Introduction to Absolute Pressure Sensors
An absolute pressure sensor is a highly precise device used to measure atmospheric or barometric pressure in a wide range of applications. Unlike gauge pressure sensors that measure pressure relative to ambient atmospheric pressure, absolute pressure sensors provide a fixed reference point by measuring pressure relative to a perfect vacuum. This makes them ideal for applications requiring accurate and consistent pressure measurements regardless of changes in ambient conditions.
How Do Absolute Pressure Sensors Work?
Absolute pressure sensors typically consist of a thin, flexible diaphragm that deflects in response to changes in pressure. The diaphragm is sealed on one side with a reference vacuum chamber, while the other side is exposed to the pressure being measured. As the pressure changes, the diaphragm flexes, and this deflection is converted into an electrical signal using various sensing technologies, such as piezoresistive, capacitive, or resonant elements.
The electrical signal generated by the sensor is then processed and converted into a standardized output, such as voltage, current, or digital data, which can be easily integrated into control systems, data acquisition equipment, or other devices.
Key Features and Benefits of Absolute Pressure Sensors
Absolute pressure sensors offer several key features and benefits that make them essential for many pressure measurement applications:
- High accuracy: Absolute pressure sensors provide highly accurate measurements, with some models offering accuracies as high as ±0.05% of full-scale output.
- Wide pressure range: These sensors are available in a wide range of pressure ranges, from low-pressure applications (e.g., 0-1 bar) to high-pressure applications (e.g., 0-1000 bar or more).
- Temperature compensation: Many absolute pressure sensors include built-in temperature compensation to ensure accurate measurements across a wide temperature range.
- Robust construction: Absolute pressure sensors are designed to withstand harsh environments, with many models featuring stainless steel or ceramic construction for improved durability and chemical resistance.
- Versatile outputs: Sensors are available with various output options, including analog voltage, current (4-20 mA), and digital interfaces (e.g., I2C, SPI, or RS-485), making them easy to integrate into existing systems.
Applications of Absolute Pressure Sensors
Absolute pressure sensors are used in a wide range of industries and applications, including:
Automotive Industry
In the automotive industry, absolute pressure sensors play a crucial role in various systems:
- Manifold Absolute Pressure (MAP) sensors: MAP sensors measure the absolute pressure in the intake manifold of an internal combustion engine, providing critical data for engine management systems to optimize fuel injection, ignition timing, and other parameters.
- Barometric Pressure Sensors (BAP): BAP sensors measure atmospheric pressure to help engine control units (ECUs) make adjustments based on altitude, improving engine performance and emissions.
- Tire Pressure Monitoring Systems (TPMS): Absolute pressure sensors are used in TPMS to accurately measure tire pressure, alerting drivers to potential safety issues caused by under-inflated or over-inflated tires.
Industrial Process Control
Absolute pressure sensors are essential for monitoring and controlling various industrial processes:
- Hydraulic and pneumatic systems: Absolute pressure sensors help monitor and control fluid pressure in hydraulic and pneumatic systems, ensuring optimal performance and preventing system failures.
- Vacuum processing: In applications such as vacuum packaging, vacuum coating, and semiconductor manufacturing, absolute pressure sensors provide precise monitoring of vacuum levels to maintain process consistency and quality.
- Gas and liquid flow measurement: Absolute pressure sensors are used in conjunction with differential pressure sensors to accurately measure the flow rates of gases and liquids in industrial processes.
Medical and Life Sciences
Absolute pressure sensors find numerous applications in the medical and life sciences fields:
- Blood pressure monitoring: Absolute pressure sensors are used in both invasive and non-invasive blood pressure monitoring devices to provide accurate and reliable measurements.
- Respiratory equipment: In ventilators and other respiratory support devices, absolute pressure sensors help monitor and control airway pressure to ensure patient safety and comfort.
- Laboratory equipment: Absolute pressure sensors are used in various laboratory equipment, such as autoclaves, centrifuges, and incubators, to monitor and control pressure levels for consistent and reliable results.
Aerospace and Defense
In the aerospace and defense industries, absolute pressure sensors are used for:
- Altimeters: Absolute pressure sensors form the core of altimeters, which measure atmospheric pressure to determine altitude in aircraft, helicopters, and UAVs.
- Engine monitoring: Absolute pressure sensors monitor pressure levels in aircraft engines to ensure optimal performance and detect potential issues before they lead to failures.
- Environmental control systems: In spacecraft and aircraft, absolute pressure sensors help maintain cabin pressure and monitor life support systems to ensure crew safety and comfort.
Choosing the Right Absolute Pressure Sensor
When selecting an absolute pressure sensor for a specific application, several key factors should be considered:
Pressure Range
Choose a sensor with a pressure range that encompasses the expected pressure levels in your application, with some headroom for unexpected spikes or fluctuations. Sensors are available in ranges from low-pressure (e.g., 0-1 bar) to high-pressure (e.g., 0-1000 bar or more).
Accuracy and Precision
Consider the required accuracy and precision for your application. Some applications may require high accuracy (e.g., ±0.05% of full-scale output), while others may tolerate lower accuracies (e.g., ±0.25% or more). Precision refers to the sensor’s ability to consistently produce the same output for a given pressure input.
Temperature Range
Ensure that the sensor’s operating temperature range matches the expected temperature conditions in your application. Many sensors offer built-in temperature compensation to maintain accuracy across a wide temperature range.
Output Type
Choose a sensor with an output type that is compatible with your data acquisition or control system. Common output options include analog voltage, current (4-20 mA), and digital interfaces (e.g., I2C, SPI, or RS-485).
