Introduction to Flex PCB Soldering
Flexible printed circuit boards (Flex PCBs) have gained significant popularity in recent years due to their versatility and ability to conform to various shapes and sizes. These PCBs find applications in a wide range of industries, including consumer electronics, medical devices, aerospace, and automotive. However, soldering components onto Flex PCBs requires specialized techniques and considerations compared to traditional rigid PCBs. In this article, we will explore five common Flex PCB soldering technologies and their key characteristics.
What is Flex PCB Soldering?
Flex PCB soldering is the process of attaching electronic components to flexible printed circuit boards using solder. The primary goal is to create reliable electrical connections between the components and the PCB while maintaining the flexibility and integrity of the board. Flex PCB soldering requires careful selection of soldering techniques, materials, and equipment to ensure optimal results.
Why is Flex PCB Soldering Important?
Proper Flex PCB soldering is crucial for several reasons:
- Reliability: Well-executed soldering ensures robust electrical connections that can withstand the stresses and strains associated with flexible PCBs.
- Functionality: Accurate soldering allows the components to function as intended, minimizing the risk of short circuits or open connections.
- Durability: Appropriate soldering techniques and materials contribute to the longevity of the Flex PCB assembly, reducing the likelihood of premature failure.
- Flexibility: Soldering methods that preserve the flexibility of the PCB are essential for applications that require bending, folding, or twisting of the board.
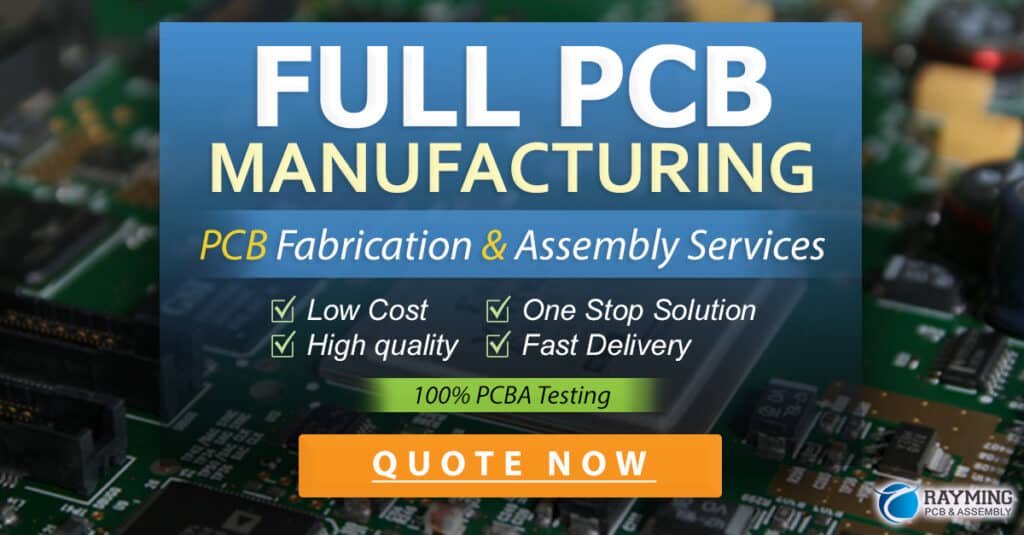
5 Common Flex PCB Soldering Technologies
1. Hand Soldering
Hand soldering is a manual soldering technique that involves using a soldering iron to apply solder to the component leads and PCB pads. This method is suitable for low-volume production, prototyping, or rework purposes.
Advantages:
- Flexibility in soldering specific components or areas
- Low initial investment in equipment
- Ideal for small-scale production or repairs
Disadvantages:
- Time-consuming and labor-intensive
- Inconsistent results due to human factors
- Limited to relatively large component sizes
2. Reflow Soldering
Reflow soldering is an automated process that uses a reflow oven to melt and bond solder paste applied to the PCB pads and component leads. This method is widely used for surface mount technology (SMT) components and is suitable for high-volume production.
