers. These boards come with pre-configured hardware and sample code, making it easier to get started with development and testing.
-
Online Resources and Communities: Utilize online resources, such as forums, blogs, and documentation provided by controller manufacturers and the embedded systems community. These resources offer valuable insights, tutorials, and support for PCB controller development.
Frequently Asked Questions (FAQ)
-
What is the difference between a microcontroller and a microprocessor?
A microcontroller is a self-contained system that includes a processor, memory, and peripherals on a single chip. It is designed for embedded applications and can operate independently. In contrast, a microprocessor is a central processing unit (CPU) that requires external memory and peripherals to function as a complete system. -
Can a single PCB have multiple controllers?
Yes, a PCB can have multiple controllers depending on the complexity and requirements of the application. For example, a PCB may have a main controller for overall system control and additional controllers for specific functions like power management or sensor data processing. -
How do I choose the right controller for my PCB?
When selecting a controller for your PCB, consider factors such as processing power, memory requirements, peripheral interfaces, power consumption, cost, and availability. Evaluate the specific needs of your application and choose a controller that meets those requirements while fitting within your budget and design constraints. -
What programming languages are commonly used for PCB controller firmware development?
C and C++ are the most commonly used programming languages for PCB controller firmware development. These languages provide low-level access to hardware, efficient memory management, and good performance. Some controllers also support other languages like Assembly, Python, or BASIC, depending on the specific controller and development environment. -
How can I ensure the security of my PCB controller?
To ensure the security of your PCB controller, consider implementing measures such as secure boot, firmware encryption, and tamper detection. Use secure communication protocols and authentication mechanisms to prevent unauthorized access. Additionally, regularly update the firmware with security patches and follow best practices for secure coding and design.
Conclusion
PCB controllers play a vital role in the functioning and performance of PCBs. They act as the brain of the board, controlling and coordinating various operations and interfaces. Understanding the types, functions, and design considerations of PCB controllers is essential for designing reliable and efficient electronic systems.
When designing a PCB with a controller, it is crucial to select the right controller, ensure proper power supply and decoupling, maintain signal integrity, and develop robust firmware. Debugging and testing are critical steps in the development process to identify and resolve issues and ensure the controller’s proper functionality.
By leveraging the appropriate development tools, resources, and best practices, designers can create PCB controllers that meet the specific requirements of their applications while optimizing performance, reliability, and cost-effectiveness.
As technology continues to advance, PCB controllers will play an increasingly important role in enabling new and innovative electronic solutions. Stay updated with the latest trends, techniques, and best practices in PCB controller design to stay ahead in the rapidly evolving world of electronics.
No responses yet