Environmental Factors
Consider the environmental factors your sensor will be exposed to, such as vibration, shock, humidity, and corrosive substances. Choose a sensor with appropriate protection and certifications (e.g., IP rating, explosion-proof) for your application.
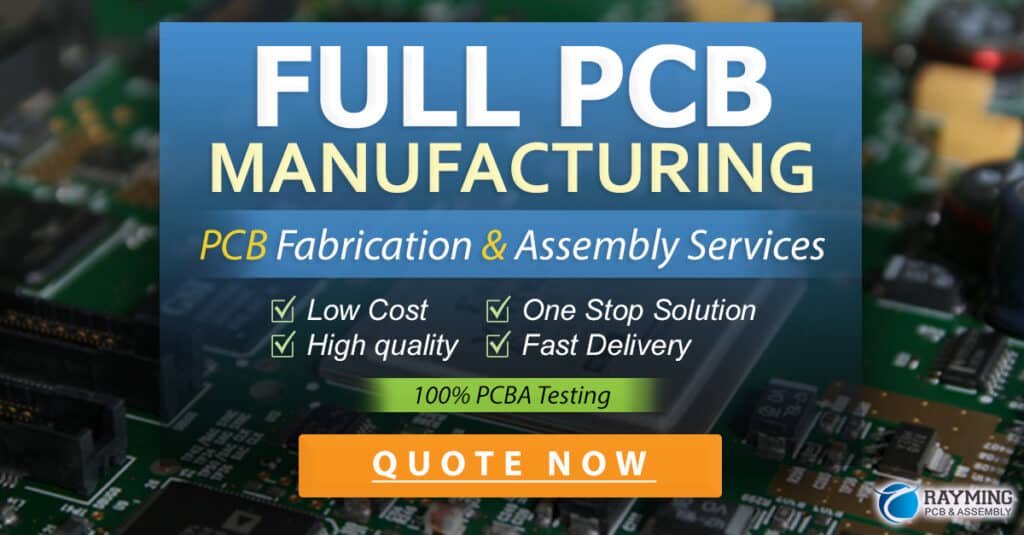
Calibration and Maintenance of Absolute Pressure Sensors
To ensure ongoing accuracy and reliability, absolute pressure sensors require periodic calibration and maintenance. Calibration involves comparing the sensor’s output to a known reference pressure and adjusting the sensor’s output to match the reference. The frequency of calibration depends on the application and the sensor’s specifications, but it is generally recommended to calibrate sensors at least once a year or as specified by the manufacturer.
In addition to calibration, regular maintenance can help extend the life of your absolute pressure sensor and prevent failures. This may include:
- Cleaning: Regularly clean the sensor’s pressure port and diaphragm to prevent buildup of debris or contaminants that could affect accuracy.
- Visual inspection: Inspect the sensor for signs of physical damage, such as cracks, corrosion, or loose connections.
- Firmware updates: For sensors with digital interfaces, ensure that the firmware is up to date to take advantage of any performance improvements or bug fixes.
By following proper calibration and maintenance procedures, you can ensure that your absolute pressure sensor provides accurate and reliable measurements throughout its service life.
Frequently Asked Questions (FAQ)
1. What is the difference between an absolute pressure sensor and a gauge pressure sensor?
An absolute pressure sensor measures pressure relative to a perfect vacuum (0 psi), while a gauge pressure sensor measures pressure relative to ambient atmospheric pressure. Gauge pressure sensors are typically used when the absolute pressure value is not required, and the pressure being measured is always higher than atmospheric pressure.
2. Can absolute pressure sensors be used to measure vacuum?
Yes, absolute pressure sensors can measure vacuum levels because they measure pressure relative to a perfect vacuum. As the pressure decreases below atmospheric pressure, the sensor’s output will decrease, indicating the level of vacuum.
3. Are absolute pressure sensors affected by changes in altitude?
No, absolute pressure sensors are not affected by changes in altitude because they measure pressure relative to a fixed reference point (a perfect vacuum). This makes them ideal for applications where accurate pressure measurements are required regardless of changes in ambient atmospheric pressure.
4. How often should I calibrate my absolute pressure sensor?
The frequency of calibration depends on the application and the sensor’s specifications. As a general guideline, it is recommended to calibrate sensors at least once a year or as specified by the manufacturer. However, in critical applications or harsh environments, more frequent calibration may be necessary to ensure ongoing accuracy.
5. Can absolute pressure sensors be used in hazardous environments?
Yes, some absolute pressure sensors are designed for use in hazardous environments, such as those with explosive atmospheres or corrosive substances. These sensors typically have appropriate certifications (e.g., ATEX, IECEx, or UL) and features (e.g., explosion-proof or intrinsically safe) to ensure safe operation in these environments. Always ensure that the sensor you choose is suitable for your specific application and meets the necessary safety requirements.
Conclusion
Absolute pressure sensors are essential tools for accurate and reliable pressure measurement in a wide range of industries and applications. By understanding the key features, benefits, and considerations when choosing an absolute pressure sensor, you can ensure that you select the right sensor for your specific needs.
Regular calibration and maintenance are crucial for ensuring ongoing accuracy and reliability, and proper selection of sensors with appropriate certifications and features is essential for safe operation in hazardous environments.
As technology continues to advance, absolute pressure sensors will likely become even more precise, compact, and versatile, enabling new applications and improvements in existing ones. By staying informed about the latest developments in absolute pressure sensor technology, you can take advantage of these advancements to improve the performance, efficiency, and safety of your pressure measurement applications.
No responses yet