Advantages:
- High throughput and efficiency
- Consistent and reliable solder joints
- Compatibility with a wide range of SMT components
Disadvantages:
- Higher initial investment in equipment
- Limited flexibility for selective soldering
- Requires precise control of temperature profiles
3. Wave Soldering
Wave soldering involves passing the PCB over a molten solder wave, which selectively solders the components to the board. This method is primarily used for through-hole components but can also be adapted for certain SMT components.
Advantages:
- Fast and efficient for high-volume production
- Suitable for both through-hole and some SMT components
- Provides good solder joint strength
Disadvantages:
- Limited control over solder joint geometry
- Potential for thermal stress on the PCB and components
- Requires proper masking and pallet design
4. Selective Soldering
Selective soldering is a targeted soldering process that uses a mini-wave or laser to apply solder to specific areas of the PCB. This method is ideal for Flex PCBs with a mix of through-hole and SMT components or for boards with heat-sensitive components.
Advantages:
- Precise control over soldering locations
- Reduced thermal stress on the PCB and components
- Flexibility in soldering different component types
Disadvantages:
- Slower than wave soldering for high-volume production
- Higher equipment and programming costs
- Requires accurate fixturing and nozzle design
5. Laser Soldering
Laser soldering uses a focused laser beam to heat and melt solder at specific points on the PCB. This method offers high precision and minimal heat transfer to the surrounding areas, making it suitable for delicate Flex PCBs and heat-sensitive components.
Advantages:
- Highly precise and localized soldering
- Minimal thermal stress on the PCB and components
- Fast and efficient for small-scale production
Disadvantages:
- High equipment costs
- Limited to relatively small solder joint sizes
- Requires specialized training and programming
Comparison of Flex PCB Soldering Technologies
Soldering Technology | Suitable for | Throughput | Initial Investment | Flexibility |
---|---|---|---|---|
Hand Soldering | Low-volume, rework | Low | Low | High |
Reflow Soldering | High-volume, SMT | High | Medium | Medium |
Wave Soldering | High-volume, through-hole | High | Medium | Low |
Selective Soldering | Mixed components | Medium | High | High |
Laser Soldering | Delicate components | Medium | High | High |
Frequently Asked Questions (FAQ)
-
Q: What are the challenges in soldering Flex PCBs compared to rigid PCBs?
A: Flex PCBs present unique challenges such as maintaining flexibility, preventing thermal damage, and accommodating different component types. Specialized techniques and materials are required to address these challenges. -
Q: Can standard soldering techniques be used for Flex PCBs?
A: While standard soldering techniques can be adapted for Flex PCBs, they may not always provide the best results. Flex PCBs often require tailored approaches to ensure reliable solder joints and preserve the board’s flexibility. -
Q: How do I choose the right soldering technology for my Flex PCB project?
A: The choice of soldering technology depends on factors such as production volume, component types, board complexity, and available resources. Consider the advantages and disadvantages of each method and consult with experienced professionals to make an informed decision. -
Q: What materials are commonly used for soldering Flex PCBs?
A: Common materials for Flex PCB soldering include lead-free solder alloys (e.g., SAC305), low-temperature solders, and flexible solder masks. The selection of materials should prioritize compatibility with the Flex PCB substrate and the ability to maintain flexibility. -
Q: How can I ensure the reliability of solder joints on Flex PCBs?
A: To ensure reliable solder joints, follow best practices such as proper board design, appropriate soldering techniques, use of compatible materials, and thorough inspection and testing. Adhere to industry standards and guidelines for Flex PCB soldering to minimize the risk of defects and failures.
Conclusion
Flex PCB soldering is a critical aspect of manufacturing reliable and high-quality flexible electronic assemblies. The five common soldering technologies discussed in this article – hand soldering, reflow soldering, wave soldering, selective soldering, and laser soldering – offer distinct advantages and considerations for different applications and production scales. By understanding the characteristics and suitability of each method, manufacturers can make informed decisions and optimize their Flex PCB soldering processes.
As the demand for flexible electronics continues to grow, staying updated with the latest advancements in Flex PCB soldering technologies is crucial. Ongoing research and development efforts aim to improve the efficiency, precision, and reliability of soldering processes while accommodating the unique requirements of Flex PCBs. By embracing innovative solutions and best practices, the electronics industry can unlock the full potential of Flex PCBs and drive the development of cutting-edge products across various sectors.
No responses yet